Sensores ECM y controlador ME17.9.71 para los estándares de toxicidad EURO-5 de un automóvil Chevrolet Niva
El sistema de control electrónico del motor (ECM) consta de un controlador, sensores para los parámetros de funcionamiento del motor y del vehículo, así como actuadores
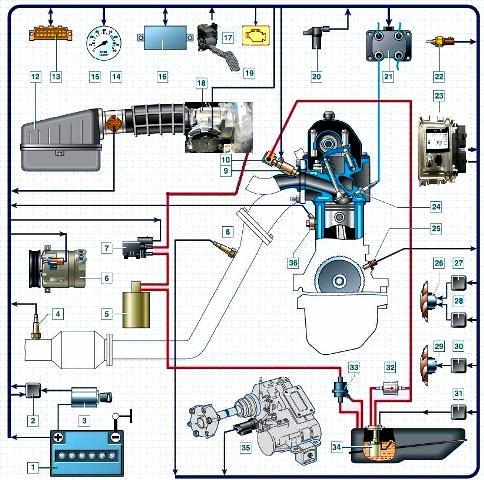
Esquema del sistema de control electrónico del motor: 1 - batería; 2 - relé principal; 3 - cerradura de encendido; 4 - sensor de concentración de oxígeno de diagnóstico; 5 - adsorbente; 6 - compresor de aire acondicionado; 7 - válvula de purga del adsorbedor; 8 - sensor de concentración de oxígeno de control; 9 - boquilla; 10 - riel de combustible; 12 - filtro de aire; 13 - conector de diagnóstico; 14 - sensor de flujo de aire masivo; 15 - tacómetro; 16 - bloque inmovilizador; 17 - pedal de gas electrónico; 18 - conjunto del acelerador; 19 - lámpara de control para un mal funcionamiento del sistema de gestión del motor; 20 - sensor de fase; 21 - bobina de encendido; 22 - sensor de temperatura del refrigerante; 23 - controlador; 24 - bujía; 25 - sensor de posición del cigüeñal; 26 - ventilador derecho del sistema de refrigeración; 27 - relé adicional; 28 - relé del ventilador derecho del sistema de refrigeración; 29 - ventilador izquierdo del sistema de enfriamiento; 30 - relé del ventilador izquierdo del sistema de refrigeración; 31 - relé de la bomba de combustible; 32 - filtro de combustible; 33 - válvula de gravedad; 34 - módulo de combustible; 35 - sensor de velocidad; 36 - sensor de golpe
Controlador
El controlador es una minicomputadora para fines especiales, consta de memoria de acceso aleatorio (RAM), memoria de solo lectura programable (PROM) y memoria reprogramable eléctricamente (EPROM).
La memoria RAM es utilizada por el microprocesador para almacenar temporalmente información actual sobre el funcionamiento del motor (parámetros medidos) y datos calculados.
Además, los códigos de error se escriben en la RAM.
Esta memoria es volátil, es decir, cuando se interrumpe la alimentación (desconectando la batería o desconectando el bloque de cableado del controlador), su contenido se borra.
La EPROM almacena el programa de control del motor, que contiene una secuencia de comandos operativos (algoritmos) y datos de calibración (configuraciones).
La PROM determina los parámetros más importantes del funcionamiento del motor: la naturaleza del cambio en el par y la potencia, el consumo de combustible, el tiempo de encendido, la composición de los gases de escape, etc. La PROM no es volátil, es decir, el contenido de su memoria no cambia cuando se apaga la alimentación.
ERPROM almacena los ID del controlador, el motor y el vehículo. Registra los parámetros operativos, así como las violaciones de la operación del motor y del vehículo. Es una memoria no volátil.
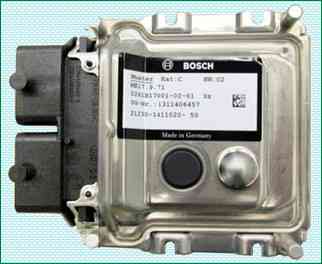
El controlador es la unidad central del sistema de control del motor.
