Die Hauptabmessungen des Zylinderblocks sind in Abbildung 1 angegeben.
Zylinderblock aus speziellem niedriglegiertem Gusseisen gegossen
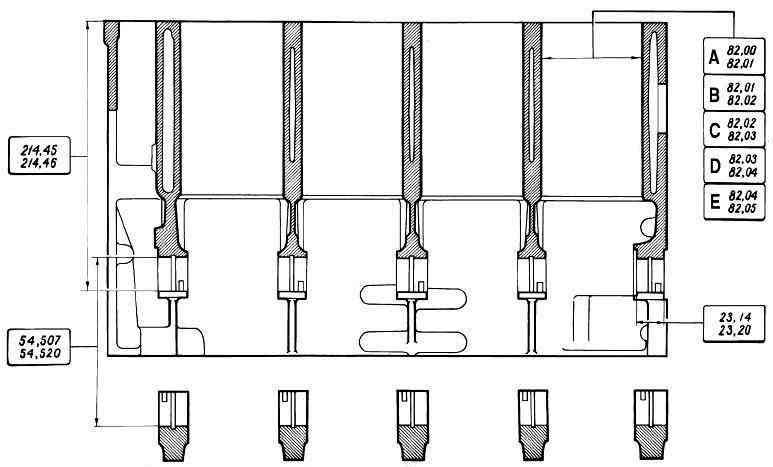
Zylinderdurchmesser werden in fünf Klassen bis 0,01 mm eingeteilt, gekennzeichnet durch die Buchstaben A, B, C, D, E.
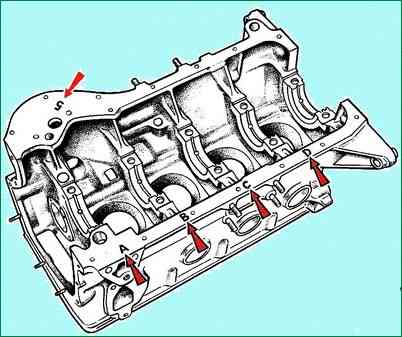
Die Zylinderklasse ist auf der unteren Ebene des Zylinderblocks eingeprägt
Es ist möglich, Zylinder für Reparaturkolben mit einem Durchmesser von 0,4 und 0,8 mm aufzubohren.
Hauptlagerdeckel werden komplett mit Zylinderblock bearbeitet.
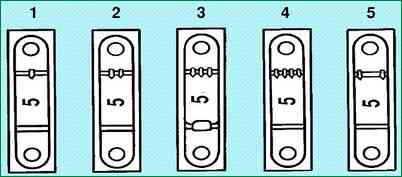
Daher sind sie nicht austauschbar und weisen zur Unterscheidung Markierungen auf der Außenfläche auf (Abb. 3).
Überprüfung des technischen Zustands und Reparatur
Waschen Sie den Zylinderblock gründlich und reinigen Sie die Ölkanäle.
Mit Druckluft ausblasen und trocknen, Zylinderblock prüfen. Risse in Lagern oder anderen Stellen im Zylinderblock sind nicht zulässig.
Wenn der Verdacht besteht, dass Kühlmittel in das Kurbelgehäuse gelangt ist, überprüfen Sie die Dichtheit des Zylinderblocks auf einem speziellen Ständer.
Zu diesem Zweck spritzen Sie nach dem Verschließen der Löcher im Kühlmantel des Zylinderblocks Wasser mit Raumtemperatur und einem Druck von 0,3 MPa (3 kgf/cm 2) hinein.
Zwei Minuten lang darf kein Wasser aus dem Zylinderblock austreten.
Wenn Öl in das Kühlmittel gelangt, prüfen Sie, ohne den Motor vollständig zu zerlegen, den Zylinderblock im Bereich der Ölkanäle auf Risse zu prüfen.
Dazu das Kühlmittel aus dem Kühlsystem ablassen, den Zylinderkopf abnehmen, den Kühlmantel des Zylinderblocks mit Wasser füllen und dem vertikalen Ölkanal des Zylinderblocks Druckluft zuführen.
Wenn im Wasser, das den Kühlmantel füllt, Luftblasen auftreten, tauschen Sie den Zylinderblock aus.
Überprüfen Sie die Trennebene des Zylinderblocks mit dem Kopf mithilfe eines Lineals und eines Satz Fühlerlehren.
Das Lineal wird entlang der Diagonalen der Ebene und in der Mitte in Längsrichtung und quer eingestellt. Die Ebenheitstoleranz sollte 0,1 mm nicht überschreiten.
Reparatur von Zylindern
Überprüfen Sie, ob der Verschleiß der Zylinder den maximal zulässigen Wert von 0,15 mm überschreitet.
