ECM-Sensoren und Controller ME17.9.71 für die EURO-5-Toxizitätsnormen eines Chevrolet Niva-Autos
Das elektronische Motorsteuerungssystem (ECM) besteht aus einem Controller, Sensoren für Motor- und Fahrzeugbetriebsparameter sowie Aktoren
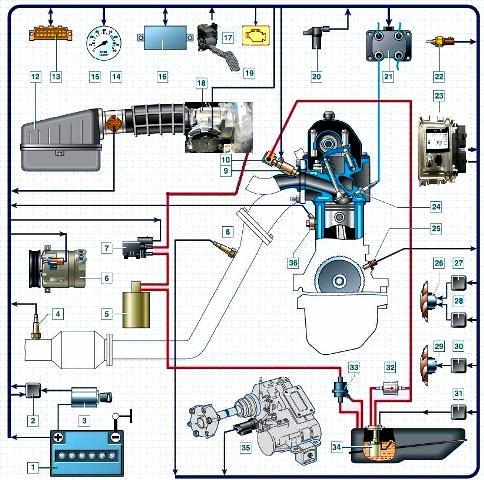
Schema des elektronischen Motorsteuerungssystems: 1 - Batterie; 2 - Hauptrelais; 3 - Zündschalter; 4 - diagnostischer Sauerstoffkonzentrationssensor; 5 - Adsorber; 6 - Klimakompressor; 7 - Adsorber-Spülventil; 8 - Sauerstoffkonzentrationssensor steuern; 9 - Düse; 10 - Kraftstoffverteiler; 12 - Luftfilter; 13 - Diagnosestecker; 14 - Luftmassenmesser; 15 - Drehzahlmesser; 16 - Wegfahrsperrenblock; 17 - elektronisches Gaspedal; 18 - Drosselklappenbaugruppe; 19 - Kontrollleuchte für eine Fehlfunktion des Motormanagementsystems; 20 - Phasensensor; 21 - Zündspule; 22 - Kühlmitteltemperatursensor; 23 - Controller; 24 - Zündkerze; 25 - Kurbelwellenpositionssensor; 26 - rechter Lüfter des Kühlsystems; 27 - zusätzliches Relais; 28 - Relais des rechten Lüfters des Kühlsystems; 29 - linker Lüfter des Kühlsystems; 30 - Relais des linken Lüfters des Kühlsystems; 31 - Kraftstoffpumpenrelais; 32 - Kraftstofffilter; 33 - Schwerkraftventil; 34 - Kraftstoffmodul; 35 - Geschwindigkeitssensor; 36 - Klopfsensor
Controller
Der Controller ist ein Mini-Computer für spezielle Zwecke. Er besteht aus einem Arbeitsspeicher (RAM), einem programmierbaren Nur-Lese-Speicher (PROM) und einem elektrisch umprogrammierbaren Speicher (EPROM).
RAM wird vom Mikroprozessor verwendet, um aktuelle Informationen über den Betrieb des Motors (gemessene Parameter) und berechnete Daten vorübergehend zu speichern.
Außerdem werden Fehlercodes im RAM aufgezeichnet.
Dieser Speicher ist flüchtig, d. h. wenn die Stromversorgung unterbrochen wird (Abklemmen der Batterie oder Trennen des Kabelbaumblocks vom Steuergerät), wird sein Inhalt gelöscht.
EPROM speichert das Motorsteuerprogramm, das eine Folge von Betriebsbefehlen (Algorithmen) und Kalibrierungsdaten (Einstellungen) enthält.
PROM bestimmt die wichtigsten Parameter des Motorbetriebs: die Art der Drehmoment- und Leistungsänderung, den Kraftstoffverbrauch, den Zündzeitpunkt, die Zusammensetzung der Abgase usw. PROM ist nichtflüchtig, d. h. der Inhalt seines Speichers ist nicht flüchtig ändern, wenn das Gerät ausgeschaltet wird.
