Thermal valve is designed to automatically control the oil supply to the oil cooler depending on the oil temperature and pressure.
On the engine, a thermal valve is installed between the cylinder block and the oil filter
The thermal valve consists of a housing 3, cast from an aluminum alloy, two valves: a safety valve, consisting of a ball 4 and a spring 5, and a bypass valve, consisting of a plunger 1 controlled by a thermal force sensor 2, and a spring 10; screw plugs 7 and 8 with gaskets 6 and 9.
The oil supply hose to the radiator is connected to fitting 11.
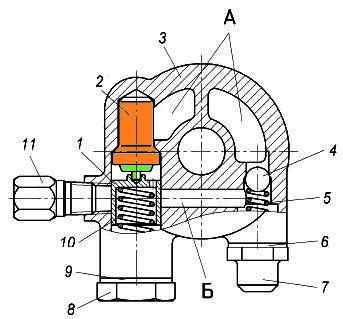
From the oil pump, oil is supplied under pressure to the cavity of the thermal valve A.
When the oil pressure is above 0.7... 0.9 kgf/cm, the ball valve opens and the oil enters the channel of the thermal valve body B to plunger 1.
When the oil temperature reaches 81 + 2°C, the piston of the thermal force element 2, washed by the flow of hot oil, starts to move the plunger 10, opening the way for the oil flow from channel B to the oil cooler.
The ball valve protects the rubbing parts of the engine from an excessive drop in oil pressure in the lubrication system.
To check the technical condition disassemble the thermal valve, wash its parts in kerosene or gasoline and blow with compressed air.
Make sure that the thermovalve plunger moves freely in the housing bore, without jamming, and that the spring is in good condition.
The mating surfaces of the plunger and body must be free of deposits and burrs that can lead to jamming of the plunger.
Check the wear of the thermal valve bore and plunger.
Mating parts: thermal valve body - plunger
- Hole - Ø22+0.02
- Shaft - Ø22-0.015-0.045
- Gap - 0.065/0.015
If the size deviates significantly from the nominal value, the worn part should be rejected.
The length of the plunger spring in the free state should be 70 mm.
The force on the spring when compressed to a length of 41.8 mm should be 57.3 ± 10.5 N. If the force is less, reject the spring.

The free length of the safety ball valve spring must be 56 mm.
The force on the spring when compressed to a length of 41 mm should be 7.5 ± 1.5 N. When weakened, replace the spring.
Check the serviceability of the thermal force sensor by the piston offset at different temperatures of the oil washing the sensor and the loads on the piston created by the spring.
The initial piston offset at an oil temperature of (20 ± 15)˚C and a piston load of 44.1 ± 4.4 N should be no more than 7 mm.
At a temperature of (95 ± 2)° C and a piston load of 113 ± 11.3 N, resulting from further compression of the spring from 44.1 ± 4.4 N, the piston overhang must be at least 12.88 mm.
At a temperature of (115 ± 2)˚C and the force generated as a result of further compression of the spring, the overhang should be no more than 21 mm.
If the overhang does not correspond to the given values, the thermal force sensor should be rejected.
Measure the outreach with a dial indicator with a division value of 0.01 mm.
The intensity of oil heating should not exceed 1˚C/min.
During the test, the oil must be continuously mixed to obtain the same temperature throughout.
When assembling the thermal valve, tighten the plunger plug with a torque of 39.2-44.1 Nm (4-4.5 kgcm), the ball valve plug with a torque of 24.5-29.4 (2.5-3 kgcm), the fitting with a torque of 19 .6-49.1 (2-5 kgcm), having previously applied the “stop-6” sealant to the fitting thread.
After installing on the engine, warm up the engine to a temperature of plus 90˚C and check the tightness of the thermal valve.