1MZ-FE Motorkopfreparatur
Bevor Sie die Ventile entfernen, entfernen Sie die Stößel und Unterlegscheiben
Bewahren Sie Stößel und Ausgleichsscheiben in der Reihenfolge auf, in der sie eingebaut wurden
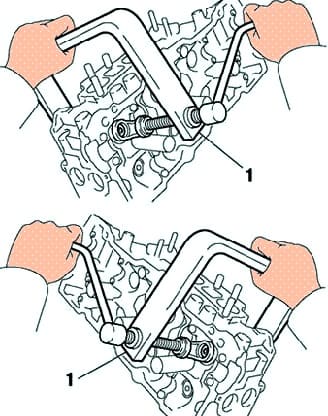
Mit dem Spezialwerkzeug die Ventilfeder zusammendrücken und die beiden Keile entfernen (Abb. 1).
Entfernen Sie die Ventilfederkappe, die Ventilfeder, das Ventil und den Federsitz.
Entfernen Sie die Ventilschaftdichtungen mit einer Zange.
Austausch des Ventils und der Führungshülse
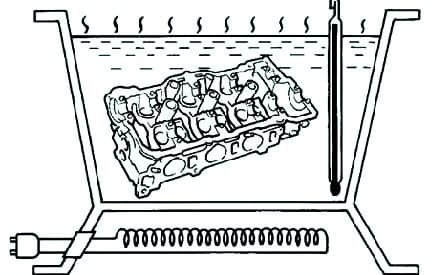
Den Zylinderkopf in einem Wasserbad langsam auf eine Temperatur von 80–100°C erwärmen (Abb. 2).
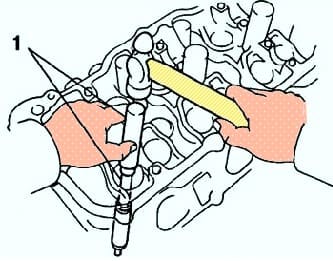
Mit einem Dorn und einem Hammer die Führungsbuchse herausdrücken (Abb. 3).
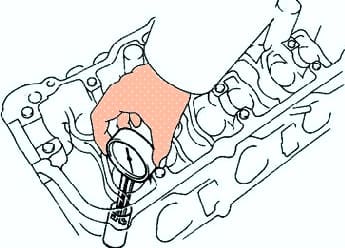
Messen Sie den Durchmesser der Bohrung für die Führungsbuchse im Zylinderkopfgehäuse mit einer Bohrungslehre (Abb. 4).
Wählen Sie eine neue Größe für den Außendurchmesser der Ventilführung (Standard oder Überholung +0,05 mm).
Wenn der Durchmesser des Lochs für die Führung im Kopfgehäuse 10,313 mm überschreitet, dann bohren Sie das Loch für die Führungshülse auf einen Reparaturdurchmesser (+0,05 mm) von 10,345–10,363 mm.
Wenn der Durchmesser des Lochs für die Führung im Kopfgehäuse das Reparaturmaß überschreitet, ersetzen Sie den Zylinderkopf.
Wählen Sie die Buchsen der Einlass- und Auslassventile in Abhängigkeit von den Durchmessern der Löcher für die Führungen aus.
Verwenden Sie eine Standardbuchse, wenn der Führungslochdurchmesser 10,295-10,313 mm beträgt.
Reparaturbuchse (+0,05 mm) verwenden, wenn der Durchmesser der Führungsbohrung 10,345–10,363 mm beträgt.
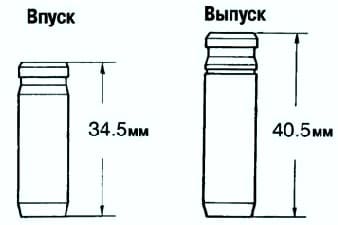
Einlass- und Auslassventilführungen sind unterschiedlich lang (Abb. 5).
Länge der Führungshülsen:
- - Einlassventile - 34,5 mm;
- - Auslassventile - 40,5 mm.
Erwärmen Sie den Zylinderkopf in einem Wasserbad auf eine Temperatur von 80–100 °C.
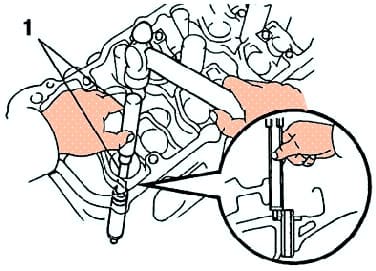
Setzen Sie die neue Ventilführung mit einem Dorn und einem Hammer so ein, dass sie um den entsprechenden Betrag aus dem Blockkopf herausragt (Abb. 6).
Führungsbuchsenüberstand:
- - Einlassventil - 11,5–11,3 mm;
- - Auslassventil - 8,9–9,3 mm.
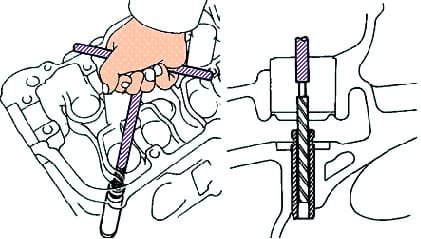
Reiben Sie mit einer 5,5-mm-Reibahle das innere Loch der Führung, um das nominelle Spiel zwischen der Führung und dem Ventilschaft bereitzustellen (Abb. 7)
Kontrolle und Läppen der Ventile
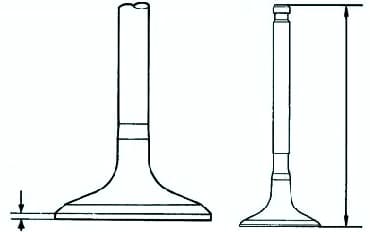
Schleifen Sie die Ventile, bis alle Kohlenstoffablagerungen und Kratzer entfernt sind.