ERPROM speichert Controller-, Motor- und Fahrzeug-IDs. Zeichnet Betriebsparameter sowie Verstöße gegen den Motor- und Fahrzeugbetrieb auf. Es handelt sich um einen nichtflüchtigen Speicher.
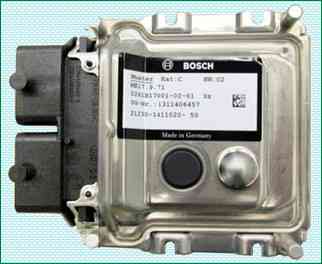
Der Controller ist die zentrale Einheit des Motormanagementsystems.
Es empfängt Informationen von Sensoren und steuert die Aktoren, um einen optimalen Motorbetrieb bei einem bestimmten Fahrzeugleistungsniveau sicherzustellen.
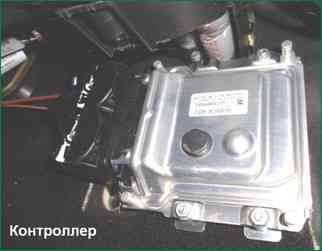
Der Controller befindet sich im Bereich der Füße des Beifahrers und ist an der Spritzwand befestigt.
Der Controller steuert Aktoren wie Kraftstoffeinspritzdüsen, Motordrossel, Zündspule, Lambdasondenheizung, Kanisterspülventil und verschiedene Relais.
Der Controller steuert das Ein- und Ausschalten des Hauptrelais (Zündrelais), über das die Versorgungsspannung von der Batterie an die Elemente des Systems geliefert wird (mit Ausnahme der elektrischen Kraftstoffpumpe, des elektrischen Lüfters, der Steuereinheit und des APS). Statusanzeige).
Der Controller schaltet das Hauptrelais ein, wenn die Zündung eingeschaltet wird.
Wenn die Zündung ausgeschaltet wird, verzögert die Steuerung das Ausschalten des Hauptrelais um die Zeit, die zur Vorbereitung auf das nächste Einschalten erforderlich ist (Abschluss der Berechnungen, Einstellen des Gashebels auf die Position vor dem Starten des Motors).
Beim Einschalten der Zündung tauscht das Steuergerät zusätzlich zu den oben genannten Funktionen auch Informationen mit dem APS aus (sofern die Wegfahrsperre aktiviert ist).
Wenn die Börse feststellt, dass der Zugang zum Fahrzeug erlaubt ist, führt die Steuerung weiterhin Motorsteuerungsfunktionen aus. Andernfalls wird der Motor blockiert.
Der Controller führt auch eine Systemdiagnosefunktion aus.
Es definiert on Das Vorhandensein von Fehlfunktionen der Systemelemente schaltet das Signalgerät ein und speichert Codes in seinem Speicher, die die Art der Fehlfunktion anzeigen und dem Mechaniker bei der Durchführung von Reparaturen helfen.
Luftmassenmesser
Das Motorsteuerungssystem verwendet einen Heißdraht-MAF mit einem Frequenzgang eines digitalen Ausgangssignals.
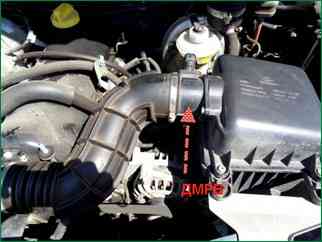
Es befindet sich zwischen dem Luftfilter und dem Ansaugrohrschlauch.
Das MAF-Signal ist ein Frequenzsignal (Hz), dessen Impulswiederholungsrate von der Luftmenge abhängt, die durch den Sensor strömt (steigt mit zunehmendem Luftstrom).
Der Diagnose-Tester misst den Luftstrom in Kilogramm pro Stunde.
Wenn im DTV-Schaltkreis eine Fehlfunktion auftritt, speichert der Controller seinen Code in seinem Speicher und schaltet das Signalgerät ein.
In diesem Fall ersetzt der Controller die Sensorwerte durch einen festen Lufttemperaturwert (20 °C).
Drosselklappensensoren (TPS)
In einem EAF-System werden zwei TPS verwendet.
