Вам потребуются: переносная лампа, набор плоских щупов, линейка, штангенциркуль, нутромер, микрометр, шабер
После разборки тщательно вымойте детали керосином, продуйте и просушите их сжатым воздухом (особенно масляные каналы деталей)
- 1. Осмотрите блок, особенно внимательно – опоры коленчатого вала.
Трещины в любых местах блока не допускаются.
Если есть подозрение на наличие трещин в блоке (попала охлаждающая жидкость в картер или масло в охлаждающую жидкость), проверьте герметичность блока на специальном стенде.
Проверку проводите в ремонтных мастерских, располагающих соответствующим оборудованием.
- 2. Осмотрите цилиндры с обеих сторон. Царапины, задиры и трещины не допускаются.
При осмотре цилиндров рекомендуем освещать зеркала цилиндров переносной лампой – при этом дефекты видны значительно лучше.
- 3. Определите нутромером фактические диаметры цилиндров.
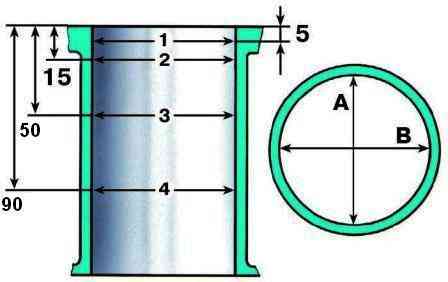
Диаметр цилиндра измеряйте в четырех поясах (рис. 1), расположенных по высоте цилиндра на расстоянии 5, 15, 50 и 90 мм от плоскости разъема с головкой блока.
В каждом поясе диаметр измеряют в двух взаимно перпендикулярных направлениях (в продольном и поперечном).
Цилиндры блока по диаметру подразделяются на пять классов:
- A = 82,00–82,01 мм;
- B = 82,01–82,02 мм;
- C = 82,02–82,03 мм;
- D = 82,03–82,04 мм;
- E = 82,04–82,05 мм.
Класс каждого цилиндра блока в соответствии с документацией завода-изготовителя отмечен клеймом на правой стороне нижней плоскости (плоскости разъема с масляным картером).
В соответствии с документацией завода-изготовителя на левой стороне нижней плоскости блока должно быть нанесено клеймо с условным номером блока цилиндров.
Такой же номер должен быть на всех крышках коренных подшипников для указания принадлежности крышек к данному блоку.
В зоне первого пояса (на расстоянии 5 мм от плоскости разъема с головкой блока) цилиндры практически не изнашиваются.
По разнице размеров в первом и остальных поясах можно судить об износе цилиндров.
Если максимальное значение износа больше 0,15 мм, расточите цилиндры до ближайшего ремонтного размера поршней (увеличенного на 0,4 или 0,8 мм), оставив припуск 0,03 мм на диаметр под хонингование.
Затем отхонингуйте цилиндры, выдерживая такой диаметр, чтобы при установке выбранного ремонтного поршня расчетный зазор между ним и цилиндром был 0,05–0,07 мм.
Дефектовку, расточку и хонингование блока проводите в мастерских, имеющих специальное оборудование.
- 4. Проверьте отклонение от плоскостности поверхности разъема блока с головкой цилиндров.
Приложите штангенциркуль (или линейку) к плоскости: в середине блока; в поперечном и продольном направлениях; по диагоналям плоскости.
В каждом положении плоским щупом определите зазор между штангенциркулем и плоскостью.
Это и будет отклонение от плоскостности. Если отклонение превышает 0,1 мм, замените блок.
- 5. Очистите от нагара днище поршня шабером (можно изготовить из старого напильника).
- 6. Очистите от нагара канавки под поршневые кольца старым кольцом, вращая его.
- 7. Осмотрите поршни, шатуны, крышки: на них не должно быть трещин.
- 8. Осмотрите вкладыши.
Если на рабочей поверхности обнаружите риски, задиры и отслоения антифрикционного слоя, замените вкладыши новыми.
Все шатунные вкладыши одинаковые и взаимозаменяемые.
- 9. Измерьте диаметр поршней в плоскости, перпендикулярной оси поршневого пальца, на расстоянии 52,4 мм от днища поршня.
