You will need: a portable lamp, a set of flat probes, a ruler, a caliper, a caliper, a micrometer, a scraper
After disassembly, thoroughly wash the parts with kerosene, blow and dry them with compressed air (especially the oil channels of the parts)
- 1. Inspect the block, especially carefully - the crankshaft bearings.
Cracks in any part of the block are not allowed.
If there is a suspicion of cracks in the block (coolant got into the crankcase or oil into the coolant), check the tightness of the block on a special stand.
Perform the check in repair shops with the appropriate equipment.
- 2. Inspect the cylinders on both sides. Scratches, nicks and cracks are not allowed.
When examining cylinders, we recommend that you illuminate the mirrors of the cylinders with a portable lamp - in this case, defects can be seen much better.
- 3. Determine the actual diameters of the cylinders with a bore gauge.
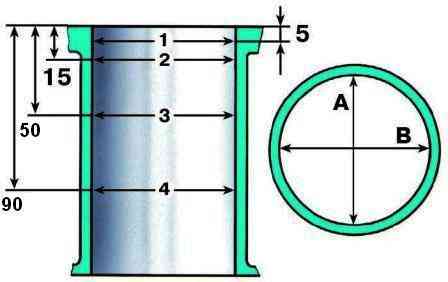
Measure the cylinder diameter in four belts (Fig. 1) located along the height of the cylinder at a distance of 5, 15, 50 and 90 mm from the plane of the connector with the block head.
In each belt, the diameter is measured in two mutually perpendicular directions (longitudinal and transverse).
Cylinders of the block are divided into five classes according to their diameter:
- A = 82.00 - 82.01 mm;
- B = 82.01–82.02 mm;
- C = 82.02-82.03 mm;
- D = 82.03–82.04 mm;
- E = 82.04-82.05 mm
The class of each cylinder of the block, in accordance with the manufacturer's documentation, is stamped on the right side of the lower plane (the plane of the connector with the oil sump).
In accordance with the manufacturer's documentation, a stamp with the conditional number of the cylinder block should be applied on the left side of the lower plane of the block.
The same number must be on all main bearing caps to indicate that the caps belong to this block.
In the zone of the first belt (at a distance of 5 mm from the plane of the connector with the block head), the cylinders practically do not wear out.
By the difference in size in the first and other zones, one can judge the wear of the cylinders.
If the maximum wear value is greater than 0.15 mm, bore the cylinders to the nearest piston oversize (increased by 0.4 or 0.8 mm), leaving an allowance of 0.03 mm for the honing diameter.
Then honing the cylinders, maintaining such a diameter that when installing the selected repair piston, the estimated gap between it and the cylinder is 0.05–0.07 mm.
Troubleshooting, boring and honing of the block should be carried out in workshops with special equipment.
- 4. Check the flatness of the cylinder head connector surface.
Apply a caliper (or ruler) to the plane: in the middle of the block; in transverse and longitudinal directions; along the diagonals of the plane.
In each position, use a feeler gauge to determine the gap between the caliper and the plane.
This will be the deviation from flatness. If the deviation exceeds 0.1 mm, replace the block.
- 5. Remove carbon from the piston bottom with a scraper (can be made from an old file).
- 6. Remove carbon deposits from the piston ring grooves with the old ring by rotating it.
- 7. Inspect pistons, connecting rods, covers: they should not be cracked.
- 8. Examine the earbuds.
If you find risks, scuffs and delamination of the anti-friction layer on the working surface, replace the liners with new ones.
All connecting rod bearings are the same and interchangeable.
- 9. Measure the diameter of the pistons in a plane perpendicular to the axis of the piston pin, at a distance of 52.4 mm from the piston crown.
Based on the measurement results, determine the clearance between the piston and the cylinder and fit new pistons to the cylinders if necessary.
The calculated clearance between the piston and the cylinder (for new parts) is 0.05–0.07 mm.
It is determined by measuring the cylinders and pistons and provided with the installation of pistons of the same class as the cylinders.
Maximum allowable clearance (when parts are worn) 0.15 mm.
If a used engine has a gap exceeding 0.15 mm, it is necessary to match the pistons to the cylinders: the gap should be as close as possible to the calculated one.
- 10. Insert an oil-lubricated finger into the bore of the piston boss.
The pin rotates freely in the piston bosses and in the upper head of the connecting rod.
According to the outer diameter, the fingers are divided into three categories at 0.004 mm.
The category is indicated by paint on the end of the finger:
- 1st (blue mark) - 21.982–21.986 mm;
- 2nd (green label) - 21.986–21.990;
- 3rd (red mark) - 21.990–21.994.
The finger should fit snugly, but without jamming, into the holes of the boss and connecting rod from the effort of the thumb.
- 11. Turn the piston vertically with the axis of your finger.
The finger must not fall out of the boss.
Replace the finger that falls out of the boss with another one of the next category.
If there is a Category 3 pin in the piston, replace the piston with the pin.
- 12. Check the height gap between the grooves in the piston and the rings with a flat feeler gauge by inserting the ring into the corresponding groove.
The nominal (calculated) clearance is:
- - for the upper (first) compression ring 0.04–0.07 mm;
- - for the second compression ring 0.03–0.06 mm;
- - for oil scraper ring 0.02–0.05 mm.
Maximum allowable gaps for wear - 0.15 mm.
- 13. Check the gap in the lock of the rings with a flat feeler gauge by installing the ring in the cylinder to a depth of about 50 mm.
To install the ring without misalignment, push the ring deep into the cylinder with the piston.
