Clutch elements are removed for replacement or repair
Preparing the car for the task. We install the car on a lift or inspection ditch
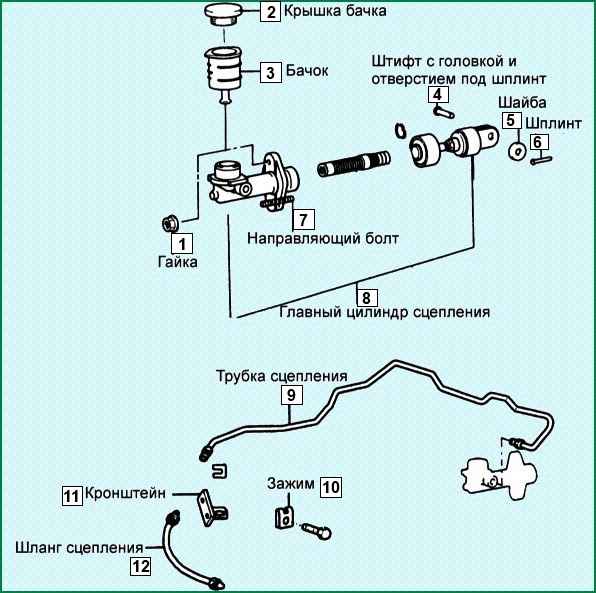
Unscrew the drain plug on the slave cylinder and drain the clutch fluid
Remove the cotter pin, washer and pin
Disconnect the tube from the side of the clutch master cylinder
Unscrew the clutch master cylinder bolt
Remove the clutch tube clamps
Unscrew the nut on the clutch tube, fixing the nut on the clutch hose before that
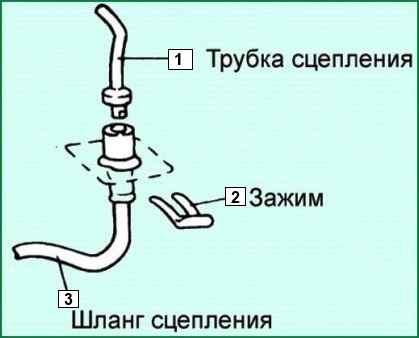
Remove the clamp and disconnect from the bracket
Remove the clutch hose
Disconnect the clutch hose from the clutch slave cylinder
Check the clutch hose and tube for cracks and blockages
Clutch master cylinder disassembly
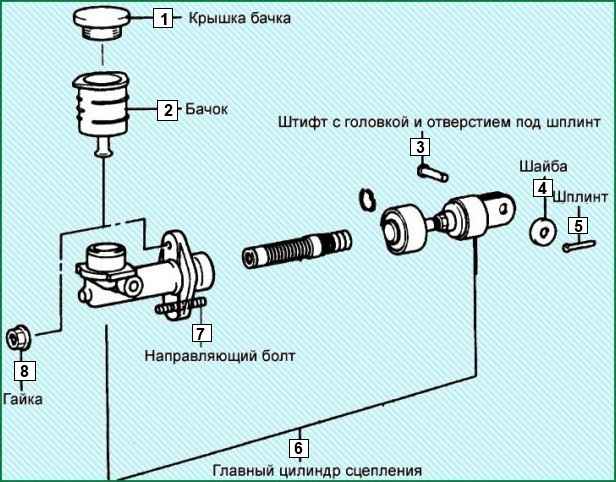
We clamp the main cylinder in a vise
Remove the piston ring
Remove the pusher and piston
Remove the tank fastening tape, tank and cover
Be careful not to damage the tappet and clutch master cylinder surface
Do not disassemble the piston assembly
Check
Check the inside of the cylinder body for rust, pitting, or gouging.
Clean the dismantled parts in solvent and blow out all parts and passages with compressed air.
Check the piston cup for wear.
Check the piston for rust, pitting, or gouging.
Check the hydraulic clutch tube for damage.
Measure the inner diameter of the clutch master cylinder and the outer diameter of the piston.
Measure the inner diameter of the clutch master cylinder in three sections (at the base, center and top) in two perpendicular directions.