Recibe información de los sensores y controla los actuadores, lo que garantiza un funcionamiento óptimo del motor en un determinado nivel de rendimiento del vehículo.
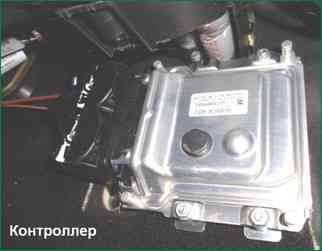
El controlador se encuentra en la zona de los pies del pasajero y se fija al mamparo.
El controlador controla los actuadores, como los inyectores de combustible, el acelerador motorizado, la bobina de encendido, el calentador del sensor de oxígeno, la válvula de purga del recipiente y varios relés.
El controlador controla el encendido y apagado del relé principal (relé de encendido), a través del cual se suministra la tensión de alimentación de la batería a los elementos del sistema (excepto la electrobomba de combustible, el electroventilador, la centralita y el APS indicador de estado).
El controlador enciende el relé principal cuando se enciende el encendido.
Cuando se apaga el encendido, el controlador retrasa el apagado del relé principal durante el tiempo necesario para prepararse para el próximo encendido (finalización de los cálculos, ajuste del acelerador a la posición antes de arrancar el motor).
Cuando se enciende el contacto, el controlador, además de realizar las funciones mencionadas anteriormente, intercambia información con el APS (si la función de inmovilización está habilitada).
Si el intercambio determina que se permite el acceso al vehículo, entonces el controlador continúa realizando funciones de control del motor. De lo contrario, el motor se bloqueará.
El controlador también realiza una función de diagnóstico del sistema.
Se define en La presencia de fallas en los elementos del sistema enciende el dispositivo de señalización y almacena códigos en su memoria que indican la naturaleza de la falla y ayudan al mecánico a realizar reparaciones.
Sensor de masa de aire
El sistema de control del motor utiliza un MAF de hilo caliente con una respuesta de frecuencia de una señal de salida digital.
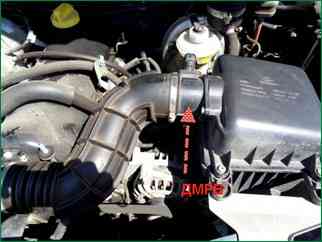
Se encuentra entre el filtro de aire y la manguera del tubo de admisión.
La señal MAF es una señal de frecuencia (Hz), cuya frecuencia de repetición de impulsos depende de la cantidad de aire que pasa por el sensor (aumenta al aumentar el flujo de aire).
La herramienta de escaneo lee el sensor como flujo de aire en kilogramos por hora.
Si ocurre un mal funcionamiento en el circuito DTV, el controlador almacena su código en su memoria y enciende el dispositivo de señalización.
En este caso, el controlador reemplaza las lecturas del sensor con un valor fijo de temperatura del aire (20 °C).
Sensores de posición del acelerador (TPS)
Se utilizan dos TPS en un sistema EAF.
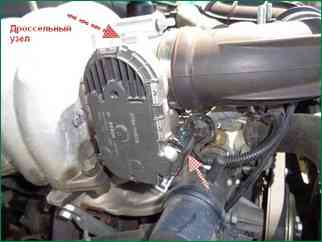
TPS son parte del acelerador eléctrico.
TPDZ es una resistencia de tipo potenciométrico, una de cuyas salidas se alimenta con un voltaje de referencia (5 V) desde el controlador, y la segunda se conecta a tierra desde el controlador.
Desde la salida conectada al contacto móvil del potenciómetro, la señal de salida del TPS se suministra al controlador.
El controlador controla la posición del acelerador eléctricamente según la posición del pedal del acelerador.
De acuerdo con las lecturas del TPS, el controlador monitorea la posición de la válvula de mariposa.
Cuando se enciende el encendido, el controlador coloca el amortiguador en la posición de prearranque, cuyo grado de apertura depende de la temperatura del refrigerante.
