Checking the kingpin and bushings for wear
The check is carried out with adjusted front wheel bearings
Raise the front wheel with a jack.
Swing the wheel vertically.
If play is felt (the upper outer edge of the brake caliper moves more than 0.5 mm - this distance can be measured, for example, using an indicator), then the kingpin and bushings are worn out and need to be replaced.
Mount the vehicle on the wheels and use a feeler gauge to measure the clearance between the upper knuckle lug and the front suspension beam boss.
The maximum allowable gap is 0.15 mm.
Eliminate the gap from 0.15 to 1 mm by selecting the appropriate set of shims installed between the upper eye of the steering knuckle and the boss of the front suspension beam.
If the clearance is greater than 1 mm, replace the thrust bearing.
Disassembly and repair of the pivot joint
Raise the front of the car.
Remove the front wheels and place stops under the beam.
Using the “10” key, unscrew the two bolts securing the upper cover of the kingpin bearing
Remove the cover of the upper kingpin bearing with a grease fitting.
With a “19” head, we unscrew the two bolts securing the brake caliper.
Remove the caliper and tie it with wire so that it does not interfere.
For convenience, we remove the shock absorber (see Replacing the shock absorber).
Using pliers, we unpin the nut securing the transverse link to the lever
Using the “24” wrench, unscrew the nut securing the transverse link to the lever. The nut should be left on the finger thread
Using the swing arm as a support, we “strain” the finger, resting the mounting blade on the transverse link.
By hitting the lever with a hammer, we press out the finger.
Having unscrewed the nut, we remove the pin from the hole of the transverse link.
Using the “10” key, unscrew the two mounting bolts and remove the lower cover of the kingpin bearing
Using a key or a “17” head, unscrew the nut of the kingpin stopper.
Use a soft metal hammer to knock out the stopper
Using a soft metal mandrel, we knock out the king pin from top to bottom
Remove the steering knuckle
Remove the thrust bearing.
Remove the protective cap from the thrust bearing.
Remove the rubber sealing ring from the upper eye of the steering knuckle.
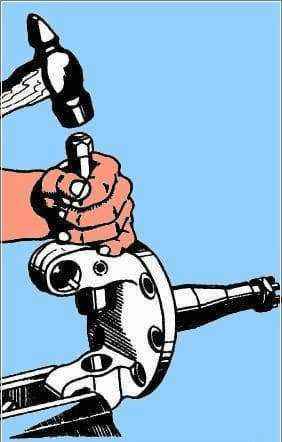
We clamp the steering knuckle in a vise and knock out the bushings from its eyes through the mandrel
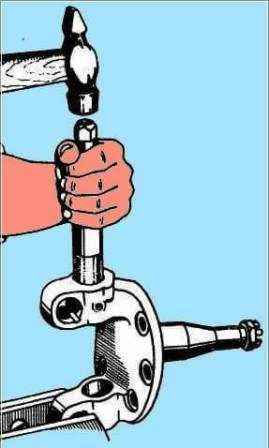
We clean the lugs of the steering knuckle and press new bushings into them using a mandrel.
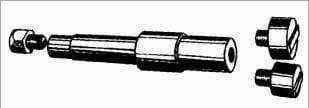
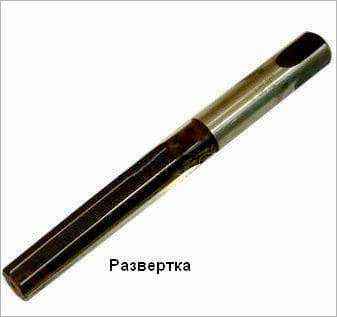
Reamer for reaming pivot bushings
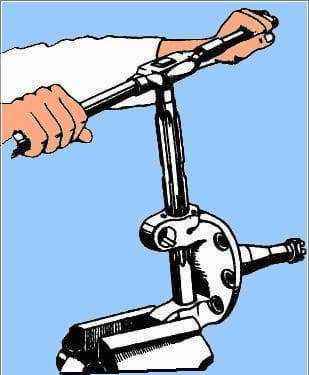
We unfold both bushings using a reamer to a diameter of 25 + 0.053 + 0.020 mm in one pass to ensure the alignment of the bushings
We wash all the details in kerosene. Lubricate the kingpin and its stopper with Litol-24 grease.
We assemble the pivot connection in the following sequence:
Insert the kingpin into the lower lug of the fist, while the lubrication groove of the kingpin should be located below, and the flat for the stopper faces the longitudinal axis of the car.
We put a thrust bearing on the kingpin.
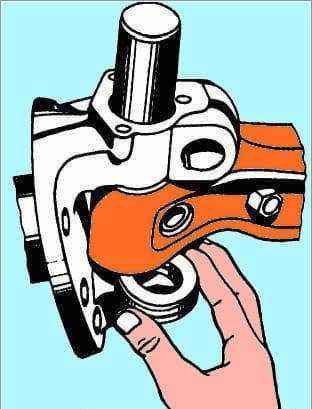
We install the steering knuckle on the beam, controlling the alignment of the holes through the upper eye of the fist.
Move the king pin up until the flat matches the hole for the stopper.
After installing the covers, we inject the connection with Litol-24 grease.
We finally assemble all the parts in reverse order and adjust the toe-in.
Lubricating the pivot joint
Lubricate the pivot connection after 10 tons ys. km.
It is more convenient to work on a viewing ditch.
We carefully wipe the upper and lower kingpin grease fittings with a rag.
Using an oil syringe, we inject Litol-24 or FIOL grease into the upper oiler
Using an oil syringe, we inject lubricant into the lower oiler until it appears from the joint gaps
If the grease does not come out of at least one gap, you should “pump” the connection with a mixture of engine oil and kerosene in a 1: 1 ratio and then lubricate.