Основными деталями кривошипно-шатунного механизма являются: коленчатый вал 5, поршни 11 с поршневыми кольцами и пальцами, шатуны 8, коренные и шатунные подшипники, маховик 15
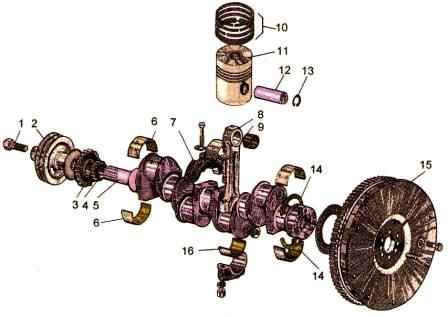
Коленчатый вал - стальной, имеет пять коренных и четыре шатунные шейки.
В шатунных шейках коленчатого вала имеются полости для дополнительной центробежной очистки масла.
Полости шеек закрыты резьбовыми заглушками.
Осевое усилие коленчатого вала воспринимается четырьмя полукольцами 14 из алюминиевого сплава, установленными в расточках блока цилиндров и крышки пятого коренного подшипника.
Для уменьшения нагрузок на подшипники от сил инерции на первой, четвертой, пятой и восьмой щеках коленчатого вала устанавливаются противовесы 7.
Впереди и сзади коленчатый вал уплотняется манжетами.
На передний конец вала устанавливаются шестерня 4 привода газораспределения, шестерня 3 привода масляного насоса, шкив 2 привода жидкостного насоса и генератора.
На задний фланец вала крепится маховик 15.
Коленчатый вал может изготавливаться и устанавливаться на дизель двух производственных размеров (номиналов).
Коленчатый вал, шатунные или коренные шейки которого изготовлены по размеру второго номинала, имеет на первой щеке дополнительную маркировку.
Определение биения шеек коленчатого вала и замер их диаметра показан на рис. 2 и 3.
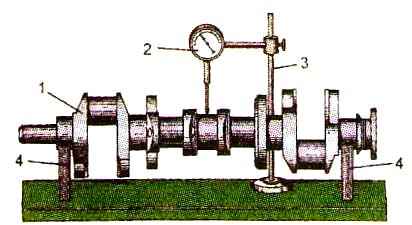
Поршень изготавливается из алюминиевого сплава. В днище поршня находится камера сгорания.
В верхней части поршень имеет четыре канавки (С 1999г. на дизель могут быть установлены поршни с тремя канавками под кольца, то есть с двумя компрессионными кольцами) - в первые три устанавливаются компрессионные кольца, в четвертую - маслосъемное кольцо.
Поршень под верхнее компрессионное кольцо трапецеидальной формы имеет вставку из специального чугуна.
В бобышках поршня расточены отверстия под поршневой палец.
Поршни по наружному диаметру юбки сортируются на три размерные группы (Б, С, М).
Маркировка группы наносится на днище поршня.
При установке на дизель гильзы и поршни должны быть одной размерной группы.
Поршневые кольца изготовлены из чугуна.
Верхнее компрессионное кольцо выполнено из высокопрочного чугуна, хромированное, в сечении имеет форму равнобокой трапеции и устанавливается в канавке любой стороной.
Второе и третье компрессионные кольца — конусные, на торцовой поверхности у замка имеют маркировку верх.
Маслосъемное кольцо коробчатого типа со спиральным стальным расширителем.
Поршневой палец - полый, изготовлен из хромоникелевой стали.
Осевое перемещение пальца в бобышках поршня ограничивается стопорными кольцами.
Шатун - стальной, двутаврового сечения.
В верхнюю головку его запрессована втулка.
Для смазки поршневого пальца в верхней головке шатуна и втулке имеются отверстия.
Расточка постели в нижней головке шатуна под вкладыши производится в сборе с крышкой. Поэтому замена крышек шатуна не допускается.
Шатун и крышка имеют одинаковые номера, нанесенные на их поверхностях.
Кроме того, шатуны имеют весовые группы по массе верхней и нижней головок.
Обозначение группы по массе наносится на торцовой поверхности верхней головки шатуна.
На дизеле должны быть установлены шатуны одной группы.
Вкладыши коренных и шатунных подшипников коленчатого вала - сталеалюминевые.
На дизелях используются вкладыши коренных и шатунных подшипников двух размеров в соответствии с номиналом шеек коленчатого вала.
Для ремонта дизеля предусмотрены также четыре ремонтных размера вкладышей.
Маховик изготовлен из чугуна, крепится к фланцу коленчатого вала болтами.
На маховик напрессован стальной зубчатый венец.
Поршни одного комплекта на дизеле должны быть одной размерной группы, соответствующей размерной группе гильз цилиндров.
Разность массы поршней одного комплекта не должна превышать 10 г.
Разность масс шатунов в сборе с поршнями не должна превышать 30 г.
Некруглость и допуск профиля продольного сечения отверстия втулки верхней головки шатуна — 0,005 мм.
При запрессовке втулки должно быть обеспечено ее симметричное расположение относительно средней плоскости шатуна.
После растачивания поверхность отверстия втулки верхней головки не должна иметь рисок и задиров, шероховатость обработанной поверхности должна быть Ra≤0,63 мкм.
На верхней поверхности втулки допускается одна спиральная или радиальная риска шириной не более 0,1 мм.
На поверхности шатунного болта трещины и риски не допускаются.
Резьба болта должна быть чистой, без забоин и заусенцев.
На поверхности поршневого пальца не должно быть рисок, забоин и трещин.
Разность массы пальцев, устанавливаемых на один дизель, не должна превышать 10 г.
