The power system includes elements of the following systems:
- - fuel supply system, including fuel tank 4 (Fig. 1), electric fuel pump 2, pipelines 5, 6 and 13, hoses 12, fuel rail 8 with injectors 7 and fuel pressure regulator 9, as well as fuel filter 11;
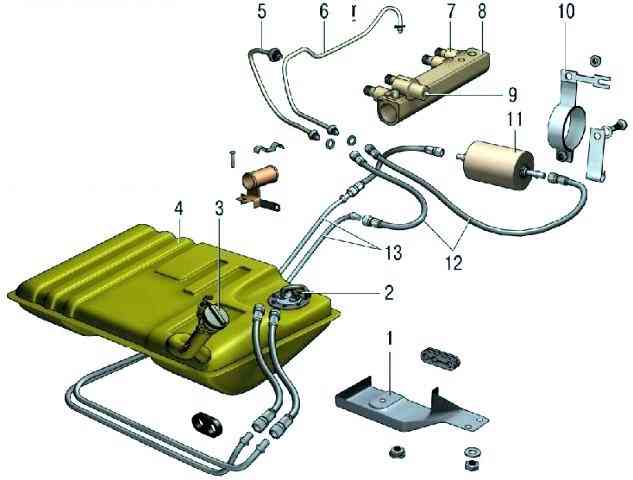
- - air supply system, including air filter 1 (Fig. 2), air supply pipe 2, throttle assembly 3;
- - fuel vapor recovery system, including adsorber 4 and connecting pipelines.
A fundamental feature of the VAZ-2123 engine power system is the absence of a carburetor in it, which combines the functions of mixture formation and dosing of the air-fuel mixture into the engine cylinders.
In the port injection system installed on this engine, these functions are separated
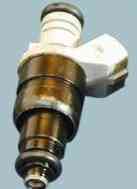
- nozzles carry out metered injection of fuel into the intake pipe, and the supply of air necessary at each moment of engine operation is carried out by a system consisting of a throttle assembly and an idle speed controller.
The fuel injection system and the ignition system are controlled by an electronic engine control unit, which continuously monitors the engine load, the vehicle speed, the thermal state of the engine, and the optimal combustion process in the engine cylinders using appropriate sensors.
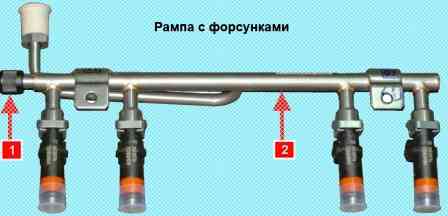
This control method makes it possible to ensure the optimal composition of the combustible mixture at each particular moment of engine operation, which allows you to get maximum power with the lowest possible fuel consumption and low exhaust gas toxicity.
The power supply system is an integral part of the engine management system.
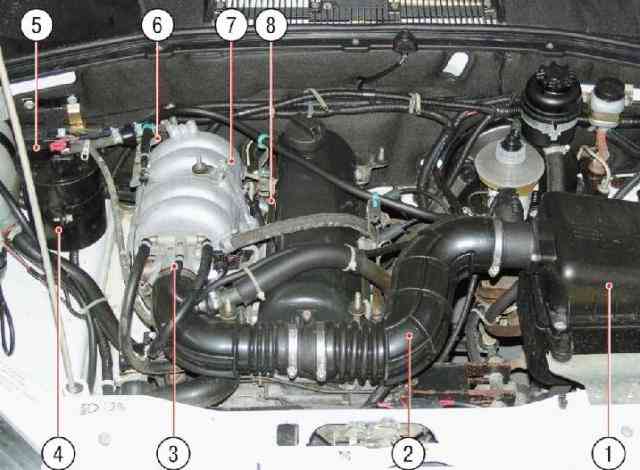
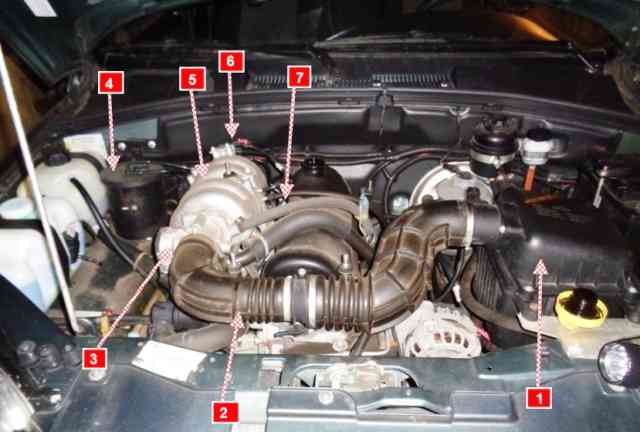
Fuel tank 4 - (see Fig. 1) welded, stamped, fixed in the luggage compartment with bolts and nuts.