En la posición de aceleración previa al arranque, la señal de salida del TPS 1 debe estar entre 0,65 y 0,79 voltios, la salida del TPS 2 debe estar entre 4,21 y 4,35 V.
Si no enciende el motor y no presiona el pedal del acelerador dentro de los 15 segundos, el controlador desactiva el accionamiento eléctrico del tubo del acelerador y la válvula del acelerador se establece en la posición de 7-8% de apertura del acelerador.
En el estado desenergizado (LIMP HOME) del actuador del acelerador eléctrico, la señal de salida de TPS 1 está en el rango de 0,80-0,85 voltios, la salida de TPS 2 está en el rango de 4,15-4,20 V.
A continuación, si no se realiza ninguna acción en 15 segundos, aparecerá el modo de comprobación ("aprendizaje") de la posición 0 de la válvula de mariposa: cierre y apertura completos de la válvula de mariposa hasta la posición de prearranque y luego el actuador del acelerador volverá a cambiar al modo desenergizado.
En cualquier posición del acelerador, la suma de las señales TPS 1 y TPS 2 debe ser igual a (5 ± 0,1) V.
Si ocurre un mal funcionamiento en los circuitos TPS, el controlador desactiva el actuador del acelerador, almacena su código en su memoria y enciende el dispositivo de señalización.
En este caso, la válvula de mariposa se ajusta en la posición de 7-8 % de apertura del acelerador.
Pedal acelerador electrónico (EPA)
Los vehículos con un conjunto de acelerador electrónico utilizan un pedal de acelerador electrónico que transmite eléctricamente la señal de posición del pedal del acelerador al controlador.
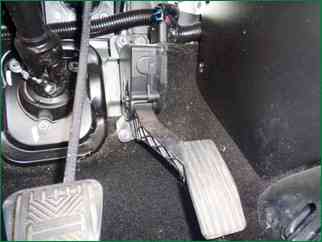
El pedal del acelerador electrónico está ubicado en un soporte debajo del pie derecho del conductor.
El pedal electrónico del acelerador utiliza dos sensores de posición del pedal del acelerador (APPS).
Los DPPA son resistencias de tipo potenciométrico alimentadas por un controlador de 5 V.
El DPPA se conecta mecánicamente al accionamiento desde la palanca del pedal.
Dos resortes independientes entre el brazo del pedal y el cuerpo proporcionan una fuerza de retorno.
Al recibir una señal eléctrica analógica del ESA, el controlador genera una señal para controlar la posición del acelerador.
El voltaje de salida del DPPA cambia en proporción a la presión del pedal del acelerador.
Cuando se suelta el pedal del acelerador, la señal DPPA 1 debe estar entre 0,46 y 0,76 V, la señal DPPA 2 debe estar entre 0,23 y 0,38 V.
Cuando el pedal del acelerador está completamente presionado, la señal DPPA 1 debe estar entre 2,80 y 3,10 V, la señal DPPA 2 debe estar entre 1,40 y 1,55 V.
En cualquier posición del pedal del acelerador, la señal DPPA 1 debe ser el doble de la señal DPPA 2.
Sensor de temperatura del refrigerante (DTOZH)
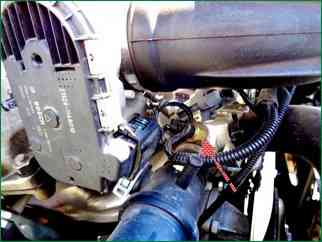
El sensor está instalado en el flujo de refrigerante del motor, en el tubo de salida de la camisa de agua del motor.
El elemento sensor del sensor de temperatura del refrigerante es un termistor, es decir, una resistencia cuya resistencia eléctrica cambia con la temperatura.
La alta temperatura provoca baja resistencia y la baja temperatura del refrigerante provoca alta resistencia.
El controlador emite 5 V al circuito del sensor de temperatura del refrigerante.
