Reparación de cabeza de motor 1MZ-FE
Antes de retirar las válvulas, retire los taqués y calzos
Guarde los taqués y calces en el orden en que fueron instalados.
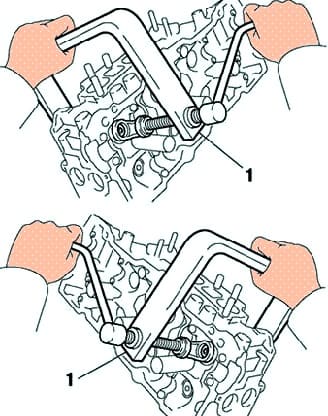
Usando la herramienta especial, comprima el resorte de la válvula y retire las dos chavetas (Fig. 1).
Retire la tapa del resorte de la válvula, el resorte de la válvula, la válvula y el asiento del resorte.
Con unos alicates, retire los sellos del vástago de la válvula.
Reemplazo de válvula y guía
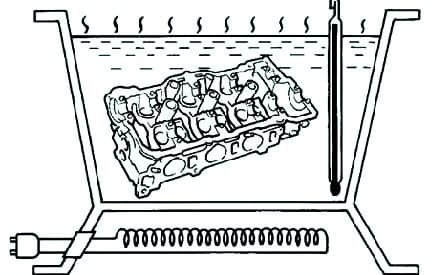
Caliente gradualmente la culata en un baño de agua a una temperatura de 80-100°C (Fig. 2).
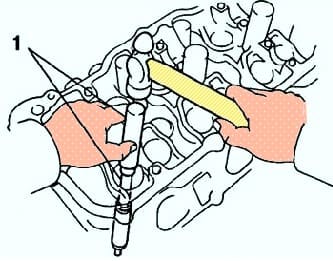
Con un punzón y un martillo, extraiga el casquillo guía (fig. 3).
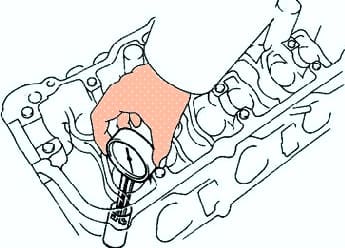
Con un calibrador interior, mida el diámetro del orificio del casquillo guía en la carcasa de la culata (Fig. 4).
Seleccione un nuevo tamaño para el diámetro exterior de la guía de la válvula (estándar o reacondicionamiento de +0,05 mm).
Si el diámetro del orificio para la guía en la carcasa del cabezal del bloque supera los 10,313 mm, taladre el orificio para el casquillo guía con un diámetro de reparación (+0,05 mm) de 10,345–10,363 mm.
Si el diámetro del orificio para la guía en la carcasa de la cabeza del bloque excede el tamaño de reparación, reemplace la cabeza del cilindro.
Seleccione los casquillos de las válvulas de entrada y salida en función de los diámetros de los orificios guía.
Utilice un casquillo estándar si el diámetro del orificio guía es de 10,295–10,313 mm.
Utilice casquillo de reparación (+0,05 mm) si el diámetro del orificio guía es de 10,345–10,363 mm.
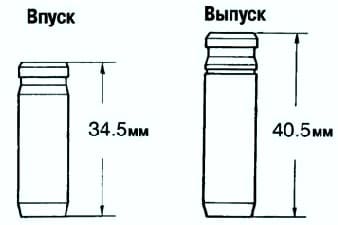
Las guías de las válvulas de admisión y escape difieren en longitud (fig. 5).
Longitud del buje guía:
- - válvulas de entrada - 34,5 mm;
- - válvulas de escape - 40,5 mm.
Caliente la culata en un baño de agua a una temperatura de 80–100 °C.
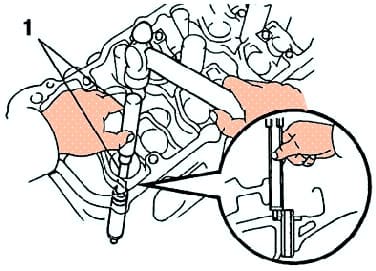
Con un punzón y un martillo, instale la nueva guía de válvula de manera que sobresalga de la cabeza del bloque en la medida adecuada (fig. 6).
Saliente del casquillo guía:
- - válvula de entrada - 11,5–11,3 mm;
- - válvula de escape - 8,9–9,3 mm.
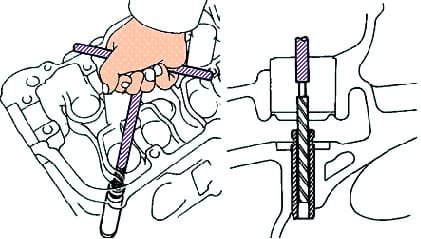
Con un escariador de 5,5 mm, escariar el orificio interior de la guía para proporcionar la holgura nominal entre la guía y el vástago de la válvula (fig. 7)
Comprobación y lapeado de válvulas
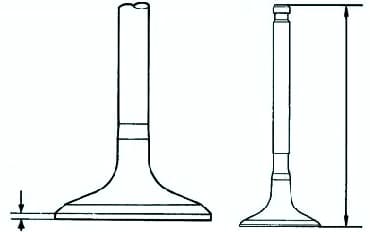
Rectifique las válvulas hasta eliminar los rastros de hollín y rayones.
