Die Anordnung des Zentrifugalölfilters ist in Abb. dargestellt. 1.
Das Waschen von Teilen des Zentrifugalölfilters aus Aluminiumlegierung ist in einer aggressiven Umgebung nicht zulässig
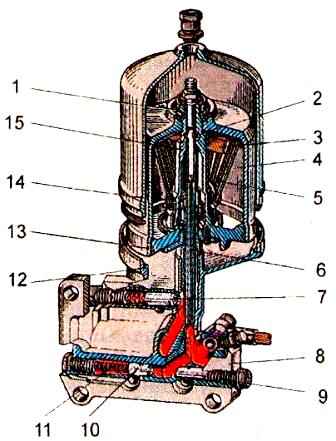
Beim Zusammenbau der Zentrifuge müssen saubere Teile verwendet werden.
Die Unebenheit der Passfläche des Filtergehäuses sollte über die gesamte Länge 0,08 mm nicht überschreiten.
Auf den Oberflächen der Öffnungen des Körpers 5 (Abb. 2) des Rotors und der Abdeckung 11, die mit den Hälsen der Achse 9 des Rotors zusammenpassen, sind Spuren chemischer Zerstörung nicht zulässig.
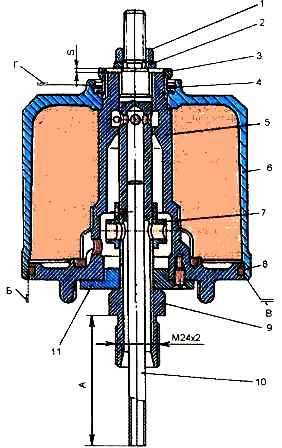
Es dürfen keine Gewindeschäden am Rotorkörper 5 vorhanden sein.
Die Fläche „G“ der Ringnut im Rotortopf für den Anlaufring 4 darf nicht beschädigt werden.
Die Unebenheit und Nichtparallelität der Seitenflächen des Druckrings sollte 0,1 mm nicht überschreiten.
Auf der Oberfläche „5“ des Rotorgehäuses, die mit dem Glas 6 des Rotors zusammenpasst, sind Kerben und Dellen nicht zulässig.
Die Unrundheit und Toleranz des Profils des Längsschnitts des Lochs im Rotorgehäuse unter dem oberen Hals der Rotorachse beträgt 0,01 mm.
Das Rotorgehäuse muss statisch ausgewuchtet sein. Restunwucht – nicht mehr als 150 g-mm.
Die Masse muss durch Bohren von Löchern mit einem Durchmesser von 6 mm am Ende des Rotorflansches bis zu einer Tiefe von maximal 2 mm korrigiert werden.
Die zylindrische Oberfläche des Bechers, die mit der Oberfläche „B“ des Rotors zusammenpasst, sollte keine Biegungen und Kerben aufweisen.
Die Unrundheit dieser Oberfläche beträgt 0,2 mm.
Die Oberfläche „B“ der Innenfase am Ende des Bechers 6 des Rotors sollte keine Kerben mit scharfen Kanten aufweisen.
Die Kerben müssen gereinigt werden.
Rotorbecher dynamisch ausgewuchtet.
Die Masse muss in zwei Ebenen korrigiert werden: am oberen Ende und an der Verdickung der unteren Fläche mit einer Tiefe von nicht mehr als 2 mm. Die Restunwucht beträgt nicht mehr als 50 mm.
Die Unrundheit und Toleranz des Profils des Längsschnitts des Lochs im Deckel 11 des Rotorgehäuses unter dem unteren Hals beträgt 0,01 mm.
Risse am Ölfiltergehäuse sind nicht zulässig.
Die Tiefe des Druckminderventilsitzes im Filtergehäuse darf 52 mm nicht überschreiten.
Die Tiefe des Ablassventilsitzes und des Zentrifugalfilterventilsitzes darf am Gehäuse 72 mm nicht überschreiten.
Die Krümmung der Federgeneratrix des Ablassventils und des Zentrifugalfilterventils, die frei auf der Platte liegen, sollte 1 mm nicht überschreiten.
Die Krümmung der Mantellinie der frei auf der Platte liegenden Druckminderventilfeder sollte 1 mm nicht überschreiten.
Der auf der Rotorachse montierte Deckel 11 des Rotorgehäuses muss sich frei von Hand drehen lassen.
Vor der Montage der Abdeckung muss der untere Zapfen der Rotorachse mit Motoröl geschmiert werden.
Kerben, Dellen, Risse und Verformungen der Düse 7 sind nicht zulässig.
Rohr 10 muss fest in der Rotorachse sitzen und herausragen, wobei das Maß „A“ 70 ± 0,5 mm beträgt.
Eine Krümmung des Rohrs 10 ist nicht zulässig.
