Clean the piston crowns and piston ring grooves from carbon deposits
Pistons in the cylinders of the block must be installed group by group, in accordance with the table
Pistons according to the outer diameter of the skirt and cylinders according to the inner diameter are sorted into three size groups and marked with the letters - A, B, C.
The letter indicating the size group of the cylinder diameter is applied with paint on the outer surface of the cylinder block on the right, opposite each cylinder.
Dimensional groups of cylinder diameters are determined during the manufacture of the cylinder block.
When repairing an engine that has been in operation and has worn cylinders, it is necessary to re-measure the cylinder diameters and determine their group.
Measurements of cylinder diameters should be made at a temperature of plus 20±3˚C.
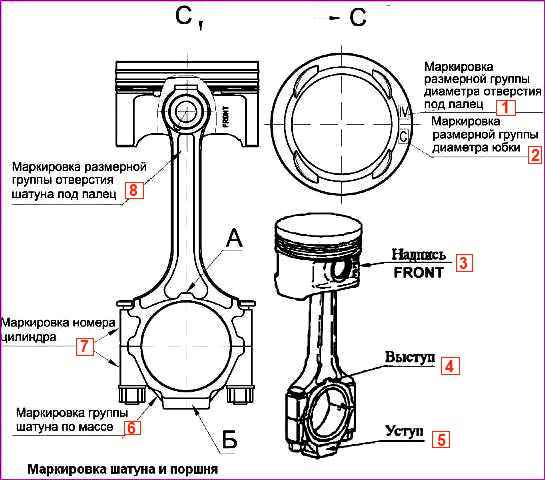
Pistons are marked with letters on the bottom (Figure 1).
The largest diameter of the piston skirt is located in a plane perpendicular to the axis of the piston pin at a distance of 47.5 mm from the piston crown.
Piston skirt diameters should be measured at a piston temperature of plus 20 ± 3 °C.
Pins by outer diameter, connecting rods and pistons by pin hole diameter are sorted into four size groups, which are marked with paint or Roman numerals (Table 1).
The size group of the connecting rod hole for the finger is marked with paint on the rod in the area of the piston head.
The group of the piston bore is indicated by Roman numerals stamped on its bottom (Figure 1), and the pin - by Roman numerals stamped on the end.
The connecting rod must be assembled with a pin of the same size group.
If the misalignment of the axes of the holes of the piston and crank heads exceeds the maximum allowable value, the connecting rod is deformed and must be replaced.
If the hole in the connecting rod bushing for the pin is worn more than allowed, it is necessary to replace the bushing, make a groove in the bushing for the oil channel and machine the bushing hole for the pin.
Before installing a new bushing, measure the diameter of the connecting rod mounting hole - if the hole is worn out, the connecting rod is rejected.
Pistons, pins and connecting rods should be measured at a temperature of 20±3 °C.
The connecting rods are sorted by weight into three groups and marked with paint on the connecting rod cap (Figure 1).
Marking color:
- - white - corresponds to the mass of the connecting rod 900...905 g;
- - green - 895-900 g;
- - yellow - 890-895
For installation on the engine, you should take connecting rods of the same mass group. Pistons are not sorted by weight.
Check the mass difference of the matched sets of piston, pin, connecting rod and rings, which should not exceed 10 g.
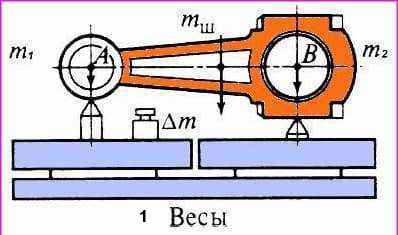
If there is a greater difference in the masses of the sets, in order to eliminate increased engine vibrations, it is necessary to equalize the mass of the sets, to do this, remove the metal from the connecting rods of heavier sets from the weight bosses of the piston or crank heads, depending on the weight of the heads, to a size not less than that shown in the figure 3.
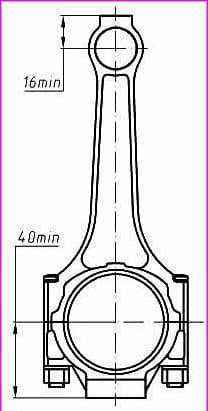
When removing material, the mass of the connecting rod heads should not exceed the following limits: piston (m1) - 211-217 g, crank (m2) - 679 ... 688 g.
Lubricate the piston pin with engine oil and insert into the piston and connecting rod bores.
The connecting rods and pistons, when assembled with the piston pin, must be oriented as follows: the inscription "Front" (front), located on the outer side of the boss under the finger and the protrusion "A" on the crank head of the connecting rod must be directed in one direction.
The connecting rod cap on the connecting rod must be installed so that the ledge "B" on the connecting rod cap and the ledge "A" on the crank head or knock out Cylinder numbers or grooves for liners located on the side of the cover and crank head were located on one side (Figure 1).
Rings intended for installation in cylinders of nominal diameter are marked with yellow paint on the upper compression ring.
For installation in cylinders of the first oversize - blue, the second oversize - green.
