Camry vehicles are equipped with an automatic air conditioning system (fig. 1 and 2)
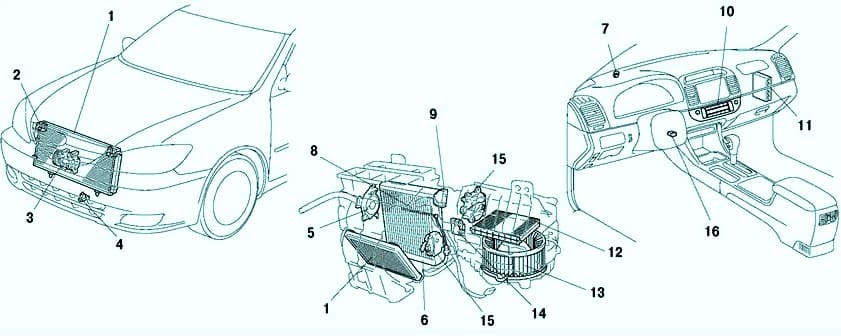
The air conditioning system uses a full-flow aluminum heater core with rectilinear circulation.
Heat transfer efficiency is increased by using an additional evaporator.
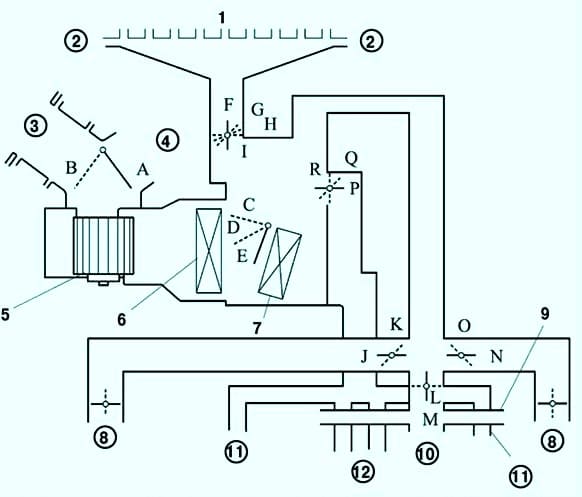
The electronic control unit of the air conditioner has a self-diagnosis function.
A system fault is stored in the DTC memory and the A/C switch indicator flashes
Air conditioning control panel
The air conditioner control panel is push-button with a liquid crystal display, which displays the set temperature, blowing mode and fan speed.
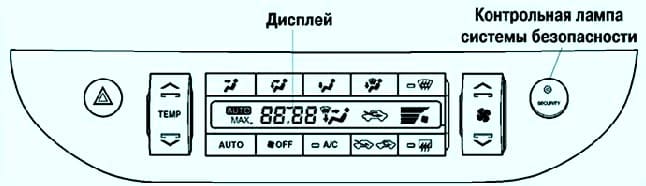
The air conditioning control system maintains a one-way communication between the multi-information display on the center console and the air conditioning electronic control unit using a local protocol.
Air conditioning unit
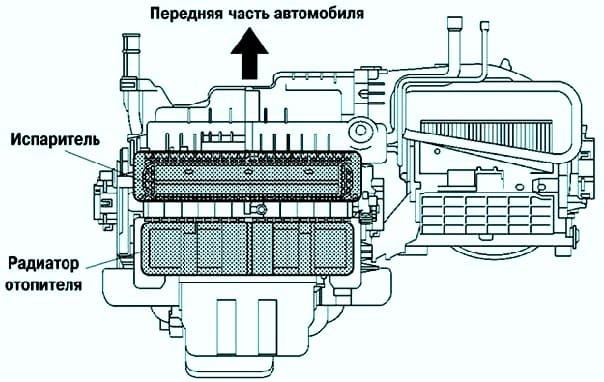
The air conditioning unit consists of an evaporator and a heater radiator.
They are located side by side, in a longitudinal plane relative to the car, thanks to which the air conditioner unit turned out to be compact and lightweight.
Heater radiator
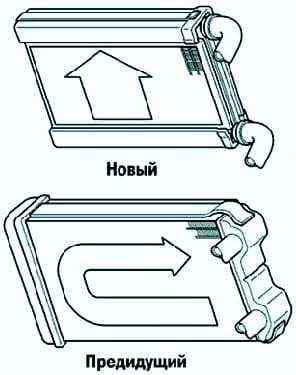
A new compact, lightweight and efficient direct-flow aluminum heater core is used (Fig. 5).