At the top of the fuel tank, an electric fuel pump is installed, combined with a fuel level sensor.
From the pump, fuel is supplied to the fuel filter installed in the engine compartment (installed on the bottom on later models), and from there it enters the engine fuel rail mounted on the engine intake pipe.
From the fuel rail, fuel is injected by injectors into the intake pipe.
Excess fuel is drained into the fuel tank through a fuel pressure regulator mounted at the rear end of the fuel rail.
Fuel pump 2 is an electrically driven, two-stage, rotary type, installed in the fuel tank, which reduces the possibility of vapor lock, since the fuel is supplied under pressure, and not under vacuum. It provides fuel supply at a pressure of more than 284 kPa.
Fuel filter 11 is built into the supply line l between the electric fuel pump and the fuel rail and is installed in the engine compartment on the front panel of the body.
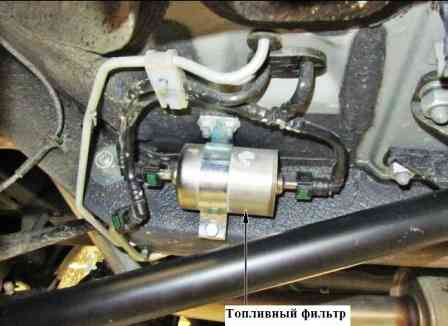
Since 2009, the fuel filter has been installed on the bottom of the car closer to the right rear arch and covered with a plastic cover.
The filter is non-separable, has a steel body with a paper filter element.
The 8-injector rail is a hollow bar with injectors and a fuel pressure regulator installed on it.
The injector rail is fixed to the intake pipe. At the rear end of the rail there is a fuel pressure control valve closed with a screw plug.
Injectors 7 - are attached to the ramp, from which fuel is supplied to them, and with their nozzles they enter the holes of the intake pipe.
In the openings of the ramp and the inlet pipe, the nozzles are sealed with rubber o-rings.
The nozzle is an electromechanical valve in which the check valve needle is pressed against the seat by a spring.
When an electrical impulse is applied from the control unit to the electromagnet winding, the needle rises and opens the atomizer hole through which fuel is supplied to the engine intake pipe. The amount of fuel injected by the injector depends on the duration of the electrical impulse.
Fuel pressure regulator 9 - mounted on the fuel rail and designed to maintain a constant pressure difference between the air pressure in the intake pipe and the fuel pressure in the rail.
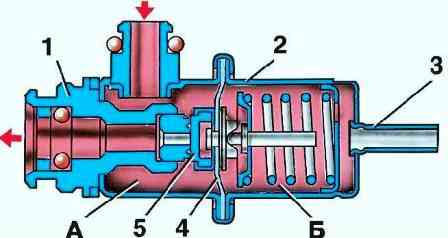
The regulator consists of a valve 5 (fig. 3) with a diaphragm 4, pressed by a spring to the seat in the regulator body.
With the engine running, the regulator maintains the pressure in the injector rail within 284–325 kPa.
Fuel pressure acts on the regulator diaphragm on one side, and pressure (vacuum) in the intake pipe on the other.
When the pressure in the intake pipe decreases (throttle valve closes), the regulator valve opens at a lower fuel pressure, bypassing excess fuel through the drain line back to the tank.
Fuel rail pressure drops.
When the pressure in the intake pipe increases (when the throttle valve is opened), the regulator valve opens already at a higher fuel pressure and the fuel pressure in the rail increases.
