Zylinderkopf-Demontage
Entfernen Sie die Hebeösen des Motors (Abb. 1).
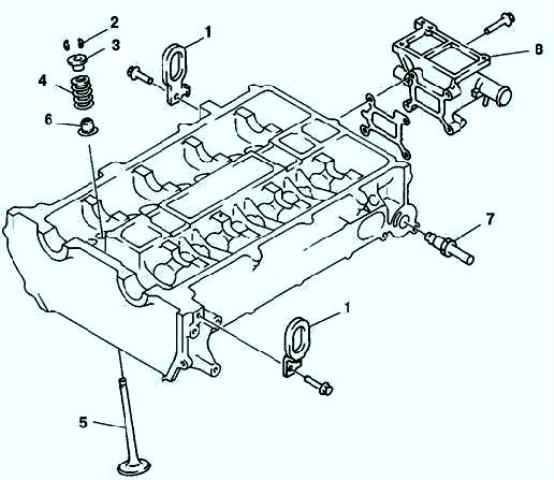
Entfernen Sie die Ventilkeile mit Spezialwerkzeug (Abb. 2).
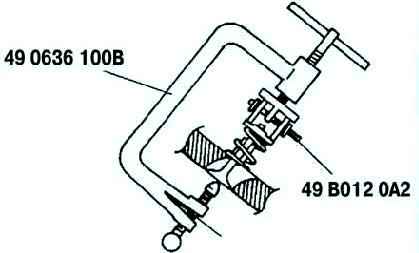
Entfernen Sie den oberen Ventilfederkopf. Entfernen Sie die Ventilfeder und das Ventil.
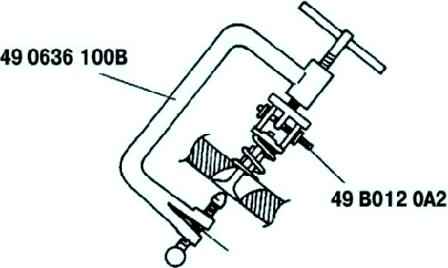
Entfernen Sie mit einem Spezialwerkzeug die Öldichtung (Abb. 3).
Entfernen Sie das Rezirkulationsrohr.
Entfernen Sie das Gehäuse der Auslassrohre des Kühlsystems.
Erkennung
Ventilführung prüfen
Messen Sie die Dicke jedes Ventilkopfes (Abb. 4).
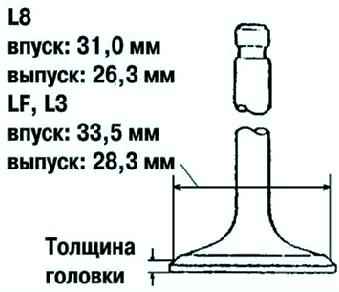
Wenn die Dicke nicht stimmt, ersetzen Sie das Ventil.
Kopfdicke: Einlass: 1,62 mm. Ausgabe: 1, 82 mm.
Ventillänge messen
Messen Sie die Länge jedes Ventils (Abb. 5). Wenn die Länge nicht stimmt, tauschen Sie das Ventil aus.
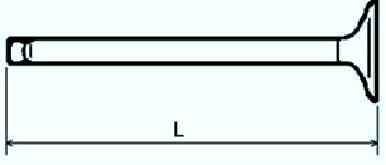
Standardlänge L: Einlass: 102,99 - 103,79 mm; Auslass: 104,25–105,05 mm.
Mindestlänge L: Einlass: 102,99 mm; Auslass: 103,79 mm.
Ventilschaftdurchmesser messen
Messen Sie mit einem Mikrometer den Schaftdurchmesser jedes Ventils in X- und Y-Richtung an drei Punkten (A, B und C), wie in Abbildung 6 dargestellt.
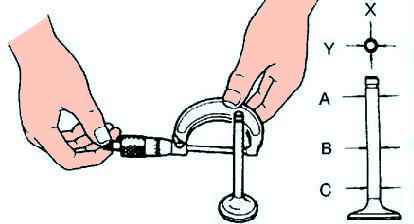
Wenn der Durchmesser nicht stimmt, ersetzen Sie das Ventil.