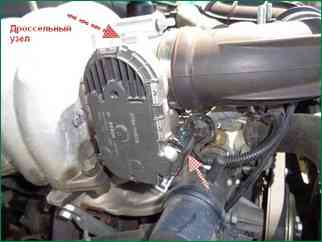
TPS sind Teil des elektrischen Gashebels.
TPDZ ist ein potentiometrischer Widerstand, dessen einer Ausgang vom Controller mit einer Referenzspannung (5 V) versorgt wird und dessen zweiter Ausgang über den Controller geerdet ist.
Vom Ausgang, der mit dem beweglichen Kontakt des Potentiometers verbunden ist, wird das Ausgangssignal des TPS dem Controller zugeführt.
Der Controller steuert die Drosselklappenstellung elektrisch entsprechend der Stellung des Gaspedals.
Anhand der Messwerte des TPS überwacht der Controller die Position der Drosselklappe.
Beim Einschalten der Zündung stellt die Steuerung die Klappe in die Vorstartposition, deren Öffnungsgrad von der Temperatur des Kühlmittels abhängt.
In der Drosselklappenstellung vor dem Start sollte das Ausgangssignal von TPS 1 zwischen 0,65 und 0,79 Volt liegen, das Ausgangssignal von TPS 2 sollte zwischen 4,21 und 4,35 V liegen.
Wenn Sie den Motor nicht starten und das Gaspedal nicht innerhalb von 15 Sekunden betätigen, schaltet die Steuerung den elektrischen Antrieb der Drosselleitung ab und die Drosselklappe wird auf die Position von 7–8 % Drosselklappenöffnung eingestellt.
Im stromlosen Zustand (LIMP HOME) des elektrischen Drosselklappenstellers liegt das Ausgangssignal von TPS 1 im Bereich von 0,80–0,85 Volt, der Ausgang von TPS 2 liegt im Bereich von 4,15–4,20 V.
Wenn innerhalb von 15 Sekunden keine Aktion erfolgt, kommt als nächstes der Modus zum Überprüfen („Lernen“) der 0-Position der Drosselklappe – vollständiges Schließen und Öffnen der Drosselklappe in die Vorstartposition und dann Der Drosselklappensteller wechselt wieder in den stromlosen Modus.
Bei jeder Drosselklappenstellung muss die Summe der TPS 1- und TPS 2-Signale gleich (5 ± 0,1) V sein.
Wenn in den TPS-Schaltkreisen eine Fehlfunktion auftritt, schaltet der Controller den Drosselklappensteller ab, speichert seinen Code in seinem Speicher und schaltet das Signalgerät ein.
In diesem Fall wird die Drosselklappe auf die Position von 7–8 % Drosselklappenöffnung eingestellt.
Elektronisches Gaspedal (EPA)
Fahrzeuge mit einer elektronischen Drosselklappenbaugruppe verwenden ein elektronisches Gaspedal, das das Signal der Gaspedalposition elektrisch an die Steuerung überträgt.
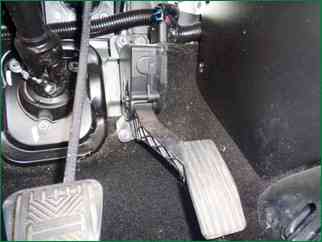
Das elektronische Gaspedal befindet sich an einer Halterung unter dem rechten Fuß des Fahrers.
Das elektronische Gaspedal nutzt zwei Gaspedalpositionssensoren (APPS).
DPPAs sind potentiometrische Widerstände, die von einem 5-V-Controller gespeist werden.
Der DPPA ist über den Pedalhebel mechanisch mit dem Antrieb verbunden.
Zwei unabhängige Federn zwischen dem Pedalarm und dem Körper sorgen für eine Rückstellkraft.
Der Controller empfängt ein analoges elektrisches Signal von der ESA und erzeugt ein Signal zur Steuerung der Drosselklappenstellung.
Die Ausgangsspannung des DPPA ändert sich proportional zum Drücken des Gaspedals.
