Después del desmontaje, instalamos el motor en un soporte para su desmontaje
Retire el generador, la culata, el volante, el filtro de aceite
Con una llave inglesa del 17 destornillamos dos tornillos 1 de la fijación inferior, y con una llave del 13 el tornillo 2 de la fijación superior del soporte del soporte delantero derecho de la unidad de potencia.
Quitar el corchete
Con una cabeza de 13, desenroscamos los tres tornillos que sujetan el soporte del generador.
Retire el soporte del generador.
Retirar el cárter de aceite del motor
Retire el depósito de aceite (consulte Extracción del depósito de aceite) y la bomba de aceite (consulte Extracción y desmontaje de la bomba de aceite).
Habiendo desatornillado los dos pernos que sujetan el tubo de suministro de la bomba de refrigerante al bloque de cilindros con una llave de 10, retire el tubo y su junta de estanqueidad.
Con una cabeza de 10, desenroscamos los seis tornillos que sujetan el prensaestopas
Retire el soporte del sello de aceite trasero
La conexión entre el soporte del sello de aceite y el bloque de cilindros está sellada con una junta
Con cabeza de 14, desenroscamos las dos tuercas de los tornillos que sujetan la tapa de biela (la biela debe estar en PMI)
Golpeando los lados de la tapa de la biela con un martillo de plástico (o metal blando)
Retire la tapa de la biela
Retire el semicojinete de biela de la tapa
Apoyando el mango de madera del martillo contra los extremos de las bielas de los tornillos de biela, desplazamos la cabeza inferior de la biela del cuello del cigüeñal
Retire el pistón con la biela del cilindro.
Retire el semicojinete de biela de la cabeza inferior de la biela.
Del mismo modo, quitamos pistones con bielas de otros cilindros.
Si las partes de la biela y el grupo de pistones no están dañadas y ligeramente desgastadas, se pueden reutilizar.
Por lo tanto, al desmontar, debe marcar las piezas para que puedan instalarse en sus lugares durante el montaje posterior.
Con los dedos, con cuidado (sin mucho esfuerzo) abra la cerradura del anillo de compresión superior
Retire el anillo de la ranura del pistón. Retire el anillo de compresión inferior de la misma manera.
Abriendo la cerradura, retire el anillo rascador de aceite
Retire el expansor del anillo raspador de aceite.
Para quitar el pistón de la biela, haga palanca en el anillo de seguridad del pasador del pistón con un destornillador y retírelo de la ranura anular del buje del pistón.
Retire el otro circlip del pasador del pistón de la misma manera
Expulsar el pasador del pistón con un mandril y quitar el pistón de la cabeza superior de la biela
También retiramos el resto de pistones
Con una cabeza de 17, desenroscamos los dos tornillos que sujetan el sombrerete del cojinete de bancada del cigüeñal.
Retire la tapa del cojinete principal.
Retire el semicojinete principal del cigüeñal inferior de la cubierta.
De la misma manera, retire cuatro tapas de cojinete principal del cigüeñal más.
Retiramos el cigüeñal del bloque de cilindros y luego retiramos los dos medios anillos de empuje del cigüeñal (que se muestran con flechas) de las ranuras del tercer soporte del cojinete principal (en el bloque de cilindros).
Retire los semicojinetes principales del cigüeñal superior de los soportes del bloque de cilindros.
Con una herramienta afilada, retire el sellador restante del plano de contacto del bloque de cilindros debajo del cárter de aceite
Eliminar los restos de la junta de culata.
Limpiamos las superficies de contacto del bloque de cilindros debajo del tubo de la bomba de refrigerante y el soporte del sello de aceite trasero del cigüeñal.
Después de desmontar el motor, lavamos a fondo y limpiamos las partes del grupo cilindro-pistón de depósitos de carbonilla para comprobar su estado técnico.
Para determinar el desgaste del cilindro con un calibre de diámetro, medimos el diámetro del cilindro en cuatro zonas (a una distancia de 8, 15, 50 y 90 mm del plano superior del bloque de cilindros) y en dos direcciones (paralelo y perpendicular al eje del cigüeñal).
En la zona de la primera correa (hasta 8 mm), el cilindro prácticamente no se desgasta. Por tanto, según la diferencia de medidas en el primer y otras correas, puede determinar el desgaste del cilindro.
Si el desgaste de los cilindros supera los 0,15 mm, es necesario perforar y rectificar los cilindros hasta un tamaño de reparación (aumentado en 0,4 o 0,8 mm).
Para determinar el desgaste de la falda del pistón con un micrómetro, medimos su diámetro en un plano perpendicular al eje del bulón, a una distancia de 55 mm del fondo del pistón
Con un micrómetro medimos los diámetros de todos los muñones principales y de biela del cigüeñal en dos planos diametralmente opuestos.
Esmerilamos los muñones del cigüeñal al tamaño de reparación más cercano si el desgaste o la ovalidad es superior a 0,03 mm, y también si hay arañazos y marcas en los muñones.
Después de rectificar los muñones del cigüeñal, se deben quitar los tapones de los canales de aceite.
Luego enjuagamos a fondo y soplamos los canales con aire comprimido para eliminar los residuos abrasivos.
Esmerilado de los muñones del cigüeñal, quitando e instalando tapones.
Montamos el motor en orden inverso.
Instalamos nuevos casquillos de cojinete principal del cigüeñal de tamaño nominal o de reparación (después de rectificar los muñones del eje).
