Drive shafts transmit torque from the engine, gearbox and differential to the front wheels
In the gearbox housing, the drive shafts are splined to the side gears of the differential.
Fixation of the splined tip of the internal joint of the drive shaft in the side gear is carried out by a snap ring.
When installed, the circlip compresses into the shaft groove.
After the shaft is fully installed in the side gear of the differential, the retaining ring is released and fixes the splined tip from axial movement.
The outer joints of the drive shafts are attached to the front wheel hubs mounted on bearings.
The shaft is attached to the hub with a flanged nut.
To avoid loosening the nut, the collar of the nut is bent into the groove of the drive shaft.
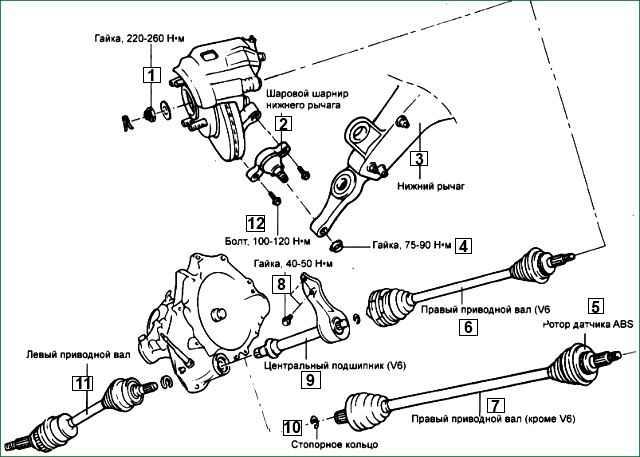
Constant velocity joints (CV joints) are installed on both sides of the drive shaft.
All outer CV joints are Birfield type, while inner CV joints are tripoid or ball type.
Tripoid type CV joints are used to prevent the transmission of engine vibrations through the drive shafts to the car body.
CV joints are needed to transmit torque and compensate for the movement of the front suspension.
Also, CV joints allow you to change the length of the drive shaft and transmit torque at constantly changing angles.
Removing drive shafts
We prepare the car and install it on a lift or an inspection ditch
We raise the car and fix it on supports and remove the front wheel
Draining the transmission fluid from the gearbox
Remove the cotter pin and unscrew the nut securing the drive shaft to the front wheel hub
We unscrew the two bolts and disconnect the ball joint from the hinge
Using a plastic hammer, we knock out the drive shaft from the front wheel hub
If the driveshaft is firmly seated in the front wheel hub, spray WD-40 on the spline area and then re-thread the nut a few turns, but do not tighten.
By hitting the nut with a soft-faced hammer, we knock the drive shaft out of the hub.
Reject the steering knuckle outward and remove the drive shaft from the front wheel hub
Then we insert the pry bar between the gearbox housing and the drive shaft and with light blows on the pry bar we remove the drive shaft from the gearbox (except V 6)
Do not pull on the drive shaft, as this will damage the constant velocity joints
Do not insert the pry bar too deep, so as not to damage the oil seal
Do not lower the vehicle onto the wheels with the driveshafts disconnected as the wheel bearing will be damaged.
If you need to put the car on wheels to move it, use a special tool to support the wheel bearing.
We release the tension mechanism and remove the drive th belt (V6 engines)
Remove the generator (V6 engines)
We unscrew the mounting bolts of the central bearing bracket.
We insert the pry bar between the center bearing bracket and the cylinder block and disconnect the bracket from the cylinder block.
Remove the internal joint of the drive shaft from the gearbox
Using a puller, remove the ABS sensor rotor from the drive shaft
Checking the drive shaft
Check the protective covers of the CV joints of the drive shaft for defects
Check the splines on the ends of the drive shaft for wear and damage
Mounting the drive shaft
Lubricate the sealing lip of the differential oil seal.
Install a new retaining ring on the inner end of the drive shaft.
Push the driveshaft into the gearbox, making sure the cut of the circlip is on the bottom.
After installation, pull the drive shaft outward and make sure it is securely fixed with the round clip.
Install a washer under the driveshaft-to-hub nut with the convex side outward as shown.
Tighten the following items with torque:
Drive shaft mounting nut: 200–260 Nm
Lower arm ball joint to joint: 100–120 Nm