Clean all mating surfaces of the block from gaskets stuck and torn during disassembly
Fix the cylinder block on the stand, carefully inspect the cylinder mirror, if necessary, remove the unworn belt above the upper compression ring with a scraper
The metal should be removed flush with the worn surface of the cylinder.
Remove the oil channel plugs and blow out all oil channels with compressed air.
Put the plugs back in place.
Pick up the crankshaft, to do this, unscrew the plugs of the dirt traps of the connecting rod journals and remove deposits from them, rinse and blow with air, put the plugs in place, tighten them with a torque of 37 ... 51 Nm (3.8 ...5.2 kgcm).
For reliable locking, apply Stopor-9 anaerobic sealant to the threads of the plugs.
Check the condition of the working surfaces of the crankshaft.
Nicks, scuff marks and other external defects are not allowed.
Wipe the bed under the liners in the block and in the main bearing caps with a napkin.
Install the upper main bearing shells (with grooves and holes) in the bed of the block, and the lower ones (without grooves) in the bed of the covers, wipe the shells with a napkin and lubricate them with engine oil.
Wipe the main and connecting rod journals of the crankshaft with a napkin, lubricate them with clean oil and install the crankshaft in the cylinder block.
Lubricate and install thrust bearing half washers:
- - upper - in the grooves of the third root bed with an anti-friction layer with grooves to the cheek of the crankshaft;
- - lower - together with the cover of the third main bearing. The protrusions of the lower half washers must go into the grooves of the cover;
Install the covers of the remaining bearings on the corresponding main journals, wrap and tighten the bolts securing the main bearing caps to a torque of 98...107.9 Nm (10...11kgcm).
On the lower surfaces of 1, 2 and 4 root caps, their serial numbers are embossed.
On the lower surface of the cover of the third main bearing there is a threaded hole for attaching the oil pump holder, and on the side surfaces there are grooves and grooves for installing half washers
The covers of the main bearings are installed according to their numbering, being oriented so that the grooves for the bearing of the liner in the cover and the block are located on one side.
Turn the crankshaft, its rotation should be free with little effort.
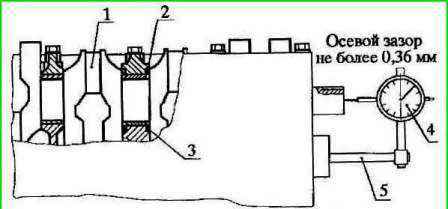
Check the axial clearance of the crankshaft (Figure 1), which should be no more than 0.36 mm.
For unworn crankshaft and thrust bearing half washers, the clearance is 0.06 ... 0.27 mm.
If the axial clearance exceeds the maximum allowable value, replace the thrust washers with new ones and re-measure the axial clearance.
If it is more than 0.36 mm when measured, replace the crankshaft.
Take the oil seal holder with the oil seal of the rear end of the crankshaft, check the suitability of the oil seal for further work.
If the oil seal has worn working edges or weakly covers the crankshaft flange, replace it with a new one.
It is recommended to press the stuffing box into the stuffing box holder using a mandrel.
The oil seal must be installed with the dust boot outside the engine, with the working edge covered by the spring inside.
Before pressing, apply Litol-24 grease to the outer surface of the stuffing box to facilitate pressing.
Fill ⅔ of the cavity between the working edge and the anther of the rubber cuff with CIATIM-221 grease, install and fix the stuffing box with the gasket to the cylinder block.
Install the flywheel on the rear end of the crankshaft, aligning the pin hole in the flywheel with the dowel pin pressed into the crankshaft flange.
Install the washer of the flywheel bolts, screw on and tighten the bolts to a torque of 70.6...78.4 Nm (7.2...8.0 kgcm).
Press the spacer sleeve and bearing into the flywheel seat.
Press in the bearing by applying force to the outer ring.
Pressing on the inner ring will damage the bearing.
Next, we assemble the connecting rod and piston group - article - Engine connecting rod and piston group subassembly.
Attach the holder to the oil pump.
Install the oil pump with gasket on the mating surface of the cylinder block and secure.
Cut off the protruding ends of the gasket protruding above the plane of the block, chain cover and gland holder ok chain cover and stuffing box gasket.
Install and secure the oil sump with gasket and clutch booster.
Lubricate the intermediate shaft bushings with engine oil, fit the slotted key into the groove at the end of the intermediate shaft, and install the intermediate shaft into the cylinder block.
Insert two bolts into the front flange of the intermediate shaft.