Sensor de golpe (DD)
instalado en el bloque de cilindros.
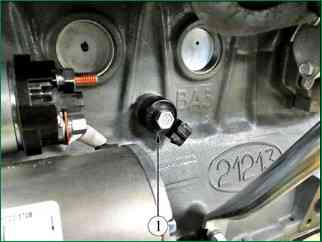
El elemento sensor piezocerámico DD genera una señal de voltaje CA, cuya amplitud y frecuencia corresponden a los parámetros de vibración del motor.
Cuando se produce la detonación, aumenta la amplitud de vibración de una determinada frecuencia. El controlador al mismo tiempo corrige el tiempo de encendido para amortiguar la detonación.
Sensor de oxígeno de control (UDC)
La reducción más eficaz de la toxicidad de los gases de escape de los motores de gasolina se consigue con una relación de masa de aire y combustible en la mezcla (14,5-14,6): 1.
Esta relación se llama estequiométrica.
Con esta relación aire-combustible, el convertidor catalítico reduce con mayor eficacia la cantidad de hidrocarburos, monóxido de carbono y óxidos de nitrógeno emitidos con los gases de escape.
Para optimizar la composición de los gases de escape con el fin de lograr la mayor eficiencia del catalizador, se utiliza un control de combustible de circuito cerrado con retroalimentación sobre la presencia de oxígeno en los gases de escape.
El controlador calcula la duración del pulso de inyección a partir de parámetros como el flujo de masa de aire, la velocidad del motor, la temperatura del refrigerante, etc.
Para corregir el cálculo de la duración del pulso de inyección, información sobre la presencia de oxígeno en los gases de escape, que es producida por el sensor de oxígeno
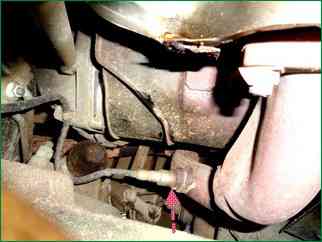
El UDC está instalado en la tubería del sistema de escape. Su elemento sensor está ubicado en la corriente de gases de escape.
El UDC genera un voltaje que varía en el rango de 50-900 mV.
Este voltaje de salida depende de la presencia o ausencia de oxígeno en los gases de escape y de la temperatura del elemento sensor UDC.
Cuando el UDC está en estado frío, la señal de salida del sensor está ausente, ya que en este estado su resistencia eléctrica interna es muy alta, varios MΩ.
A medida que el sensor se calienta, la resistencia cae y aparece la capacidad de generar una señal de salida.
Para un funcionamiento eficaz, el UDC debe tener una temperatura de al menos 300 °C.
Para un calentamiento rápido después de arrancar el motor, el UDC está equipado con un elemento calefactor eléctrico interno controlado por el controlador.
El ciclo de trabajo de las señales de pulso de control del calentador (la relación entre la duración del estado encendido y el período de repetición del pulso) depende de la temperatura UDC y del modo de funcionamiento del motor.
Si la temperatura del sensor es superior a 300 °C, en el momento de pasar por el punto de estequiometría, la señal de salida del sensor cambia entre nivel bajo (50-200 mV) y nivel alto (700-900 mV).
Un nivel de señal bajo corresponde a una mezcla pobre (presencia de oxígeno), una señal alta corresponde a una rica (sin oxígeno).
Descripción del funcionamiento de la cadena
El controlador emite un voltaje de referencia estable de 1,6 V al circuito UDC. Cuando el UDC no se calienta, el voltaje de la señal de salida del sensor está en el rango de 1,2-1,6 V.
A medida que el sensor se calienta, su resistencia interna disminuye y comienza a generar un voltaje fluctuante fuera de este rango.
Al cambiar el voltaje, el controlador determina que el UDC se ha calentado y su señal de salida se puede usar para controlar el suministro de combustible en modo de circuito cerrado.
Durante el funcionamiento normal del sistema de suministro de combustible en modo de circuito cerrado, el voltaje de salida del UDC cambia entre niveles bajo y alto.