Wenn das Gaspedal losgelassen wird, sollte das DPPA 1-Signal zwischen 0,46 und 0,76 V liegen, das DPPA 2-Signal sollte zwischen 0,23 und 0,38 V liegen.
Wenn das Gaspedal vollständig durchgetreten ist, sollte das DPPA 1-Signal zwischen 2,80 und 3,10 V liegen, das DPPA 2-Signal sollte zwischen 1,40 und 1,55 V liegen.
In jeder Stellung des Fahrpedals muss das DPPA 1-Signal doppelt so groß sein wie das DPPA 2-Signal.
Kühlmitteltemperatursensor (DTOZH)
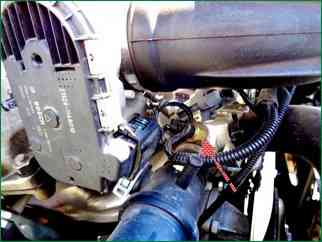
Der Sensor ist im Motorkühlmittelstrom am Auslassrohr des Motorwassermantels installiert.
Das Messelement des Kühlmitteltemperatursensors ist ein Thermistor, also ein Widerstand, dessen elektrischer Widerstand sich mit der Temperatur ändert.
Hohe Temperaturen führen zu niedrigem Widerstand und niedrige Kühlmitteltemperatur zu hohem Widerstand.
Der Controller gibt 5 V an den Kühlmitteltemperatursensorkreis aus.
Klopfsensor (DD)
am Zylinderblock montiert.
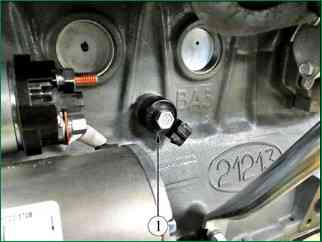
Das piezokeramische Sensorelement DD erzeugt ein Wechselspannungssignal, dessen Amplitude und Frequenz den Vibrationsparametern des Motors entsprechen.
Bei einer Detonation erhöht sich die Schwingungsamplitude einer bestimmten Frequenz. Gleichzeitig korrigiert die Steuerung den Zündzeitpunkt, um die Klopfgeräusche zu dämpfen.
Sauerstoffsensor (UDC) steuern
Die wirksamste Reduzierung der Toxizität der Abgase von Ottomotoren wird mit einem Massenverhältnis von Luft und Kraftstoff im Gemisch (14,5-14,6) von 1 erreicht.
Dieses Verhältnis wird als stöchiometrisch bezeichnet.
Bei diesem Luft-Kraftstoff-Verhältnis reduziert der Katalysator die Menge an Kohlenwasserstoffen, Kohlenmonoxid und Stickoxiden, die mit den Abgasen ausgestoßen werden, am effektivsten.
Um die Zusammensetzung der Abgase zu optimieren und den größtmöglichen Wirkungsgrad des Katalysators zu erreichen, wird eine Kraftstoffregelung mit geschlossenem Regelkreis und Rückmeldung über das Vorhandensein von Sauerstoff in den Abgasen eingesetzt.
Die Steuerung berechnet die Dauer des Einspritzimpulses aus Parametern wie Luftmassenstrom, Motordrehzahl, Kühlmitteltemperatur usw.
Um die Berechnung der Einspritzimpulsdauer zu korrigieren, werden Informationen über das Vorhandensein von Sauerstoff in den Abgasen benötigt, die vom Sauerstoffsensor erzeugt werden
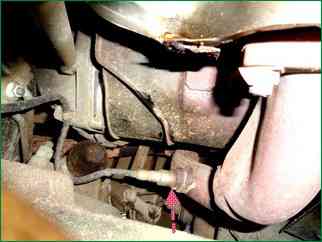
Der UDC wird am Rohr der Abgasanlage montiert. Sein Sensorelement befindet sich im Abgasstrom.
Der UDC erzeugt eine Spannung, die im Bereich von 50–900 mV variiert.
Diese Ausgangsspannung hängt vom Vorhandensein oder Fehlen von Sauerstoff in den Abgasen und von der Temperatur des UDC-Sensorelements ab.