Standarddurchmesser: - Einlass: 5,470-5,485 mm; - Auslass: 5.465–5.480 mm.
Maximaler Durchmesser: - Einlass: 5.440 mm; - Auslass: 5,435 mm.
Messung des Innendurchmessers der Ventilführung
Messen Sie den Innendurchmesser jeder Ventilführung in X- und Y-Richtung an drei Punkten (A, B und C), wie in Abbildung 7 dargestellt.
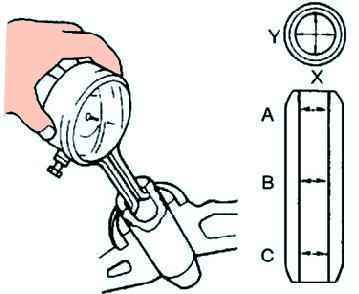
Wenn der Durchmesser nicht stimmt, ersetzen Sie die Ventilführung.
Standardbohrung: - Einlass: 5,509–5,539 mm; - Auslass: 5,509–5,539 mm.
Berechnen Sie das Spiel zwischen Ventilschaft und Ventilführung, indem Sie den Außendurchmesser des Ventilschafts vom Innendurchmesser der entsprechenden Ventilführung abziehen (Abbildung 8).
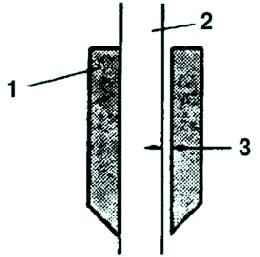
Wenn das Ergebnis nicht korrekt ist, ersetzen Sie das Ventil und/oder die Ventilführung.
Normales Spiel:
- - Einlass: 0,024–0,069 mm;
- - Auslass: 0,029–0,074 mm.
- - Maximaler Spalt: 0,10 mm.
Messen des Überstands der Ventilführung
Messen Sie die Überstandshöhe (Maß A) jeder Ventilführung, mit Ausnahme des unteren Ventilfedersitzes (Abb. 9).
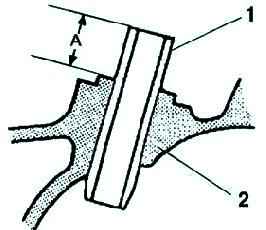
Wenn die Höhe nicht stimmt, ersetzen Sie die Ventilführung.
Standarddurchmesser:
- - Einlass: 12,2–12,8 mm;
- - Auslass: 12,2–12,8 mm.
Ventilführung austauschen
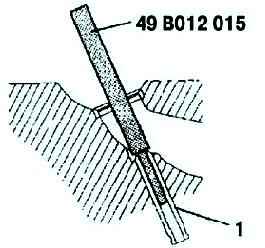
Entfernen Sie die Ventilführung mit dem Spezialwerkzeug von der Brennraumseite (Abb. 10).
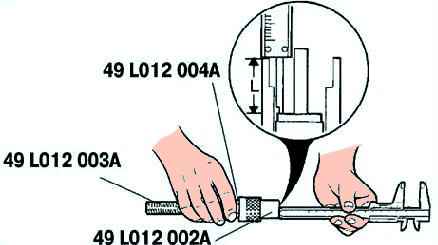
Montieren Sie die Spezialwerkzeuge so, dass die Tiefe L der angegebenen entspricht (Abb. 11). - Tiefe L: - Einlass: 12,2-12,8 mm; - Auslass: 12,2–12,8 mm
Einschieben der Ventilführung
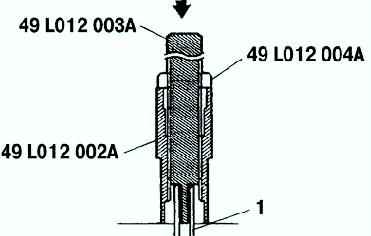
Drücken Sie die Ventilführung von der Seite gegenüber der Nockenwelle, bis das Spezialwerkzeug am Zylinderkopf anschlägt (Abb. 12).