Vergewissern Sie sich, dass Sie es haben Die Mündungsfase des Ventils bildet einen Winkel von 44,5° relativ zur Ebene senkrecht zur Achse der Stange.
Überprüfen Sie die Dicke des zylindrischen Teils des Ventiltellers (Abb. 8).
Die Standardplattendicke beträgt 1,0 mm.
Wenn die Dicke des zylindrischen Teils des Ventiltellers geringer als der zulässige Mindestwert ist, ersetzen Sie das Ventil.
Gesamtventillänge prüfen
Wenn die Gesamtlänge unter dem Mindestwert liegt, ersetzen Sie das Ventil.
Nennlänge:
- - Einlassventil - 95,45 mm;
- - Auslassventil - 95,40 mm.
Mindestgesamtlänge:
- - Einlassventil - 94,95 mm;
- - Auslassventil - 94,90 mm.
Überprüfen Sie den Zustand der Ventilflächen auf Verschleiß.
Wenn das Ventilende abgenutzt ist, schleifen Sie das Ende nach oder ersetzen Sie das Ventil.
Überprüfen Sie nach dem Schleifen die Gesamtventillänge.
Verwenden Sie dann einen 45°-Hartmetallfräser, um die Ventilsitze zu schleifen, und entfernen Sie nur die minimale Metallmenge, um die Sitzschrägen zu reinigen.
Prüfen Sie den korrekten Sitz des Ventils.
Tragen Sie eine dünne weiße Schicht auf die Abschrägung des Ventils auf.
Drücken Sie die Ventilfläche gegen den Sitz, aber drehen Sie das Ventil nicht.
Entfernen Sie dann das Ventil und überprüfen Sie den Ventilsitz und die Schräge.
Bleibt die Farbe um den gesamten Umfang (360°) der Ventilfase, dann ist das Ventil konzentrisch.
Wenn nicht, ersetzen Sie das Ventil.
Wenn die Farbe um den gesamten Umfang (360°) des Ventilsitzes erscheint, sind Ventilführung (Hülse) und Ventilsitz konzentrisch.
Fase andernfalls nachschleifen.
Stellen Sie sicher, dass sich die Kontaktfläche in der Mitte der Ventilfläche befindet und 1,0–1,4 mm breit ist.
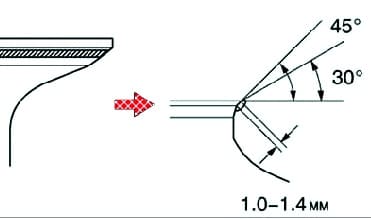
Wenn nicht, stellen Sie die Fase so ein, dass die Kontaktfläche nicht zu hoch auf der Ventilfase liegt.
Zum Nachschleifen des Sitzes 30°- und 45°-Konusfräser verwenden (Abb. 10)
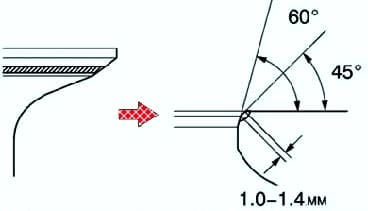
Wenn die Kontaktfläche auf der Ventilfläche zu niedrig ist, verwenden Sie 75°- und 45°-Konusfräser, um den Sitz nachzuschleifen (Abb. 11).
Ventil und Ventilsitz von Hand mit Schleifpaste läppen.
Reinigen Sie nach dem Läppen das Ventil und den Ventilsitz.
Ventilfederprüfung
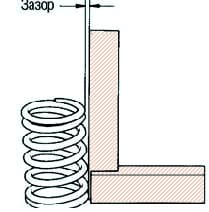
Mit einem Metallwinkel (90°) überprüfen, dass die Ventilfeder nicht senkrecht steht, wie in Abbildung 12 gezeigt.
Die maximal zulässige Abweichung von der Rechtwinkligkeit beträgt 2,0 mm
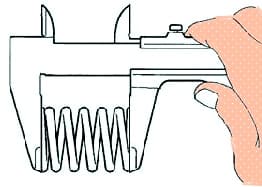
Messen Sie die freie Länge der Feder mit einem Messschieber (Abb. 13).
Die Länge der Ventilfeder beträgt 45,50 mm.
Wenn die Federlänge außerhalb der Spezifikation liegt, ersetzen Sie die Ventilfeder.

Messen Sie mit einem Federprüfgerät die Kraft, die erforderlich ist, um die Feder auf die Einbaulänge zusammenzudrücken (Abb. 14).
Die Federkraft bei einer Länge von 33,8 mm beträgt 186–206 N.
Wenn die Kraft außerhalb des zulässigen Bereichs liegt, ersetzen Sie die Ventilfeder
Ventilstößel prüfen
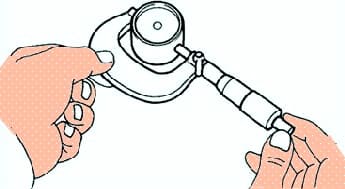
Messen Sie den Durchmesser des Ventilstößels mit einem Mikrometer (Abb. 15).
Schieberdurchmesser - 30,968–30,976 mm.
Berechnen Sie das Ölspiel.
Subtrahieren Den Wert des Drückerdurchmessers aus dem Wert des Stößelbohrungsdurchmessers im Kopfkörper ermitteln und das Spiel ermitteln.
Ölfreiheit:
- - Standard - 0,024–0,050 mm;
- - maximal - 0,07 mm.
Wenn der Abstand den maximal zulässigen Wert überschreitet, ersetzen Sie die Schubstange. Ersetzen Sie ggf. den Zylinderkopf.