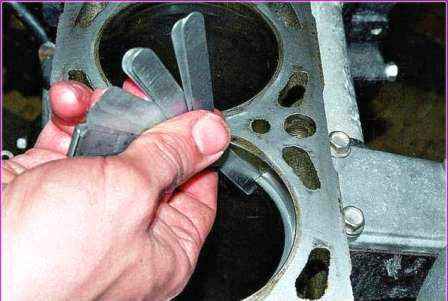
The clearance measured at the joints placed in the cylinder (Figure 4) for new rings should be:
- - 0.25-0.45 mm at the top compression ring;
- - 0.45-0.65 at the lower compression ring;
- - 0.30-0.55 mm at the box-shaped oil scraper ring.
For worn rings, the maximum size in the lock is allowed no more than 1.5 mm.
Place rings for measuring the thermal gap in the lock in the upper unworn part of the cylinder (from the upper edge of the cylinder to the location of the first compression ring when the piston is at TDC) or in a mandrel of the same diameter.
Pre-clean the surface of the cylinder from carbon deposits. Installing piston rings with a smaller thermal gap in the joint will lead to convergence of the joint of the ring during engine operation and nadir of the cylinder.
Installation of worn rings with a large gap will lead to a decrease in compression stroke pressure and increased oil consumption.
Check the backlash between the rings and the wall of the piston groove with a feeler gauge (Figure 6).
Check along the circumference of the piston at several points.
The side clearance for new rings and pistons should be 0.045...0.090 mm.
For worn rings and pistons, a maximum clearance of no more than 0.15 mm is allowed.
A larger clearance will result in increased oil burnout due to the "pumping" action of the rings.
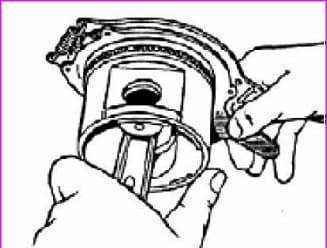
Use the tool (Figure 5) to put the piston rings on the piston.
Install the lower compression ring with the inscription "TOP" (top) on the end towards the piston bottom.
The rings in the grooves must move freely.
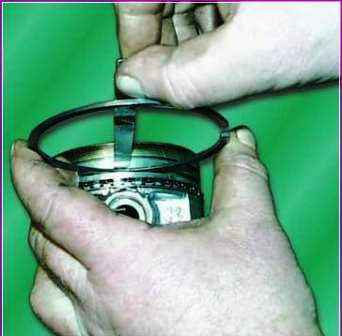
Insert the piston into the cylinders as follows:
- - orient the connecting rod and piston group in such a way that the inscription "FRONT" (front) on the piston boss faces the front of the cylinder block,
- - wipe the beds of the connecting rods and their caps with a napkin, wipe and insert the liners into them,
- - turn the crankshaft so that the cranks of the first and fourth cylinders take the position corresponding to BDC;
- - lubricate the liners, piston, connecting rod journal and the first cylinder with clean engine oil;
- - move the ring locks at an angle of 120° (approximately) to each other, while the joint of the spring expander must be placed opposite the lock of the oil scraper ring box before installing the ring on the piston.
It is recommended not to place the locks of the rings in a plane perpendicular to the axis of the finger;
- - put safety tips on the connecting rod bolts, use a special mandrel with an inner conical surface to compress the rings and insert the piston into the cylinder (Figure 7).
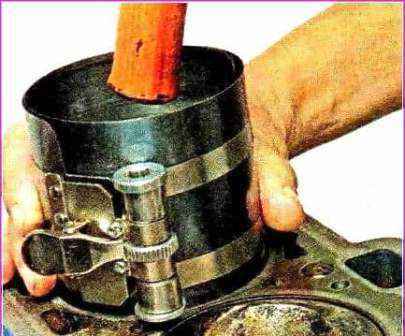
Before installing the piston, you should once again make sure that the numbers stamped on the connecting rod and its cover correspond to the serial number of the cylinder, check the correct position of the piston and connecting rod in the cylinder.
Pull the connecting rod by the crank head to the connecting rod neck, remove the brass tips from the bolts, put on the connecting rod cover.
The connecting rod cover should be placed so that the numbers stamped on the cover and connecting rod, or the grooves for the liners, are on the same side.
Tighten the nuts with a torque wrench to a torque of 68...75 Nm (6.8...7.5 kgcm).
In the same order, insert the piston of the fourth cylinder.
Rotate the crankshaft 180˚ and insert the second and third cylinder pistons.
Turn the crankshaft several times, which should turn easily with little effort.
Dimensional groups for pins, pistons and connecting rods |
||||
---|---|---|---|---|
diameter, mm |
Marking |
|||
Fingers
|
Holes |
Crank
|
Piston and pin |
|
Boss piston |
In the sleeve rod |
|||
21.9935-21.9960 21.9910-21.9935 21.9885-21.9910 21.9860-21.9885 |
21.9975-22.0000 21.9950-21.9975 21.9925-21.9950 21.9900-21.9925 |
22.0045-22.0070 22.0020-22.0045 21.9995-22.0020 21.9970-21.9995 |
white green yellow red |
I II III IV |