The controller is the central unit of the engine management system
It receives information from sensors and controls the actuators, ensuring optimal engine operation at a given level of vehicle performance
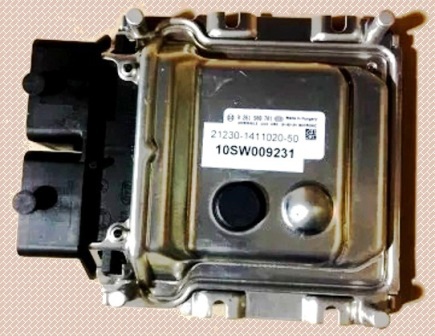
The controller is located in the area of the passenger's feet and is attached to the front panel (Fig. 2).
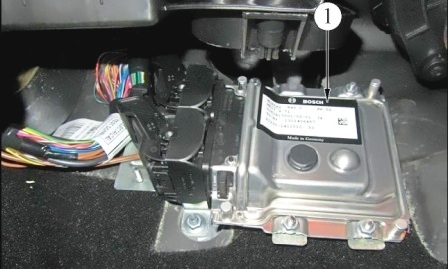
The controller controls actuators such as fuel injectors, motorized throttle, ignition coil, oxygen sensor heater, canister purge valve, and various relays.
The controller controls the on and off of the main relay (ignition relay), through which the supply voltage from the battery is supplied to the elements of the system (except for the electric fuel pump, electric fan, control unit and APS status indicator).
The controller turns on the main relay when the ignition is turned on.
When the ignition is turned off, the controller delays turning off the main relay for the time necessary to prepare for the next turn on (completion of calculations, setting the throttle to the position before starting the engine).
When the ignition is turned on, the controller, in addition to performing the functions mentioned above, exchanges information with the APS (if the immobilization function is enabled).
If the exchange determines that access to the vehicle is allowed, then the controller continues to perform engine control functions. Otherwise, the engine will be blocked.
The controller also performs a system diagnostic function.
It determines the presence of malfunctions of system elements, turns on the alarm and stores codes in its memory that indicate the nature of the malfunction and help the mechanic to carry out repairs.
The controller is a complex electronic device and should only be repaired at the factory.
During the operation and maintenance of the vehicle, disassembly of the controller is prohibited.
Unauthorized modification of the controller software may result in poor engine performance and even damage.
In this case, the warranty obligations of the vehicle manufacturer for the maintenance and repair of the engine and control system are lost.
The controller supplies various devices with 5 or 12 V power supply.
In some cases, it is supplied through the resistors of the controller, which have such a high nominal resistance that when the control light is connected to the circuit, it does not light up.
In most cases, a conventional voltmeter with low internal resistance will not give accurate readings.
To monitor the voltage of the controller output signals, you need a digital voltmeter with an internal resistance of at least 10 MΩ.
Controller memory
The controller has three types of memory: Programmable Read Only Memory (ROM), Random Access Memory (RAM), and Electrically Reprogrammable Memory (EPROM).
Read Only Memory (ROM)
The ROM stores the control program, which contains the sequence of operating commands and calibration information.
Calibration information is injection, ignition, idle control data, etc., which in turn depend on vehicle weight, engine type and power, transmission ratios, and other factors.
This memory is non-volatile, ie. its contents are saved when the power is turned off.
Random Access Memory (RAM)
Random access memory is used by the microprocessor for temporary storage of measured parameters, calculation results, fault codes.
The microprocessor can write or read data into RAM as needed.
This memory is volatile.
When power is interrupted (disconnecting the battery or disconnecting the harness from the controller), the diagnostic trouble codes and calculated data contained in the RAM are erased.
Electrically Reprogrammable Memory (EPROM)
EEPROM is used to store controller, engine and vehicle identifiers, as well as vehicle anti-theft system (ATS) passcodes.
The password codes received by the controller from the APS control unit are compared with the storedmi in EEPROM and are changed by the microprocessor according to a certain law. Diagnostics and fault codes for the Chevrolet Niva ECM with the ME17.9.71 controller
EPROM is a non-volatile memory, its contents are saved when the power is turned off.
Controller replacement
To prevent damage to the controller, when disconnecting the wire from the negative terminal of the battery or the wiring harness from the controller, the ignition must be turned off.
Remove controller
Turn off the ignition.
Disconnect the wire from the negative terminal of the battery.
Unscrew the nuts securing the controller and remove the controller by disconnecting the wiring harness blocks from it.
Only remove the pads from the controller when the controller is removed.
In the event of a controller malfunction, a "clean" controller must be used for replacement
Installing the controller
Connect the wiring harness pads to the controller.
Install the controller on the car.
Connect the wire to the negative terminal of the battery.