If the clearance between piston and cylinder is greater than the allowable value, replace the master cylinder and/or piston assembly.
Gap: 0.15 mm
Assembly
Before assembling, we lubricate the piston and the inner cavity of the cylinder with clutch fluid
Installing the piston assembly
Connect the clutch hose to the clutch slave cylinder
Manually we tighten the nut that secures the hose to the tube, then tighten it to the recommended torque
Installing the hose clamps to the bracket
Installing the clutch master cylinder
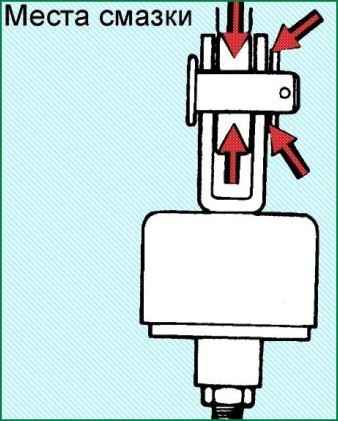
Before installation, lubricate the bushing, pin with SAE J 310, NGLI No. 2 grease
Install the pusher on the clutch pedal
Pour fluid into the clutch master cylinder
Pumping the hydraulic clutch
Removing and repairing the clutch slave cylinder
Unscrew the drain plug (A) and drain the clutch fluid
Fix the clutch hose between the clutch slave cylinder and the tube
We unscrew the bolt securing the working cylinder and remove the working cylinder
Install the slave cylinder in reverse order
Disassembly of the slave cylinder
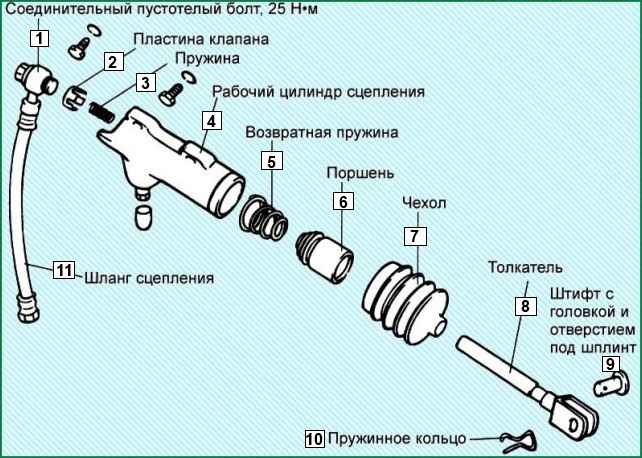
Remove the clutch hose, valve plate, spring, pusher and boot
Removing dirt from the piston hole in the clutch cylinder
Remove the piston and cuff, supplying compressed air through the hole for connecting the hydraulic tube while:
- close the opening of the working cylinder with a rag in order to catch the piston pushed out by compressed air.
Check the slave cylinder for damage
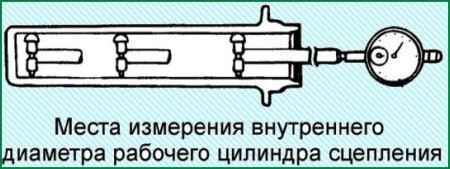
Measure the inner diameter of the clutch slave cylinder
Measure the inner diameter of the clutch master cylinder in three sections (at the base, center and top) in two perpendicular directions.
If the clearance between the piston and the cylinder is too large, replace the master cylinder and/or the piston assembly.
Gap: 0.15 mm
Removing and installing clutch discs
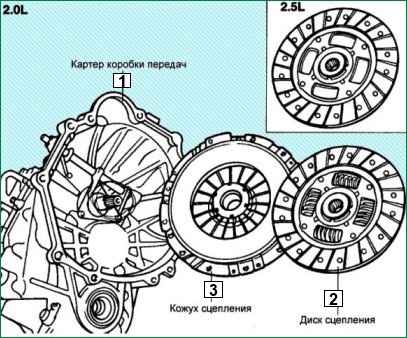
Remove the manual transmission
To remove the gearbox, you need to remove the air filter connections, bracket, disconnect the wires, etc.