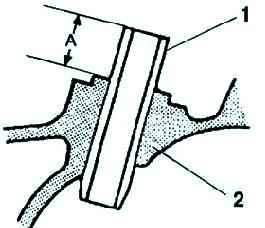
Überprüfen Sie, ob die Überstandshöhe der Ventilführung (Maß A) korrekt ist (siehe Abb. 13).
Standardhöhe: - Einlass: 12,2–12,8 mm; - Auslass: 12,2–12,8 mm
Ventilsitz prüfen und reparieren
Messen Sie die Breite des Ventilsitzkontaktbereichs.
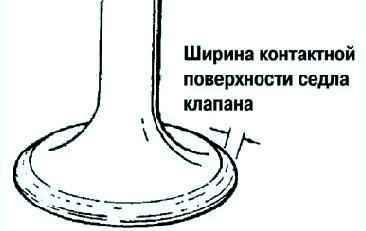
Wenn nötig, bearbeiten Sie den Ventilsitz oder die Ventilscheibe mit dem entsprechenden Werkzeug (Abb. 14). Standardbreite: 1,2–1,6 mm.
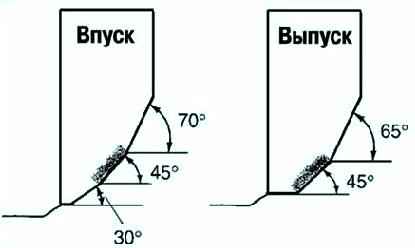
Überprüfen Sie die Ausrichtung der Kontaktfläche zum Ventilsitz (Abb. 15).
Wenn die Kontaktfläche nach außen verschoben ist, bearbeiten Sie den Ventilsitz mit einem Schneidwerkzeug mit einem Arbeitswinkel von 70° (Einlass) oder 65° (Auslass) und einem Schneidwerkzeug mit einem Winkel von 45°.
Wenn die Kontaktfläche nach innen verschoben ist, bearbeiten Sie den Ventilsitz mit einem Schneidwerkzeug mit einem Arbeitswinkel von 30° (Einlass) oder 0° (Auslass) und einem Schneidwerkzeug mit einem Winkel von 45°.
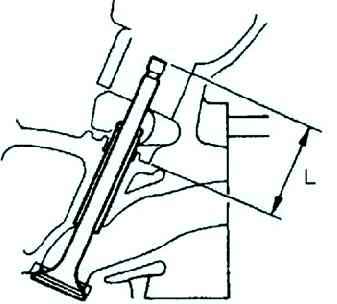
Überprüfen Sie die Ventilsitztiefe. Messen Sie den Überstand (Maß L) des Ventilschafts (Abb. 16).
Wenn die gemessene Höhe nicht korrekt ist, ersetzen Sie den Zylinderkopf.
Standardgröße L:
- - Einlass: 40,64–42,24 mm;
- - Auslass: 40,50–42,10 mm.
Ventilfederprüfung
Üben Sie eine Druckkraft auf die Feder aus und prüfen Sie die Höhe der Feder (Abb. 17).
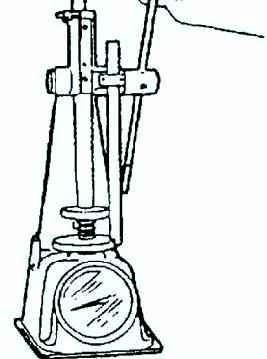
Wenn die Höhe nicht stimmt, ersetzen Sie die Ventilfeder.
Klemmkraft: 494,9 N. Standardhöhe: 27,80 mm.
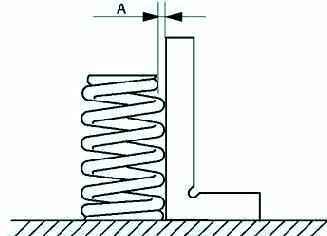
Messen Sie die Unrundheit der Ventilfeder mit einem Winkel, wie in Abbildung 19 dargestellt.
Drehen Sie die Ventilfeder um 360°, um den größten Abstand „A“ zu messen.
