The ECU is the central unit of the engine management system
The unit is fixed on the rear wall of the battery platform.
An ECU is a special-purpose minicomputer, it consists of a random access memory - RAM and a programmable read-only memory - PROM.
RAM is used for temporary storage of current information about the operation of the engine (measured parameters) and calculated data. Fault codes are also recorded in RAM.
This memory is volatile, i.e. when the power is interrupted (disconnecting the battery or disconnecting the wiring harness from the ECU), its contents are erased.
EPROM stores the engine control program, which contains a sequence of operating commands (algorithms) and calibration data (settings).
PROM determines the most important parameters of engine operation: the nature of the change in torque and power, fuel consumption, ignition timing, composition of exhaust gases, etc. PROM is non-volatile, i.e. its contents do not change when the power is turned off.
The ECU receives information from the sensors of the control system, the switch and pressure sensor of the refrigerant of the air conditioner, the pressure sensor of the power steering, and also controls the actuators, such as the fuel pump, injectors, ignition coils (coil-engine K7M), idle speed controller, electromagnetic canister purge valve, cooling system electric fan, engine overheating alarm, air conditioning compressor electromagnetic clutch, and various system relays.
When the ignition is turned on, the ECU outputs a control signal to the main relay, and when the ignition is turned off, it delays turning off the main relay for the time necessary to prepare for the next turn on (to complete calculations, set the idle speed controller, control the electric fan of the cooling system).
The ECU also performs diagnostic functions for the engine management system (on-board diagnostic system).
The computer determines the presence of malfunctions of the control system elements and stores fault codes in its memory.
If a malfunction is detected, in order to avoid negative consequences (burning of the pistons due to detonation, damage to the catalytic converter in the event of misfires in the air-fuel mixture, exceeding the limits for exhaust gas toxicity, etc.), the computer turns on the malfunction indicator in the instrument cluster and switches the system to emergency operation modes.
Their essence is that in case of failure of any sensor or its circuit, the ECU uses replacement data stored in the PROM to control the engine.
When the ignition is switched on, the ECU activates the control system:
- turns on the fuel pump to create the necessary pressure in the fuel rail and processes the signals from the coolant temperature and throttle position sensors to calculate the composition of the air-fuel mixture when starting the engine.
If during this time the crankshaft does not start cranking, the ECU turns off the fuel pump after 2 seconds and turns it on again after cranking starts.
When the engine is running, the ECU processes information from the sensors:
- crankshaft position, throttle position, coolant temperature, absolute air pressure, intake air temperature, vehicle speed (on a vehicle without ABS), wheel speed (on a vehicle with ABS), oxygen concentration.</p >
The ECU, depending on the engine operating mode, controls the operation of the injectors, ignition coils, idle speed controller, canister purge valve, engine cooling fan.
When the air conditioner is turned on, the ECU increases the engine idle speed and sends a signal to turn on the A/C compressor clutch.
The ECU calculates the ignition timing depending on the engine speed, engine load and coolant temperature.
The composition of the mixture is controlled by the duration of the control pulse applied to the injectors - the longer the pulse, the greater the fuel supply, and vice versa.
Under normal engine operation, fuel is injected alternately into each cylinder at the start of the intake stroke.
To do this, the ECU uses information from the crankshaft position sensor, which determines the TDC of the pistons of the 1st and 4th, as well as the 2nd and 3rd cylinders.
There is no camshaft position sensor (phase sensor) in the system.
Therefore, to determine which of the two cylinders to inject fuel, the ECU uses the following algorithm.
Each time the engine is stopped, the last activated injector is recorded in the ECU memory, and when the engine is restarted, the command is first sent to this injector.
If The fuel is not injected into the cylinder at the start of the intake stroke, the ECU turns on the test program and determines the desired order of fuel injection into the cylinders.
If there is no signal from the crankshaft position sensor (the shaft does not rotate or the sensor and its circuits are faulty), the ECU turns off the fuel supply to the cylinders.
The fuel supply is also turned off when the ignition is turned off, which prevents the mixture from spontaneous ignition in the engine cylinders.
