Am Dieselmotor ist ein Turbolader installiert, der die Energie der Abgase nutzt, um Luft in die Dieselzylinder zu pumpen
Der Turbolader besteht aus einem einstufigen Radialverdichter und einer radialen Zentripetalturbine.
Das Funktionsprinzip eines Turboladers besteht darin, dass die Abgase der unter Druck stehenden Zylinder durch den Abgaskrümmer in die Kammern der Gasturbine gelangen.
Gase, die sich ausdehnen, drehen das Rad eines Zentrifugalturboladers.
Der Radialturbolader saugt Luft durch den Luftfilter an, komprimiert sie und führt sie unter Druck den Dieselzylindern zu.
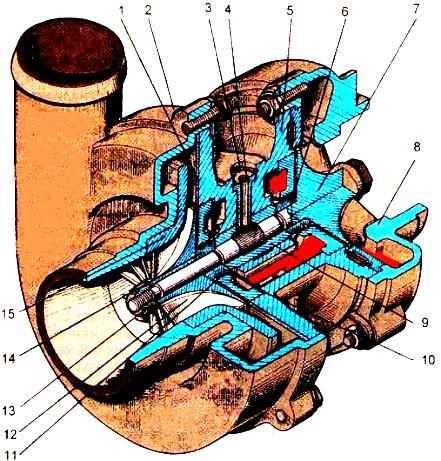
Das Turboladerlager wird durch Öl geschmiert, das über die Rohrleitung vom Zentrifugalölfilter zugeführt wird.
Vom Turbolader wird das Öl durch ein Ölablassrohr in das Dieselkurbelgehäuse abgelassen.
Das Turbinenrad 7 ist aus einer hitzebeständigen Nickellegierung gegossen und mit der Rotorwelle verschweißt.
Das Kompressorrad 12 ist aus einer Aluminiumlegierung gegossen und mit einer speziellen Mutter 13 an der Rotorwelle befestigt.
Der Turbolader ist mit Gasöl-Kontaktdichtungen mit Federringen 11 ausgestattet.
Turbinenseitig werden die Dichtringe in die Nut der auf die Rotorwelle gepressten Hülse 6 eingebaut.
Auf der Kompressorseite werden die O-Ringe in die Nut der Hülse 14 eingebaut.
Um die Effizienz der Öldichtung auf der Kompressorseite zu verbessern, ist die Dichtringzone von der Zone des aktiven Ölausstoßes aus dem Lager durch den Ölabweiser 16 getrennt, der ein zusätzliches Labyrinth bildet.
Der übermäßige Luftdruck nach dem Kompressor sollte bei Nennbetriebsart des Dieselmotors im Bereich von 0,08–0,14 MPa liegen.
Während des Betriebs bedarf der Turbolader keiner besonderen Wartung.
Der Turbolader darf nicht zerlegt und repariert werden.
Der Zustand des Turboladers sollte anhand der Auslaufzeit des Rotors beim Stoppen des Dieselmotors überprüft werden; dazu wird der Dieselmotor nach 3-5 Minuten Betrieb im minimalen Leerlaufdrehzahlmodus auf Hochtouren gebracht Stellen Sie den Höchstgeschwindigkeitsmodus ein und schalten Sie dann die Kraftstoffzufuhr ab.
Nach dem Abstellen des Dieselmotors sollte die Drehung des Turboladerrotors mindestens 5 Sekunden lang zu hören sein.
Ein gleichmäßiger, konstanter Geräuschpegel mit allmählichem Abfall zeigt den normalen Zustand des Turboladers an.
Einer der Gründe für einen Rückgang der Dieselleistung und eine erhöhte Rauchentwicklung kann ein Rückgang des Ladedrucks aufgrund einer Verunreinigung des Kompressorströmungswegs sein, was durch die enge Drehung des Rotors festgestellt werden kann.
Wenn sich der Rotor stark dreht, ist es notwendig, den Turbolader teilweise zu zerlegen und den Kompressorteil zu spülen.
Reinigen Sie vor der Demontage die Außenflächen des Turboladers gründlich von Schmutz und Staub.
Um eine Beschädigung der Schaufeln bei der Demontage und Montage des Turboladers zu vermeiden, darf die mittlere Gehäusebaugruppe mit dem Rotor nicht auf dem Verdichter-Turbinenrad platziert werden, hierfür muss ein spezieller Ständer verwendet werden.
Teilweise Demontage, Spülung und Montage sollten in der folgenden Reihenfolge erfolgen:
- - Lösen Sie die Schrauben, mit denen das Kompressorgehäuse 2 am mittleren Gehäuse 5 befestigt ist, und trennen Sie das Kompressorgehäuse vom mittleren Gehäuse;
- - Waschen Sie das Kompressorgehäuse, die Radoberfläche und das Mittelgehäuse mit sauberem Dieselkraftstoff
- - Verbinden Sie das Kompressorgehäuse mit dem mittleren Gehäuse und platzieren Sie dabei eine Paronitdichtung zwischen den Flanschen.
Achten Sie beim Einbau des Kompressorgehäuses auf die korrekte Ausrichtung des Kompressorauslassrohrs relativ zum Flansch des Turbinengehäuses;
- - Gießen Sie 10-15 g sauberes Motoröl in den Ölkanal des Mittelgehäuses und drücken Sie abwechselnd mit den Fingern auf die Enden des Rotors auf beiden Seiten. Drehen Sie den Rotor mehrmals, um zu prüfen, ob er gleichmäßig dreht und nicht blockiert .