Um Schäden an der Lackierung der Kotflügel der Karosserie zu vermeiden, ist es notwendig, eine spezielle Beschichtung zu verwenden
Um Schäden am Zylinderkopf zu vermeiden, warten Sie, bis der Motor abgekühlt ist, bevor Sie ihn entfernen
Achten Sie beim Entfernen der Zylinderkopfdichtung aus Metall darauf, dass Sie sie nicht verpassen oder die Kontaktfläche des Blocks mit dem Kopf beschädigen
Wenden Sie beim Trennen eines Kabels Kraft direkt auf den Stecker und nicht auf das Kabel an.
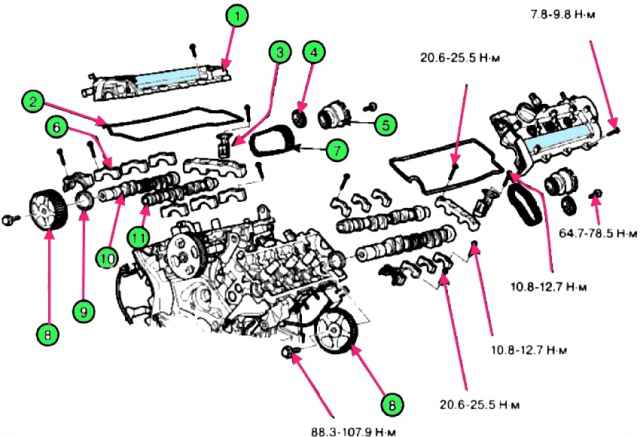
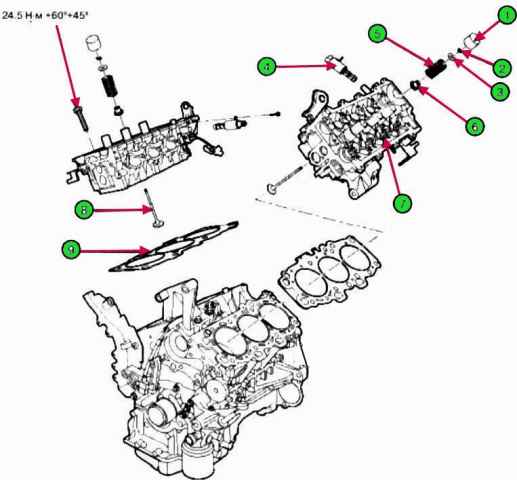
Um einen falschen Anschluss zu vermeiden, müssen alle Kabel mit Etiketten versehen werden.
Drehen Sie die Kurbelwellenriemenscheibe, um den Kolben des ersten Zylinders in die Position des oberen Totpunkts (OT) zu bringen.
Entfernen Sie den Luftkanal (A) und die Batterie (B), nachdem Sie die Plus- und Minuspole abgeklemmt haben.
Entfernen Sie die Motorabdeckung (A).
Den Lufteinlassschlauch und die Luftfilterbaugruppe trennen.
Ziehen Sie den MAF-Sensorstecker (A) ab.
Lösen Sie den Entlüftungsschlauch (B) vom Luftfilterschlauch.
Entfernen Sie den Lufteinlassschlauch und die Luftfiltereinheit (C).
Ziehen Sie den PCM-Stecker (D) ab.
Entfernen Sie die oberen und unteren Kühlerschläuche (B).
Entfernen Sie den Kraftstoffeinlassschlauch (A) von der Hauptleitung.
Elektrische Anschlüsse trennen.
Trennen Sie die Stecker Nr. 1, Nr. 2 Klopfsensor (A, B), Einspritzdüsen (C), Zündspulenverkabelung (D) und Stecker Nr. 1 VIS (E).
Lösen Sie die Steckverbinder der Lambdasonde in der ersten Reihe.
Hochdruckschlauchanschlüsse (A, B, C) und Erdungskabel (D) trennen. Kondensator (E) und Zündspule (F).
Trennen Sie die Stecker Nr. 1 und Nr. 2 der Ventile (A, B) und des Öltemperatursensors (C).
Die Steckverbinder des MAP-Sensors (A), der Drosselklappenstellungssteuerung (B) und der positiven Kurbelgehäuseentlüftung (C) trennen.
Den Stecker der Lichtmaschine (A) und des A/C-Kompressors (B) abziehen.
Nockenwellenpositionssensor Bank Nr. 2 und Stecker (B) des Kühlmitteltemperatursensors trennen.
Die Steckverbinder (A, B) der Lambdasonde der Reihe Nr. 2 und den Kurbelwellenpositionssensor (C) trennen.
Den Stecker des Nockenwellensensors Bank Nr. 1 (A) trennen.
Den Bremsunterdruckschlauch (A) trennen.
Entfernen Sie die Heizungsschläuche.
Entfernen Sie den Nebenantriebsriemen (A).
Entfernen Sie die Servolenkungspumpe.
Entfernen Sie die Abgaskrümmerbaugruppe.
Entfernen Sie die Ansaugkrümmerbaugruppe.
