Removing, checking and installing Mazda 3 clutch
Remove the gearbox in the final drive unit.
Remove the cover of the clutch release fork.
Remove the clutch release fork assembly.
Remove the clutch release bearing clutch clip.
Remove the clutch release fork support from the transmission.
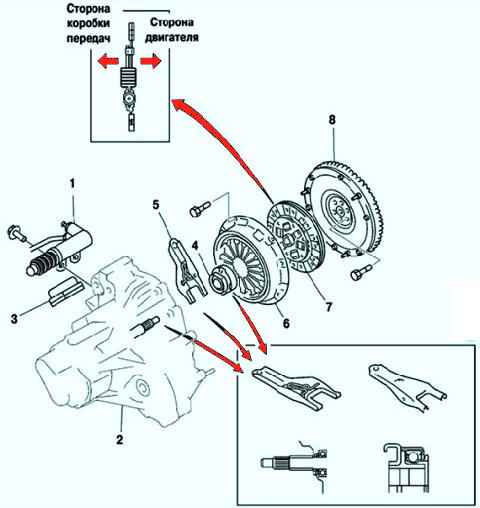
Remove each bolt in one go, one turn, until the spring force is released.
Remove the clutch release bearing clutch clip.
Remove the clutch release fork support from the transmission.
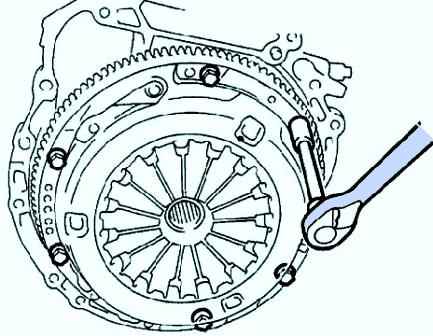
Remove the bolts and clutch cover (fig. 2).
Keep the clutch disc, pressure plate and flywheel surfaces free of oil and foreign objects.
Using the special tool, remove the gearbox input shaft support bearing.
Do not remove the transmission input shaft support bearing unless you are replacing it.
Install a special tool to keep the flywheel from turning.
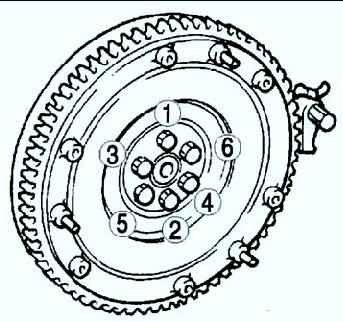
Remove the flywheel mounting bolts in the sequence shown in Figure 3.
Check
Check the clutch cover.
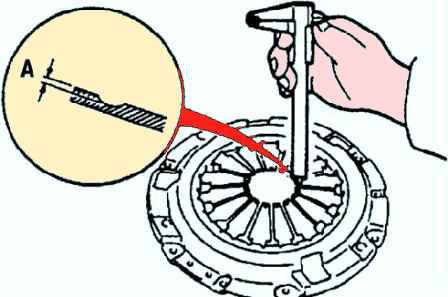
Using a vernier caliper, measure the wear depth of the diaphragm spring petals (fig. 4).
Maximum allowable wear in depth A: 0.6 mm.
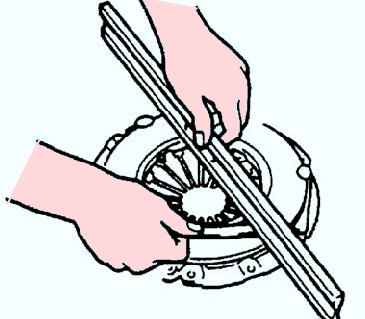
Using a ruler and feeler gauge, measure the gap between the pressure plate and the ruler as shown in Figure 5.
Maximum gap: 0.5 mm.
Install the dial indicator on the cylinder block.
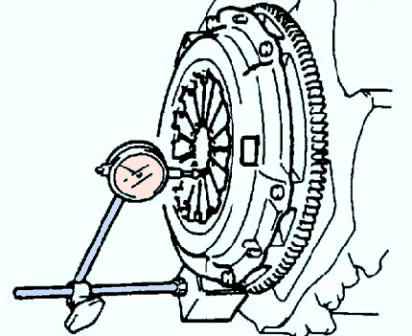
Turning the flywheel, measure the deflection of the tops of the diaphragm spring petals (Fig. 6).
Maximum deviation from plane: 0.6 mm.
If one of the measured values is out of specification, replace the clutch cover.
Check the clutch disc.