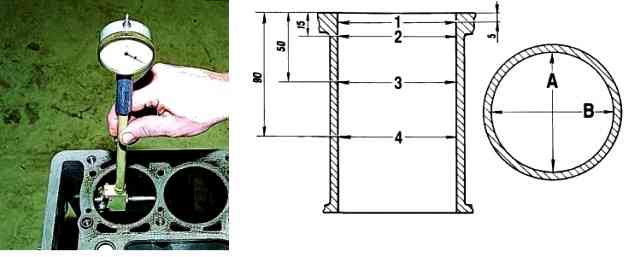
Der Zylinderdurchmesser wird mit einem Bohrungsmessgerät (Abb. 4) in vier Zonen sowohl in Längs- als auch in Querrichtung des Motors gemessen. Mit einem Mikrometer wird die Innenlehre auf Null eingestellt.
Im Bereich von Band 1 verschleißen die Zylinder praktisch nicht. Daher kann man anhand der Differenz der Messungen in der ersten und anderen Zonen das Ausmaß des Zylinderverschleißes beurteilen.
Wenn der maximale Verschleißwert mehr als 0,15 mm beträgt, bohren Sie die Zylinder auf das nächstliegende Reparaturmaß auf und lassen dabei eine Toleranz von 0,03 mm für den Hondurchmesser.
Anschließend werden die Zylinder gehont und dabei ein solcher Durchmesser beibehalten, dass beim Einbau des ausgewählten Reparaturkolbens das geschätzte Spiel zwischen ihm und dem Zylinder 0,025–0,045 mm beträgt.
Endkappen austauschen
Ersetzen der Ölkanalstopfen:
- - Bohren Sie in der Mitte des Dübels 1, Abbildungen 5 und 6, ein Loch mit einem Durchmesser von 4 ... 5 mm;
- - Entfernen Sie den Stub aus Block 2;
- - Entgraten, reinigen und entfetten Sie die Sitzfläche unter dem Stopfen;
- - Entfetten Sie den neuen Stopfen;
- - Tragen Sie anaeroben Kleber auf die Sitzfläche des Zylinderblocks unter dem Stopfen auf (anaerober Kleber AN-112);
Beim Einbau der Endkappe 1/01586/01:
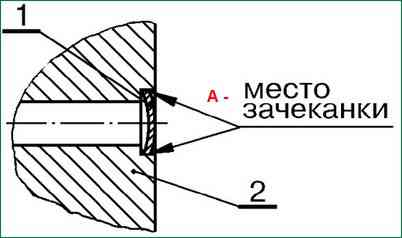
- - Setzen Sie den Stopfen 1 (Abb. 5) in das Loch des Ölkanals ein und stauchen Sie ihn ein;
- - Achten Sie auf die Passform des Steckers;
Beim Einbau des Steckers 21083-1002046:
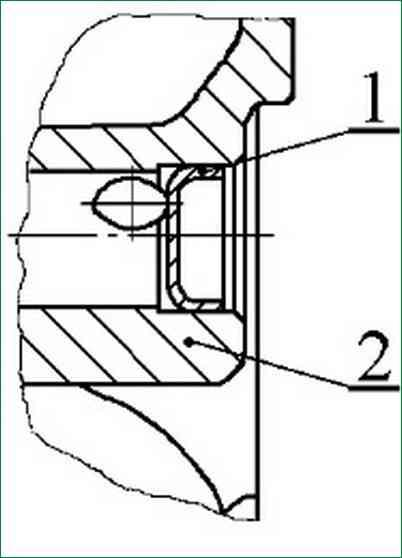
- - Setzen Sie den Stopfen 1 (Abb. 6) in das Loch im Ölkanal ein und drücken Sie ihn mit einem Dorn hinein. Die Presstiefe ist technologisch gegeben (Dorn 67.7853-9631).
Ersetzen der Kühlsystemstopfen:
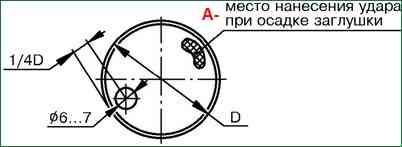
- - Bohren Sie ein Loch in den Dübel mit einem Durchmesser von 6-7 mm in einem Abstand von 1/4 seines Durchmessers vom Rand, wie in Abbildung 7 gezeigt;
- - Drücken Sie den Stopfen auf der dem Loch diametral gegenüberliegenden Seite, bis ein Spalt zwischen der Innenwand des Zylinderblocks und der Kante des Stopfens entsteht;
- - Führen Sie die Firmware oder einen Technologiestab in das Loch ein und entfernen Sie den Stopfen vom Zylinderblock;
- - Entgraten, reinigen und entfetten Sie die Sitzfläche unter dem Stopfen;
- - Entfetten Sie den neuen Stopfen;
- - Tragen Sie anaeroben Kleber auf die Sitzfläche des Zylinderblocks unter dem Stopfen auf (anaerober Kleber AN-112);
- - einen neuen Dübel einbauen (Bohrer 67.7853-9590 für Dübel 00001-0043299-01-0 mit einem Durchmesser von 40 mm, Dorn 67.7853-9591 für Dübel 00001-0043289-01-0 mit einem Durchmesser von 25 mm, Hammer ).