Remove the release lever, for this:
- - unscrew the nuts securing the release lever
- - remove the pin and spring ring from the clutch cylinder
- - remove the release lever
Unscrew the bolts and remove the clutch release cylinder
We unscrew the bolts securing the gearbox to the engine, and remove the gearbox
Using pliers, remove the clutch release bearing from the clutch housing diaphragm spring
Rotate the clutch bearing in any direction to determine the position of the circlip.
Insert the pliers under the wave washer as shown and place it in the center of the retaining spring ring.
Increase the space around the circlip by pressing on the bearing as shown
Expanding the snap ring as shown
While holding the snap ring in the expanded state, remove the clutch release bearing
Install the mandrel to center the clutch disc
Gradually loosen the bolts securing the clutch basket diagonally, turning each bolt half a turn until the action of the diaphragm spring stops, and then unscrew all the bolts by hand
Remove the clutch cover with pressure plate and clutch disc
Remove the fork shaft and bushing
Checking the clutch discs
Clean the dust from the clutch cover using a vacuum brush or vacuum cleaner. Do not use compressed air.
Remove the flywheel and check the crankshaft rear O-ring for leaks. If necessary, replace the O-ring.
Check the pressure plate for cracks, burn marks and surface wear.
Check the friction surface of the flywheel for partial damage, cracks and wear.
Check the condition of the friction linings of the clutch disc and if there are traces of oil or mechanical damage on them, replace the clutch disc.
Check the protrusion of the friction linings over the rivet heads. If the protrusion is less than acceptable, replace the clutch disc.
Protrusion: 0.3 mm
Check the hub splines and clutch disc damper springs for excessive wear.
Clean the friction surface of the pressure plate with cleaning solvent.
Check the diaphragm spring at the points of contact with the clutch release bearing for wear, cracks and determine the difference in height of the ends of the diaphragm spring.
If there are defects, replace the clutch cover with pressure plate.
Difference in the height of the ends of the diaphragm spring: 0.5 mm
Make sure the flywheel has three dowel pins to center the clutch cover.
The clutch release bearing is sealed and must not be flushed.
Check the condition of the clutch release bearing, which should rotate easily, evenly and silently, and there should be no play in it.
The working surface of the bearing acting on the pressure spring must be smooth, without cracks, local corrosion or wear.
If there is uneven wear at the contact points of the bearing with the release fork, replace the release bearing.
If there is uneven wear at the contact points of the clutch release fork with the bearing, replace the clutch release fork.
Installation
Apply grease to the splines of the clutch disc.
Lubricant: CASMOLY L 9508
When installing the clutch, apply grease to all moving parts, but do not use excessive grease, as this may cause the clutch to slip.
Install the clutch disc and center it with special tool 09411-11000.
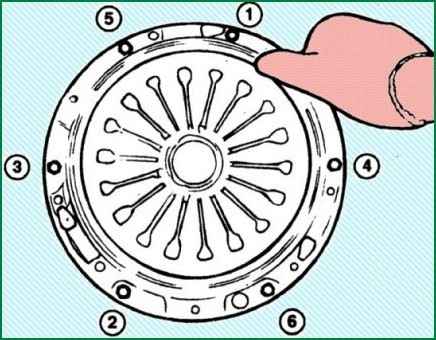
Mount the clutch cover with pressure plate onto the flywheel guide pins.
Gradually, in a diagonal sequence and in a certain order, tighten the bolts securing the clutch cover.
Tightening torque:
- 2.0L engine: 15 - 22 Nm
- 2.5L engine: 20-27 Nm
Align the clutch release bearing, decompress the circlip and install the bearing on the clutch housing bushing.
Apply CASMOLY L9508 Multipurpose Grease to the bearing bush and release fork contact points.
Install the release lever to the release fork.
If gearboxes are installed on the engine without following this step, the clutch release bearing may be disengaged as the clutch release fork rotates freely.
Mount the gearbox to the engine.
Then, while pushing the release lever in the direction of the arrow, move the cam, as a result of which the clutch release bearing and clutch cover will be installed correctly.
Stroke of release lever: no more than 3°
If the release lever travel is more than 3°, then the clutch release bearing and clutch cover are not installed correctly.