Evaporator
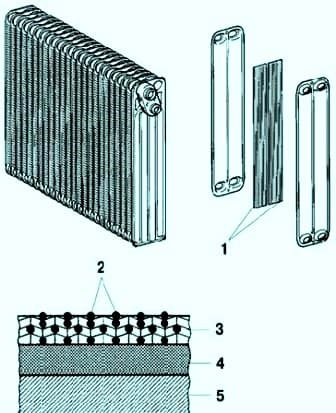
Since 2002, Camry has been using a new type of evaporator (fig. 6), which combines a multi-flow evaporator (consisting of two cooling elements: a condensation element and a subcooling element) and a gas-liquid separator (modulator).</p >
The evaporator body is coated with a polymer that contains an antibacterial agent to eliminate the source of unpleasant odor and the spread of bacteria.
The placement of the tanks at the top and bottom of the evaporator block, as well as the internal design of the plates, made it possible to ensure the following:
- – improved heat transfer efficiency;
- – the temperature distribution has become more uniform;
- – the vaporizer has become thinner.
Evaporator pre-cooling cycle
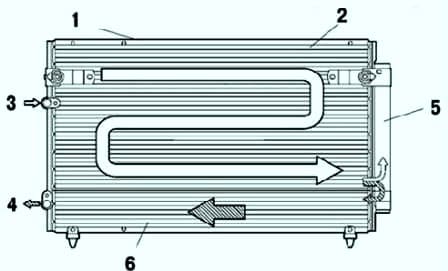
In the adopted pre-cooling cycle (Fig. 7), after the refrigerant passes through the condensing element of the evaporator, the liquid and gaseous refrigerant that could not be liquefied is cooled again in the subcooling element.
Thus, the refrigerant is sent to the evaporator in an almost completely liquefied state.
The point at which air bubbles disappear in the subcooling cycle refrigerant is lower than the corresponding amount of refrigerant to be filled in the system.
Therefore, if the system is recharged with refrigerant at the point where the air bubbles disappear, the amount of refrigerant will be insufficient.
This will affect system performance as a result.
A/C compressor
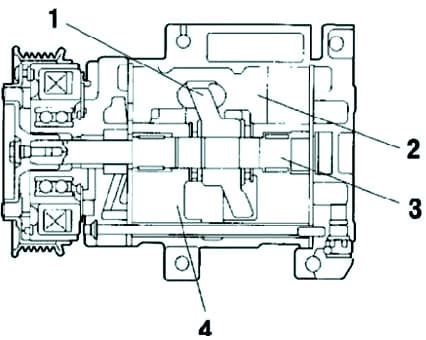
The Camry uses a compact, quiet swashplate compressor (Figure 8).
Quick coupler
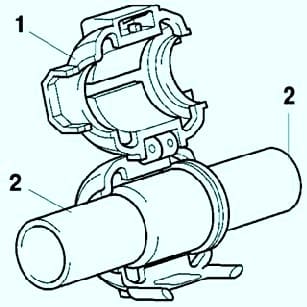
To connect the air conditioning pipes that run from the engine compartment to the passenger compartment, instead of the threaded coupling used on the previous model, a quick-release coupling (Fig. 9) of the clamp type is used.
This ensures ease of maintenance.
Air filter
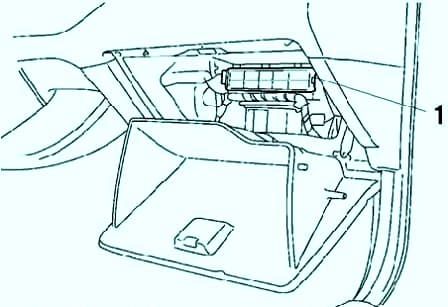
The cabin air filter (fig. 10) is made of polyester and can be easily disposed of as a combustible material.
This feature is dictated by modern environmental protection requirements.
To facilitate filter replacement, the filter cover uses a quick-release clip, the filter cover is integral with the housing.
The frequency of replacing the air filter is 15,000 km.
However, replacement intervals may vary depending on operating conditions (or environment).