Основними деталями кривошипно-шатунного механізму є: колінчастий вал 5, поршні 11 з поршневими кільцями та пальцями, шатуни 8, корінні та шатунні підшипники, маховик 15
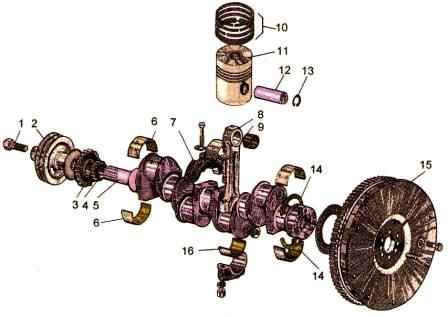
Колінчастий вал - сталевий, має п'ять корінних і чотири шатунні шийки.
У шатунних шийках колінчастого валу є порожнини для додаткового відцентрового очищення олії.
Порожнини шийок закриті різьбовими заглушками.
Осіве зусилля колінчастого валу сприймається чотирма півкільцями 14 з алюмінієвого сплаву, встановленими в розточках блоку циліндрів та кришки п'ятого корінного підшипника.
Для зменшення навантажень на підшипники від сил інерції на першій, четвертій, п'ятій та восьмій щоках колінчастого валу встановлюються противаги 7.
Попереду та ззаду колінчастий вал ущільнюється манжетами.
На передній кінець валу встановлюються шестерня 4 приводу газорозподілу, шестерня 3 приводу масляного насоса, шків 2 приводу рідинного насоса та генератора.
На задній фланець валу кріпиться маховик 15.
Колінчастий вал може виготовлятися та встановлюватись на дизель двох виробничих розмірів (номіналів).
Колінчастий вал, шатунні або корінні шийки якого виготовлені за розміром другого номіналу, має на першій щоці додаткове маркування.
Визначення биття шийок колінчастого валу та замір їх діаметра показаний на рис. 2 та 3.
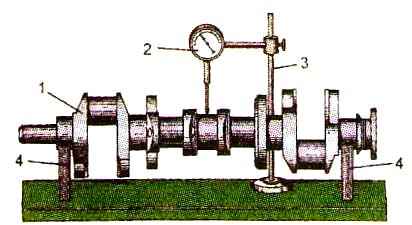
Поршень виготовляється з алюмінієвого сплаву. У днищі поршня знаходиться камера згоряння.
У верхній частині поршень має чотири канавки (З 1999р. на дизель можуть бути встановлені поршні з трьома канавками під кільця, тобто з двома компресійними кільцями) - у перші три встановлюються компресійні кільця, в четверту - кільце знімання.
>
Поршень під верхнє компресійне кільце трапецеїдальної форми має вставку із спеціального чавуну.
У бобишках поршня розточені отвори під поршневий палець.
Поршні по зовнішньому діаметру спідниці сортуються на три розмірні групи (Б, С, М).
Маркування групи наноситься на днище поршня.
При установці на дизель гільзи та поршні повинні бути однієї розмірної групи.
Поршневі кільця виготовлені з чавуну.
Верхнє компресійне кільце виконане з високоміцного чавуну, хромоване, у перерізі має форму рівнобічної трапеції та встановлюється в канавці будь-якою стороною.
Друге та третє компресійні кільця — конусні, на торцевій поверхні біля замку мають маркування верх.
Маслознімне кільце коробчатого типу зі спіральним сталевим розширювачем.
Поршневий палець - порожнистий, виготовлений з хромонікелевої сталі.
Осіве переміщення пальця в бобишках поршня обмежується стопорними кільцями.
Шатун - сталевий, двотавровий переріз.
У верхню головку його запресовано втулку.
Для мастила поршневого пальця у верхній головці шатуна та втулці є отвори.
Расточка ліжка в нижній голівці шатуна під вкладки проводиться у зборі з кришкою. Тому заміна кришок шатуна не допускається.
