After repairing the crankshaft, as well as the flywheel, clutch or pulley installed on it, it is necessary to balance them
Dynamic balancing of parts mounted on the crankshaft (flywheel, pulley, crankshaft, pressure and driven clutch discs) must be carried out on machines mod. MS-970 or PBM-4.
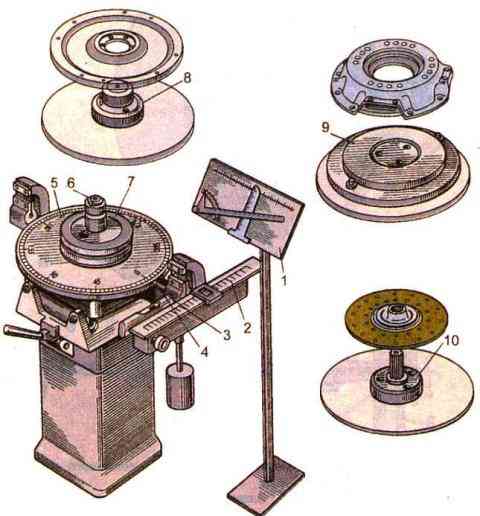
Machine model 40U-314 for static balancing of the flywheel, pulley, pressure and driven clutch discs: 1 - a device for determining the place of imbalance; 2 - measuring ruler to determine the imbalance; 3 - level; 4 - arrow for determining the angle of rotation of the limb; 5 - limbus; 6 - mandrel for static balancing of the crankshaft pulley; 7 - balanced pulley; 8,9 and 10 - mandrels for static balancing, respectively, of the flywheel, pressure and driven discs
A less precise static balancing of these parts is carried out on machines mod. 40U-314 (Fig. 1).
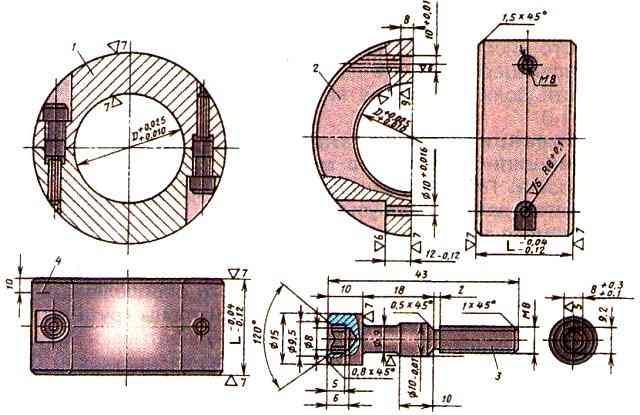
Balancing weight mounted on the connecting rod journals of the crankshaft: 1 - detachable weight assembly: 2 - weight half ring; 3 - half-ring fastening bolt; 4 - risk (mark) 0.3x10 mm in size, applied on the outer surface of both half rings
Balancing the crankshaft, as well as the crankshaft with the flywheel and clutch mounted on it, should be carried out in dynamic mode with weights on the connecting rod journals replacing the connecting rod and piston group on the connecting rod journal.
The balancing weight (Fig. 2) consists of two identical half-rings connected by two bolts made of steel 40x (GOST 4543-71), with a hardness of 35-40 HRC.
The outer, inner surfaces of certain diameters and the ends of the load are finally processed after connecting the half-rings with bolts.
The internal diameter of the weight is D+0.025 mm, where 13 is the diameter of the crankpin.
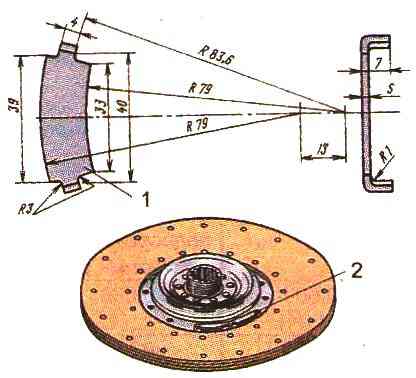
Balancing weight mounted on the clutch driven disk: 1 - weight; 2 - the location of the balancing weights on the disk; S - size in thickness, selected during balancing
The displacement of the axes of the bolts relative to the ends and the internal diameter of the load should be no more than 0.05 mm.
The bolts must be of the same mass.
The load is adjusted by weight with a decrease in the outer diameter with an accuracy of +1 g and statically balanced on the mandrel with an accuracy of 2 g/cm so that the center of gravity of the load is on the axis of the load and in the middle of its width.
After that, risks are applied to the outer surface to ensure the assembly of the half-rings in one position.
The clutch disc assembly is balanced relative to the side surfaces of the hub slots when one or three weights are installed (Fig. 3), which are attached to the disc with antennae.
After bending them, the immobility of the connection is ensured.
Residual imbalance - no more than 25 gcm.
Balancing weights are made of sheet steel 08 with a thickness of 2.0 mm and a weight of 12 g; 1.2 mm thick and 7.5 g.
Clutch pressure plate with casing assembly is balanced relative to the working surface of the pressure plate and two diametrically located holes for fastening the casing to the flywheel by drilling holes with a diameter of 13.8 mm in the bosses under the springs to a depth of not more than 23 mm .
The distance between the supporting surfaces of the disk and the casing should be 9.8 4-0.1 mm with a non-parallelism tolerance of these surfaces of 0.03 mm.
Residual imbalance should not exceed 50 gsm.
After balancing, the mounting holes are marked.
With any re-installation on the same holes, the imbalance should be no more than 90 gcm.
The crankshaft with flywheel and clutch assembly is balanced relative to the extreme main journals when drilling holes with a diameter of 15 mm (to a depth of not more than 15 mm, with a distance between them of at least 5 mm) at a distance of 184 mm from the axis of the shaft in uncovered clutch casing segments of the flywheel running surface or when drilling holes in the bosses under the clutch pressure plate springs.
Residual unbalance on the clutch (flywheel) side should be no more than 70 gsm.
Before balancing, a load is put on each crankpin, and the clutch disc is centered relative to the inner diameter of the bearing on the crankshaft flange using the input shaft of the gearbox or a special mandrel.