Veneno sonda de oxigeno
El UDC puede envenenarse con el uso de gasolina con plomo o el uso de selladores de curado a temperatura ambiente que contienen altos niveles de silicona altamente volátil (compuestos de silicio) en el ensamblaje.
Los vapores de silicona pueden ingresar al sistema de ventilación del cárter y estar presentes durante el proceso de combustión. La presencia de compuestos de plomo o silicio en los gases de escape puede provocar la falla del UDC.
El mal funcionamiento de los circuitos UDC, un defecto del sensor, su envenenamiento o un estado sin calefacción pueden hacer que el voltaje de la señal permanezca en el rango de 1,2-1,6 V durante mucho tiempo.
Al mismo tiempo, el código de falla correspondiente se ingresará en la memoria del controlador. El suministro de combustible se controlará en un circuito abierto.
Si el controlador recibe una señal con un voltaje que indica una condición pobre prolongada, el código de falla correspondiente (nivel de señal bajo del sensor de oxígeno) se almacena en su memoria.
La causa del mal funcionamiento puede ser un cortocircuito a tierra en el circuito de salida del UDC, una fuga en el sistema de admisión de aire o una baja presión de combustible.
Si el controlador recibe una señal con un voltaje que indica una condición de mezcla rica a largo plazo, el código de falla correspondiente (nivel alto de la señal del sensor de oxígeno) se almacena en su memoria.
La causa del mal funcionamiento puede ser un cortocircuito del circuito de salida UDC a una fuente de voltaje o una mayor presión de combustible en el riel del inyector.
Cuando se producen códigos de problemas del sensor de oxígeno, el controlador controla el suministro de combustible en modo de bucle abierto.
Mantenimiento del sensor de oxígeno
Si el arnés, las almohadillas o los enchufes del sensor de oxígeno están dañados, se debe reemplazar el CC.
No se permite la reparación del arnés, enchufe o enchufes. Para un funcionamiento normal, el DC debe comunicarse con el aire atmosférico.
La comunicación con el aire atmosférico la proporcionan los espacios de aire de los cables del sensor.
Intentar reparar cables, almohadillas o enchufes puede provocar una violación de la comunicación con el aire atmosférico y un deterioro en el funcionamiento del CC.
Al realizar el mantenimiento del DC, se deben observar los siguientes requisitos:
No permita que el limpiador de contactos u otros materiales entren en contacto con el sensor o las almohadillas del arnés. Estos materiales pueden ingresar al DC y causar interrupciones.
Además, no se permite dañar el aislamiento de los cables, lo que lleva a su exposición.
Está prohibido doblar o torcer con fuerza el mazo de cables de CC y el mazo de cables del sistema de inyección conectado a él. Esto puede interrumpir el flujo de aire atmosférico hacia el centro de recreación.
Para evitar un mal funcionamiento debido a la entrada de agua, es necesario evitar que se dañe el sello en la periferia del bloque del arnés de control.
Sensor de diagnóstico de oxígeno (DOC)
Se utiliza un convertidor catalítico para reducir el contenido de hidrocarburos, monóxido de carbono y óxidos de nitrógeno en los gases de escape.
El neutralizador oxida los hidrocarburos y el monóxido de carbono, por lo que se convierten en vapor de agua y dióxido de carbono.
El neutralizador también recupera nitrógeno de los óxidos de nitrógeno.
El controlador supervisa las propiedades redox del convertidor mediante el análisis de la señal del sensor de oxígeno de diagnóstico instalado después del convertidor.
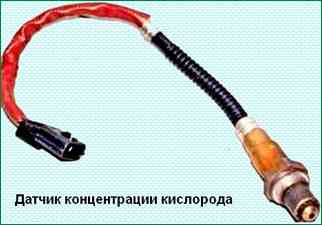
DDC funciona según el mismo principio que UDC.
El UDC genera una señal que indica la presencia de oxígeno en los gases de escape a la entrada del convertidor.