Шатун та кришка мають однакові номери, нанесені на їх поверхнях.
Крім того, шатуни мають вагові групи по масі верхньої та нижньої головок.
Позначення групи по масі наноситься на торцевій поверхні верхньої головки шатуна.
На дизелі повинні бути встановлені шатуни однієї групи.
Вкладиші корінних та шатунних підшипників колінчастого валу - сталеалюмінієві.
На дизелях використовуються вкладиші корінних та шатунних підшипників двох розмірів відповідно до номіналу шийок колінчастого валу.
Для ремонту дизеля передбачено також чотири ремонтні розміри вкладишів.
Маховик виготовлений із чавуну, кріпиться до фланця колінчастого валу болтами.
На маховик напресовано сталевий зубчастий венец.
Поршні одного комплекту на дизелі повинні бути однієї розмірної групи, що відповідає розмірній групі гільз циліндрів.
Різниця маси поршнів одного комплекту не повинна перевищувати 10 г.
Різниця мас шатунів у зборі з поршнями не повинна перевищувати 30 г.
Некруглість та допуск профілю поздовжнього перерізу отвору втулки верхньої головки шатуна — 0,005 мм.
При запресуванні втулки має бути забезпечене її симетричне розташування щодо середньої площини шатуна.
Після розточування поверхня отвору втулки верхньої головки не повинна мати рисок і задир, шорсткість обробленої поверхні повинна бути Ra≤0,63 мкм.
На верхній поверхні втулки допускається один спіральний або радіальний ризик шириною не більше 0,1 мм.
На поверхні шатунного болта тріщини та ризики не допускаються.
Різьба болта має бути чистою, без вибоїн і задирок.
На поверхні поршневого пальця не повинно бути рисок, вибоїн та тріщин.
Різність маси пальців, що встановлюються на один дизель, не повинна перевищувати 10 г.
Не змащений олією палець повинен легко від зусилля руки провертатися в шатуні, не мати поперечного гойдання і не випадати з шатуна під дією власної маси (рис. 4).
Вкладиші шатунних підшипників мають бути підібрані відповідно до розмірів шийок колінчастого валу.
Вкладиші повинні сидіти в ліжках шатунів та кришок з натягом від 0,22 до 0,08 мм.
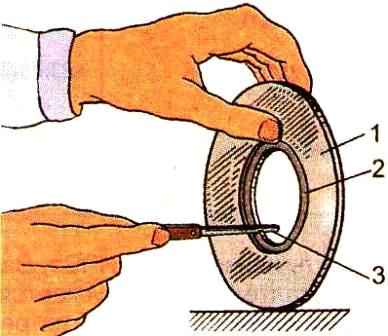
Радіальний зазор (просвіт) між поршневим кільцем і контрольним калібром 70-8618-3515 (рис. 5) для верхнього компресійного кільця не повинен перевищувати 0,02 мм не більше ніж на 10 % поверхні і не ближче 20 ° від замку; а для маслознімних кілець — овальність має бути в межах 0,15.0,65 мм.
Зазор у стику кілець повинен бути в межах 0,3…0,6 мм, причому підгонка цього зазору не допускається.
Межа міцності кілець при вигині кільця - не менше 441 Нм.
Колінчастий вал
Правка валів у процесі механічної обробки та після загартування ТВЧ не допускається.
Допускається редагування тільки після накатки жолобників. Стріла прогину валу під час правки має бути не більше 1 мм.
При шліфуванні шатунних шийок необхідно зберігати початкові радіуси кривошипу (62,5±0,04 мм) та жолобників (4+0,3мм).
Шорсткість оброблених поверхонь шатунних і корінних шийок повинна відповідати Ra≤0,32 мкм.
Некруглість та допуск профілю поздовжнього перерізу шатунних та корінних шийок —0,01 мм.
Твердість поверхонь шийок після шліфування повинна бути не менше 46 HRCе.
Гартування жолобників не допускається.