During engine braking (gear and clutch engaged), when the throttle is fully closed and the engine speed is high, no fuel injection is performed to reduce exhaust emissions.
When the voltage drops in the car's on-board network, the ECU increases the energy accumulation time in the ignition coils (for reliable ignition of the combustible mixture) and the injection pulse duration (to compensate for the increase in nozzle opening time).
When the voltage in the on-board network increases, the energy accumulation time in the ignition coils and the duration of the pulse applied to the injectors decrease.
The ECU controls the activation of the cooling fan (via a relay) depending on the engine temperature, engine speed and air conditioning (if installed).
The cooling fan will turn on if the coolant temperature is too high.
Removing the ECM
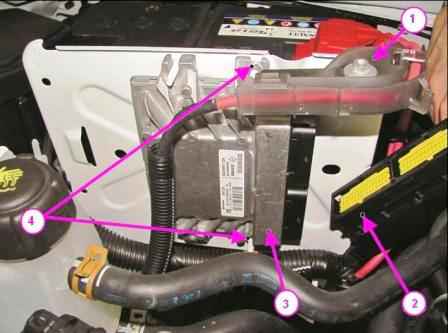
Installing the car to do the job.
The ECM is removed for replacement or when performing vehicle repair operations related to the possibility of harming the electronic components of the unit (for example, when drying the car in a drying chamber after painting, etc.).
Disconnect the wire terminal from the "negative" terminal of the battery.
With a head of 10, we unscrew the fastening bolt, disconnect the bracket 1 and move it to the side.
Disconnect wiring harness connector 2 from ECM 3.
With a head of 10, unscrew the nuts 4 and remove the ECM.
Installation
Install the controller 3, the ECM on the car, install and tighten the nuts 4. The tightening torque of the nuts is 8 Nm (0.8 kgf.m) (replaceable head 10, extension cord, wrench, torque wrench).
Connect the harness connector 2 to the ECM.
Install the bracket 1, install and tighten the bolt of the bracket (replaceable head 10, extension, crank).
Connect the ground wire terminal to the battery.
ECU pin assignment
Contact. Purpose
- Cylinder 2-3 ignition coil control
- Not used
- "Mass"
- Canister Purge Solenoid Valve Control
- Not used
- Not used
- Not used
- Control signal "-" on the engine cooling fan low speed relay
- Coolant temperature warning light
- Control signal "-" on the A/C compressor relay
- Fuel consumption alarm
- Control signal 1 to idle control
- Coolant temperature sensor signal
- Not used
- Ground for absolute pressure sensor
- An absolute pressure sensor signal
- Not used
- Refrigerant pressure sensor signal
- Knock sensor screen
- Knock sensor + signal
- Not used
- Not used
- Not used
- Engine speed signal
- Not used
- Diagnostic connector line L
- Not used
- "Mass"
- "+" after ignition switch
- "+" battery
- Not used
- Ignition coil control for cylinders 1-4
- "Mass"
- Emission control failure warning light
- Not used
- Not used
- Not used
- Control signal "-" on the engine cooling fan high speed relay
- Control signal "-" to the relay winding of actuators
- Not used
- Control signal 2 to idle control
- Control signal 3 to idle control
- Throttle position sensor + signal
- Downstream oxygen sensor signal
- Upstream oxygen sensor signal
- A/C request signal
- Not used
- Not used
- Signal "+" air temperature sensor
- Not used
- Not used
- Not used
- Vehicle speed signal
- Engine speed signal
- Not used
- Diagnostic connector line K
- Not used
- Electronic immobilizer signal
- Control signal "-" to the injector of cylinder No. 1
- Control signal "-" to the injector of cylinder No. 3
- Not used
- Not used
- Control signal "-" to the heating element of the upper oxygen sensor
- Not used
- Control signal "-" to the heating element of the lower oxygen sensor
- "+" after the actuator relay
- Not used
- Control signal "-" to the fuel pump relay coil
- Not used
- Tachometer signal
- Not used
- Control signal 4 to idle control
- "-" coolant temperature sensor
- "+" throttle position sensor
- "-" throttle position sensor
- "Ground" of the downstream oxygen sensor
- "-" air temperature sensor
- "+" absolute pressure sensor
- "-" knock sensor
- Upstream oxygen sensor ground
- Not used
- "-" refrigerant pressure sensor
- "+" refrigerant pressure sensor
- Not used
- Power steering pressure sensor signal
- Not used
- Not used
- Not used
- control signal "-" to the injector of cylinder No. 4
- control signal "-" to the injector of cylinder No. 2
Replacing, programming or reprogramming an ECU
When an ECM is replaced, the new ECM must be programmed.