По результатам замеров определите зазор между поршнем и цилиндром и при необходимости подберите новые поршни к цилиндрам.
Расчетный зазор между поршнем и цилиндром (для новых деталей) составляет 0,05–0,07 мм.
Его определяют промером цилиндров и поршней и обеспечивают установкой поршней того же класса, что и цилиндры.
Максимально допустимый зазор (при износе деталей) 0,15 мм.
Если у двигателя, бывшего в эксплуатации, зазор превышает 0,15 мм, необходимо подобрать поршни к цилиндрам: зазор должен быть максимально приближен к расчетному.
- 10. Вставьте смазанный моторным маслом палец в отверстие бобышки поршня.
Палец свободно вращается в бобышках поршня и в верхней головке шатуна.
По наружному диаметру пальцы делятся на три категории через 0,004 мм.
Категория указывается краской на торце пальца:
- 1-я (синяя метка) – 21,982–21,986 мм;
- 2-я (зеленая метка) – 21,986–21,990;
- 3-я (красная метка) – 21,990–21,994.
Палец должен плотно, но без заедания входить в отверстия бобышки и шатуна от усилия большого пальца.
- 11. Поверните поршень осью пальца вертикально.
Палец не должен выпадать из бобышки.
Выпадающий из бобышки палец замените другим, следующей категории.
Если в поршне палец третьей категории, замените поршень с пальцем.
- 12. Проверьте плоским щупом зазор по высоте между канавками в поршне и кольцами, вставляя кольцо в соответствующую канавку.
Номинальный (расчетный) зазор составляет:
- – для верхнего (первого) компрессионного кольца 0,04–0,07 мм;
- – для второго компрессионного кольца 0,03–0,06 мм;
- – для маслосъемного кольца 0,02–0,05 мм.
Предельно допустимые зазоры при износе – 0,15 мм.
- 13. Проверьте плоским щупом зазор в замке колец, установив кольцо в цилиндр на глубину около 50 мм.
Чтобы установить кольцо без перекоса, продвиньте кольцо вглубь цилиндра поршнем.
Зазор проверяют у колец, вставленных в специальный калибр, имеющий диаметр отверстия, равный номинальному диаметру кольца с допуском ±0,003 мм.
Зазор должен составлять 0,25–0,45 мм для всех новых колец.
Предельно допустимый при износе зазор – 1,0 мм.
При отсутствии калибра допустимо применять показанный способ.
Если зазор недостаточный, спилите стыковые поверхности кольца. Если зазор превышает допустимый, замените кольцо.
- 14. При возможности проверьте массу поршней: для одного двигателя они не должны отличаться друг от друга более чем на ±2,5 г.
Можно подогнать их по массе удалением металла в показанном месте с обеих сторон поршня.
Глубина снятия металла не должна превышать 4,5 мм, считая от номинальной высоты поршня 59,4 мм.
- 15. Измерьте нутромером внутренний диаметр Dв посадочного места шатуна в сборе с крышкой.
Перед измерением затяните гайки шатунных болтов номинальным моментом
Измерьте толщину Т шатунных вкладышей штангенциркулем
Измерьте микрометром диаметр Dн шатунных шеек
- 18. Рассчитайте зазор z между шатунными вкладышами и шейками коленчатого вала по формуле z=Dв–2T–Dн.
Номинальный расчетный зазор составляет 0,02–0,07 мм.
Предельный зазор 0,1 мм.
Если фактический расчетный зазор меньше предельного, можно снова использовать вкладыши, которые были установлены.
Если зазор больше предельного, замените вкладыши на этих шейках новыми номинальной толщины (1,723–1,730 мм).
Если шейки коленчатого вала изношены и перешлифованы до ремонтного размера, замените вкладыши ремонтными (увеличенной толщины):
- «0,25» = 1,848–1,855 мм;
- «0,50» = 1,973–1,980 мм;
- «0,75» = 2,098–2,105 мм;
- «1,0» = 2,223–2,230 мм.
Номинальный диаметр шатунных шеек 47,83–47,85 мм.
