Braking is at its most effective when the grip of the tire on the road surface is at its maximum
During braking, the tire slides over the surface, and the circumferential speed of the wheel becomes less than the speed of the car
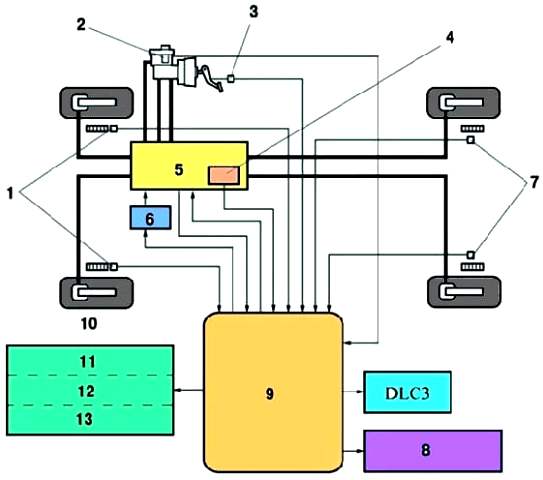
The anti-lock braking system (fig. 2) limits the pressure generated in the hydraulic brake actuator so that the amount of slip is optimal.
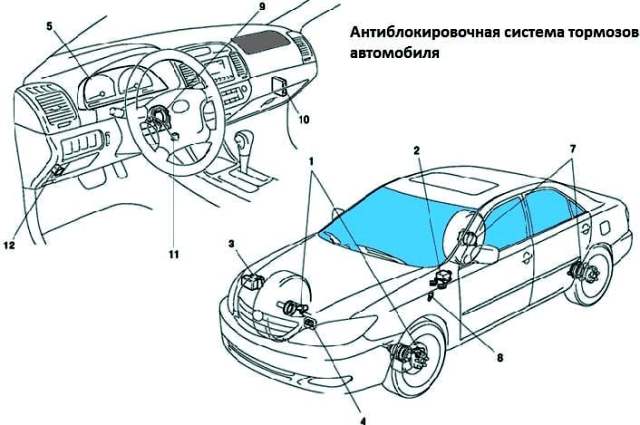
The operation of this system should be separate for each wheel.
The system must immediately respond to every change in the surface (traction coefficient) and the load on the car.
The anti-lock braking system prevents the wheels from locking during heavy braking, thereby reducing the braking distance.
The grip force between the wheels and the road in this case is greater if the wheels continue to rotate during braking.
Even with full braking, the car remains steerable.
Rate sensors, one for each wheel, measure wheel speed.
Based on the signals from the sensors, the electronic control unit calculates an average speed approximately corresponding to the speed of the vehicle.
By comparing the rotational speed of each individual wheel with the average calculated speed, the electronic unit determines the slip state of the individual wheel and thereby determines which wheel is in the pre-lock state.
When one of the four wheel speed sensors transmits a locked wheel signal to the respective wheel, the ECU immediately sends a close signal to the respective inlet solenoid valve, which shuts off the brake fluid supply through the line to the wheel brake.
In this case, the braking force remains constant.
If the sliding continues, the release valve opens and the pressure in the hydraulic system of this brake decreases.
The wheel does not brake, excess brake fluid returns to the reservoir.
Once the wheel starts spinning again, the intake valve opens and the exhaust valve closes.
The pressure in the circuit increases and the wheel brakes again.
The cycles of braking and free rotation of the wheel change very quickly (several times per second) and continue until the car stops or the brake pedal is released.
The process is repeated under hard braking separately for each wheel until the brake pedal is released.
The alarm system ensures that the ABS is turned off in case of any malfunction or low voltage in the vehicle's on-board network (below 10 V).
An ABS malfunction does not affect the operation of the brakes.
The hydraulic drive consists of a hydraulic unit, brake calipers and brake pipes.
The hydraulic unit includes an electric pressure pump and solenoid valves.