Install the gear with nut on the rear end of the shaft, aligning the keyway of the gear with the key, and turning the intermediate shaft with two bolts, tighten the gear nut until it stops.
Install and secure the intermediate shaft flange.
Lubricate the oil pump drive shaft and gear teeth with engine oil and insert the shaft into the hole of the block until the oil pump drive gears and the intermediate shaft engage.
Insert the hexagonal shaft of the oil pump drive into the hole of the drive shaft bushing so that it enters the hexagonal hole of the oil pump shaft.
Install and secure the oil pump drive cover with gasket.
Check for ease of rotation of the intermediate shaft. The shaft should rotate freely, without jamming.
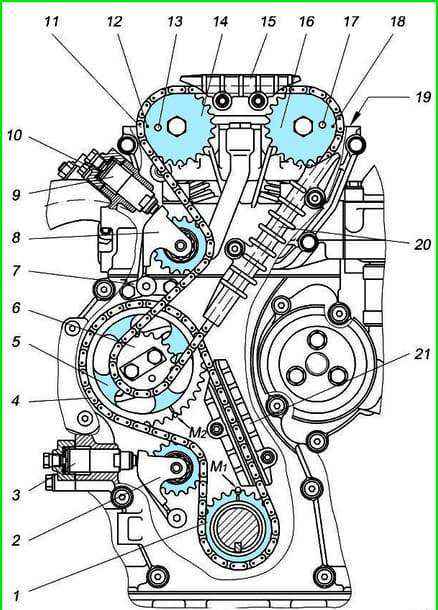
Camshaft drive installation (Picture 2):
Press the segment key into the keyway of the front end of the crankshaft.
Using a special tool, press the sprocket onto the engine crankshaft, orienting the mark forward.
Install the rubber o-ring into the groove of the front end of the crankshaft.
Turn the engine crankshaft until the mark on the crankshaft sprocket matches the mark "M1" on the cylinder block, which will correspond to the position of the piston of the first cylinder at TDC.
In this case, the mark on the cylinder block must be located symmetrically relative to the axis of the cavity of the sprocket teeth.
Install the lower chain damper without completely tightening the fastening bolts, having previously applied anaerobic sealant "Stopper - 6" to the threads of the bolts.
Put the lower chain on the driven sprocket (number of teeth 38) of the intermediate shaft and on the engine crankshaft sprocket.
Install the sprocket with the chain on the intermediate shaft, while the mark on the driven sprocket of the intermediate shaft must match the mark "M2" on the cylinder block, and the leading branch of the chain passing through the damper must be tensioned.
Install the intermediate shaft drive sprocket with pin and fasten both sprockets to the intermediate shaft with bolts to a torque of 24.5...26.5 Nm (2.5...2.7 kgcm).
Bend the two corners of the locking plate on the edges of the bolt heads.
Install the tensioner lever with the sprocket of the lower camshaft drive chain and secure it with the lever bolt, having previously applied Stopor-6 anaerobic sealant to the bolt thread.
Applying too much sealant will extrude it from the threads and immobilize the tensioner arm on the axle.
By pressing the tensioner lever, tighten the chain, check the correct installation of the sprockets according to the marks and tighten the bolts of the lower damper.
After installing the lower chain, the rotation of the crankshaft is not allowed until the camshaft drive chain and hydraulic tensioners are installed.
Install the bolt support of the tensioner lever and fasten it with bolts, having previously applied Stopor-6 anaerobic sealant to the threads of the bolts
Install the tensioner lever with the sprocket of the upper camshaft drive chain and fasten the lever bolt to the support, having previously applied Stopor-6 anaerobic sealant to the bolt thread.
Put the upper camshaft drive chain on the intermediate shaft drive sprocket.
Apply Unisil H50-1 silicone sealant to the cylinder block around the mounting sleeve of the chain cover on the right side of the block (inside which there is an oil supply channel to the lower hydraulic tensioner).
Take the chain cover with the oil seal, check the suitability of the oil seal Ika to further work.
If the oil seal has a worn working edge or weakly covers the hub of the damper pulley, replace it with a new one.

It is recommended to press the oil seal into the chain cover using a mandrel (Figure 3).
The oil seal must be installed with the dust boot outside the engine, the working edge covered by the spring - inside.
Before pressing, apply Litol-24 grease to the outer surface of the stuffing box to facilitate pressing.
Fill the cavity between the working edge and the anther of the rubber cuff of the chain cover with CIATIM-221 grease.
While holding the second stage chain from jumping off the intermediate shaft sprocket, install and secure the chain cover with gaskets and the alternator bracket.