Wenn sich der UDC im kalten Zustand befindet, fehlt das Ausgangssignal des Sensors, da in diesem Zustand sein elektrischer Innenwiderstand sehr hoch ist – mehrere MΩ.
Wenn sich der Sensor erwärmt, sinkt der Widerstand und es entsteht die Fähigkeit, ein Ausgangssignal zu erzeugen.
Für einen effektiven Betrieb muss der UDC eine Temperatur von mindestens 300 °C haben.
Zum schnellen Aufwärmen nach dem Starten des Motors ist der UDC mit einem internen elektrischen Heizelement ausgestattet, das von der Steuerung gesteuert wird.
Der Arbeitszyklus der Heizungssteuerimpulssignale (das Verhältnis der Dauer des Ein-Zustands zur Impulswiederholungsperiode) hängt von der UDC-Temperatur und dem Motorbetriebsmodus ab.
Wenn die Sensortemperatur über 300 °C liegt, wechselt das Sensorausgangssignal im Moment des Durchschreitens des Stöchiometriepunkts zwischen niedrigem Pegel (50–200 mV) und hohem Pegel (700–900 mV).
Ein niedriger Signalpegel entspricht einem mageren Gemisch (Anwesenheit von Sauerstoff), ein hoher Signalpegel entspricht einem fetten Gemisch (kein Sauerstoff).
Beschreibung der Kettenoperation
Der Controller gibt eine stabile Referenzspannung von 1,6 V an den UDC-Schaltkreis aus. Wenn der UDC nicht aufgewärmt ist, liegt die Sensorausgangssignalspannung im Bereich von 1,2 -1,6 V.
Wenn sich der Sensor erwärmt, verringert sich sein Innenwiderstand und er beginnt, außerhalb dieses Bereichs eine schwankende Spannung zu erzeugen.
Durch Änderung der Spannung stellt der Controller fest, dass der UDC aufgewärmt ist, und sein Ausgangssignal kann zur Steuerung der Kraftstoffzufuhr im geschlossenen Regelkreis verwendet werden.
Während des normalen Betriebs des Kraftstoffversorgungssystems im geschlossenen Regelkreis wechselt die Ausgangsspannung des UDC zwischen niedrigem und hohem Pegel.
Gift Sauerstoffsensor
UDC kann durch die Verwendung von bleihaltigem Benzin oder die Verwendung von bei Raumtemperatur aushärtenden Dichtstoffen, die einen hohen Anteil an leicht flüchtigem Silikon (Siliziumverbindungen) enthalten, bei der Montage vergiftet werden.
Silikondämpfe können in das Kurbelgehäuseentlüftungssystem gelangen und während des Verbrennungsprozesses vorhanden sein. Das Vorhandensein von Blei- oder Siliziumverbindungen in den Abgasen kann zum Ausfall des UDC führen.
Fehlfunktionen der UDC-Schaltkreise, ein Sensordefekt, dessen Vergiftung oder ein unbeheizter Zustand können dazu führen, dass die Signalspannung für längere Zeit im Bereich von 1,2–1,6 V bleibt.
Gleichzeitig wird der entsprechende Fehlercode in den Speicher der Steuerung eingetragen. Die Kraftstoffzufuhr wird in einem offenen Regelkreis gesteuert.
Wenn der Controller ein Signal mit einer Spannung empfängt, die auf einen längeren Magerzustand hinweist, wird der entsprechende Fehlercode (niedriger Signalpegel des Sauerstoffsensors) in seinem Speicher gespeichert.
Die Ursache der Fehlfunktion kann ein Kurzschluss im UDC-Ausgangskreis zur Masse, ein Leck im Luftansaugsystem oder ein niedriger Kraftstoffdruck sein.
Wenn der Controller ein Signal mit einer Spannung empfängt, die auf einen langfristig fetten Gemischzustand hinweist, wird der entsprechende Fehlercode (hoher Pegel des Sauerstoffsensorsignals) in seinem Speicher gespeichert.