Los insertos con una ranura en la superficie de trabajo se instalan en los soportes del bloque de cilindros, y sin ranuras, en las tapas de los cojinetes principales.
Lubrica las camisas con aceite de motor y coloca el cigüeñal en los soportes del bloque de cilindros.
Introducimos semicojinetes de empuje lubricados con aceite de motor en las ranuras del tercer soporte del cojinete de bancada.
Las superficies de los semianillos con revestimiento antifricción (en ellos se realizan ranuras) deben mirar hacia las superficies de empuje del cigüeñal.
Instalamos los sombreretes de bancada de acuerdo con las marcas impresas en su superficie exterior (los sombreretes se cuentan desde el lado de transmisión por correa de distribución).
Al instalar, oriente las cubiertas de modo que sus marcas estén ubicadas más cerca del lado frontal del bloque de cilindros (lado de montaje del generador).
En este caso, los bloqueos de los casquillos superior e inferior de cada cojinete principal se encuentran en el mismo lado.
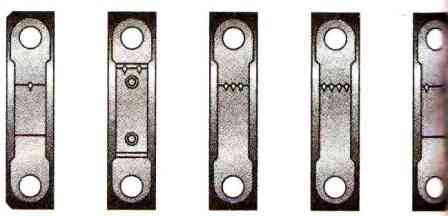
Apretamos los tornillos de las tapas de los cojinetes de bancada con un par de 68 - 84 Nm.
Los pistones para cilindros se seleccionan de acuerdo con las clases de diámetro del cilindro y las faldas del pistón.
La clase de diámetro de cada cilindro (indicada en nuestro caso por la letra "C") está estampada frente al cilindro en el plano inferior del bloque (el plano del accesorio del cárter de aceite).
La clase de faldón del pistón está marcada en la cabeza del pistón. Los pistones de la misma clase de masa están instalados en el motor.
Marca en la cabeza del pistón:
- - d– clase de pistón según el diámetro del orificio del pasador;
- - C – clase de diámetro de la falda del pistón;
- - ↓ - al instalar el pistón en el cilindro, la flecha debe apuntar hacia la transmisión de sincronización;
- - Ã - clase de masa del pistón.
La marca de las clases de biela por masa y diámetro del orificio para el bulón del pistón se aplica en la tapa de la biela.
Marca en sombrerete de biela:
- - H: clase de peso de la biela;
- - 2 - clase de biela según el diámetro del orificio para el pasador del pistón.
Antes de ensamblar la biela y el grupo de pistones a partir de piezas nuevas, es necesario levantar los dedos de los pistones y las bielas.
La clase del pistón y la biela en cuanto al diámetro de los agujeros para el pasador debe corresponder a la clase del diámetro del pasador.
Un pasador de pistón correctamente seleccionado, lubricado con aceite de motor, debe entrar en el orificio de la cabeza de la biela superior con la presión del pulgar y no caerse en posición vertical.
Al ensamblar el pistón con la biela, los orientamos de modo que cuando se instalan en el cilindro, el número de serie estampado en la biela se encuentra más cerca de la pared trasera del bloque de cilindros (en el que se encuentra el filtro de aceite).
Antes de instalar los anillos de pistón en el pistón, es necesario verificar los espacios térmicos en las cerraduras de los anillos.
Para ello, inserte el segmento del pistón en el cilindro en el que se instalará durante el montaje y alinee el segmento con la cabeza del pistón.
Comprobamos el espacio en el bloqueo del anillo del pistón con un juego de palpadores planos.
El espacio debe ser de 0,25 - 0,45 mm. El espacio de desgaste máximo permitido es de 1 mm.
Lubrique las ranuras de los pistones debajo de los anillos del pistón con aceite de motor. Instalamos los anillos en los pistones.
Coloque el anillo de compresión inferior con la ranura ("raspador") hacia abajo.
Si el anillo está marcado como "TOP" o "TOP", el anillo se coloca con la marca hacia arriba. Organice los anillos de la siguiente manera:
- - orientamos la traba del anillo de compresión superior en un ángulo de aproximadamente 45˚ con respecto al eje del pasador del pistón;
- - bloqueo del anillo de compresión inferior—en un ángulo de 180˚ con respecto al eje del bloqueo del anillo superior;
- - bloqueo del anillo rascador de aceite - en un ángulo de 90˚ con respecto al eje del bloqueo del anillo de compresión superior.
Al instalar el anillo rascador de aceite, colocamos la junta de expansión en el lado opuesto al bloqueo del anillo.
Antes de instalar el pistón en el cilindro, colocamos un mandril ajustable en el pistón y, apretando el mandril, comprimimos los anillos del pistón.
Instale el pistón con la biela en el cilindro. En este caso, el muñón de la biela del cigüeñal de este cilindro debe estar en la posición BDC.
Apoyando el mango del martillo contra la parte inferior del pistón, lo empujamos hacia el interior del cilindro.
Habiendo quitado el mandril, enviamos el pistón dentro del cilindro con el mango del martillo hasta que se detenga.
Al mismo tiempo, controlamos el ajuste del buje de la cabeza inferior de la biela en el muñón del cigüeñal.
Al instalar la tapa de la biela, los números de serie de la biela y la tapa deben coincidir y estar ubicados en el mismo lado de la biela
El montaje posterior del motor se realiza en orden inverso.