Install and secure the solenoid clutch water pump with gasket to the chain cover by tightening the bolt securing the water pump to the chain cover.
Lubricate the hole for the hydraulic tensioner in the chain cover with clean engine oil used for the engine and install the assembled hydraulic tensioner until it touches the tensioner lever, but do not press it in order to prevent the hydraulic tensioner lock from actuating.
Install a soundproof washer in the cover, close the hydraulic tensioner with a cover with a gasket, insert the bolts (the lower bolt with the synchronization sensor wire fastening bracket) and tighten the cover fastening bolts.
Through the hole in the cover of the hydraulic tensioner, press the hydraulic tensioner with a mandrel, moving it until it stops, then release it, while the retaining ring on the plunger will disengage from the hydraulic tensioner body and allow the plunger and the body to move under the action of the spring.
The body will move to the stop, and the chain will be tensioned through the tensioner lever.
Put the plug into the cover of the hydraulic tensioner, having previously applied Stopor-6 anaerobic sealant to the thread of the plug.
Cut off the ends of the gaskets of the chain cover protruding above the plane of the cylinder block and chain cover.
If there are no rubber seals on the cylinder head gasket in two places that lie on the joints of the chain cover with the cylinder block, Unisil H50-1 silicone adhesive-sealant should be applied to these places of the gasket (window).
Install the cylinder head gasket on the cylinder block pins and chain cover studs.
Install on the water pump nozzle a hose connecting the water pump nozzle to the thermostat housing.
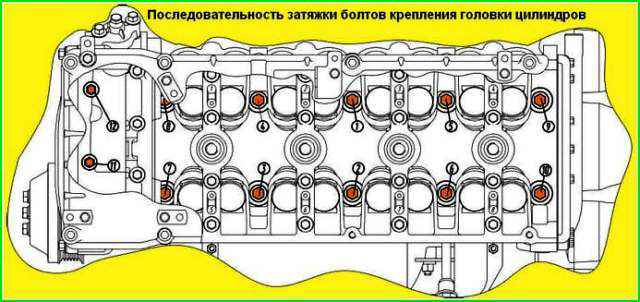
Place the assembled cylinder head on the cylinder block and secure.
Tighten the cylinder head bolts in the sequence shown in Figure 4, in two stages: pre-tighten the bolts to a torque of 40...50 Nm (4.0...5.0 kgf m), then hold for at least 1 ,2 min and finally tighten the bolts by turning 90˚.
Before installing, lubricate the threads of the bolts with engine oil.
Tighten bolts No. 11, 12 to a torque of 19.6...24.5 Nm (2.0...2.5 kgcm).
In order to avoid water hammer when tightening the bolts and the occurrence of cracks in the cylinder block, there must be no oil in the threaded wells of the block.
Unscrew the bolts and remove the camshaft covers, wipe the beds under the camshafts in the head and in the covers with a napkin, lubricate the bolt threads with clean engine oil before installing the covers.
Lubricate the holes in the head for the hydraulic tappets with engine oil and install the hydraulic tappets into the cylinder head.
When repairing the engine without replacing the hydraulic pushers, install them in accordance with their location before disassembly.
If the hydraulic pusher fails, it must be replaced, as it cannot be repaired.
It is necessary to remove the hydraulic pushers with a suction cup or a magnet.
Install the camshafts on the cylinder head, having previously lubricated the beds in the head with the oil used for the engine.
The intake camshaft is installed with the pin on the sprocket up, and the exhaust camshaft with the sprocket pin to the right.
Due to the angular arrangement of the cams, these positions of the camshafts are stable.
Lubricate the bearing journals with clean engine oil.
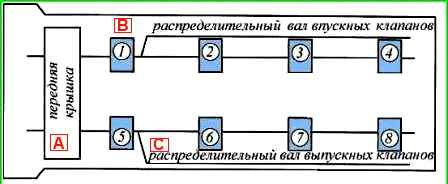
Camshaft covers must be installed according to their numbering (Figure 5), guided by round bosses with numbers for the intake shaft - to the left, exhaust - to the right, when viewed from the front end of the engine.
This orientation is due to the asymmetrical arrangement of the oil channel groove in the covers.
Install the front cover of the camshafts with the thrust flanges installed in it on the mounting sleeves, while due to the longitudinal movement of the camshafts, ensure that the thrust flanges are installed in the grooves.
Before installing, lubricate the thrust flange with clean engine oil used in the engine.
Install covers No. 3 and No. 7 of the camshafts and pre-tighten the bolts of the covers until the surface of the covers touches the upper plane of the cylinder head.
