In accordance with the maintenance schedule, the timing belt (timing) is replaced every 120 thousand km of the vehicle or after 6 years (whichever comes first), regardless of its condition
Belt failure (broken or sheared teeth) will cause the valves to hit the pistons due to the misalignment of the crankshaft and camshaft rotation angles and, as a result, to costly engine repairs.
Therefore, we recommend checking the condition of the belt every time the car is serviced.
We perform work on a viewing ditch or overpass.
The surface of the toothed part of the belt should not have folds, cracks, undercutting of the teeth and delamination of the fabric from the rubber.
The reverse side of the belt should not show wear, exposing the cord threads, and signs of burning.
There should be no delaminations on the end surfaces of the belt.
The belt should also be replaced if it shows traces of oil.
It should be noted that there are no marks on the engine toothed pulleys for setting the engine valve timing - at authorized dealer services, when replacing the timing belt, a special tool and fixtures are used to fix the crankshaft and camshafts.
When replacing a belt, it is necessary to change not only the toothed belt, but also its tension and support rollers, as well as the bolt for securing the accessory drive pulley.
Therefore, we recommend that the timing belt replacement operations be performed at a specialized service that has the necessary equipment and spare parts, at the same time, an experienced driver with the appropriate skills to repair modern engines will be able to perform the timing belt replacement operations on their own.
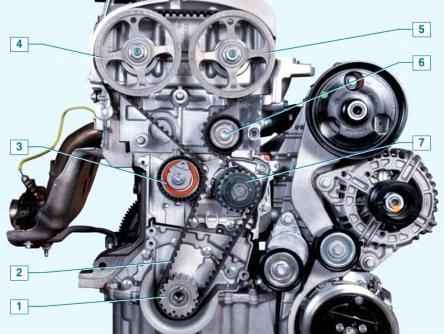
To assess the condition and replace the timing belt, remove the right support of the power unit and the right mudguard of the engine compartment.
For clarity, we show the operation on a dismantled engine.
With a 13 head, we unscrew the three bolts and two nuts securing the upper timing cover
Remove the cover
With a head of 18, we turn the crankshaft clockwise for the bolt securing the auxiliary drive pulley and visually assess the condition of the timing belt, as described above.
You can estimate the belt tension by the location of the pointers on the belt tensioner.
With normal belt tension, the movable pointer 1 (Fig. 3) should coincide with the notch of the fixed pointer 2 of the tension roller (for clarity, shown with the lower timing cover removed).
If the movable pointer is slightly offset relative to the fixed pointer counterclockwise, then the belt tension is not enough and the belt can be tightened.
To do this, loosen the tightening of the tension roller fastening nut with a 13 wrench and turn the roller clockwise by 6 with a hexagon (pulling the belt) until the pointers are aligned.
Holding the roller in this position, tighten the nut of its fastening.
Having turned the crankshaft two turns clockwise for the bolt securing the accessory drive pulley, we again check the belt tension and repeat the adjustment if necessary.
Install the dismantled parts in reverse order.
To replace the timing belt, remove the accessory drive belt and top timing cover.
Before loosening the bolt securing the accessory drive pulley, it is necessary to block the crankshaft from turning.
To do this, the assistant must shift the gearbox to the highest gear, press the brake pedal and apply the parking brake.
With a head of 18, we unscrew the bolt securing the accessory drive pulley
Remove the bolt with washer
Remove the accessory drive pulley
With a head of 8, we unscrew the four bolts securing the lower timing cover
Remove the bottom cover
In order not to disturb the valve timing, before removing the timing belt, it is necessary to set the crankshaft and camshafts to the TDC (top dead center) position of the compression stroke of the 1st cylinder
To turn the crankshaft, we screw in place the bolt securing the auxiliary drive pulley, installing a spacer (sleeve or set of washers) between the bolt and the end of the shaft.
The crankshaft can also be rotated by turning the (in place) front right wheel clockwise with the transmission in top gear.
In order to facilitate turning the shaft, we turn out the spark plugs.
To determine the position of the camshafts, it is necessary to remove two rubber-metal plugs from the holes in the left end of the cylinder head.
Remove the air intake with the air path resonator.
Poke the center of the plug with a screwdriver
Using a screwdriver as a lever, we remove the plug from the hole in the cylinder head.
We also extract another stub.
Turn the crankshaft clockwise until the grooves on the ends of the camshafts take a horizontal position (located parallel to the plane of the connector of the cover and cylinder head) and are shifted down relative to the axes of the camshafts.