Checking the functionality of the controller
After replacing the controller or resetting the controller using the scan tool (mode "5 - Advanced tests; 1 - ECU reset with initialization"), the throttle zero adaptation procedure and the misfire diagnostic function adaptation procedure must be performed.
Throttle Zero Adaptation Procedure:
- with the car at a standstill, turn on the ignition, wait 30 seconds, turn off the ignition, wait for the main relay to turn off.
Adaptation will be aborted if:
- - the engine scrolls;
- - car is moving;
- - accelerator pedal pressed;
- - engine temperature below 5 °С or above 100 °С;
- - ambient temperature is below 5 °С.
Procedure for adapting the misfire diagnostic function:
- - warm up the engine to operating temperature (monitored parameter TMOT_W = 60-90 °С);
- - accelerate the car in 2nd gear until the increased crankshaft speed is reached (NMOT_W = 4000 min -1) and apply engine braking (NMOT_W = 1000 min -1 );
- - perform engine braking six times in one trip.
Perform diagnostics (see the procedure in card A "Checking the diagnostic circuit").
Assignment of controller contacts ME17.9.71 21230-1411020-50
contact - circuit
Connector X1
- 1 Not used.
- 2 Not used.
- 3 Mass of the refrigerant pressure sensor. The voltage on the contact must be zero.
- 4 Mass of analog sensors. Not used.
- 5 Ground for accelerator pedal sensor 1. The voltage on the contact must be zero.
- 6 Accelerator pedal sensor ground 2. The voltage on the contact must be zero.
- 7 Not used.
- 8 Not used.
- 9 Not used.
- 10 Sign in. Refrigerant pressure sensor. The pressure sensor signal is directly proportional to the pressure applied to it, and changes in a straight line between 0.25 V and 3.35 V when the pressure changes from 100 kPa to 2400 kPa.
- 11 Accelerator pedal sensor 2. When the accelerator pedal is released, the signal should be between 0.23-0.38 V. When the accelerator pedal is depressed, the signal increases to 1.40-1.55 V.
- 12 Not used.
- 13 Not used.
- 14 Mass of analog sensors. Not used.
- 15 Exit. main relay. The supply voltage is supplied to the relay winding from the positive terminal of the battery. The control signal is discrete, the active level is low, not more than 1.5 V.
When turning the ignition switch from the "off" to the "on" position, the relay should turn on immediately.
When turning the ignition switch from the "on" to the "off" position, the controller delays turning off the main relay for about 10 seconds.
- 16 Login. Terminal "15" of the ignition switch. The nominal voltage with the ignition on and the engine off is 12 V. With the engine running - 13.5-14.5 V.
- 17 Not used.
- 18 Not used.
- 19 Not used.
- 20 Not used.
- 21 Accelerator pedal sensor 1. When the accelerator pedal is released, the signal should be between 0.46-0.76 V. When the accelerator pedal is depressed, the signal increases to 2.80-3.10 V.
- 22 Not used.
- 23 Not used.
- 24 Not used.
- 25 5V supply for refrigerant pressure sensor. A stabilized voltage of 5 V is applied to the contact.
- 26 5V power supply for accelerator pedal position sensor 2. Stabilized voltage of 5V is applied to the terminal.
- 27 LIN bus. Not used.
- 28 Engine speed signal output to tachometer. Active signal level - low, no more than 1 V.
The high signal level voltage is vehicle electrical system voltage. The pulse repetition rate is equal to twice the engine speed. The active level fill factor is 33%.
- 29 Fuel consumption signal output to the trip computer. Not used.
- 30 Not used.
- 31 A/C relay control output. The control signal is discrete, the active level is low, not more than 1 V, it is issued when the air conditioner is allowed to turn on.
- 32 Not used.
- 33 Not used.
- 34 Air conditioning request signal input. In the absence of a request signal, this pin is connected to ground through the internal resistor of the controller. When the air conditioner switch is turned on, the contact is energized.
- 35 Login. Brake pedal switch 1. When the brake pedal is released, there is voltage on the contact from the terminal "15" of the ignition switch.
- 36 Login. Clutch pedal switch. When the clutch pedal is released, there is voltage on the on-board network from terminal "15" of the ignition switch.
- 37 Power supply 5 V. Not used.
- 38 Accelerator pedal position sensor 5V power supply 1. Stabilized voltage of 5V is applied to the terminal.
- 39 Input/output K-line. Through this contact, the controller exchanges data with the APS control unit and external diagnostic equipment.
Data is transmitted in the form of a pulsed voltage change from a high level (at least 0.8 of the onboard voltage) to a low level (no more than 0.2 of the onboard voltage).
The data exchange session with the APS starts after the ignition is turned on.
If, as a result, the APS is disarmed, the controller enters the normal mode of performing all engine control functions and communicating with diagnostic equipment. Otherwise, the controller disables engine operation and performs only external diagnostic support functions.