Install all other covers, in accordance with the marking, and tighten the bolts of the covers in advance.
Tighten the camshaft cover bolts finally to 18.6...22.6 Nm (1.9...2.3 kgcm).
Lubricate all camshaft lobes with engine oil and check the rotation of each camshaft in the bearings by turning the camshaft with a wrench using a special square on the camshaft until the valve springs of one of the cylinders are fully compressed.
With further rotation, the camshaft should turn independently under the action of the valve springs until the next cams touch the pushers.
After checking the ease of rotation of the camshafts by turning, orient them so that the locating pins for the sprockets are approximately horizontal and point in different directions (Figure 2).
These camshaft positions are stable and provided by the angular arrangement of the cams.
Start setting the angular position of the camshafts from the exhaust shaft, for this, throwing a drive chain over the sprocket, install the sprocket on the flange and camshaft pin, while turning the camshaft clockwise by the square to match the pin and the hole on the sprocket.
By turning the camshaft anti-clockwise, tighten the drive branch of the chain, while the mark on the sprocket must coincide with the upper plane of the cylinder head. The crankshaft must not be allowed to turn.
For angular installation of the intake camshaft, throw the drive chain over the sprocket, install the sprocket on the flange and the camshaft pin with a slightly slack branch of the chain between the sprockets.
Turn the camshaft counterclockwise to tighten the chain, while the mark on the sprocket should coincide with the upper plane of the cylinder head.
Install and tighten to 54.9 ... 60.8 Nm (5.6 ... 6.2 kgcm) the sprocket mounting bolts, holding the camshafts from turning with a square wrench.
Install the hydraulic tensioner of the upper camshaft drive chain in the same way as installing the hydraulic tensioner of the lower chain.
Install the middle and upper chain guides, tighten, without finally tightening the fastening bolts, having previously applied Stopor-6 anaerobic sealant to the threads of the bolts.
By turning the engine crankshaft in the direction of rotation, tighten the working branches of the upper chain and finally tighten the bolts for securing the middle and upper chain guides.
Install the sleeve on the front end of the crankshaft close to the sprocket, orienting the large internal chamfer to the sealing ring, and the groove under the end of the key towards the front of the engine.
Press the featherkey into the keyway of the front end of the crankshaft so that it fits into the groove of the sleeve as far as it will go with its hemispherical end.
Using a special tool, press the damper pulley onto the front end of the crankshaft until it stops, aligning the keyway of the damper pulley with the key.
Install the tie bolt and tighten to 166.6...215.6 Nm (17...22 kgcm).
At the end of the assembly, check the installation of the camshafts, to do this, turn the engine crankshaft in the direction of rotation two turns until the mark on the crankshaft damper matches the mark on the chain cover.
In this case, the marks on the camshaft sprockets must coincide with the upper plane of the cylinder head.
When repairing the engine associated with the removal of camshafts, cylinder heads and sprockets on the intermediate shaft, install the camshaft drive during assembly as described above.
If the intermediate shaft sprockets and the chain cover are not removed during the repair, then before disassembly, it is necessary to install the piston of the 1st cylinder to the TDC position on the compression stroke, while the risk on the crankshaft damper pulley must coincide with the protrusion on the chain cover, and the marks on the camshaft sprockets must be located horizontally, directed in different directions, and coincide with the upper plane cylinder heads.
After removing the camshafts and the cylinder head, the crankshaft can only be rotated with a return to its original position or with a rotation of 2 turns of the crankshaft.
Turning the crankshaft 1 turn, even if the marks on the pulley and the chain cover match, will lead to incorrect timing.
If the camshafts and sprockets are installed incorrectly, the marks on the sprockets will not match the upper plane of the cylinder head.
In this case, it is necessary to remove the sprockets, turn the crankshaft in the direction of rotation by 1 turn and repeat the installation of the sprockets as described above
Subsequent engine assembly steps
Install and secure the front cylinder head cover with gasket.
Install the thermostat housing into the thermostat hose and secure the thermostat housing with gasket to the cylinder head, tighten the hose clamps.
Press the tube of the oil level indicator rod and install the indicator.
To increase the reliability of installation and tightness, first apply Loctite-638 sealant to the surface of the lower end of the tube.
Install the exhaust manifold with gasket onto the cylinder head studs. Screw on and tighten all but the last manifold mounting nuts.
Install the exhaust manifold shield onto the exhaust manifold studs and secure with nuts.
