Before you begin troubleshooting any electrical circuit, carefully study the relevant diagram to understand its function as clearly as possible
The circle of troubleshooting is usually narrowed by gradually identifying and eliminating normally functioning elements of the same circuit.
If several elements or circuits fail at the same time, the most likely cause of the failure is a blown fuse or a broken contact with the "ground" (different circuits in many cases can be closed to one fuse or ground terminal).
Electrical equipment failures are often due to the simplest causes, such as corrosion of connector contacts, fuse failure, fuse blown, or relay damage.
Visually check the condition of all fuses, wiring, and connectors in the circuit before proceeding to a more detailed check of the health of its components.
When using diagnostic tools for troubleshooting, carefully plan (in accordance with the attached electrical diagrams) where and in what sequence the device should be connected in the loop for the most effective troubleshooting.
Checking indicators and gauges for cars manufactured before 2003
Oil pressure gauge
To check the oil pressure indicator 23.3829, we remove the instrument cluster (see Removing the combination appliances).
Assembling the circuit (Figure 1)
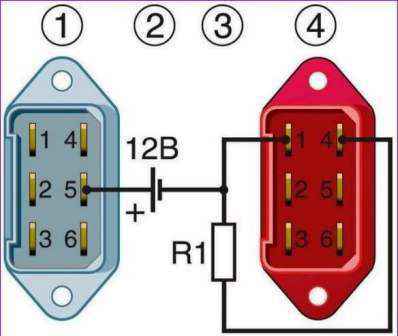
With a resistor of 300 ohms, the arrow of the device should be at the zero mark of the scale, and with a resistance of 180 ohms, at the beginning of the green zone.
With a resistance of 68 ohms, the arrow of the device should move to the beginning of the red zone.
In addition, an emergency oil pressure sensor is installed in the cylinder head, which should open its contacts at a pressure of 40–80 kPa (0.4–0.8 kgf / cm 2).
Coolant temperature gauge
Coolant temperature gauge 37.3807 works in conjunction with a ТМ-106-10 temperature sensor screwed into the cylinder head.
The sensor has a thermistor (a resistor that changes its resistance depending on temperature).
You can check the sensor with an ohmmeter.
A serviceable sensor at a liquid temperature of 20–25 °C (temperature indicator needle at the beginning of the scale) should have a resistance of 1400…1900 Ohm, and at 80 °C (arrow at the border of the green and white zones) - 100…110 Ohm.
The sensor is non-separable and cannot be repaired.
Removing the temperature sensor for ZMZ-402 engines
Disconnect the wire from the output of the temperature gauge sensor
Turn off the sensor with a head of 21
Removing the temperature sensor for engines of the ZMZ-405, ZMZ-406 type
Disconnect the connector block from the sensor output
By unscrewing the 21 sensor from the thermostat housing with a key.
Remove the sensor.
To check the temperature gauge, remove the instrument cluster (see Removing the instrument cluster). We assemble the circuit (Fig. 3).
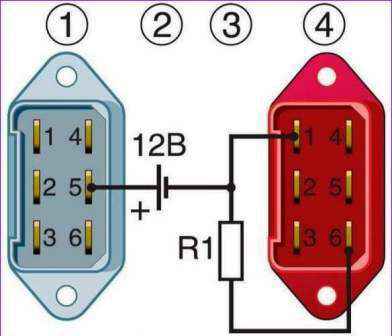
With a resistor of 68 ohms, the arrow of the device should be in the middle of the red zone, at 180 ohms - at the beginning of the green zone, and at 910 ohms - at the beginning of the white zone.
An additional sensor TM 111-02 is additionally installed in the head of the block to signal the overheating of the coolant.
The sensor should work at a liquid temperature of 104 - 109 ° C.
Fuel gauge
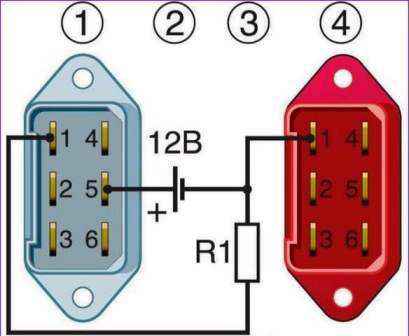
Fuel gauge 32.3806 works together with sensor 5412.3827 installed in the fuel tank.
The sensor is a rheostat with a nichrome wire resistor.
The moving contact of the rheostat is moved by a lever with a float.
At the end of the lever there is an additional contact that closes the circuit of the warning lamp when there is a reserve supply of fuel in the tank.
The correctness of the fuel gauge sensor can be checked with an ohmmeter.
Data for checking the fuel gauge sensor
Amount of fuel in the tank - Sensor resistance, Ohm
- Empty tank 315 - 345
- Half tank 108 - 128
- Full tank 6 – 16
We replace the defective sensor.
To check the fuel gauge, remove the instrument cluster.
Sequentially changing the resistance, we test the pointer.
At 330 ohms, the device should show an empty tank, at 118 ohms - half a tank, and at 11 ohms - a full tank.
Voltmeter
A voltmeter can be checked by comparing its readings with those of a conventional tester used by radio amateurs.
Before testing, we recommend that you hold the voltmeter at 12 V for about 5 minutes.
Failed control devices - we replace, for which we unscrew eight self-tapping screws with a slotted screwdriver
Remove the glass frame
Using the “5.5” head, we unscrew the nuts securing the faulty control device
Removing the device
Install the new device in the instrument cluster in reverse order.