A turbocharger is installed on the diesel engine, which uses the energy of exhaust gases to pressurize air into the diesel cylinders
The turbocharger consists of a single-stage centrifugal compressor and a radial centripetal turbine.
The principle of operation of a turbocharger is that the exhaust gases from the cylinders under pressure enter through the exhaust manifold into the chambers of the gas turbine.
Expanding, gases rotate the wheel of a centrifugal turbocharger.
The centrifugal turbocharger sucks in air through the air cleaner, compresses it and supplies it under pressure to the diesel cylinders.
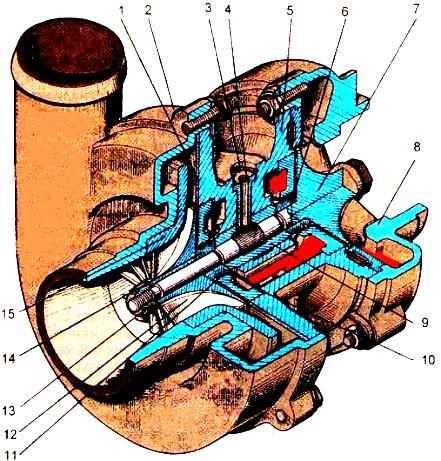
The turbocharger bearing is lubricated by oil supplied through the pipeline from the centrifugal oil filter.
From the turbocharger, oil is drained through an oil drain pipe into the diesel crankcase.
Turbine wheel 7 is cast from heat-resistant nickel alloy and welded to the rotor shaft.
Compressor wheel 12 is cast from aluminum alloy and fixed to the rotor shaft with a special nut 13.
The turbocharger is provided with contact gas-oil seals with spring rings 11.
On the turbine side, the sealing rings are installed in the groove of the sleeve 6 pressed onto the rotor shaft.
On the compressor side, the O-rings are installed in the groove of the sleeve 14.
To improve the efficiency of the oil seal on the compressor side, the sealing ring zone is separated from the zone of active oil ejection from the bearing by oil deflector 16, which forms an additional labyrinth.
Excessive air pressure after the compressor at the nominal mode of operation of the diesel engine should be in the range of 0.08-0.14 MPa.
During operation, the turbocharger does not require special maintenance.
The turbocharger must not be dismantled and repaired.
The condition of the turbocharger should be checked by the run-out time of the rotor when the diesel engine is stopped; for this, after 3-5 minutes of operation at the minimum idle speed mode, the diesel engine is brought to the maximum speed mode, and then turn off the fuel supply.
The rotation of the turbocharger rotor after stopping the diesel engine should be heard for at least 5 seconds.
A smooth, constant sound level with gradual decay indicates the normal condition of the turbocharger.
One of the reasons for a decrease in diesel power and increased smoke may be a decrease in boost pressure due to contamination of the compressor flow path, which can be determined by the tight rotation of the rotor.
If the rotor rotates hard, then it is necessary to partially disassemble the turbocharger and flush the compressor part.
Before disassembly, thoroughly clean the external surfaces of the turbocharger from dirt and dust.
In order to avoid damage to the blades during disassembly and assembly of the turbocharger, the middle housing assembly with the rotor cannot be placed on the compressor turbine wheel; a special stand must be used for this purpose.
Partial disassembly, flushing and assembly should be done in the following order:
- - unscrew the bolts securing the compressor casing 2 to the middle casing 5 and disconnect the compressor casing from the middle casing;
- - wash the compressor housing, the surface of the wheel and the middle housing with clean diesel fuel
- - connect the compressor housing to the middle housing, placing a paronite gasket between the flanges.
When installing the compressor housing, pay attention to the correct orientation of the compressor outlet pipe relative to the flange of the turbine housing;
- - pour 10-15 g of clean engine oil into the oil channel of the middle housing and, pressing the ends of the rotor alternately on both sides with your fingers, turn the rotor several times to check for smooth rotation and no jamming.