Wenn die Fehlausrichtung nicht korrekt ist, ersetzen Sie die Ventilfeder.
Maximale Fehlausrichtung der Ventilfeder: 1 % (2,10 mm).
Verteilung prüfen Welle
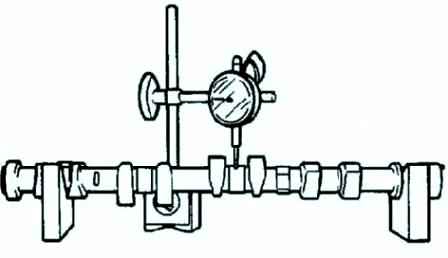
Montieren Sie die Lagerzapfen Nr. 1 und Nr. 5 der Nockenwelle auf Prismen.
Messen Sie den Schlag der Nockenwelle (Abb. 20). Wenn der Rundlauf nicht korrekt ist, ersetzen Sie die Nockenwelle. Maximaler Rundlauf: 0,03 mm.
Messen Sie die Höhe der Nockenkontur an zwei Punkten, wie in Abbildung 21 gezeigt.
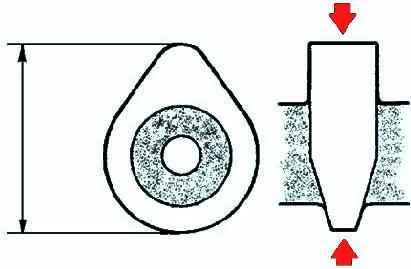
Wenn die Höhe nicht stimmt, ersetzen Sie die Nockenwelle.
Hals Nr. 1. Standard-Nockenwellenhöhe L8:
- - Einlass – 40,79 mm;
- - Freigabe – 41,08 mm.
- Nockenwelle LF, L3:
- - Einlass – 42,12 mm;
- - Freigabe – 41,08 mm.
Mit variabler Ventilsteuerung:
- - Einlass – 42,44 mm;
- - Freigabe – 41,18 mm.
- - Hals Nr. 5
Standard-Nockenwellenhöhe L8:
- - Einlass – 40,692 mm;
- - Auslass – 40,982 mm.
LF, L3 Nockenwelle:
- - Einlass – 42,022 mm;
- - Auslass – 40,982 mm.
Mit variabler Ventilsteuerung:
- - Einlass – 42,342 mm;
- - Auslass – 41,082 mm.
Messen des Durchmessers des Nockenwellenzapfens
Messen Sie die Durchmesser des Wellenzapfens in X- und Y-Richtung an zwei Punkten (A und B), wie in Abbildung 22 dargestellt.
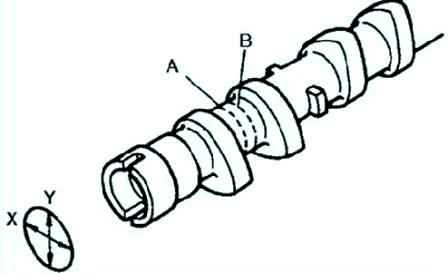
Wenn die Werte nicht korrekt sind, ersetzen Sie die Nockenwelle.
Standarddurchmesser: 24,96 - 24,98 mm.
Mindestdurchmesser: 24,95 mm.
Messen des Radialspiels des Nockenwellenzapfens
Entfernen Sie den Ventilstößel.
Platzieren Sie kalibrierte Kunststoffdrahtstücke oben auf den Nockenwellenzapfen und positionieren Sie sie entlang der Achse (Abb. 23).
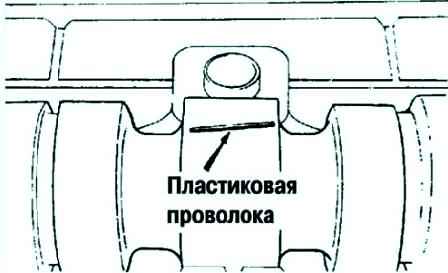
Bauen Sie den Nockenwellenlagerdeckel ein.
Entfernen Sie den Nockenwellenlagerdeckel.