Zahnriemen entfernen.
Entfernen Sie die Zündspulen.
Entfernen Sie den Thermostat.
Den Zylinderkopfdeckel (A) entfernen.
Entfernen Sie den Nockenwellenlagerdeckel (A).
Entfernen Sie den Steuerkettenspanner (A).
Entfernen Sie die Nockenwelle.
Entfernen Sie die hintere Abdeckung des Antriebsriemens Reihe Nr. 2 (A).
Entfernen Sie die hintere Abdeckung des Antriebsriemens Reihe Nr. 1 (A).
Entfernen Sie die Steckerhalterung des Kurbelwellenpositionssensors (A)
Entfernen Sie die Zylinderkopfbaugruppe.
Entfernen Sie die Schrauben in 2-3 Schritten in der im Bild gezeigten Reihenfolge.
Unsachgemäßer Einbau kann zu Schäden am Zylinderkopf führen.
Legen Sie nach dem Entfernen des Zylinderkopfs den Block auf eine Holzoberfläche.
Stellen Sie sicher, dass die Fläche zwischen Blockkopf und Block nicht beschädigt ist.
INSTALLATION
Spülen Sie alle Teile vor der Installation,
Verwenden Sie immer eine neue Zylinderkopfdichtung und Auspuffkrümmerdichtung.
Immer neue Zylinderkopfschrauben verwenden.
Die Zylinderkopfdichtung ist aus Metall, achten Sie darauf, sie nicht zu beschädigen.
Drehen Sie die Kurbelwelle, um den Zylinder Nr. 1 auf OT zu stellen.
Nach dem Einbau der Zylinderblockdichtung den Blockkopf einbauen.
Beim Einbau Maße der linken und rechten Zylinderkopfdichtung angeben.
Zylinderkopfschrauben mit Unterlegscheibe in folgender Reihenfolge festziehen:
Bei der Montage der Unterlegscheibe muss die markierte Fläche oben liegen.
Tragen Sie beim Einbau der Schrauben Motoröl auf die Schraubengewinde und die Oberfläche der Unterlegscheiben auf. Anzugsdrehmoment: 24,5 Nm.
Mit dem Spezialwerkzeug (09221-4А000) die Schrauben mit der Winkelanzugsmethode anziehen.
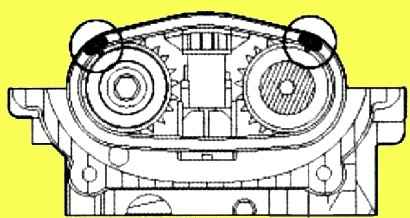
Bauen Sie die Phasenschieberbaugruppe und das Steuerkettenrad mit Fixierstift in den an der Einlassnockenwelle montierten Phasenschieber ein.
Stellen Sie sicher, dass sich der Stift nicht in der Ölversorgungsöffnung befindet. Anzugsdrehmoment: 66,7 - 78,5 Nm.
Drehen Sie nach dem Einbau der Phasenschieberschrauben die Phasenschieberbaugruppe von Hand gegen den Uhrzeigersinn und bringen Sie den Stift in die entsprechende Position.
Befestigen Sie den Sechskantbereich der Nockenwelle mit einem Schraubstock und ziehen Sie dann die Schrauben fest. Fixieren Sie nicht den Phasenschieber oder das Kettenrad.
Installieren Sie die Nockenwelle auf der Zylinderkopfbaugruppe.
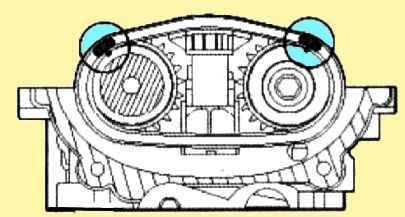
Richten Sie die Markierungen auf der Einlass- und Auslassnockenwelle und den Steuerkettenrädern aufeinander aus.
Bei der Montage müssen beide Markierungen oben sein
Einlass- und Auslassnockenwelle auf dem Zylinderkopf einbauen und dabei die Markierungen ausrichten.
Den Steuerkettenspanner einbauen.
Setzen Sie den Stift ein, indem Sie auf den Kettenspanner drücken.
Den Spanner (A) am Zylinderkopf einbauen.
Entfernen Sie den Stift nach der Installation vom Spanner.
Die Nockenwellen-Lagerdeckel einbauen. Anzugsmoment: Schraube (A: 6x38): 10,8 - 12,7 Nm, Schraube (6: 8x38): 20,6 - 22,5 Nm.
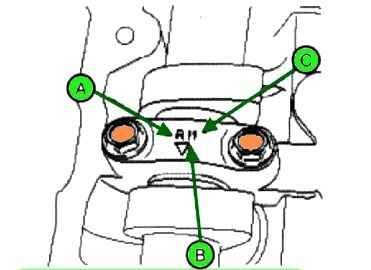
Achten Sie beim Einbau der Lagerdeckel auf die Markierungen wie in der Abbildung gezeigt und bringen Sie sie in der richtigen Position an.