Не смазанный маслом палец должен легко от усилия руки проворачиваться в шатуне, не иметь поперечного качания и не выпадать из шатуна под действием собственной массы (рис. 4).
Вкладыши шатунных подшипников должны быть подобраны в соответствии с размерами шеек коленчатого вала.
Вкладыши должны сидеть в постелях шатунов и крышек с натягом от 0,22 до 0,08 мм.
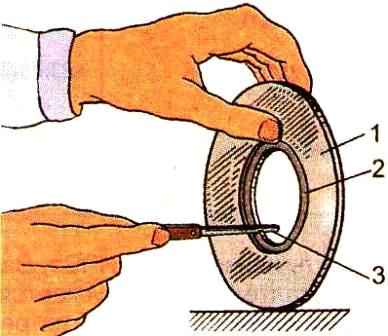
Радиальный зазор (просвет) между поршневым кольцом и контрольным калибром 70-8618- 3515 (рис. 5) для верхнего компрессионного кольца не должен превышать 0,02 мм не более чем на 10 % поверхности и не ближе 20° от замка; а для маслосъемных колец — овальность должна быть в пределах 0,15.0,65 мм.
Зазор в стыке колец должен быть в переделах 0,3…0,6 мм, причем подгонка этого зазора не допускается.
Предел прочности колец при изгибе кольца - не менее 441 Нм.
Коленчатый вал
Правка валов в процессе механической обработки и после закалки ТВЧ не допускается.
Допускается правка только после накатки галтелей. Стрела прогиба вала во время правки должна быть не более 1 мм.
При шлифовании шатунных шеек необходимо сохранять первоначальные радиусы кривошипа (62,5±0,04 мм) и галтелей (4+0,3мм).
Шероховатость обработанных поверхностей шатунных и коренных шеек должна соответствовать Ra≤0,32 мкм.
Некруглость и допуск профиля продольного сечения шатунных и коренных шеек —0,01 мм.
Твердость поверхностей шеек после шлифования должна быть не менее 46 HRCэ.
Закалка галтелей не допускается.
После перешлифовки на ремонтный размер биение средней коренной шейки относительно крайних не должно превышать 0,07 мм (для нового вала - 0,03 мм).
Отклонение от параллельности образующих поверхностей шатунных шеек относительно оси вала, установленного на крайние коренные шейки, не должно превышать 0,03 мм на длине 100 мм.
Смещение всех шатунных шеек относительно диаметральной плоскости 3-й коренной и 3-й шатунной шеек (развал шеек) после перешлифовки не должно превышать 0,3 мм.
Биение цилиндрической и торцовой поверхностей фланца крепления маховика на крайних точках относительно поверхностей крайних коренных шеек допускается до 0,05 мм (для нового вала - не более 0,03 мм).
Трубки должны быть плотно запрессованы в шатунные шейки коленчатого вала; люфт трубок не допускается.
Края развальцованных трубок должны утопать относительно поверхности шеек на 1.3 мм.
Заглушки должны утопать в резьбе не менее чем на 2 мм и быть законтрены.
Шестерня коленчатого вала должна быть напрессована меткой наружу до упора в торец коренной шейки вала.
Коленчатый вал должен быть динамически отбалансирован снятием металла с периферии любых щек.
Остаточный дисбаланс — не более 900 г-мм на каждом конце вала.
Коленчатый вал в сборе с противовесами надо балансировать динамически.
Массу следует корректировать сверлением, в противовесах в радиальном направлении отверстий диаметром 10 мм на глубину не более 25 мм.
Остаточный дисбаланс — не более 650 г/мм на каждом конце вала.
Коленчатые валы после окончательной обработки необходимо проверить с помощью магнитного дефектоскопа на отсутствие поверхностных дефектов.
После проверки валы должны быть размагничены.
Маховик в сборе
Трещины и выкрашивание рабочей поверхности зубьев венца маховика не допускаются.
Уменьшение длины зубьев венца (без длины фаски) допускается до 16 мм (длина зубьев нового венца - 18 мм).
Износ зубьев венца маховика допускается до толщины 3,2 мм, при высоте установки штангензубомера 2,4 мм (толщина зуба нового венца соответствует 4,73 мм).
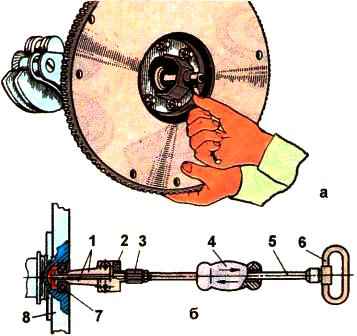
Венец маховика перед напрессовкой необходимо нагреть до температуры 195. .200°С.
Посадочные места маховика и венца не должны иметь забоин и заусенцев.
Допускается зазор в сопряжении между торцовой поверхностью венца и маховика не более 0,5мм В одном месте на дуге не более 60°.
Маховик с венцом надо балансировать динамически в сборе с предварительно уравновешенным коленчатым валом путем сверления радиальных отверстий.
Остаточный дисбаланс на каждом конце вала — не более 350 г/мм.
После балансировки обезличивание деталей не допускается.
Если необходимо заменить передний подшипник первичного вала коробки передач, то перед снятием маховика с вала его следует выпрессовать с помощью винтового съемника мод. И 803.16.000 (рис. 6,а) или, сняв маховик, выпрессовать подшипник с помощью ударного съемника мод. 2476 (рис. 6,б).
Установив захваты на торцы колец подшипника, их раздвигают резьбовым упором 3, а затем, при ударе груза в упор вала 5, выпрессовывают подшипник.
Поверхность маховика, сопряженная с поверхностью ведомого диска сцепления, шлифуется.
Шероховатость поверхности должна быть не ниже Ra≤1,0.