- 40 Exit. MIL control lamp. The power supply voltage of the signaling device comes from the terminal "15" of the ignition switch.
When the ignition is turned on without starting the engine, as well as in the presence of malfunctions, the signal has a low voltage level - no more than 2 V. In the absence of malfunctions, the onboard network voltage is present on the contact.
- 41 Engine cooling fan relay 1 control output - reduced performance.
The supply voltage of the fan relay winding comes from the output (terminal "87") of the main relay.
The control signal is discrete, the active level is low, not more than 1 V. The controller turns on the relay when the coolant temperature is above 99 ° C, as well as when there are DTOZH fault codes in the controller memory or when the air conditioner is running.
- 42 Electric fuel pump relay control output. The supply voltage of the relay winding of the electric fuel pump comes from the output (terminal "87") of the main relay. The control signal is discrete, the active level is low, not more than 1 V, it is issued when fuel supply is enabled.
- 43 Not used.
- 44 Not used.
- 45 Not used.
- 46 Not used.
- 47 Login. Switch 2 brake pedals. When the brake pedal is depressed, there is voltage on the contact from the terminal "30" of the ignition switch.
- 48 Not used.
- 49 Not used.
- 50 Not used.
- 51 Control output of auxiliary starter relay. The supply voltage of the auxiliary starter relay winding is supplied from terminal "15" of the ignition switch.
The control signal is discrete, the active level is low, not more than 1 V. When a control signal is received, the additional relay turns on and connects terminal "50" of the ignition switch to terminal "50" of the starter solenoid relay.
- 52 Engine cooling fan relay 2 control output - maximum performance.
The supply voltage of the fan relay winding comes from the output (terminal "87") of the main relay. The control signal is discrete, the active level is low, no more than 1 V.
The controller turns on the relay when the coolant temperature is above 101 ° C, as well as at high refrigerant pressure in the line, both with the air conditioner running and the air conditioner not running
- 53 Mass of output stages. Used to connect the mass of output keys for controlling actuators with the car body.
- 54 Mass of output stages. Used to connect the mass of output keys for controlling actuators with the car body.
- 55 Vehicle voltage input at main relay output. The voltage from the output of the main relay (terminal "87") with the engine off (for an unlimited time after the ignition is turned on without starting the engine, and also within 10 seconds after the ignition is turned off) is 12 V. With the engine running - 13.5-14, 5 V.
- 56 Onboard voltage input at main power output barely. The voltage from the output of the main relay (terminal "87") with the engine off (for an unlimited time after the ignition is turned on without starting the engine, and also within 10 seconds after the ignition is turned off) is 12 V. With the engine running - 13.5-14, 5 V.
Connector X2
- 1 Crankshaft position sensor signal input (terminal "B"). When the engine crankshaft rotates, an AC voltage signal is present on the contact, close in shape to a sinusoid. The frequency and amplitude of the signal are proportional to the crankshaft speed.
- 2 Diagnostic oxygen sensor signal input. If the oxygen sensor has a temperature below 150 ° C (not warmed up), there is a voltage of 1.6 V on the contact.
- When the oxygen sensor is warmed up, when operating in feedback mode and with a working neutralizer in steady state, the voltage should change in the range of 590-750 mV.
- 3 Sign in. Throttle position sensor 1. With the ignition on, the input must have a DC voltage signal, the value of which depends on the degree of throttle opening: with a fully closed damper 0.3-0.6 V.
- 4 Mass of the control oxygen sensor. The voltage on the contact must be zero.
- 5 Weight DTOZH. The voltage on the contact must be zero.
- 6 Diagnostic oxygen sensor ground. The voltage on the contact must be zero.
- 7 Throttle position sensor ground. The voltage on the contact must be zero.
- 8 Mass of analog sensors. Not used.
- 9 Not used.
- 10 Power supply 5 V. Not used.
- 11 Not used.
- 12 Not used.
- 13 Crankshaft position sensor signal input (terminal "A"). When the engine crankshaft rotates, an AC voltage signal is present on the contact, close in shape to a sinusoid. The frequency and amplitude of the signal are proportional to the crankshaft speed.
- 14 Not used.
- 15 DTOZH signal input. The voltage at the contact depends on the temperature of the coolant: at a temperature of 27 ° C, the voltage is about 2.4 V. In the event of an open in the sensor circuit, the voltage at the contact is 5 ± 0.1 V.
- 16 Not used.
- 17 Not used.
- 18 Not used.
- 19 Not used.
- 20 Login. Throttle position sensor 2. With the ignition on, there should be a DC voltage signal at the input, the value of which depends on the degree of throttle opening: with a fully closed damper 4.4-4.7 V.