Drehen Sie beim Einbau der Lagerdeckel die Kurbelwelle, um den Kolben in der Mitte des Blocks zu platzieren es kann zu einer Kollision zwischen dem Ventil und dem Kolben kommen.
Mit dem Spezialwerkzeug (09214-21000) den Nockenwellen-Öldichtring einbauen.
Motoröl vor dem Einbau auftragen
Die Nockenwellenabdeckung muss fest mit der Zylinderkopfeinheit verbunden sein.
Keine außermittige Belastung erzeugen.
Bauen Sie das Nockenwellenrad ein.
Halten Sie den Sechskantbereich der Nockenwelle in einen Schraubstock und schrauben Sie die Schrauben ein. Anzugsmoment: 88,3 - 107,9 Nm.
Falls Sie die Nockenwelle durch eine neue ersetzen, überprüfen Sie das Ventilspiel und bauen Sie dann den Stößel ein.
Um zu verhindern, dass Ventil und Kolben kollidieren, drehen Sie das Kurbelwellenrad 3 Umdrehungen vom OT des ersten Zylinders und messen Sie dann das Ventilspiel.
Die Steckerhalterung des Kurbelwellenpositionssensors einbauen.
Die hintere Abdeckung (A) des Zahnriemens der ersten Reihe einbauen.
Die hintere Abdeckung (A) des Zahnriemens der zweiten Reihe einbauen.
Die Länge von Schraube B ist größer als die Länge von Schraube C.
Zylinderkopfhaube einbauen
Entfernen Sie Öl, Staub und Dichtmittel von der Zylinderoberfläche, bevor Sie die Zylinderkopfhaube montieren.
Bauen Sie die Zylinderkopfhaube fünf Minuten nach dem Auftragen des Dichtmittels auf die Nockenwellenabdeckung wieder zusammen.
Ziehen Sie die Zylinderkopfschrauben in der richtigen Reihenfolge fest (A). Anzugsdrehmoment: 7,8 - 9,8 Nm.
Starten Sie den Motor erst 30 Minuten nach dem Einbau der Zylinderkopfhaube.
Bauen Sie keine alte Zylinderkopfdichtung ein.
Zahnriemen einbauen.
Markierungen am linken und rechten Nockenwellenrad ausrichten.
Um zu verhindern, dass Ventil und Kolben kollidieren, drehen Sie das Kurbelwellenrad 3 Umdrehungen vom OT des ersten Zylinders und richten Sie dann die Markierungen auf den Kettenrädern aus.
Nachdem Sie die Markierungen auf den Nockenwellenrädern ausgerichtet haben, drehen Sie das Kurbelwellenrad 3 Umdrehungen im Uhrzeigersinn und richten Sie die Markierung des Kurbelwellenrads aus, um den Kolben des Zylinders Nr. 1 auf den oberen Totpunkt zu stellen.
Zahnriemen einbauen.
Montage der Thermostatbaugruppe.
Die Ansaugkrümmerbaugruppe einbauen.
Bauen Sie die Abgaskrümmerbaugruppe ein.
Die Servolenkungspumpe einbauen.
Eingestellt Antriebsriemen (A).
Den Heizungsschlauch einbauen.
Den Bremsunterdruckschlauch (A) anschließen.
Schließen Sie die Motorkabelstecker an.
Den Stecker des Nockenwellensensors der ersten Reihe (A) anschließen.
Die Stecker des Kurbelwellenpositionssensors (C), der vorderen und hinteren Lambdasonden (A, B) der zweiten Reihe anschließen.
Die Stecker des Wassertemperatursensors (B) und des Nockenwellenpositionssensors (A) der zweiten Reihe anschließen.
Anschlüsse der Lichtmaschine (A) und des A/C-Kompressors (B) anschließen.
Schließen Sie die Stecker des Ölabsolutdrucksensors (A), des Drosselklappenstellungssensors (B) und des positiven Kurbelgehäuseentlüftungsventils (C) an.
Verbinden Sie die Stecker von Ventil 1 und Nr. 2 (A, B) und den Öltemperatursensor (C).
Schließen Sie die Stecker der Einspritzdüsen (A, B, C), Massekabel (D), Kondensator (E) und Zündspulen (F) an.
Schließen Sie die vorderen und hinteren Lambdasondenstecker (A) der ersten Reihe an.
Klopfsensorstecker 1 und 2 (A, B), Einspritzdüsen (C), Zündspulenkabel (D) und VIS (E) anschließen.
Den Kraftstoffeinlassschlauch (A) am Hauptrohr anbringen.
Den oberen (A) unteren (B) Kühlerschlauch einbauen.
Installieren Sie den Lufteinlassschlauch und die Luftfiltereinheit.
Anschluss anschließen wir sind PCM (D).
Installieren Sie den Lufteinlassschlauch und die Luftfiltereinheit (C).
Verbinden Sie den Entlüftungsschlauch (B) mit dem Filterschlauch.
Schließen Sie den Stecker des Luftmassensensors an.
Kühlmittel einfüllen.