Головка цилиндров и механизм газораспределения Д-245
Головка цилиндров представляет собой чугунную отливку, во внутренних полостях которой имеются впускные и выпускные каналы, закрываемые клапанами
Для обеспечения отвода тепла головка цилиндров имеет внутренние полости, в которых циркулирует охлаждающая жидкость.
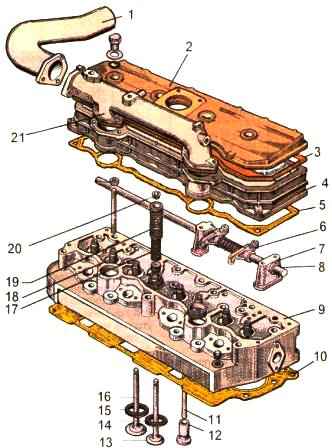
Головка цилиндров 9 имеет вставные седла клапанов 14 и 15, изготовленные из жаропрочного и износостойкого сплава.
На головке цилиндров сверху устанавливаются стойки 7, ось 8 коромысел с коромыслами 6, крышка головки 4, впускной коллектор и колпак 2 крышки, закрывающий клапанный механизм.
Со стороны топливного насоса в головке установлены четыре форсунки, а со стороны генератора к головке крепится выпускной коллектор.
Для уплотнения разъема между головкой и блоком цилиндров установлена прокладка 10 из асбостального полотна.
Отверстия для гильз цилиндров и масляного канала окантованы листовой сталью.
При сборке дизеля на заводе цилиндровые отверстия прокладки дополнительно окантовываются фторопластовыми разрезными кольцами.
Головка цилиндров должна быть очищена от накипи, нагара и промыта.
Трещины, негерметичность посадки технологических заглушек не допускаются.
При гидравлическом испытании жидкостной рубашки головки цилиндров под давлением 0,40±02 МПа в течение 3 мин течь и появление капель не допускаются.
После замены негерметичных заглушек головку цилиндров следует вторично испытать на герметичность.
Неплоскостность поверхности прилегания головки цилиндров к блоку не должна превышать 0,1 мм на длине головки (0,05 мм для новой головки).
Неплоскостность поверхности прилегания головки цилиндров к выхлопному коллектору не должна превышать 0,2 мм на всей длине (0,1 мм для новой головки).
Высота головки цилиндров должна быть не менее 100,7 мм (103-0,22 мм для новой головки).
Резьбовые отверстия под шпильки в головке цилиндров не должны иметь повреждений.
Рабочие фаски седел и тарелок клапанов должны быть обработаны под углом 45+0,5.
Биение поверхности рабочей фаски седла относительно поверхности направляющей втулки после обработки не должно превышать 0,05 мм.
Биение поверхности рабочей фаски тарелки клапана относительно, поверхности стержня допускается не более 0,03 мм.
Ширина рабочей фаски седла после обработки должна быть 2,0-2,2 мм.
Высота цилиндрического пояска тарелки клапана должна быть не менее 1,5 мм.
Седла клапана, охлажденные до -120°С, должны быть запрессованы в головку цилиндров, нагретую до 70°С.
Выступание направляющей втулки над плоскостью головки цилиндров, то есть размер от верхнего торца направляющей втулки до поверхности выточки цилиндров под пружины клапанов, должно соответствовать 33-1,0 мм.
Клапаны должны быть притерты и герметично прилегать к седлам.
Качество притирки следует проверять по наличию на конических поверхностях клапана и седла кольцевой матовой полоски.
Ширина полоски должна быть 15…2,0 мм; разрывы полоски не допускаются.
Ширина притертой фаски седла клапана должна быть одинакова по всей длине; разность ширины притертой фаски седла допускается не более 0,5 мм.
Полоска на клапане должна располагаться не далее 1,0 мм от кромки цилиндрического пояска тарелки клапана.
Герметичность прилегания тарелки клапана к седлу следует проверять пневматическим приспособлением КИ-16311 - при давлении воздуха 0,03-0,05 МПа; просачивание воздуха (появление пузырей) не допускается.
Допускается проверка герметичности прилегания клапанов к седлам заливкой керосина во впускные и выпускные каналы; течь или появление капель керосина из-под тарелок клапанов в течение 2 мин не допускается.
После притирки клапанов к седлам головка цилиндров и клапаны должны быть промыты до полного удаления с деталей притирочной пасты.
Стержни клапанов в направляющих втулках должны перемещаться свободно, без заметного поперечного покачивания.
Стержни клапанов перед сборкой должны быть смазаны моторным маслом М-10Г2.
Утопание нижних плоскостей тарелок впускных и выпускных клапанов относительно нижней плоскости головки цилиндров должно быть в пределах 1,05-1,25 мм.
Заглушки при установке в головку цилиндров допускается уплотнять цинковыми или титановыми белилами.
Торцы заглушек после запрессовки не должны выступать над плоскостью головки цилиндров.
Непрямолинейность стержня клапана допускается на всей длине не более 0,022 мм (для нового клапана - 0,015).
На поверхностях клапана не допускаются трещины и волосовины. Контролю подлежат 100% клапанов.
Проверку следует проводить люминесцентным методом.
Пружины клапанов должны быть подвергнуты 100 % контролю на магнитном дефектоскопе; трещины на пружинах не допускаются.
Зазор между концевыми и рабочими нитками пружин клапанов должен быть не более 0,3 мм при измерении на расстоянии 5-10 мм от конца витка.
Неперпендикулярность опорных поверхностей пружин клапана к их оси в свободном состоянии допускается не более 1° на длине пружин.
При осмотре опорных поверхностей пружин они должны быть плоскими на дуге не менее ¾ окружности концевого витка.
После заворачивания шпилек в головку цилиндров на участках, не имеющих резьбы, допускаются вмятины глубиной до 0,1 мм.
Сухари должны выступать над плоскостью тарелки клапанной пружины не более 1,4 мм; утопать не более 1,8 мм.
Механизм коромысел
Регулировочные винты коромысел должны ввинчиваться в коромысла на всю длину резьбы, а контргайки навертываться на винты туго, но без заеданий.
Твердость поверхности бойка коромысла должна соответствовать 49-57 HRC.
Шероховатость обработанной поверхности бойка должна быть Ra≤0,3 мкм.
Стойки коромысел должны плотно прилегать к опорной поверхности головки цилиндров.
Пробки оси коромысел - должны быть плотно завернуты и обеспечивать герметичность соединений.
Масляные каналы коромысел клапана и оси коромысел должны быть тщательно очищены, промыты и продуты сжатым воздухом.
Коромысла должны свободно, без заеданий проворачиваться на оси коромысел.
Радиальное биение стержня штанги относительно ее сферической поверхности допускается до 0,5 мм.
Неплоскостность поверхности крышки, прилегающей к головке цилиндра, и поверхности крышки, прилегающей к колпаку крышки, допускается не более 0,25 мм на всей длине.
Впускной и выпускной коллекторы
Поверхности фланцев, прилегающих к головке цилиндров, должны находиться в одной плоскости; под нагрузкой не менее 300 Н отклонение от плоскостности допускается не более 0,15 мм (для нового фланца - 0,1 мм).
Внутренние поверхности впускного коллектора должны быть чистыми, без нагара и сажи.