Die Ursache der Fehlfunktion kann ein Kurzschluss des UDC-Ausgangskreises mit einer Spannungsquelle oder ein erhöhter Kraftstoffdruck in der Einspritzschiene sein.
Wenn Fehlercodes für den Sauerstoffsensor auftreten, steuert die Steuerung die Kraftstoffzufuhr im offenen Regelkreis.
Wartung des Sauerstoffsensors
Wenn der Kabelbaum, die Pads oder Stecker des Sauerstoffsensors beschädigt sind, muss der Gleichstrom ausgetauscht werden.
Eine Reparatur des Kabelbaums, der Steckdose oder der Stecker ist nicht gestattet. Für den Normalbetrieb muss der DC mit der atmosphärischen Luft kommunizieren.
Die Kommunikation mit der atmosphärischen Luft erfolgt über die Luftspalte der Sensorkabel.
Der Versuch, Kabel, Pads oder Stecker zu reparieren, kann zu einer Unterbrechung der Kommunikation mit der atmosphärischen Luft und einer Verschlechterung des DC-Betriebs führen.
Bei der Wartung des DC müssen folgende Anforderungen beachtet werden:
Lassen Sie keinen Kontaktreiniger oder andere Materialien mit dem Sensor oder den Kabelbaumpolstern in Kontakt kommen. Diese Materialien können in den DC gelangen und Störungen verursachen.
Darüber hinaus ist eine Beschädigung der Isolierung der Drähte, die zu deren Freilegung führt, nicht zulässig.
Es ist verboten, den DC-Kabelbaum und den daran angeschlossenen Kabelbaum des Einspritzsystems stark zu biegen oder zu verdrehen. Dies kann den Luftstrom in das Freizeitzentrum stören.
Um eine Fehlfunktion aufgrund von Wassereintritt zu vermeiden, muss eine Beschädigung der Dichtung am Umfang des Steuerkabelbaumblocks verhindert werden.
Diagnostischer Sauerstoffsensor (DOC)
Um den Gehalt an Kohlenwasserstoffen, Kohlenmonoxid und Stickoxiden in den Abgasen zu reduzieren, wird ein Katalysator eingesetzt.
Der Neutralisator oxidiert Kohlenwasserstoffe und Kohlenmonoxid, wodurch sie in Wasserdampf und Kohlendioxid umgewandelt werden.
Der Neutralisator gewinnt auch Stickstoff aus Stickoxiden zurück.
Der Controller überwacht die Redoxeigenschaften des Konverters, indem er das Signal des nach dem Konverter installierten diagnostischen Sauerstoffsensors analysiert.
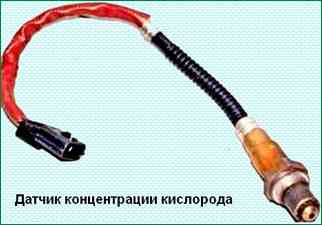
DDC funktioniert nach dem gleichen Prinzip wie UDC.
Der UDC erzeugt ein Signal, das das Vorhandensein von Sauerstoff in den Abgasen am Einlass des Konverters anzeigt.
Das vom DDC erzeugte Signal zeigt das Vorhandensein von Sauerstoff in den Abgasen nach dem Konverter an.
Wenn der Neutralisator ordnungsgemäß funktioniert, weichen die Messwerte des DDC deutlich von den Messwerten des UDC ab.
Das Ausgangssignal des beheizten diagnostischen Sauerstoffsensors sollte im Feedback-Modus mit einem funktionierenden Konverter im eingeschwungenen Zustand im Bereich von 590 bis 750 mV liegen und das UDC-Signal nicht wiederholen.
Wenn eine Fehlfunktion in den Schaltkreisen oder im diagnostischen Sauerstoffsensor selbst auftritt, speichert der Controller seinen Code in seinem Speicher und schaltet den Alarm ein, um eine Fehlfunktion zu signalisieren.
Die Wartungsanforderungen und das Verfahren zum Ersetzen des DDK unterscheiden sich nicht von denen, die oben für das UDC beschrieben wurden.
