Crank angle sensor
The crankshaft timing rotor has 34 teeth, 2 teeth are missing
The crank angle sensor (fig. 1) outputs crankshaft rotation signals every 10°, the missing teeth are used to determine top dead center.
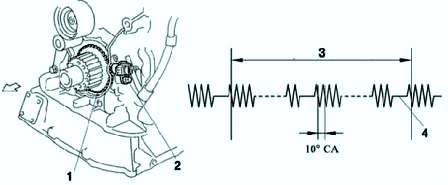
Camshaft position sensor
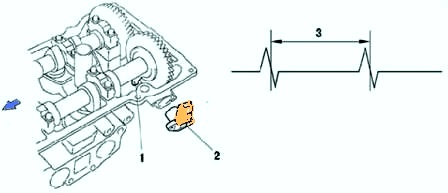
The camshaft position sensor (fig. 2) is mounted on the left cylinder head.
The timing rotor is used to determine the camshaft position, which is used to generate one pulse every 2 revolutions of the crankshaft.
Fuel pedal position sensor
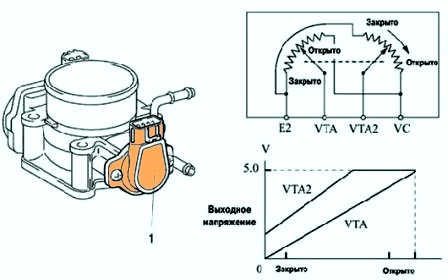
This sensor (fig. 3) converts the throttle angle into electrical signals with two different characteristics and transmits them to the engine's electronic control unit.
One signal (VPA) for voltage ramp over the entire throttle angle range, the other signal (VPA2) for bias voltage.
EFI (Electronic Fuel Injection)
The L-type electronically controlled fuel injection system directly senses the intake air mass using a hot-wire air mass sensor.
An independent injection system is used (in which fuel is injected into each cylinder once every two revolutions of the crankshaft).
In addition, group injection is used when starting the engine (fuel is injected once into two cylinders for each revolution of the crankshaft).
There are two operating modes of the fuel injection system:
- a) synchronous injection, in which the basic injection duration is adjusted according to the signals of the sensors so that fuel injection always occurs at a certain position of the crankshaft;
- b) asynchronous injection, in which fuel is injected when requests are detected from sensor signals, regardless of the angle of rotation of the crankshaft.
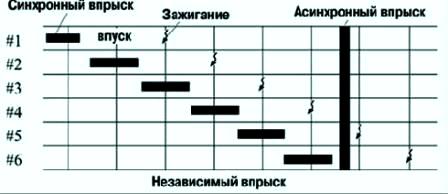
In addition, to protect the engine and increase fuel efficiency, the system performs a fuel cut-off, at which fuel injection is temporarily stopped according to driving conditions.
ETCS-I (Electric Throttle Control System)
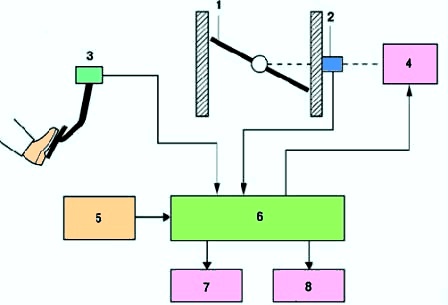
In a conventional throttle valve, throttle opening is uniquely determined by the force on the throttle pedal.
In contrast, with ETCS-i (fig. 5), the ECM calculates the optimum throttle opening angle that suits driving conditions and uses the throttle motor to control the opening.
The throttle cable and lever would removed, and the position sensor is installed on the pedal control.
How it works
The engine ECM operates the throttle motor by setting the target throttle opening angle according to the vehicle's driving mode.
Engine idle speed control
The engine control unit maintains the engine speed at idle at a certain level.
Shock protection when shifting gears
During gear changes, throttle control is synchronized with the ECT (Electronic Controlled Transmission) system to reduce shock loads.
Automatic speed control system
Engine control unit with integrated cruise control electronic control unit, directly actuates the throttle valve for cruise control.
ACIS (Acoustic Induction System Control)
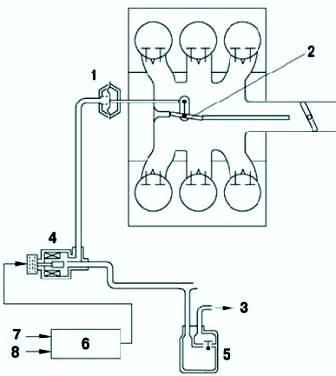
To implement the control of the intake system, a partition is installed in the intake manifold (see Fig. 6), dividing the manifold into 2 chambers.
There is an intake air control valve in the baffle, opening and closing of which can change the effective length of the intake manifold in accordance with the throttle opening angle and engine speed.
This system increases engine power in all operating frequency ranges.
Intake air control valve
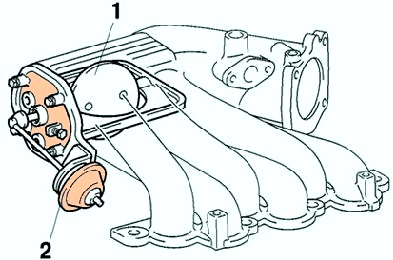
Inlet air control valves (Fig. 7) that are installed in the receiver open and close in two stages to change the effective length of the intake manifold.
VSV (vacuum valve)
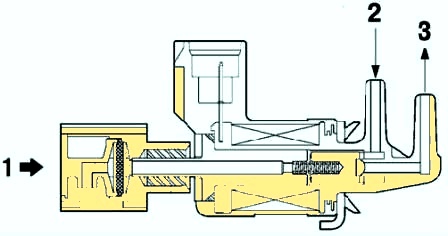
The valve (Fig. 8) controls the vacuum that is supplied to the actuator by a signal (ACIS) from the engine's electronic control unit.
Vacuum reservoir
The vacuum reservoir, equipped with an internal check valve, creates a reserve of vacuum that is applied to the actuator to keep the intake air control valve fully closed, even in low vacuum conditions.
Intake control valve closed (VSV on)
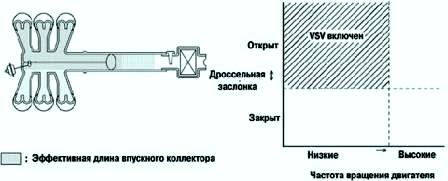
The engine's ECM activates the VSV to increase the duration of the pulsation cycle, while the vacuum acts on the diaphragm of the actuator.
Control valve closes
As a result, the effective length of the intake manifold is increased, and the intake efficiency in the low and medium speed range is improved due to the influence of intake airflow dynamics, thus increasing engine power.
Inlet control valve open (VSV off)
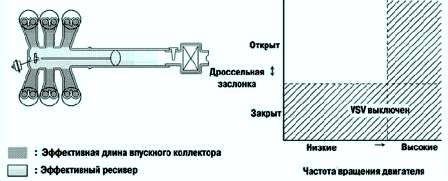
Electric The onboard engine control unit turns off the VSV to reduce the duration of the pulsation cycle, while the diaphragm of the actuator is exposed to atmospheric air and the control valve opens.
When the control valve is open, the effective length of the intake manifold is reduced and peak intake efficiency shifts to the high engine speed region, thus providing more power in this region.