Überprüfung der Details des Zylinderkopfs des 1AZ-FE-Motors
Wir prüfen die Teile, um die Möglichkeit des weiteren Betriebs der Zylinderkopfteile festzustellen
Kontrolle des Zylinderkopfes
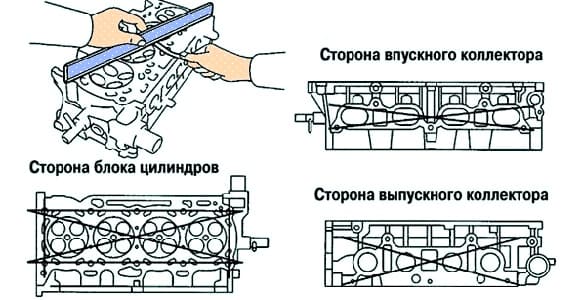
Überprüfen Sie mit einem Lineal und einer flachen Fühlerlehre die Verformung der Zylinderkopfflächen, die mit der Zylinderblockfläche und mit den Flächen der Einlass- und Auslasskrümmer zusammenpassen (Abb. 1).
Maximale Warp-Toleranz:
- Zylinderblockseite - 0,05 mm;
- Saugrohrseite - 0,08 mm;
- Auspuffkrümmerseite - 0,08 mm
Wenn die Krümmungsebene größer als das Maximum ist, ersetzen Sie den Zylinderkopf.
Verwenden Sie den Farbstoff, um die Verbrennungskammern, Einlass- und Auslassöffnungen und die Gasschnittstelle auf Risse zu prüfen.
Wenn Risse vorhanden sind, ersetzen Sie den Zylinderkopf.
Kontrolle der Zylinderkopfventilsitze
Tragen Sie eine dünne weiße Schicht auf die Abschrägung des Ventils auf.
Drücken Sie die Ventilfläche leicht gegen den Sitz, aber drehen Sie das Ventil nicht.
Entfernen Sie dann das Ventil und überprüfen Sie den Ventilsitz und die Schräge.
Bleibt die Farbe um den gesamten Umfang (360°) der Ventilfase, dann ist das Ventil konzentrisch.
Wenn nicht, ersetzen Sie das Ventil.
Wenn die Farbe um den gesamten Umfang (360°) des Ventilsitzes erscheint, sind Ventilführung (Hülse) und Ventilsitz konzentrisch.
Fase andernfalls nachschleifen.
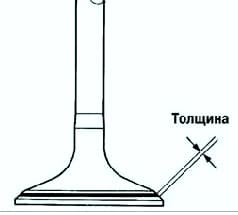
Achten Sie darauf, dass sich die Kontaktfläche in der Mitte der Ventilfläche befindet und 1,0–1,4 mm breit ist (Abbildung 2).
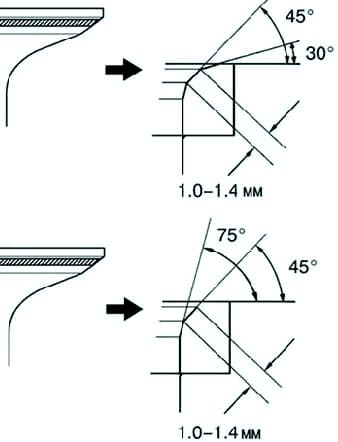
Wenn die Kontaktfläche zu hoch ist, korrigieren Sie die Fase mit 30°- und 45°-Konusfräsern.
Wenn die Kontaktfläche zu niedrig ist, korrigieren Sie die Fase mit 75°- und 45°-Konusfräsern (Abb. 3).
Axialspiel der Nockenwelle prüfen
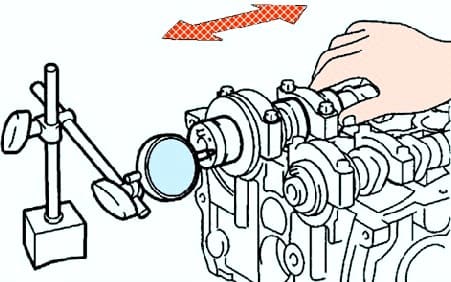
Die Nockenwellen einbauen.
Messen Sie das Axialspiel mit einer Messuhr, indem Sie die Nockenwelle hin und her bewegen (Abb. 4).
Nennspiel:
- Einlass - 0,040-0,095 mm;
- Auslass - 0,080–0,135 mm.
Freigabe begrenzen:
- Einlass. – 0,11 mm;
- Auslass - 0,15 mm.
Wenn das Endspiel größer als das Maximum ist, die Nockenwelle ersetzen.
Falls erforderlich, Lagerdeckel und Zylinderkopf ersetzen.
Radialspiel der Nockenwellenlager prüfen
Laufflächen der Lagerdeckel und Nockenwellenzapfen reinigen.
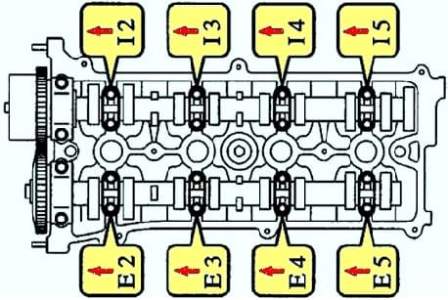
Die vordere Lagerschale einbauen.
Die Nockenwelle in das Bett des Zylinderkopfes legen.
Legen Sie ein Stück Plastiklehre auf jeden Nockenwellenzapfen.
Die Lagerdeckel einbauen.