Шейки шлифуют, если на них есть забоины и риски или износ (или овальность) составляет более 0,03 мм, уменьшая диаметр с шагом 0,25 мм так, чтобы получить (в зависимости от степени износа) следующие значения:
- «0,25» = 47,58–47,60 мм;
- «0,50» = 47,33–47,35 мм;
- «0,75» = 47,08–47,10 мм;
- «1,0» = 46,83–46,85 мм. Обозначения «0,25» и др. указывают, насколько уменьшается диаметр шеек коленчатого вала после шлифовки.
- 19. Осмотрите верхние и нижние вкладыши коренных подшипников.
Верхние вкладыши 1, 2, 4 и 5-го коренных подшипников имеют канавку на внутренней поверхности (у нижних ее нет).
Вкладыши центрального (3-го) коренного подшипника отличаются от остальных большей шириной, кроме того, его верхний вкладыш не имеет канавки.
Если на рабочей поверхности вкладышей есть риски, задиры, отслоения антифрикционного слоя, замените вкладыши новыми.
Запрещается проводить какие-либо подгоночные операции на вкладышах.
- 20. Осмотрите коленчатый вал. Трещины не допускаются.
На поверхностях, сопрягаемых с рабочими кромками сальников, не должно быть царапин, забоин, рисок. При обнаружении замените вал.
- 21. Измерьте микрометром наружный диаметр Dн коренных шеек.
Фактический зазор между вкладышами коренных подшипников и коренными шейками коленчатого вала определяют по методике, изложенной для шатунных вкладышей.
Номинальный расчетный зазор составляет 0,026–0,073 мм.
Предельный зазор – 0,15 мм.
Если фактический расчетный зазор меньше предельного, можно снова использовать вкладыши, которые были установлены.
Если зазор больше предельного, замените на этих шейках вкладыши новыми номинальной толщины (1,824–1,831 мм).
Если шейки коленчатого вала изношены и перешлифованы до ремонтного размера, замените вкладыши ремонтными (увеличенной толщины):
- «0,25» = 1,949–1,956 мм;
- «0,50» = 2,074–2,081 мм;
- «0,75» = 2,199–2,206 мм;
- «1,0» = 2,324–2,331 мм.
Номинальный диаметр коренных шеек 50,799–50,819 мм.
Шейки шлифуют, если на них есть забоины и риски или износ (или овальность) составляет более 0,03 мм, уменьшая диаметр с шагом 0,25 мм так, чтобы получить (в зависимости от степени износа) следующие значения:
- «0,25» = 50,549–50,569 мм;
- «0,50» = 50,299–50,319 мм;
- «0,75» = 50,049–50,069 мм;
- «1,0» = 49,799–49,819 мм.
Обозначения «0,25» и др. указывают, насколько уменьшается диаметр шеек коленчатого вала после шлифовки.
Соответствующее клеймо ставят на первой щеке коленчатого вала, например К 0,75; Ш 0,50.
- 22. Установите вал крайними коренными шейками на призмы и проверьте индикатором:
- – осевое биение остальных коренных шеек (не более 0,03 мм);
- – осевое биение посадочных поверхностей под звездочку и подшипник первичного вала коробки передач (не более 0,04 мм);
- – смещение осей шатунных шеек от номинальной плоскости, проходящей через оси шатунных и коренных шеек (не более ±0,35 мм);
- – торцовое биение фланца на диаметре 68 мм (не более 0,025 мм).
Проверка биения в гаражных условиях практически невыполнима, поэтому проводите ее в мастерских, имеющих специальное оборудование.
- 23. Осмотрите заглушки каналов системы смазки. Проверьте надежность их посадки отверткой, не прилагая значительных усилий.
Если заглушки установлены ненадежно, замените их. Заглушки установите на герметик УГ-6 и зачеканьте в трех местах.
Не рекомендуем самостоятельно вскрывать заглушки для очистки каналов, которая, безусловно, полезна.
Обратитесь в мастерские, имеющие специальное оборудование, или промойте каналы, не вскрывая заглушки, для чего залейте в радиальные каналы (показаны стрелками) бензин, предварительно заглушив их с одной стороны деревянными пробками.
Выдержите не менее 20 мин и промойте каналы бензином, впрыскивая его резиновой грушей.
Деревянные заглушки снимите после промывки соединительных каналов (показаны пунктиром). При необходимости повторяйте промывку до вытекания чистого бензина.