- 21 Not used.
- 22 Not used.
- 23 5V power for throttle position sensors. A stabilized voltage of 5 V is applied to the contact.
- 24 Not used.
- 25 Not used.
- 26 Not used.
- 27 Login. Intake air temperature sensor. The voltage at the contact depends on the temperature of the air entering the engine: at a temperature of 33 ° C, the voltage is about 1.8 V. In the event of an open in the sensor circuit, the voltage at the contact is 5 ± 0.1 V.
- 28 Not used.
- 29 Not used.
- 30 Control oxygen sensor signal input. If the oxygen sensor has a temperature below 150 ° C (not warmed up), there is a voltage of 1.6 V on the contact.
When the oxygen sensor is warm, with the engine running in closed loop mode, the voltage switches several times per second between a low value of 50-100 mV and a high value of 800-900 mV.
- 31 Phase sensor signal input. In the absence of a signal, the voltage of the onboard network is applied to this contact through the internal resistor of the controller.
The sensor pulses the circuit to ground once per revolution of the camshaft, which makes it possible to recognize the order of operation of the engine cylinders.
- 32 Vehicle speed sensor input. The voltage of the onboard network is supplied to this contact through the internal resistor of the controller.
When the car is moving, the sensor pulses the circuit to ground with a frequency proportional to the speed of the car (6 pulses per meter).
- 33 Mass air flow sensor signal input. The signal is digital with a frequency dependence on the amount of air passing through the MAF (the frequency increases with increasing air flow).
- 34 Not used.
- 35 Canister purge valve control output. The supply voltage for the canister purge valve comes from the output (terminal "87") of the main relay.
The control signal is pulsed, the active level is low, not more than 1 V. The duty cycle varies depending on the engine operating mode in the range of 0-100%.
- 36 Not used.
- 37 Knock sensor signal input 1. The signal is an alternating current voltage, the amplitude and frequency of which depend on the vibrations of the engine block.
- 38 Input 2 sensor signals detonation tick. The signal is an alternating current voltage, the amplitude and frequency of which depend on the vibrations of the engine block.
- 39 Diagnostic oxygen sensor heater control output. The supply voltage for the oxygen sensor heater comes from the output (terminal "87") of the main relay.
The control signal is pulsed, the active level is low, not more than 2 V. The duty cycle varies in the range of 0-100% depending on the temperature and humidity in the area where the sensor is installed.
- 40 Not used.
- 41 Not used.
- 42 Cylinder 2 injector control output. The supply voltage of the injector winding comes from the output (terminal "87") of the main relay.
The control signal is pulsed, the active level is low, not more than 1.5 V. The duration depends on the engine operating mode and ranges from several to tens of milliseconds.
- 43 Cylinder 3 injector control output. The supply voltage of the injector winding comes from the output (terminal "87") of the main relay.
The control signal is pulsed, the active level is low, not more than 1.5 V. The duration depends on the engine operating mode and ranges from several to tens of milliseconds.
- 44 Cylinder 1 injector control output. The supply voltage of the injector winding comes from the output (terminal "87") of the main relay.
The control signal is pulsed, the active level is low, not more than 1.5 V. The duration depends on the engine operating mode and ranges from several to tens of milliseconds.
- 45 Cylinder 4 injector control output. The supply voltage of the injector winding comes from the output (terminal "87") of the main relay.
The control signal is pulsed, the active level is low, not more than 1.5 V. The duration depends on the engine operating mode and ranges from several to tens of milliseconds.
- 46 Control oxygen sensor heater control output. The supply voltage for the oxygen sensor heater comes from the output (terminal "87") of the main relay.
The control signal is pulsed, the active level is low, not more than 2 V. The duty cycle varies in the range of 0-100% depending on the temperature and humidity in the area where the sensor is installed.
- 47 Mass of sensors. The voltage on the contact must be zero.
- 48 Not used.
- 49 Not used.
- 50 Mass of output stages. Used to connect the mass of output keys for controlling actuators with the car body.
- 51 Exit. Throttle actuator "+" (terminal "1").
- 52 Exit. Throttle actuator "-" (terminal "4").
- 53 Not used.
- 54 Primary control output of the ignition coil for cylinders 2-3. The supply voltage of the primary winding of the ignition coil comes from terminal "15" of the ignition switch.
The control signal is pulsed, the active level is low, not more than 2.5 V. The duration depends on the voltage of the onboard network - from several to tens of milliseconds.
- 55 Not used.
- 56 Primary control output for ignition coils 1-4 cylinders. The supply voltage of the primary winding of the ignition coil comes from terminal "15" of the ignition switch.
The control signal is pulsed, the active level is low, not more than 2.5 V. The duration depends on the voltage of the onboard network - from several to tens of milliseconds.