Air filter 1 - (see fig. 2) is installed in the front of the engine compartment on rubber mounts.
The filter element is paper, flat, with a large filtering surface area.
The filter is connected to the throttle assembly by a two-piece corrugated air supply pipe.
A mass air flow sensor is installed between the nozzle and the filter.
Throttle assembly 3 - (fig. 5) is fixed on the receiver. It doses the amount of air entering the intake pipe.
The intake of air into the engine is controlled by a throttle valve connected to the accelerator pedal drive.
The throttle pipe includes a throttle position sensor 4 (Fig. 5) and an idle speed controller 5.
In the flow part of the throttle pipe (before and behind the throttle valve) there are vacuum extraction holes necessary for the operation of the crankcase ventilation system and the adsorber of the gasoline vapor recovery system.
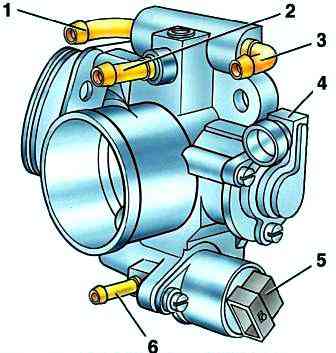
Idle speed control 5 - (see fig. 5) regulates the speed of the crankshaft at idle, controlling the amount of air supplied bypassing the closed throttle.
It consists of a two-pole stepper motor and a cone valve connected to it.
The valve is extended or retracted by controller signals.
When the regulator needle is fully extended (corresponding to 0 steps), the valve completely blocks the air passage.
When the needle is retracted, an air flow is provided that is proportional to the number of steps the needle moves away from the seat.
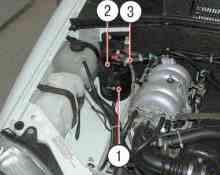
In the fuel vapor recovery system, the method of vapor absorption by a carbon adsorber 4 was used (see Fig. 6).
It is installed in the engine compartment and is connected by pipelines to the fuel tank and throttle pipe.
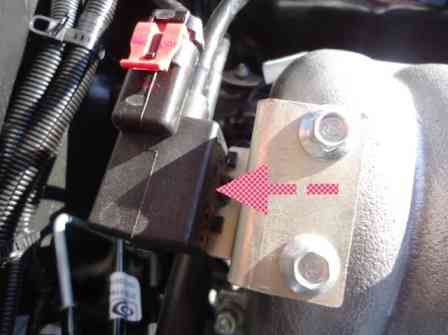
On the canister cover there is an adsorber purge solenoid valve (on new models, the canister purge valve is installed on the rear of the receiver), which switches the system operation modes based on signals from the engine control unit.
When the engine is not running, the solenoid valve is closed and gasoline vapors from the fuel tank are piped to the canister, where they are absorbed by granular activated carbon.
When the engine is running, the canister is purged with air and the vapors are sucked off to the throttle assembly, and then into the inlet pipe for combustion during the working process.
The controller controls the purge of the canister, including the solenoid valve located on the canister cover.
When voltage is applied to the valve, it opens, releasing vapors into the intake pipe. The valve is controlled by the method of pulse-width modulation.
The valve turns on and off at a rate of 16 times per second (16 Hz). The higher the air flow, the longer the duration of the valve activation pulses.
The controller turns on the canister purge valve when all of the following conditions are met:
- - coolant temperature above 75 °С;
- – vehicle speed exceeds 10 km/h.
After the valve is turned on, the speed criterion changes. The valve will only turn off when the speed drops to 7 km/h;
- - Throttle opening is greater than 4%. This factor does not matter further if it does not exceed 99%.
When the throttle valve is fully opened, the controller turns off the canister purge valve.
Failures in the evaporative emission system will result in unstable idling, engine shutdown, increased toxicity of exhaust gases and deterioration in driving performance.
The following system malfunctions are possible:
- - purge solenoid valve malfunction;
- – adsorber damage;
- – adsorber overflow, gaining more than 60 g of fuel (the weight of the new adsorber is not more than 1.1 kg);
- - damage or incorrect connection of hoses.