We examined the disassembly of the axle gearbox in the article - Disassembly for the repair of the rear axle of a Gazelle car
In this article, we will consider how to properly assemble and adjust the rear axle gearbox of a Gazelle car.
Reducer assembly
We assemble the main gear in the reverse order of disassembly, lubricating the bearings and gears with gear oil.
Having installed the drive gear in the gearbox housing, with a torque wrench we tighten the flange nut with a torque of 16–20 kgf.m, while the gear must be rotated to properly install the rollers in the bearings.
We install an indicator on a tripod with a division value of not more than 0.01 mm, resting its leg against the end of the flange and moving the shaft behind the flange, measuring the axial play of the drive gear
To eliminate the backlash, we take out the spacer ring mounted on the gear shaft (see Dismantling for the repair of the rear axle of the Gazelle car) and measure its thickness with a micrometer.
We select and install a new spacer ring.
It should be thinner than the removed amount of play and additionally thinner by 0.05 mm if the drive gear bearings are new or by 0.01 mm if the bearings are left the same.
In the absence of axial play of the drive gear, we check the moment of resistance to shaft rotation with a special torque wrench with a division value of up to 0.5 kgf.m.
When properly adjusted, the moment of resistance should be 15–20 kgfcm for new bearings, or 7–10 kgfcm if the bearings are left the same.
With sufficient accuracy, the moment of resistance can be measured with a household steelyard by hooking its hook to the flange hole.
In this case, the required values will be less - 3.8–5 kgf and 1.8–2.5 kgf, respectively.
If the moment of resistance is greater, we change the spacer ring to another, thicker by 0.01–0.02 mm, if less, we select a ring of smaller thickness accordingly.
The bolts for fastening the parts of the differential box and the bolts for fastening the driven gear, as well as their threaded holes, are degreased before assembly and coated with an anaerobic sealant.
We pay special attention to the cleanliness of the end seating surfaces of the gears and the satellite box, the slightest dirt or nicks are unacceptable.
When installing the driven gear on the satellite box, we center it with long M10x1 bolts (you can use bolts from old connecting rods).
With adjusting nuts, we tighten the differential bearings with a slight interference, while turning the gear in one direction or the other, so that the bearing rollers take the correct position.
To measure the side clearance in the meshing of the main gear gears, we fix the indicator on the rear axle housing by bringing its probe to the top of the tooth on the outside of the driven gear.
The gap should be 0.15–0.20 mm.
Measurements should be repeated on at least six teeth in opposite zones of the crown.
To reduce the clearance (with a screwdriver or a thin steel rod), loosen the adjusting nut on the side opposite the driven gear, and tighten the other.
Unscrew one nut and tighten the other by the same amount, guided by the grooves of the adjusting nuts.
At the same time, each unscrewing of the adjusting nut must be completed by tightening it a little.
For example, to loosen a nut by five slots, unscrew it by six, and then tighten it by one slot.
This will ensure that the outer race of the bearing is in constant contact with the nut and thus guarantees its fixation during operation.
To increase the gap, repeat the entire procedure in reverse order.
After adjusting the side clearance in engagement, we check the axial play in the bearings of the differential, for which we fix the indicator on a tripod, resting its probe against the end face of the driven gear.
Swinging the gear in the axial direction, we measure the play in the differential bearings.
With the adjusting nut located on the opposite side of the driven gear, set the axial play 0.035–0.055.
Further, tightening the nut, we set the bearing preload: 0.1 - with a bearing run of less than 10 thousand km; 0.05 - with a run of more than 10 thousand km.
Turning the nut one slot corresponds to a "compression" of the bearing by 0.03 mm.
After adjusting, tighten the bolts of the bearing caps and install the locking plates (see Disassembly for repairing the rear axle of the Gazelle car) and check the side clearance again.
Adjustment of the main gear according to the contact patch of the teeth
Before the final tightening of the cap bolts, unscrew them one by one and apply an anaerobic sealant to the threaded part.
Adjusting the final drive by tooth contact pattern is an effective way to adjust gear meshing.
It also allows you to check the quality of adjustments made in other ways.
Paint the teeth of the driven gear with paint, preferably bright.
Turn the flange of the drive gear several times in both directions, while slowing down the driven gear until the paint is rubbed off at the points of contact of the teeth.
We examine the contact spots on the teeth of the driven gear from the convex and concave sides.
If the contact patch is located at the top of the teeth, it is necessary to increase the thickness of the adjusting ring at the drive gear, and if at the base, reduce it.
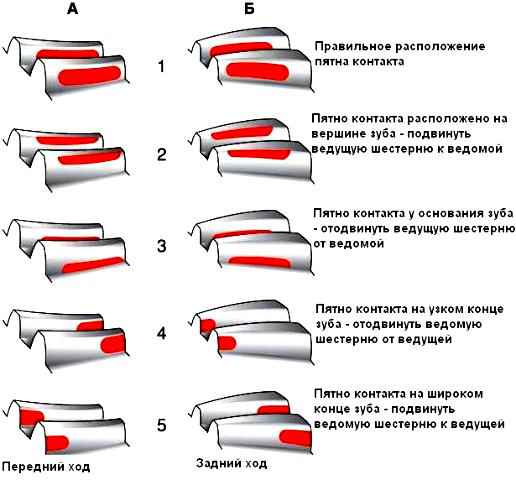
If the contact patch is shifted to the center of the gear, it is necessary to increase the gap between the driven and driving gears, and if outwards, reduce it.
After adjustment, we install the gearbox in the rear axle, while applying a thin layer of oil-resistant sealant to the mounting bolts and flange.
Having assembled the rear axle and filling it with oil (see Changing the oil in the gearbox of the rear axle of a Gazelle car), we test the gearbox on the go.
To do this, we make a trip at a speed of 60–70 km / h for 20–30 minutes.
The temperature of the crankcase throat must not exceed 95° (water drops must not boil).
Otherwise, reduce the drive gear bearing preload.