Asegúrese de que el bisel lapeado de la válvula forme un ángulo de 44,5° con respecto a un plano perpendicular al eje del vástago.
Verificar el espesor de la parte cilíndrica del disco de la válvula (Fig. 8).
El grosor estándar de la placa es de 1,0 mm.
Si el grosor de la parte cilíndrica del disco de la válvula es inferior al valor mínimo permitido, reemplace la válvula.
Compruebe la longitud total de la válvula
Si la longitud total es menor que el mínimo, reemplace la válvula.
Longitud nominal:
- válvula de entrada - 95,45 mm;
- válvula de escape - 95,40 mm.
Longitud total mínima:
- válvula de entrada - 94,95 mm;
- válvula de escape - 94,90 mm.
Compruebe el estado de las caras de las válvulas para ver si están desgastadas.
Si la cara de la válvula está desgastada, rectificar la cara de la válvula o reemplazar la válvula.
Después de rectificar, verifique la longitud total de la válvula.
Luego, con un cortador de carburo de 45°, pula los asientos de las válvulas, quitando solo la cantidad mínima de metal para limpiar los biseles de los asientos.
Compruebe el asiento adecuado de la válvula.
Aplique una fina capa de blanco al bisel de la válvula.
Presione la cara de la válvula contra el asiento, pero no gire la válvula.
Luego retire la válvula e inspeccione el asiento y el bisel de la válvula.
Si queda pintura alrededor de toda la circunferencia (360°) del bisel de la válvula, entonces la válvula es concéntrica.
De lo contrario, reemplace la válvula.
Si la pintura aparece alrededor de toda la circunferencia (360°) del asiento de la válvula, la guía de la válvula (manguito) y el asiento de la válvula son concéntricos.
De lo contrario, rectificar el bisel.
Asegúrese de que el parche de contacto esté en el centro de la cara de la válvula y tenga un ancho de 1,0 a 1,4 mm.
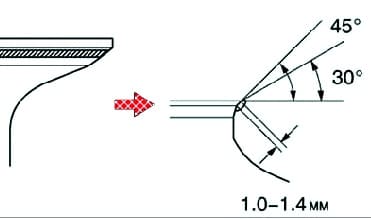
De lo contrario, ajuste el chaflán para que el parche de contacto no quede demasiado alto en el chaflán de la válvula.
Para rectificar el asiento, utilice fresas cónicas de 30° y 45° (fig. 10)
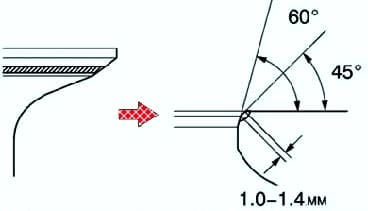
Si el parche de contacto está demasiado bajo en la cara de la válvula, use cortadores cónicos de 75° y 45° para rectificar el asiento (fig. 11).
Pula a mano la válvula y el asiento de la válvula con pasta abrasiva.
Después de lapear, limpie la válvula y el asiento de la válvula.
Comprobación del resorte de la válvula
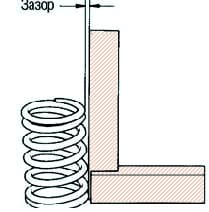
Con una escuadra de metal (90°), verifique que el resorte de la válvula no esté perpendicular, como se muestra en la figura 12.
La no perpendicularidad máxima permitida es - 2,0 mm
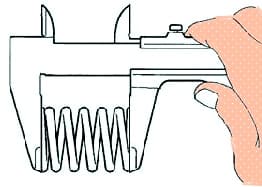
Utilice un calibrador para medir la longitud libre del resorte (Fig. 13).
La longitud del resorte de la válvula es de 45,50 mm.
Si la longitud del resorte está fuera de las especificaciones, reemplace el resorte de la válvula.

Con un probador de resortes, mida la fuerza requerida para comprimir el resorte a la longitud de instalación (fig. 14).
La fuerza elástica del resorte con una longitud de 33,8 mm es de 186 a 206 N.
Si la fuerza está fuera de rango, reemplace el resorte de la válvula
Comprobación del levantaválvulas
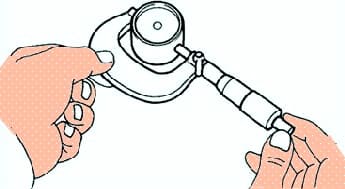
Con un micrómetro, mida el diámetro del levantaválvulas (Fig. 15).
El diámetro del empujador es de 30,968–30,976 mm.
Calcular la holgura de aceite.
Reste el diámetro del empujador del orificio del empujador en la carcasa del cabezal y determine la holgura.
Liquidación de aceite:
- estándar - 0,024–0,050 mm;
- máximo - 0,07 mm.
Si el espacio excede el máximo permitido, reemplace el empujador. Si es necesario, reemplace la culata.