Install a hose connecting the pump to the water intake pipe on the water pump fitting and secure with a clamp.
Put the bracket on the water intake pipe.
Insert the water intake pipe into the hose, put on the water pump fitting, and put the bracket on the last manifold stud.
Fix the bracket by tightening the nut and tighten the hose clamp.
Install the drain plug of the cylinder block, having previously applied Unisil H50-1 silicone adhesive-sealant or Stopor-6 anaerobic sealant to the thread of the plug.
Install and secure the valve cover with gasket and spark plug well seals. Install the timing sensor connector holder on the valve cover.
Install and secure the upper and lower generator brackets and the front engine lift bracket at the same time.
Install the coolant extraction pipe with gasket.
Preliminarily apply Stopor-6 anaerobic sealant to the thread of the bolts of the branch pipe.
Install and secure the intake pipe with gasket to the cylinder head.
Install the receiver with the gasket on the intake pipe studs and secure with nuts.
Fix the reservoir to the cylinder head using two angle brackets mounted on the cylinder head studs.
First, loosely tighten the screws that secure the brackets to the receiver, then tighten the nuts that secure the brackets to the head and tighten the screws that secure the receiver.
Install the ventilation hose with the ventilation tube and secure with clamps.
Install the hose of the small ventilation branch on the fittings of the ventilation tube and the receiver and secure with clamps.
Install and secure the driven and pressure plates of the clutch, centering the driven plate using a special mandrel.
The gearbox input shaft can be used as a mandrel.
Turn the pressure plate bolts sequentially in several stages to prevent the pressure plate from being skewed up to a moment of 19.6 ... 24.5 Nm (2.0 ... 2.5 kgcm).
Install the release fork pin and studs into the clutch housing.
Install the clutch housing with engine lift bracket on the cylinder block dowel pins and bolt to the cylinder block.
Remove the engine from the stand.
Procedure for installing attachments on the engine
- 1. Lubricate the rubber sealing rings of the injectors with clean engine oil, install the fuel line with the ends of the injectors into the holes in the intake pipe and fix the fuel line.
- 2. Install the emergency oil pressure indicator sensor in the cylinder head, having previously applied Stopor-6 anaerobic sealant to the threaded part of the sensor.
- 3. Install the generator and secure it. First, tighten the nuts of the bolts securing the generator to the upper and lower brackets, then the bolt securing the upper bracket bushing.
- 4. Install the automatic tensioner so that the pin of the device goes into the hole of its fastening boss, and tighten the screw of its fastening, having previously applied Stopor-6 anaerobic sealant to the screw thread.
Then follows:
- - move the tensioner roller with a key by the roller fastening bolt to its extreme position;
- - insert the locking pin (Ø 4 mm and length 55 mm) into the hole of the tensioner to the stop;
- - release the roller, which at the same time the roller pin in the extreme position;
- - put the belt on the pulleys;
- - move the roller slightly with a key, loosening the pin, and remove the pin with pliers;
- - bring the roller to the belt and release the roller. The belt will be tensioned by the tensioner.
- 5. Install the phase sensor in the hole of the cylinder head and fix it with a bolt, having previously lubricated the sealing ring of the sensor with clean engine oil.
The sensor flange must fit snugly against the surface of the block head before bolting.
- 6. Install the timing sensor in the lug hole of the chain cover. Put the sensor wire in the bracket, fixed with the lower bolt of the lower hydraulic tensioner cover, install the connector in the holder on the valve cover.
- 7. Install the knock sensor and secure with a nut and spring washer to a torque of 20 ± 0.5 Nm (2.0 ± 0.05 kgcm).
- 8. Install and secure the throttle with the gasket to the receiver.
- 9. Screw in the spark plugs.
When installing spark plugs, take care not to damage the threads of the spark plug hole in the cylinder head.
Spark plugs should be installed by slightly turning the wrench and then tightened with a torque of 20.0...30.0 Nm (2.1...3.1 kgcm).
- 10. Install the ignition coils and secure with nuts.
- 11. Install the starter and secure with bolts.
- 12. Screw the coolant temperature sensors of the control system and the coolant overheating signaling device into the thermostat housing, having previously applied Stopor-6 anaerobic sealant to the threaded part of the sensors.
- 13. Install the thermal valve with gasket, orienting it with the fitting upwards, and secure the thermal valve with the oil filter fitting.
- 14. Install oil filter.
Before installing the filter, lubricate the rubber gasket of the filter with clean engine oil.
Screw the filter onto the fitting until the gasket touches the bearing surface and then tighten it ¾ turn.