Після перешліфування на ремонтний розмір биття середньої корінної шийки щодо крайніх не повинно перевищувати 0,07 мм (для нового валу - 0,03 мм).
Відхилення від паралельності утворюючих поверхонь шатунних шийок щодо осі валу, встановленого на крайні корінні шийки, не повинно перевищувати 0,03 мм на довжині 100 мм.
Зміщення всіх шатунних шийок щодо діаметральної площини 3-ї корінної та 3-ї шатунної шийок (розвал шийок) після перешліфування не повинно перевищувати 0,3 мм.
Биття циліндричної та торцевої поверхонь фланця кріплення маховика на крайніх точках щодо поверхонь крайніх корінних шийок допускається до 0,05 мм (для нового валу - не більше 0,03 мм).
Трубки повинні бути щільно запресовані в шатунні шийки колінчастого валу; люфт трубок не допускається.
Краї розвальцьованих трубок повинні потопати щодо поверхні шийок на 1.3 мм.
Заглушки повинні потопати в різьбленні не менше ніж на 2 мм і бути законтреними.
Шестірня колінчастого валу повинна бути напресована міткою назовні до упору в торець корінної шийки валу.
Колінчастий вал має бути динамічно відбалансований зняттям металу з периферії будь-яких щік.
Залишковий дисбаланс — не більше 900 г мм на кожному кінці валу.
Колінчастий вал у зборі з противагами треба балансувати динамічно.
Масу слід коригувати свердлінням, на противагу в радіальному напрямку отворів діаметром 10 мм на глибину не більше 25 мм.
Залишковий дисбаланс — не більше 650 г/мм на кожному кінці валу.
Колінчасті вали після остаточної обробки необхідно перевірити за допомогою магнітного дефектоскопа на відсутність поверхневих дефектів.
Після перевірки вали мають бути розмагнічені.
Маховик у зборі
Тріщини та фарбування робочої поверхні зубців вінця маховика не допускаються.
Зменшення довжини зубців вінця (без довжини фаски) допускається до 16 мм (довжина зубців нового вінця - 18 мм).
Зношування зубців вінця маховика допускається до товщини 3,2 мм, при висоті установки штангензубоміра 2,4 мм (товщина зуба нового вінця відповідає 4,73 мм).
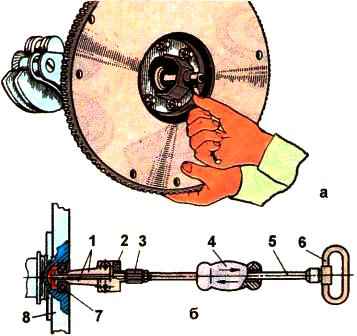
Венок маховика перед напресуванням необхідно нагріти до температури 195. .200°С.
Посадкові місця маховика та вінця не повинні мати вибоїн та задирок.
Допускається зазор у поєднанні між торцевою поверхнею вінця та маховика не більше 0,5мм. В одному місці на дузі не більше 60°.
Маховик з вінцем треба балансувати динамічно у зборі з попередньо врівноваженим колінчастим валом шляхом свердління радіальних отворів.
Залишковий дисбаланс на кожному кінці валу — не більше 350 г/мм.
Після балансування знеособлення деталей не допускається.
Якщо необхідно замінити передній підшипник первинного валу коробки передач, перед зняттям маховика з валу його слід випресувати за допомогою гвинтового знімача мод. І 803.16.000 (рис. 6, а) або, знявши маховик, випресувати підшипник за допомогою ударного знімач мод. 2476 (рис. 6,б).
Встановивши захвати на торці кілець підшипника, їх розсувають різьбовим упором 3, а потім, при ударі вантажу в упор вала 5, випресовують підшипник.
Поверхня маховика, пов'язана з поверхнею веденого диска зчеплення, шліфується.
Шорсткість поверхні повинна бути не нижче Ra≤1,0.