The nozzle is used to inject and atomize the fuel supplied to the diesel cylinders
The ZMZ-245.12 diesel engine uses a closed-type nozzle with hydraulically controlled needle lifting.
The nozzle is strictly fixed relative to the combustion chamber and bolted to the cylinder head.
The diesel has injectors (part no. 17.1112010-01).
The injectors are marked on the body.
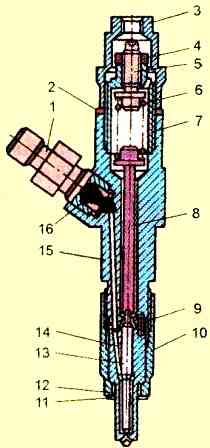
nozzles are installed with atomizer mod. 145.1112110 or Motorpal (Czech Republic). The use of other models of sprayers is not allowed.
The injector is a vulnerable part of the fuel supply system.
Violation of the seal between the conical surfaces of the sprayer body and the needle, loss of mobility of the needle; a decrease in the pressure of the start of fuel injection, a deterioration in the quality of atomization and an increase in the throughput of the atomizer due to wear of the nozzle holes are the main defects of the injectors
Checking the performance of the injectors should be done during vehicle maintenance.
It is recommended to evaluate the performance of the injector on test benches at a frequency of full strokes of the lever of the manual test fixture of 60-80 min.
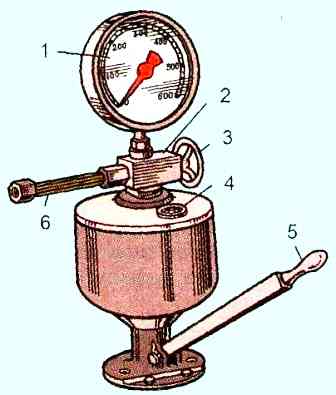
In fig. 2 shows a device for controlling the injector nozzles and adjusting the injection pressure mod. "Motorpal" NS 50.
When using the KI-9917 device, the start of fuel injection by injectors can be checked without removing them from the diesel engine.
Regulation of the fuel injection start pressure is carried out by turning the adjusting screw 5, having first unscrewed the cap and released the lock nut 4 (Fig. 1).
The pressure recorded at the start of fuel injection should be 21.6-22.4 MPa;
After adjustment, tighten the locknut and cap. Tightening torque - 80-100 Nm.
Quality of fuel atomization should be checked on the adjusted injector.
It is considered satisfactory if the fuel is atomized to a misty state and distributed evenly in the cross section of the jet cone from all five nozzle holes.
Coarsely emitted drops, continuous jets and thickening are not allowed.
The beginning and end of the injection must be clear.
It is not allowed to leak fuel from the atomizer after the end of injection.
The tightness of the locking cone of the sprayer needle must be checked by creating a pressure in the nozzle that is 1.0-1.5 MPa less than the injection start pressure.
The tightness is considered to be broken if, within 15 s, the fuel flows down in drops and forms a swell that can be seen with the naked eye on the nozzle of the sprayer under the nozzle holes.
If fuel leaks or the needle is stuck, the atomizer must be replaced or repaired.
In case of coking of the nozzle holes, disassemble the nozzle, rinse the atomizer and clean the holes.
It is recommended to clean the nozzle holes with steel wire with a diameter of 0.3 mm.
Before assembly, the atomizer and needle, which are a precision pair, must be thoroughly rinsed in clean gasoline and lubricated with filtered diesel fuel.
To check the smooth movement of the needle in the atomizer body it should be pulled out of the body by one third of the length of the guide surface.
When tilting the atomizer at an angle of 45°, the needle should smoothly, without stopping, completely lower under its own weight.
Injector disassembly
Disassembly of the nozzle must be done in the following sequence:
- - unscrew the cap 3 (see Fig. 1) and release the lock nut 4;
- - unscrew the adjusting screw 5 by 2-3 turns, thereby weakening the spring 6;
- - unscrew the atomizer nut 10;
- - remove atomizer 11.
Faulty disassembly may break the pins that center the atomizer.
New atomizers must be depreserved before being installed in the nozzle by washing them in gasoline or heated diesel fuel.
It is necessary to assemble the nozzle in the reverse order of disassembly. Tightening torque of the atomizer nut 50-70 Nm.
After assembly, it is required to repeat the injector performance test in the sequence indicated above.
When assembling, the sealing gasket 12 must be replaced.
When installing injectors on a diesel engine, the bolts of their fastening must be tightened evenly in 2 - 3 steps. Final tightening torque 20-25 Nm.