Culata y mecanismo de distribución de gas D-245
La culata es una fundición de hierro fundido, en cuyas cavidades internas hay canales de entrada y salida cerrados por válvulas
Para garantizar la disipación del calor, la culata tiene cavidades internas por las que circula el refrigerante.
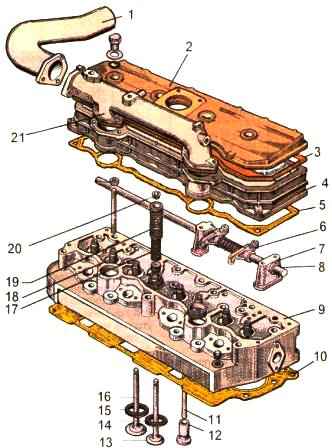
La culata 9 tiene asientos de válvula enchufables 14 y 15 de aleación resistente al calor y al desgaste.
En la parte superior de la culata, se instalan las cremalleras 7, el eje de balancines 8 con los balancines 6, la tapa de la cabeza 4, el colector de admisión y la tapa de la tapa 2, que cierra el mecanismo de la válvula.
Cuatro inyectores están instalados en el cabezal del lado de la bomba de combustible y un colector de escape está conectado al cabezal del lado del generador.
Para sellar el conector entre la culata y el bloque de cilindros, se instala una junta 10 fabricada en chapa de acero al amianto.
Los agujeros para las camisas de los cilindros y el paso de aceite están revestidos con chapa de acero.
Al ensamblar el motor diesel en la fábrica, los orificios del cilindro de la junta se bordean adicionalmente con anillos partidos de fluoroplástico.
La culata debe limpiarse de incrustaciones, depósitos de carbón y lavarse.
No se permiten grietas, fugas de tapones tecnológicos.
Durante una prueba hidráulica de la camisa de líquido de la culata bajo una presión de 0,40 ± 02 MPa, no se permiten fugas ni caídas durante 3 minutos.
Después de reemplazar los tapones con fugas, se debe volver a probar la culata para detectar fugas.
La falta de planitud de la superficie de la culata al bloque no debe exceder de 0,1 mm en la longitud de la culata (0,05 mm para una culata nueva).
La planitud de la culata al colector de escape no debe superar los 0,2 mm en toda su longitud (0,1 mm para una culata nueva).
La altura de la culata debe ser como mínimo de 100,7 mm (103-0,22 mm para una culata nueva).
Los agujeros roscados para los espárragos en la culata no deben dañarse.
Los chaflanes de trabajo de los asientos y platos de las válvulas deben mecanizarse con un ángulo de 45 + 0,5.
El descentramiento de la superficie del chaflán de trabajo del asiento en relación con la superficie del manguito guía después del procesamiento no debe exceder los 0,05 mm.
El descentramiento de la superficie del chaflán de trabajo del disco de la válvula en relación con la superficie de la varilla no se permite más de 0,03 mm.
El ancho del chaflán de trabajo del sillín después del procesamiento debe ser de 2,0-2,2 mm.
La altura del collarín cilíndrico del disco de la válvula debe ser de al menos 1,5 mm.
Los asientos de válvula enfriados a -120 °C deben presionarse en la culata calentada a 70 °C.
La protuberancia del casquillo guía sobre el plano de la culata, es decir, el tamaño desde el extremo superior del casquillo guía hasta la superficie del hueco de los cilindros para los resortes de válvula, debe corresponder a 33-1,0 mm.
Las válvulas deben lapearse y sellarse contra los asientos.
La calidad del lapeado debe comprobarse mediante la presencia de una tira anular mate en las superficies cónicas de la válvula y el asiento.
El ancho de la tira debe ser de 15…2,0 mm; No se permiten roturas de tiras.
El ancho del chaflán traslapado del asiento de la válvula debe ser el mismo en toda su longitud; la diferencia en el ancho del chaflán traslapado del asiento no se permite más de 0,5 mm.