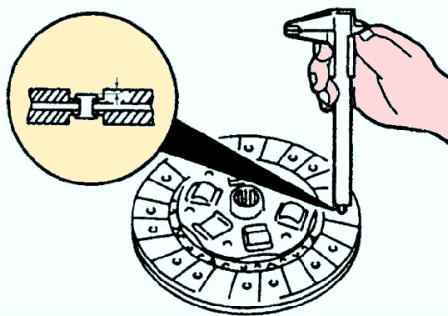
Using a vernier caliper, check the thickness of the friction linings on both sides of the release plate in relation to the rivet heads (fig. 7). Minimum lining thickness: 0.3 mm.
If the lining thickness is less than the minimum, replace the disc.

Using a dial indicator, check the axial runout of the disc (Fig. 8).
Maximum axial runout: 0.7 mm.
If the axial runout is out of specification, replace the disc.
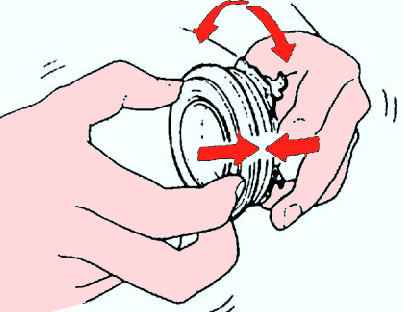
While exerting axial pressure on the release bearing, rotate it (Fig.With. 9).
If the bearing is seizing or there is significant rotational resistance, replace the bearing.
NOTE
The sealed bearing does not require flushing or lubrication.
Turn the gearbox input shaft bearing with thrust.
If the bearing is seizing or there is significant rotational resistance, replace the bearing.
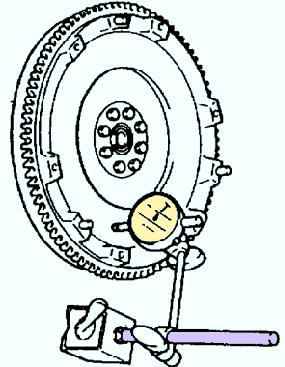
Using a dial gauge, check the axial runout of the flywheel (fig. 10).
Maximum axial runout: 0.2 mm.
If the axial runout is out of specification, replace the flywheel.
Installation
Mount the flywheel to the crankshaft.
When using old bolts, remove any old sealant from the threaded holes for the flywheel bolts in the crankshaft and from the flywheel bolts. Apply sealant to the flywheel mounting bolts and install them.
If installing a new bolt, do not apply sealant to it.
Tighten the flywheel mounting bolts by hand.
Secure the flywheel with a special tool.
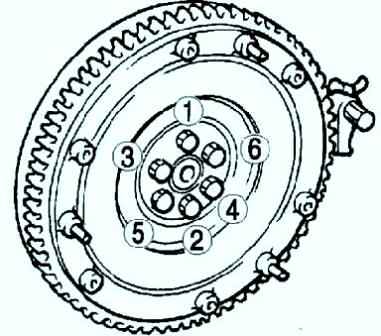
Tighten the mounting bolts in two or three passes in the sequence shown in Figure 11.
Tightening torque: 108-115 Nm.
Using the special tool, install a new transmission input shaft support bearing.
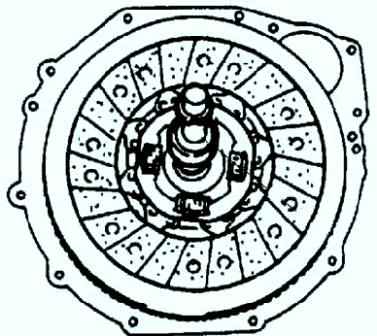
Install the clutch disc and fix its position with the disc centering tool (fig.12.). Install the clutch cover.
Install the special tool.
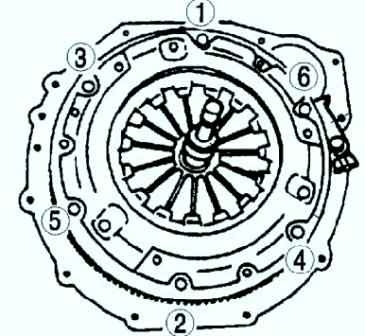
Evenly and gradually tighten the pressure plate mounting bolts in the sequence shown in the figure (fig. 13). Tightening torque: 18.6-25.5 Nm
Install the clutch release fork support in the gearbox.
Install the Clutch Release Bearing clutch clip onto the bearing.
Apply grease to the contact surfaces of the clutch and release fork, the fork and pushrod, and the fulcrum of the fork.
Apply grease to the clutch splines and driveshaft splines.
Install the clutch release fork with the clutch release bearing into the gearbox.
After installation, move the fork back and forth to check that the release bearing moves smoothly.
Install the cover of the clutch release fork.
Install the gearbox.