To fix the camshafts when replacing the belt, a simple tool can be made from a metal plate 5 mm thick (see sketch).
We install the device in the grooves of the shafts.
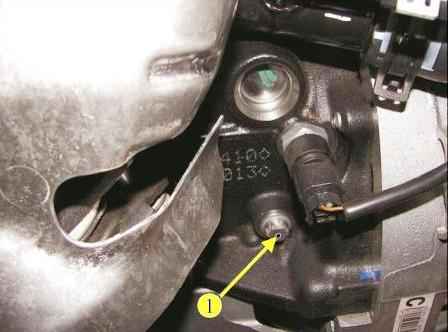
To check that the crankshaft is in the TDC position of the pistons of the 1st and 4th cylinders, a threaded hole is provided on the front wall of the cylinder block (under the starter), into which a plug is screwed
Unscrew the cap with the E-14 head.
It is necessary to screw a special locating pin (with a threaded length of 75 mm) into the hole.
When the crankshaft is in the TDC position of the pistons of the 1st and 4th cylinders, the finger should rest against the milled area on the cheek of the crankshaft and block the shaft when you try to turn it clockwise.
An M10 bolt can be used as a mounting pin.
We screw two adjusting nuts onto the bolt and lock them so that the length of the threaded part of the bolt is 75 mm.
We screw the assembled fixture (installation pin) into the threaded hole of the cylinder block.
When the crankshaft is in the TDC position of the pistons of the 1st and 4th cylinders, the mounting pin 1 must be screwed into the hole to the end of the thread and rest against the milled area 2 on the crankshaft web (shown with the crankcase removed).
This will prevent the crankshaft from turning clockwise.
If, when screwing in the adjusting pin, it rests, and the end of the adjusting nut on the pin does not come into contact with the end face of the boss of the hole in the cylinder block (there will be a gap between the nut and the boss), then you need to turn a little (by removing the device from the grooves of the camshafts) crankshaft shaft counterclockwise.
Then you need to screw the mounting pin into the hole of the cylinder block to the end (until the ends of the pin nut and the boss of the hole in the block touch) and turn the crankshaft clockwise until the platform of the shaft cheek stops against the pin.
Install the camshaft locking tool, if it was removed
Having loosened the tightening nut of the tension roller with a 13 wrench, turn the roller counterclockwise, reducing the tension of the timing belt
Remove the belt from the tensioner
Then remove from the pulleys of the coolant pump, crankshaft and camshafts.
Marking of the timing belt (the number of teeth is 131, the width is 25.4 mm).
When replacing the belt, the idler and idler rollers must also be replaced.
We unscrew the nut securing the tension roller and remove it from the stud of the coolant pump housing.
Use the Torx-50 key to unscrew the support roller fastening screw
Remove the support roller and its bushing.
Install the new support roller in reverse order.
When installing a new timing belt (which has arrows), we orient it so that the arrows coincide with the direction of movement of the belt (clockwise).
We install the belt on the gear pulleys of the crankshaft, coolant pump and camshaft pulleys.
Then, at the same time, we put the belt on a new tension roller and install the roller on the stud of the coolant pump housing
When installing the tension roller, insert the bent end 1 of the roller bracket into the recess 2 of the coolant pump housing.
Adjust the tension of the timing belt.
We unscrew the mounting pin from the hole in the cylinder block and remove the device for fixing the camshafts.
Turn the crankshaft two turns clockwise until the grooves on the ends of the camshafts are in the desired position.
Check the valve timing and belt tension.
If necessary, repeat the installation of the timing belt.
We wrap the plug into the hole in the cylinder block.
With light blows of a hammer with a plastic striker, we press new plugs into the holes of the cylinder head.
Further assembly of the engine is carried out in the reverse order.
Replace the accessory drive pulley bolt with a new one and tighten to the prescribed torque.
Tightening torques for fasteners when replacing the timing belt:
- - bolt for fastening the right support to the body - 62 Nm;
- - nut of the bolt for fastening the pillow of the right support to the body;
- - bolt for fastening the accessory drive pulley 20 Nm, tighten 135˚±15˚;
- - nut for fastening the axle of the timing belt tensioner roller:
- - stage 1 - 7 Nm;
- - stage 2 - 27 Nm.
- - bolt for fastening the timing belt support roller - 45 Nm.