La señal generada por el DDC indica la presencia de oxígeno en los gases de escape después del convertidor.
Si el neutralizador funciona correctamente, las lecturas del DDC diferirán significativamente de las lecturas del UDC.
La señal de salida del sensor de oxígeno de diagnóstico calentado, cuando funciona en modo de retroalimentación, con un convertidor en funcionamiento en estado estable, debe estar en el rango de 590 a 750 mV y no debe repetir la señal UDC.
Si ocurre un mal funcionamiento en los circuitos o en el sensor de oxígeno de diagnóstico, el controlador almacena su código en su memoria y enciende la alarma, lo que indica un mal funcionamiento.
Los requisitos de mantenimiento y el procedimiento para reemplazar el DDK no difieren de los descritos anteriormente para el UDC.
El sensor de velocidad del vehículo genera una señal de pulso que informa al controlador sobre la velocidad del vehículo.
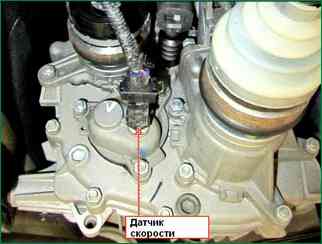
DSA configurado como entrada eje de la caja de transferencia m.
Cuando giran las ruedas motrices, el DSA genera 6 pulsos por metro de movimiento del vehículo. El controlador determina la velocidad del coche por la frecuencia de los pulsos.
En caso de mal funcionamiento de los circuitos DSA, el controlador almacena su código en su memoria y enciende el dispositivo de señalización.
Sensor de posición del cigüeñal
montado en la tapa del accionamiento del árbol de levas a una distancia de aproximadamente 1 ± 0,4 mm desde la parte superior del diente del disco de accionamiento montado en el cigüeñal del motor.
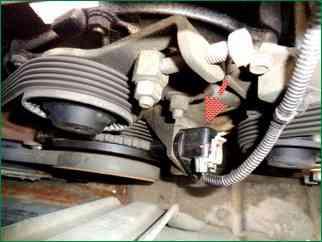
El disco impulsor está integrado con la polea impulsora del alternador y es una rueda dentada con 58 dientes en incrementos de 6° y una cavidad de sincronización "larga" formada por dos dientes faltantes.
Cuando la mitad del primer diente del sector del engranaje del disco después de la cavidad "larga" está alineado con el eje DPKV, el cigüeñal del motor está en la posición 114 ° (19 dientes) con respecto al punto muerto superior del 1er. y cuarto cilindros.
Cuando el disco maestro gira, el flujo magnético en el circuito magnético del sensor cambia, induciendo pulsos de voltaje de corriente alterna en su devanado.
El controlador determina la posición y frecuencia de rotación del cigüeñal por el número y frecuencia de estos pulsos y calcula la fase y duración de los pulsos para controlar los inyectores y la bobina de encendido.
Los cables DPKV están protegidos de interferencias por una pantalla cerrada a tierra.
Si ocurre una falla en el circuito del sensor de posición del cigüeñal, el motor deja de funcionar, el controlador almacena el código de falla en su memoria y enciende la alarma.
Sensor de fase
montado en la marea de la culata.
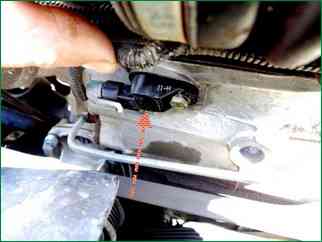
El principio de funcionamiento del sensor se basa en el efecto Hall.
Hay un pasador especial en el árbol de levas del motor. Cuando el pasador pasa contra el extremo del sensor, el sensor emite un pulso de voltaje de bajo nivel (alrededor de 0 V) al controlador, que corresponde a la posición del pistón del 1er cilindro en la carrera de compresión.
El controlador utiliza la señal del sensor de fase para organizar la inyección secuencial de combustible de acuerdo con el orden de funcionamiento de los cilindros del motor.