Ziehen Sie die Schrauben der Abdeckungen mit dem Anzugsdrehmoment:
fest
- #1 - 30 Nm (301 kg cm);
- #2 - 30 Nm (301 kg cm);
- #3 - 9 Nm (92 kg cm).
Ventilfederprüfung
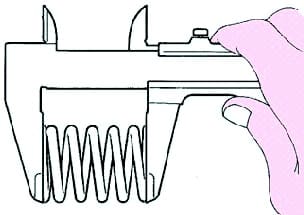
Messen Sie die freie Länge der Feder mit einem Messschieber (Abb. 6).
Ventilfederlänge: 45,70 mm.
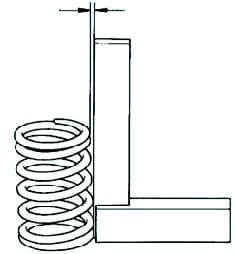
Mit einem Metallwinkel (90°) das nicht rechtwinklige Spiel der Ventilfeder prüfen (Abb. 7).
Abweichungsgrenze: 1,6 mm.
Kontrolle der Zylinderkopfventillänge
Überprüfen Sie die Gesamtventillänge.
Nennlänge:
- Einlassventil - 101,71 mm;
- Auslassventil - 101,15 mm.
Längenbegrenzung:
- Einlassventil - 101,21 mm;
- Auslassventil - 100,70 mm.
Wenn die Gesamtlänge unter dem Mindestwert liegt, ersetzen Sie das Ventil.
Dicke der Zylinderkopfventilscheibe prüfen
Überprüfen Sie die Dicke des Ventilkopfes mit einem Messschieber.
Standard-Einlassventildicke: 1,05 - 1,45 mm.
Mindesttoleranz: 0,5 mm.
Standarddicke der Auslassventile: 1,20 - 1,60 mm.
Mindesttoleranz: 0,5 mm.
Wenn die Dicke des zylindrischen Teils des Ventilkegels geringer als der zulässige Mindestwert ist, ersetzen Sie das Ventil.
Durchmesser des Zylinderkopf-Ventilschafts messen
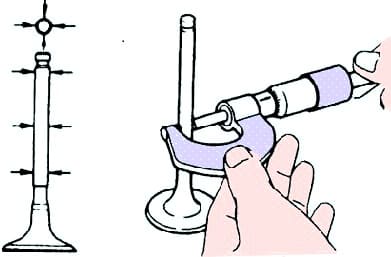
Messen Sie den Ventilschaftdurchmesser mit einem Mikrometer (Abb. 8).
Ventilschaftdurchmesser:
- Einlassventil - 5.470-5.485 mm;
- Auslassventil - 5.465-5.480 mm.
Kontrolle der Innendurchmesser der Zylinderkopfventilführungen
Überprüfen Sie die Innendurchmesser der Ventilführungen.
Messen Sie mit einer Innenlehre die Innendurchmesser der Ventilführungen auf drei Ebenen.
Der Innendurchmesser der Hülse beträgt 5.510–5.530 mm.
Führen Sie eine Berechnung durch, indem Sie den Ventilschaftdurchmesser und den Innendurchmesser der Führungsbuchse subtrahieren, und ermitteln Sie so das Standardspiel zwischen dem Ventilschaft und seiner Führung.
Standardspielwert:
- Einlass - 0,025-0,060 mm;
- Auslass - 0,030–0,065 mm.
Maximale Toleranz:
- Einlass - 0,08 mm;
- Auslass - 0,10 mm.
Wenn das Spiel größer als das Maximum ist, ersetzen Sie das Ventil und die Führungshülse.
Stößel und Stößelbohrungen im Zylinderkopfgehäuse prüfen
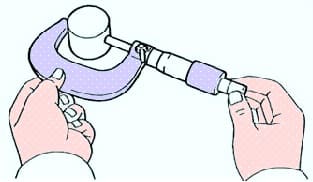
Messen Sie den Durchmesser des Drückers mit einem Mikrometer (Abb. 9).
Schieberdurchmesser - 30,966–30,976 mm.
Führen Sie eine Berechnung durch, indem Sie den Stößeldurchmesser vom Durchmesser der Stößelbohrung im Kopfgehäuse abziehen und das Spiel bestimmen.
- Das Standardspiel beträgt 0,033–0,059 mm.
- Das Grenzspiel beträgt 0,079 mm.
Wenn der Abstand den maximal zulässigen Wert überschreitet, ersetzen Sie den Drücker.
Ersetzen Sie bei Bedarf den Zylinderkopf.
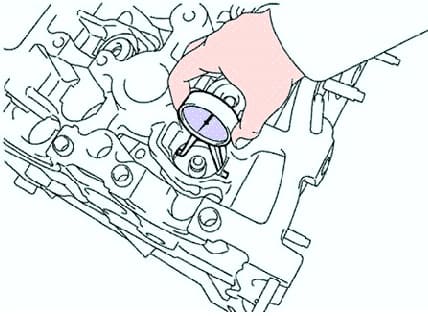
Überprüfen Sie die Stößel und Stößelbohrungen im Zylinderkopfgehäuse.
Messen Sie mit einer Innenlehre die Durchmesser der Stößelbohrungen im Zylinderkopf (Abb. 10).
Bohrungsdurchmesser - 31.000–31.025 mm.
Die Verzugsgrenze beträgt 0,7 mm.
Auf Knicke an der Kontaktfläche des Auspuffkrümmers prüfen.
Wenn der Verzug das Maximum überschreitet, ersetzen Sie den Verteiler.