The computer is programmed using the PB programmer, according to the operating instructions attached to the programmer.
After completing the ECU programming / reprogramming procedure, you must start, then stop the engine (to initialize the ECU) and wait 30 seconds, then turn the ignition back on and use the diagnostic tool to perform the following operations:
- - write the VIN-code of the car into the ECU memory - for this, on the diagnostic tool, select the mode "Additional tests" - "Identification number (VIN)";
- - After programming or reprogramming the ECM, stored faults may appear in the memory of other ECUs, so it is necessary to delete information about faults from the memory of these ECUs;
- - perform the necessary programming (programming the torque of the engine crankshaft and the parameters of the adaptive correction of the composition of the working mixture).
ECM Configuration
The ECU self-configures automatically depending on the presence of sensors and / or optional equipment available on the vehicle.
LC001 Communication type for vehicle speed information
→ Multiplex network
LC003 Upstream oxygen sensor
→ 1 wire
LC004 Downstream oxygen sensor
→ C
LC005 Gearbox type
- → AKP
- → MCP
LC008 Camshaft Phaser
→ WITHOUT
LC032 Read configuration: air conditioning
- → C
- → WITHOUT
LC075 Communication between ABS and injection ECU
→ WITHOUT
LC077 Electronic immobilizer system
→TYPE #3
LC078 Cooling fan control when the engine is running
→ C
LC079 OBD warning light
→ C
LC080 Shift Display
→ WITHOUT
LC090 Low flow fuel pump
→ WITHOUT
LC095 Receipt of information about the operation of the refrigerant circuit of the air conditioner in the injection computer
→ C
LC105 Heated windshield
→ WITHOUT
LC138 Fixed capacity compressor
→ WITHOUT
LC140 Finger type ignition coil
- → C
- → WITHOUT
LC152 Brake light switch NC
→ WITHOUT
LC168 Interior heating element
→ WITHOUT
LC176 DF output
→ WITHOUT
Table of fault codes
Code - Description
- DF001 Coolant temperature sensor circuit
- DF002 Air temperature sensor circuit
- DF022 OBD warning light circuit
- DF023 Coolant temperature warning light circuit
- DF038 ECU
- DF040 No. 1 injector circuit
- DF041 No. 2 injector circuit
- DF042 No. 3 injector circuit
- DF043 No. 4 injector circuit
- DF081 Canister Purge Solenoid Valve Circuit
- DF082 Top oxygen heating circuit one sensor
- DF083 Downstream oxygen sensor heating circuit
- DF084 Actuator relay control circuit
- DF091 Vehicle speed information
- DF092 Upstream oxygen sensor circuit
- DF093 Downstream oxygen sensor circuit
- DF123 Mixture misfires leading to an increase in the content of toxic substances in the exhaust gases
- DF124 Misfire causing catalytic converter failure
- DF232 Refrigerant Pressure Sensor Circuit
- DF328 Throttle Position Sensor Circuit
- DF330 Knock Sensor Circuit
- DF336 Engine speed and position sensor circuit
- DF352 Immobilizer Circuit
- DF353 Absolute Pressure Sensor Circuit
- DF360 Idle control circuit
- DF361 No. 1 and No. 4 ignition coil circuit
- DF362 No. 2 and No. 3 ignition coil circuit
- DF378 Communication of the ABS computer with the injection computer
- DF390 Oxygen sensor malfunction
- DF394 Catalytic converter malfunction
- DF514 Fuel pump relay circuit
- DF524 Actuator relay output voltage
- DF587 Supply voltage + 5V sensors