Die Demontage eines Einspritzzahnradpaares sowie des Gehäuses und Deckels der Ölpumpe ist nicht gestattet
Es dürfen keine Risse am Pumpengehäuse und am Deckel sowie Beschädigungen oder ausgerissene Gewinde vorhanden sein
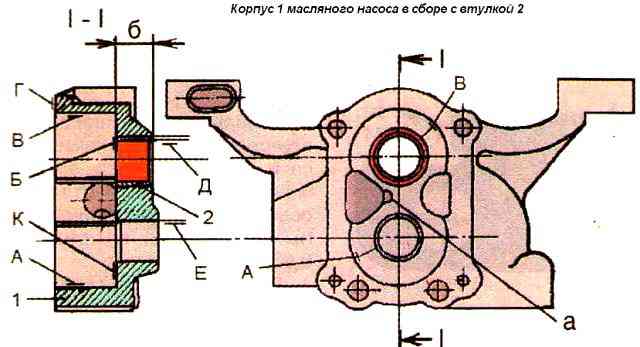
Die Unebenheit der Oberfläche „G“ (Abb. 1) des Pumpengehäuses sollte über die gesamte Länge 0,03 mm nicht überschreiten.
Der lokale Verschleiß der Oberfläche „B“ des Ölpumpengehäuses an den Stellen, an denen die Einspritzzahnräder aufeinandertreffen, ist bis zu 0,03 mm zulässig.
Bei stärkerem Verschleiß ist das Schleifen des Körpers zulässig; Dabei sollte die Rauheit der behandelten Oberfläche Ra≤1,25 µm betragen.
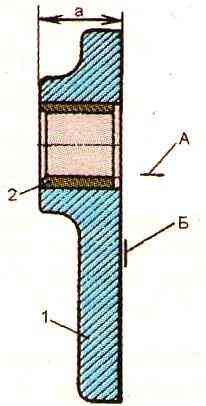
Die Dicke der Abdeckung (Maß „a“ in Abb. 2) darf mindestens 16 mm betragen.
Die Unebenheit der Oberfläche „B“ des Pumpendeckels sollte 0,03 mm nicht überschreiten.
Die Nichtsenkrechtigkeit der Fläche „B“ zur Fläche „A“ sollte über die gesamte Länge 0,03 mm nicht überschreiten.
Die Höhe der Einspritzzahnräder muss gleich sein und 28-0,040 mm betragen; Der Höhenunterschied darf nicht mehr als 0,03 mm betragen.
Die Tiefe der Pumpengehäusetaschen für die Druckzahnräder muss mit einer Toleranz von 0,06 mm gleich sein.
Beträgt der Tiefenunterschied der Buchsen mehr als 0,06 mm oder sind tiefe Kratzer und Schrammen an den Endflächen der Buchsen vorhanden, ist eine Bearbeitung bis zur Beseitigung der Abnutzungsspuren zulässig.
Der Rundlauf der bearbeiteten Fläche „B“ (siehe Abb. 1) relativ zur Fläche „D“, der Fläche „K“ relativ zur Fläche „D“, der Fläche „K“, relativ zur Fläche „E“. " bei einem Radius von 18 mm sollte 0,05 mm nicht überschritten werden.
Es ist zulässig, die Nester um einen Betrag zu vertiefen, bei dem das Maß „b“ mindestens 15 mm beträgt.
Die Rauheit der behandelten Oberflächen beträgt Ra≤0,25 µm. Schlagkontrolle nach RTM 70.0001.234-83.

Die Tiefe der Nut (Maß „a“) am Pumpengehäuse muss mindestens 3 mm betragen.
Die Senkung des Endes des Stifts des angetriebenen Zahnrads relativ zur Ebene des Anschlusses des Pumpengehäuses (S1) sollte innerhalb von 0,7–1,3 mm liegen (Abb. 3).
Das Überstehen der Buchse über die Enden des angetriebenen Zahnrads der Pumpe und die Oberflächen des Pumpendeckels ist nicht zulässig.
Die Unrundheit und Toleranz des Profils des Längsschnitts des Lochs der Buchse des angetriebenen Zahnrads sollte nach der Bearbeitung 0,025 mm nicht überschreiten.
Die Einsenkung der Einspritzzahnräder der Ölpumpe relativ zur Fläche „G“ (siehe Abb. 1) sollte innerhalb von 0,04–0,13 mm liegen.
Bei einem höheren Sinkwert ist es zulässig, Metall von der „G“-Oberfläche zu entfernen.
Der Rundlauf der bearbeiteten Fläche „P“ relativ zur Fläche D bei einem Radius von 29 mm sollte 0,07 mm nicht überschreiten.
Die Rauheit der bearbeiteten Oberfläche sollte Ra ≤ 1,25 µm betragen.