Si ocurre un mal funcionamiento en los circuitos o en el sensor de fase, el controlador almacena su código en su memoria y enciende el dispositivo de señalización.
Interruptor de luz de freno
incluido en el conjunto del pedal del freno y está diseñado para proporcionar las señales adecuadas al ECM cuando el conductor presiona/suelta el pedal del freno.
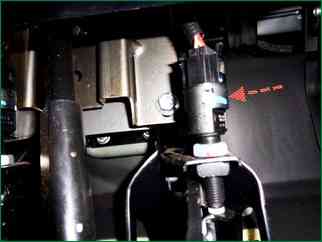
En los sistemas de control de aceleración por cable (E-gas), las señales del interruptor del pedal de freno juegan un papel importante porque son utilizadas por la función de seguridad del software ECM.
Por esta razón, es muy importante asegurarse de que el interruptor de la luz de freno esté siempre en buen estado de funcionamiento.
En caso de discrepancia entre su característica funcional de conmutación, por ejemplo, en caso de cambios espontáneos en los valores de los ajustes especificados en las instrucciones (por vibraciones del pedal de freno, desgaste del interruptor y bloqueo del pedal), el motor del automóvil puede cambiar a operación de emergencia con una potencia reducida forzosamente.
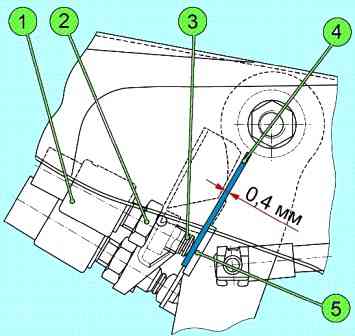
El valor del espacio de ajuste del interruptor debe estar dentro de 0,4 ± 0,1 mm (figura).
El interruptor de la luz de freno tiene dos juegos de contactos.
El primer grupo de contactos cambia el voltaje del terminal "15" del interruptor de encendido, el segundo, el voltaje del terminal "30" del interruptor de encendido, que se suministra a la luz de freno. Ambas señales se envían al ECM.
Cuando se suelta el pedal del freno, los contactos del primer grupo deben estar normalmente cerrados y los contactos del segundo grupo deben estar normalmente abiertos.
Si el interruptor de la luz de freno no funciona correctamente, el controlador almacena su código en su memoria y enciende el dispositivo de advertencia.
El código de falla también se ingresa cuando el º ajuste del espacio (0,4 ± 0,1 mm) entre la cabeza de la varilla móvil 3 y el cuerpo del interruptor 1
Interruptor de posición del embrague
Incluido en el conjunto del pedal del embrague y está diseñado para señalar al ECM que el pedal del embrague está presionado.
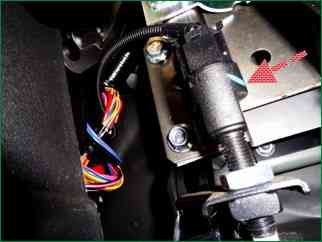
El interruptor tiene un grupo de contactos que conmutan el voltaje del terminal "15" del interruptor de encendido.
Cuando se pisa el pedal del embrague, los contactos están abiertos.
El software ECM utiliza la señal del interruptor de posición del pedal del embrague para mejorar el rendimiento de conducción del vehículo.
En caso de mal funcionamiento del SSPS, el controlador almacena su código en su memoria y enciende el dispositivo de señalización.
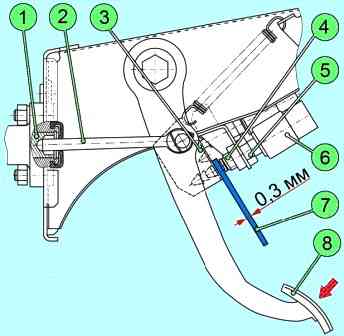
El valor del espacio de ajuste debe estar dentro de 0,3±0,1 mm (imagen).