Der Fahrzeuggeschwindigkeitssensor erzeugt ein Impulssignal, das den Controller über die Geschwindigkeit des Fahrzeugs informiert.
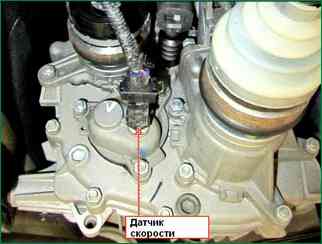
DSA auf Eingang eingestellt m Verteilergetriebewelle.
Wenn sich die Antriebsräder drehen, erzeugt das DSA 6 Impulse pro Meter Fahrzeugbewegung. Der Controller bestimmt die Geschwindigkeit des Autos anhand der Frequenz der Impulse.
Im Falle einer Fehlfunktion der DSA-Schaltkreise speichert der Controller seinen Code in seinem Speicher und schaltet das Signalgerät ein.
Kurbelwellenpositionssensor
Montiert auf der Abdeckung des Nockenwellenantriebs in einem Abstand von etwa 1 ± 0,4 mm von der Oberseite des Zahns der auf der Kurbelwelle des Motors montierten Antriebsscheibe.
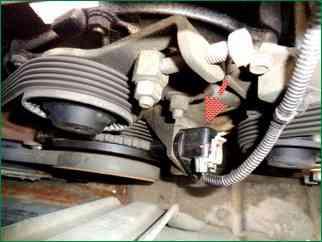
Die Antriebsscheibe ist in die Antriebsriemenscheibe des Generators integriert und besteht aus einem Zahnrad mit 58 Zähnen in 6°-Schritten und einem „langen“ Steuerhohlraum, der aus zwei fehlenden Zähnen besteht.
Wenn die Mitte des ersten Zahns des Zahnradsektors der Scheibe nach dem „langen“ Hohlraum mit der DPKV-Achse ausgerichtet ist, befindet sich die Motorkurbelwelle in einer Position von 114 ° (19 Zähne) zum oberen Totpunkt des 1 und 4. Zylinder.
Wenn sich die Masterscheibe dreht, ändert sich der magnetische Fluss im Magnetkreis des Sensors und induziert Wechselspannungsimpulse in seiner Wicklung.
Der Controller bestimmt anhand der Anzahl und Frequenz dieser Impulse die Position und Drehfrequenz der Kurbelwelle und berechnet die Phase und Dauer der Impulse zur Steuerung der Einspritzdüsen und der Zündspule.
Die DPKV-Drähte sind durch eine zur Erde geschlossene Abschirmung vor Störungen geschützt.
Wenn im Schaltkreis des Kurbelwellen-Positionssensors eine Fehlfunktion auftritt, funktioniert der Motor nicht mehr, die Steuerung speichert den Fehlfunktionscode und schaltet den Alarm ein.
Phasensensor
auf der Flut des Zylinderkopfes montiert.
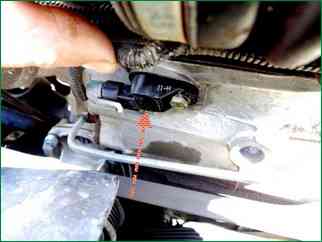
Das Funktionsprinzip des Sensors basiert auf dem Hall-Effekt.
Auf der Motornockenwelle befindet sich ein spezieller Stift. Wenn der Stift das Ende des Sensors berührt, gibt der Sensor einen Spannungsimpuls mit niedrigem Pegel (ca. 0 V) an die Steuerung aus, der der Position des Kolbens des 1. Zylinders im Kompressionshub entspricht.
Das Phasensensorsignal wird von der Steuerung verwendet, um die sequentielle Kraftstoffeinspritzung entsprechend der Betriebsreihenfolge der Motorzylinder zu organisieren.
Wenn eine Fehlfunktion in den Schaltkreisen oder im Phasensensor selbst auftritt, speichert der Controller seinen Code in seinem Speicher und schaltet das Signalgerät ein.