Der Rundlauf der Außenfläche des Endes des gepressten Rohrs im Verhältnis zum durchschnittlichen Durchmesser des Gewindes M24x2 der Rotorachse sollte 0,3 mm nicht überschreiten.
Vor der Montage von Deckel und Rotorgehäuse müssen die Achszapfen mit Motoröl geschmiert werden.
Die Rotorachse muss zunächst mit Druckluft ausgeblasen werden.
Am zusammengebauten Rotorbecher sollte sich die Spezialmutter 3 frei von Hand drehen lassen.
Vor der Montage des Rotorbechers 6 am Rotorgehäuse muss der Gummidichtring mit Fett oder M-10G2-Motoröl geschmiert werden.
Das Schneiden und Zerreißen des Rings ist nicht gestattet.
Bei einem mit einer Achse montierten Rotor sollte der Spalt zwischen der Stirnfläche des Rotorkörpers 5 und der Anlaufscheibe 2 innerhalb von S = 0,3–1,5 mm liegen (siehe Abb. 2).
Der Rotor sollte sich durch die Kraft der Hand frei auf der Achse drehen können, ohne zu ruckeln und zu blockieren.
Das Filtergehäuse muss vor der Montage mit Druckluft ausgeblasen werden.
Bei der Montage der Rotorbaugruppe mit der Achse am Filtergehäuse muss die Rotorachse mit einem Drehmoment von 160…200 Nm angezogen werden.
Die Ventile müssen sich durch ihr Eigengewicht in den Sitzen des Filtergehäuses bewegen, ein Hängenbleiben der Ventile ist nicht zulässig.
Tests Der Zentrifugalölfilter am Stand KI-5278 sollte mit einem Gemisch aus Motoröl und Dieselkraftstoff mit einer Viskosität von 11,5–16 mm 2/s (cSt) bei der Testtemperatur durchgeführt werden.
Die Verwendung anderer Mineralöle ist zulässig, sofern die angegebene Viskosität während des Tests eingehalten wird.
Bei einer Prüftemperatur von 18..22°C kann eine Mischung bestehend aus 40 % M-10G- oder M-10V-Motoröl (nach Volumen) und 60 % Dieselkraftstoff verwendet werden.
Nach der Einstellung sollte sich das Zentrifugalölfilterventil bei einem Öldruck von 0,7 ± 0,02 MPa öffnen.
Der Beginn des Öffnens des Ablassventils sollte bei einem Druck des Arbeitsmediums über dem Ventil von 0,25–0,35 MPa erfolgen.
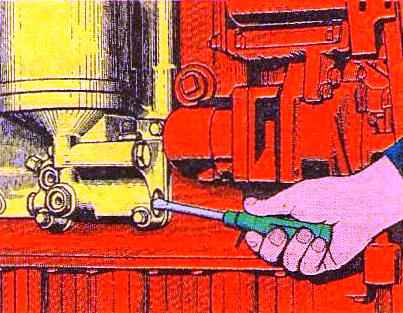
Die endgültige Einstellung des Ventils (Abb. 3) muss bei laufendem Dieselmotor durchgeführt werden, um den Öldruck in der Leitung bei Nennkurbelwellendrehzahl und Öltemperatur von 70–80 °C auf 0,25–0,35 MPa einzustellen.
Das Druckminderventil sollte bei einem Öldruck vor ihm von 0,05–0,06 MPa öffnen und das Öl sollte zur Atmosphäre umgeleitet werden.
Der blockierte Rotor auf der Achse muss bei einem Öldruck davor von mindestens 0,8 MPa und einem Gegendruck am Ausgang des Filters von mindestens 0,2 MPa auf Dichtheit geprüft werden.
In diesem Fall darf das Arbeitsmedium nicht mehr als 0,067 dm3/s durch die Rotorlager unter der Rotormutter (einschließlich entlang des Gewindes) austreten; Öllecks unter der Rotorschale sind nicht zulässig.
Auf dem KI-5278-Prüfstand sollten die Parameter bei einem Öldurchfluss durch den Rotor von 0,53 dm3/s und einem Filtereinlassdruck von 0,7 ± 0,02 MPa wie folgt sein:
- – Druck hinter dem Filter – nicht weniger als 0,25 MPa; Ölverbrauch in der Leitung – nicht weniger als 0,53 3/s;
- - Rotordrehzahl nicht weniger als 5500 min-1.
Der zusammengebaute Filter muss innerhalb von 1 Minute bei einem Druck am Eingang des Filters von 0,7–0,8 MPa und einem Gegendruck am Ausgang von mindestens 0,2 MPa auf Dichtheit überprüft werden.
Gleichzeitig sind Leckagen oder das Auftreten von Öltropfen auf der Außenfläche des Filters und an den Verbindungsstellen nicht zulässig.