Clean the bottoms of the pistons and the surface of the cylinder block mating with the cylinder head
Turning the crankshaft, sequentially set the pistons to TDC.
Clean the surfaces of the piston bottoms from carbon deposits with a scraper.
Use a scraper to remove the remaining head gasket from the cylinder block connector surface.
Use compressed air to remove carbon deposits and head gasket residue from surfaces and bolt holes.
Clean the cylinder head.
Clean the surface of the head of the block from the remnants of the head gasket.
Clean the surfaces of the combustion chambers of the block head with a wire brush, removing any remaining carbon deposits.
Clean the surface of the cylinder head (mating with the surface of the cylinder block) using a soft brush and solvent.
Clean the valve guide bores with a brush and solvent.
Checking the cylinder head for warpage
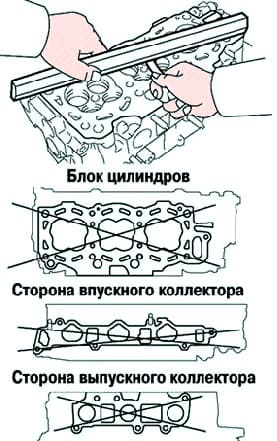
Using a straightedge and a flat feeler gauge as shown in Figure 1, check for warping of the cylinder head mating surfaces on the cylinder block surface and on the surfaces of the intake and exhaust manifolds.
Maximum surface distortion allowed:
- cylinder block - 0.05 mm;
- collectors - 0.08 mm.
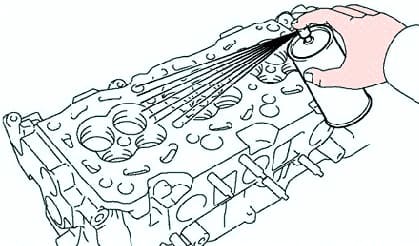
If the amount of warping is greater than the maximum, replace the cylinder head or grind it.
Using a penetrating dye, check for cracks in the combustion chambers, inlet and outlet ports, and at the gas interface (fig. 2).
If there are cracks, replace the cylinder head or weld it (with subsequent grinding).
The welding of cracks in the cylinder head must be carried out in specialized workshops.
Checking valves and valve guides
Clean the valves, to do this, remove carbon deposits from the valve plate with a scraper, then clean the valve with a brush.
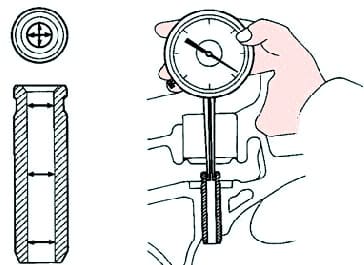
Check the diameters of the valve stems and the inner diameters of the valve guides, to do this, measure the inner diameter of the valve guides with an inside gauge (Fig. 3).
Sleeve Inner Diameter: 1MZ-FE - 5.510-5.530mm
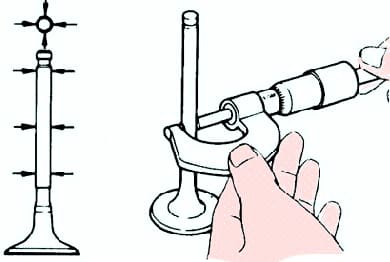
Also measure the diameter of the valve stem with a micrometer (Fig. 4).
Valve stem diameter:
- inlet valve - 5.470-5.485 mm;
- exhaust valve - 5.465-5.480 mm.
From the difference between the measurements of the valve stem diameter and the internal diameter of the guide sleeve, find the gap between the valve stem and its guide.
Standard oil clearance:
- inlet valve - 0.025-0.060 mm;
- outlet valve - 0.030-0.065 mm.
Maximum oil clearance:
- inlet valve - 0.08 mm;
- outlet - 0.10 mm. If the clearance is greater than the maximum, replace the valve and guide sleeve.