La tira de la válvula debe ubicarse a no más de 1,0 mm del borde de la banda cilíndrica del disco de la válvula.
La estanqueidad del ajuste del disco de la válvula al asiento debe verificarse con un dispositivo neumático KI-16311, a una presión de aire de 0,03-0,05 MPa; no se permiten fugas de aire (burbujas).
Se permite verificar la estanqueidad de las válvulas a los asientos vertiendo queroseno en los canales de entrada y salida; No se permiten fugas o la aparición de gotas de queroseno debajo de las placas de válvula durante 2 minutos.
Después de lapear las válvulas en los asientos, la culata y las válvulas deben enjuagarse hasta que la pasta de lapeado se elimine por completo de las piezas.
Los vástagos de válvula en los casquillos guía deben moverse libremente, sin movimientos laterales perceptibles.
Los vástagos de las válvulas deben lubricarse con aceite de motor M-10G2 antes del montaje.
El hundimiento de los planos inferiores de las placas de las válvulas de admisión y escape en relación con el plano inferior de la culata debe estar entre 1,05 y 1,25 mm.
talones cuando se instala en la culata, se permite sellar con zinc o titanio blanco.
Los extremos de los tapones después de presionar no deben sobresalir por encima del plano de la culata.
Se permite la falta de rectitud del vástago de la válvula a lo largo de toda la longitud de no más de 0,022 mm (para una válvula nueva - 0,015).
No se permiten grietas ni rayitas en las superficies de la válvula. El 100% de las válvulas están sujetas a control.
La prueba debe realizarse por el método luminiscente.
Los resortes de las válvulas deben someterse al 100 % de control en un detector de fallas magnéticas; no se permiten grietas en los resortes.
El espacio entre el extremo y las roscas de trabajo de los resortes de válvula no debe ser superior a 0,3 mm cuando se mide a una distancia de 5 a 10 mm del extremo de la bobina.
La no perpendicularidad de las superficies de apoyo de los resortes de válvula a su eje en estado libre no se permite más de 1° a lo largo de los resortes.
Al inspeccionar las superficies de apoyo de los resortes, deben estar planas en un arco de al menos ¾ de la circunferencia de la bobina final.
Después de atornillar los espárragos en la culata, se permiten muescas de hasta 0,1 mm de profundidad en áreas que no tienen roscas.
Las galletas deben sobresalir por encima del plano de la placa del resorte de la válvula no más de 1,4 mm; fregadero no más de 1,8 mm.
Mecanismo de roca
Los tornillos de ajuste de los balancines deben atornillarse en los balancines en toda la longitud de la rosca, y las contratuercas deben atornillarse en los tornillos firmemente, pero sin atascarse.
La dureza de la superficie del percutor del balancín debe corresponder a 49-57 HRC.
La rugosidad de la superficie mecanizada del percutor debe ser Ra≤0,3 µm.
Los balancines deben encajar perfectamente contra la superficie de apoyo de la culata.
Los tapones del eje del balancín - deben estar bien envueltos y asegurar la estanqueidad de las conexiones.
Los canales de aceite de los balancines y los ejes de balancines deben limpiarse a fondo, enjuagarse y soplarse con aire comprimido.
Los balancines deben girar libremente, sin atascarse, sobre el eje de los balancines.
El descentramiento radial del vástago del vástago con respecto a su superficie esférica se permite hasta 0,5 mm.
La falta de planitud de la superficie de la tapa adyacente a la culata y la superficie de la tapa adyacente a la tapa de la tapa no se permite más de 0,25 mm en toda la longitud.
Múltiples de admisión y escape
Las superficies de las bridas adyacentes a la culata deben estar en el mismo plano; bajo una carga de al menos 300 N, la desviación de la planitud no se permite más de 0,15 mm (para una nueva brida - 0,1 mm).
Las superficies internas del múltiple de admisión deben estar limpias, libres de depósitos de carbón y hollín.