The gap is checked for rings inserted into a special gauge having a hole diameter equal to the nominal diameter of the ring with a tolerance of ±0.003 mm.
Gap should be 0.25-0.45 mm for all new rings.
The maximum wear gap is 1.0 mm.
In the absence of a caliber, it is permissible to use the method shown.
If there is not enough clearance, saw off the joint surfaces of the ring. If the gap exceeds the limit, replace the ring.
- 14. If possible, check the mass of the pistons: for one engine, they should not differ from each other by more than ± 2.5 g.
They can be weighted down by removing the metal at the location shown on both sides of the piston.
The metal removal depth should not exceed 4.5 mm, based on the nominal piston height of 59.4 mm.
- 15. Measure the inner diameter D in the seat of the connecting rod assembly with the cover with a caliper.
Tighten the nuts of the connecting rod bolts to the specified torque before measuring
Measure the thickness T of the connecting rod bearings with a caliper
Measure the diameter Dn of the crankpins with a micrometer
- 18. Calculate the gap z between the connecting rod bearings and the crankshaft journals using the formula z=Dв–2T–Dн.
The nominal design gap is 0.02-0.07 mm.
Limit clearance 0.1 mm.
If the actual design gap is less than the limit, you can reuse the liners that were installed.
If the gap is greater than the limit, replace the bearings on these journals with new ones of nominal thickness (1.723–1.730 mm).
If the crankshaft journals are worn and ground to repair size, replace the liners with repair ones (increased thickness):
- "0.25" = 1.848 - 1.855 mm;
- "0.50" = 1.973 - 1.980 mm;
- "0.75" = 2.098 - 2.105 mm;
- "1.0" = 2.223 - 2.230 mm.
The nominal diameter of the connecting rod journals is 47.83–47.85 mm.
The necks are ground if they have nicks and risks or wear (or ovality) is more than 0.03 mm, reducing the diameter in increments of 0.25 mm so as to obtain (depending on the degree of wear) the following values:</ p>
- "0.25" = 47.58 - 47.60 mm;
- "0.50" = 47.33-47.35 mm;
- "0.75" = 47.08 - 47.10 mm;
- "1.0" = 46.83 - 46.85 mm. The designations "0.25" and others indicate how much the diameter of the crankshaft journals decreases after grinding.
- 19. Inspect the upper and lower main bearing shells.
The upper shells of the 1st, 2nd, 4th and 5th main bearings have a groove on the inner surface (the lower ones do not).
The center (3rd) main bearing shells differ from the rest in a larger width, in addition, its upper shell has no groove.
If on the working surface of the liners there are marks, scuffs, delamination of the anti-friction layer, replace the liners with new ones.
It is forbidden to carry out any fitting operations on the liners.
- 20. Inspect the crankshaft. Cracks are not allowed.
On the surfaces mating with the working edges of the seals, there should be no scratches, nicks, scratches. If found, replace the shaft.
- 21. Measure the outer diameter Dn of the main journals with a micrometer.
The actual clearance between the main bearing shells and the crankshaft main journals is determined by the method described for connecting rod bearings.
The nominal design gap is 0.026-0.073 mm.
The limit clearance is 0.15 mm.
If the actual design gap is less than the limit, you can reuse the liners that were installed.
If the gap is greater than the limit, replace the liners on these necks with new ones of nominal thickness (1.824–1.831 mm).
If the crankshaft journals are worn and ground to repair size, replace the liners with repair ones (increased thickness):
- "0.25" = 1.949 - 1.956 mm;
- "0.50" = 2.074 - 2.081 mm;
- "0.75" = 2.199 - 2.206 mm;
- "1.0" = 2.324 - 2.331 mm.
Nominal journal diameter 50.799–50.819 mm.
The necks are ground if they have nicks and risks or wear (or ovality) is more than 0.03 mm, reducing the diameter in increments of 0.25 mm so as to obtain (depending on the degree of wear) the following values:</ p>
- "0.25" = 50.549 - 50.569 mm;
- "0.50" = 50.299 - 50.319 mm;
- "0.75" = 50.049 - 50.069 mm;
- "1.0" = 49.799 - 49.819 mm.
The designations "0.25" and others indicate how much the diameter of the crankshaft journals decreases after grinding.
The corresponding stamp is placed on the first cheek of the crankshaft, for example, K 0.75; W 0.50.
- 22. Install the shaft with extreme main journals on the prisms and check with the indicator:
- - axial runout of the remaining main journals (no more than 0.03 mm);
- - axial runout of the seating surfaces for the sprocket and bearing of the input shaft of the gearbox (no more than 0.04 mm);
- - displacement of the axes of the connecting rod journals from the nominal plane passing through the axes of the connecting rod and main journals (no more than ± 0.35 mm);
- – face runout of the flange on a diameter of 68 mm (no more than 0.025 mm).
Checking the runout in a garage is nearly impossible, so have it done in a workshop with special equipment.
- 23. Inspect sys channel plugs lubrication topics. Check the tightness of their fit with a screwdriver, without applying much force.
If the plugs are not securely installed, replace them. Install the plugs on the UG-6 sealant and caulk in three places.
We do not recommend opening the plugs yourself to clean the channels, which is certainly useful.
Contact workshops with special equipment, or flush the channels without opening the plugs, for which fill the radial channels (shown by arrows) with gasoline, first plugging them on one side with wooden plugs.
Hold for at least 20 minutes and flush the channels with gasoline, injecting it with a rubber bulb.
Remove the wooden plugs after flushing the connecting channels (shown in dotted lines). If necessary, repeat flushing until clean gasoline flows out.