Bremslichtschalter
ist in der Bremspedalbaugruppe enthalten und soll die entsprechenden Signale an das ECM senden, wenn der Fahrer das Bremspedal drückt/loslässt.
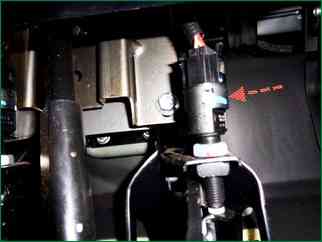
In Throttle-by-Wire (E-Gas)-Steuerungssystemen spielen die Bremspedalschaltersignale eine wichtige Rolle, da sie von der Sicherheitsfunktion der ECM-Software verwendet werden.
Aus diesem Grund ist es sehr wichtig sicherzustellen, dass der Bremslichtschalter immer funktionsfähig ist.
Im Falle einer Diskrepanz zwischen seiner Funktionscharakteristik des Schaltens, zum Beispiel bei spontanen Änderungen der Werte der in der Anleitung angegebenen Einstellungen (aufgrund von Vibrationen des Bremspedals, Verschleiß des
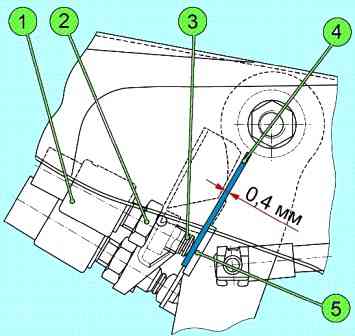
Der Wert des Einstellspalts des Schalters sollte innerhalb von 0,4 ± 0,1 mm liegen (Abbildung).
Der Bremslichtschalter verfügt über zwei Kontaktsätze.
Die erste Kontaktgruppe schaltet die Spannung von der Klemme „15“ des Zündschalters, die zweite die Spannung von der Klemme „30“ des Zündschalters, die der Bremsleuchte zugeführt wird. Beide Signale werden an das ECM gesendet.
Wenn das Bremspedal losgelassen wird, müssen die Kontakte der ersten Gruppe normalerweise geschlossen sein und die Kontakte der zweiten Gruppe müssen normalerweise geöffnet sein.
Bei einer Fehlfunktion des Bremslichtschalters speichert der Controller seinen Code im Speicher und schaltet die Warnvorrichtung ein.
Der Fehlercode wird auch eingegeben, wenn der Einstellung des Spalts (0,4 ± 0,1 mm) zwischen dem Kopf der beweglichen Stange 3 und dem Schalterkörper 1
Kupplungspositionsschalter
In der Kupplungspedalbaugruppe enthalten und soll dem ECM signalisieren, dass das Kupplungspedal gedrückt ist.
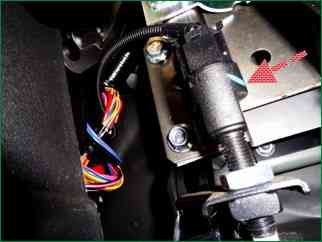
Der Schalter verfügt über eine Gruppe von Kontakten, die die Spannung von Klemme „15“ des Zündschalters schalten.
Bei gedrücktem Kupplungspedal sind die Kontakte geöffnet.
Das Signal des Kupplungspedalpositionsschalters wird von der ECM-Software verwendet, um die Fahrleistung des Fahrzeugs zu verbessern.
Im Falle einer Fehlfunktion des SSPS speichert der Controller seinen Code in seinem Speicher und schaltet das Signalgerät ein.
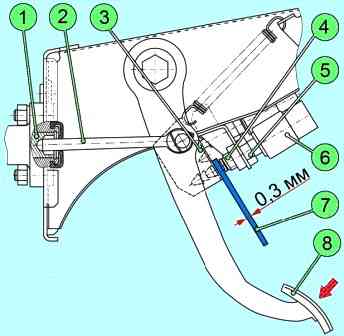
Der Wert des Einstellspalts sollte innerhalb von 0,3 ± 0,1 mm liegen (Bild).