Messen Sie das Radialspiel. Wenn das Spiel nicht korrekt ist, ersetzen Sie den Zylinderkopf.
- Normaler Spalt 0,04–0,08 mm
- Maximaler Abstand: 0,09 mm
Messung des Axialspiels des Nockenwellenzapfens
Bauen Sie den Nockenwellenlagerdeckel ein.
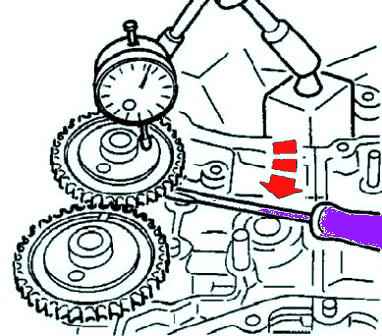
Messen Sie das Axialspiel der Nockenwelle (Abb. 24).
Wenn das Spiel nicht korrekt ist, ersetzen Sie den Zylinderkopf oder die Nockenwelle.
Standard-Axialspiel: 0,09 - 0,24 mm.
Maximales Axialspiel: 0,25 mm.
Entfernen Sie den Nockenwellenlagerdeckel erneut.
Überprüfung des Ventilstößels
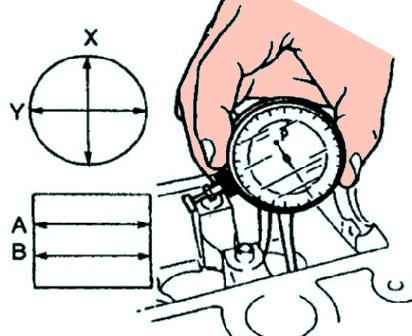
Messen Sie den Innendurchmesser der Stößelbohrung in X- und Y-Richtung an zwei Punkten (A und B) (Abb. 25).
Innendurchmesser: 31,00 - 31,03 mm.
Messen Sie den Außendurchmesser des Stößelkörpers in X- und Y-Richtung an zwei Punkten (A und B) (Abb. 26).
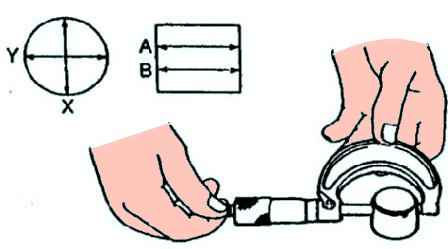
Außendurchmesser: 30,97–30,98 mm.
Subtrahieren Sie den Außendurchmesser des Ventilstößelkörpers vom Innendurchmesser der Ventilstößelbohrung.
Wenn das Spiel nicht korrekt ist, ersetzen Sie den Ventilstößel oder Zylinderkopf.
Standardspalt: 0,02 - 0,06 mm. Maximal: 0,15 mm.
Zylinderkopfbaugruppe
Installieren Sie das Auslassgehäuse des Kühlsystems.
Installieren Sie das Rezirkulationsrohr.
Einbau der Öldichtung
Drücken Sie die Ventilschaftdichtung von Hand auf die Ventilführung.
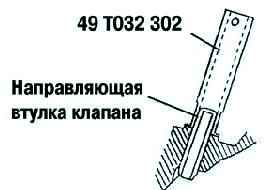
Mit einem Spezialwerkzeug und einem Nylonhammer leicht andrücken (Abb. 27).
Montieren Sie die Ventile, Ventilfedern und Ventilfeder-Abdeckkappen.
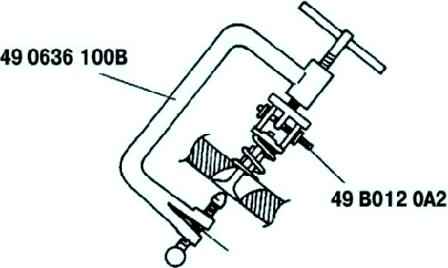
Montieren Sie die Ventilkeile mit den Spezialwerkzeugen (Abb. 28).
Montieren Sie die Motorhebeösen.
Eine neue Zylinderkopfdichtung einbauen.