Der Durchmesser der Löcher in den Buchsen des Pumpengehäuses und -deckels sowie der Buchse des Abtriebsrads muss 1 8 + 0,059 mm entsprechen. Bei einem größeren Durchmesser die Buchsen durch neue ersetzen und anschließend auf den erforderlichen Durchmesser bearbeiten.
Die Buchse muss bündig mit der Fläche „B“ in das Ölpumpengehäuse eingepresst werden.
Die Bearbeitung der Löcher der Hülsen muss am zusammengebauten Pumpengehäuse mit Deckel bei einmaliger Installation des Werkzeugs erfolgen. Oberflächenrauheit Ra ≤ 2,25 µm.
Die Unrundheit und Toleranz des Profils des Längsschnitts der bearbeiteten Löcher beträgt 0,025 mm.
Der Durchmesser der Pumpengehäusebuchsen in den Bereichen mit dem größten Verschleiß sollte 42,25 mm betragen.
Wenn die Oberflächen „A“ und „B“ auf einen Durchmesser von mehr als 42,41 mm abgenutzt sind, ist es zulässig, sie durch anschließendes Aufbohren auf den Durchmesser eines neuen Körpers wiederherzustellen.
Exzentrisches Bohren von Nestern für Zahnräder mit Nenngröße ist auch zulässig, wobei die Achsen der Nester in Richtung des Saugkanals der Pumpe verschoben werden. Der Versatz ist bis zu 2,1 mm zulässig.
Die Rauheit der bearbeiteten Oberflächen beträgt Ra ≤ 0,20 µm.
Das radiale Spiel zwischen dem Pumpengehäuse und den Oberseiten der Zähne der Pumpenräder sollte zwischen 0,125 und 0,245 mm liegen.
Die Abstände zwischen den Löchern der Gehäusebuchsen, den Pumpendeckeln und der Pumpenwelle sowie zwischen dem Buchsenloch und der Achse des angetriebenen Zahnrads sollten innerhalb von 0,032–0,07 mm liegen.
Der Überstand der Zylinderstifte 4 (siehe Abb. 3) über der Steckebene sollte 7 ± 0,2 mm betragen.
Der Spalt S zwischen der Stirnfläche der Antriebsradnabe und dem Deckel der zusammengebauten Pumpe sollte nicht mehr als 0,2 betragen
Die Schrauben, mit denen der Pumpendeckel am Gehäuse befestigt ist, müssen mit einem Drehmoment von 18–25 Nm angezogen werden.
Die Zahnräder der zusammengebauten Pumpe sollten sich frei von Hand drehen lassen, ohne zu klemmen und zu ruckeln.
Das Einlaufen und Testen der Ölpumpe auf dem ki-5278-Prüfstand sollte mit einer Mischung aus Motoröl und Dieselkraftstoff mit einer Viskosität von 11,5–16 mm 2/s durchgeführt werden (cSt) bei der Testtemperatur.
Die Verwendung anderer Mineralöle ist zulässig, sofern die angegebene Viskosität während des Tests eingehalten wird.
Bei einer Prüftemperatur von 18–22 °C kann eine Mischung aus 40 % M-10G-Motorenöl und 60 % Dieselkraftstoff verwendet werden.
Die Ölpumpe muss jedes Mal für 2 Minuten mit einer Pumpenwellendrehzahl von 2320 ± 50 min -1 bei einem Pumpenausgangsdruck von 0,30 ± 02 MPa und einem Gegendruck von 0,7 eingefahren werden ± 0,3 MPa.
Während des Einlaufvorgangs sind eine Überhitzung der Teile, Fremdgeräusche sowie Öllecks an den Verbindungsstellen nicht zulässig. Durch die Lücken zwischen der Pumpenwelle, den Buchsen des Gehäuses und dem Pumpendeckel ist eine leichte Ölleckage zulässig.
Die zusammengebaute Pumpe muss auf dem Prüfstand getestet werden. Bei einer Pumpenwellendrehzahl von 3170 ± 25 min -1 und einem Gegendruck am Pumpenausgang von 0,7–0,75 MPa sollte der Volumenstrom der reparierten Pumpe mindestens 0,8 dm 3 /s und die für den Antrieb aufgewendete Leistung beträgt nicht mehr als 1,3 kW.
Bei der Dichtheitsprüfung von Düsen mit Dieselkraftstoff oder Luft bei einem Druck von 0,1 ± 0,02 MPa sind keine Undichtigkeiten, Tropfen oder Lufteinbrüche zulässig.
Die Unebenheit der Passflächen der Anschlussflansche des Auslassrohrs sollte 0,05 mm nicht überschreiten.
Beim Testen der Auslassleitung auf Dichtheit mit Wasser bei einem Druck von 1,0 MPa sind keine Undichtigkeiten oder Wassertropfen zulässig.