Sie benötigen: eine tragbare Lampe, einen Satz flacher Sonden, ein Lineal, einen Messschieber, einen Messschieber, ein Mikrometer, einen Schaber
Nach der Demontage die Teile gründlich mit Kerosin waschen, ausblasen und mit Druckluft trocknen (insbesondere die Ölkanäle der Teile).
Inspizieren Sie den Block, insbesondere die Kurbelwellenlager.
Risse in irgendeinem Teil des Blocks sind nicht zulässig.
Wenn der Verdacht auf Risse im Block besteht (Kühlmittel gelangt in das Kurbelgehäuse oder Öl in das Kühlmittel), überprüfen Sie die Dichtheit des Blocks auf einem speziellen Ständer.
Führen Sie die Überprüfung in Werkstätten mit entsprechender Ausrüstung durch.
Inspizieren Sie die Zylinder auf beiden Seiten.
Kratzer, Kerben und Risse sind nicht erlaubt.
Bei der Untersuchung von Zylindern empfehlen wir Ihnen, die Spiegel der Zylinder mit einer tragbaren Lampe zu beleuchten – in diesem Fall sind Mängel deutlich besser zu erkennen.
Bestimmen Sie die tatsächlichen Zylinderdurchmesser mit einem Bohrungsmessgerät.
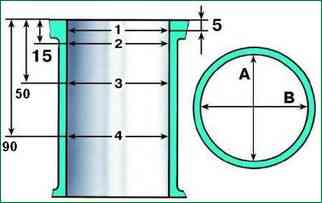
Messen Sie den Zylinderdurchmesser in vier Bändern (Abb. 1), die sich entlang der Höhe des Zylinders in einem Abstand von 5, 15, 50 und 90 mm von der Ebene des Anschlusses mit dem Blockkopf befinden.
Bei jedem Gürtel wird der Durchmesser in zwei zueinander senkrechten Richtungen (Längs- und Querrichtung) gemessen.
Zylinder des Blocks werden nach ihrem Durchmesser in fünf Klassen eingeteilt:
- A = 82,00 - 82,01 mm;
- B = 82,01–82,02 mm;
- C = 82,02-82,03 mm;
- D = 82,03–82,04 mm;
- E = 82,04-82,05 mm
Die Klasse jedes Zylinders des Blocks ist gemäß der Herstellerdokumentation auf der rechten Seite der unteren Ebene (der Ebene des Anschlusses mit der Ölwanne) eingeprägt.
Gemäß der Dokumentation des Herstellers sollte auf der linken Seite der unteren Ebene des Blocks ein Stempel mit der bedingten Nummer des Zylinderblocks angebracht werden.
Auf allen Hauptlagerdeckeln muss die gleiche Nummer vorhanden sein, um anzuzeigen, dass die Deckel zu diesem Block gehören.
Im Bereich des ersten Riemens (in einem Abstand von 5 mm von der Verbindungsebene mit dem Blockkopf) verschleißen die Zylinder praktisch nicht.
Anhand des Größenunterschieds in der ersten und anderen Zonen kann man den Verschleiß der Zylinder beurteilen.
Wenn der maximale Verschleißwert mehr als 0,15 mm beträgt, bohren Sie die Zylinder auf das nächste Kolbenübermaß auf (erhöht um 0,4 oder 0,8 mm) und lassen Sie dabei eine Toleranz von 0,03 mm für den Hondurchmesser.
Dann werden die Zylinder gehont und dabei ein solcher Durchmesser beibehalten, dass beim Einbau des ausgewählten Reparaturkolbens der geschätzte Spalt zwischen ihm und dem Zylinder 0,05–0,07 mm beträgt.
Fehlerbehebung, Bohren und Honen des Blocks sollten in Werkstätten mit Spezialausrüstung durchgeführt werden.
Überprüfen Sie die Ebenheit der Oberfläche des Zylinderkopfanschlusses.
Befestigen Sie einen Messschieber (oder ein Lineal) am Hobel: in der Mitte des Blocks; in Quer- und Längsrichtung; entlang der Diagonalen der Ebene.
Verwenden Sie in jeder Position eine Fühlerlehre, um den Abstand zwischen dem Messschieber und dem Hobel zu bestimmen.
Dies ist die Abweichung von der Ebenheit. Wenn die Abweichung mehr als 0,1 mm beträgt, ersetzen Sie den Block.
Reinigen Sie die Unterseite des Kolbens mit einem Schaber (kann aus einer alten Feile hergestellt werden).
Reinigen Sie die Kolbenringnuten mit dem alten Ring, indem Sie ihn drehen.
Überprüfen Sie die Kolben, Pleuel und Kappen: Sie dürfen keine Risse aufweisen.
Inspizieren Sie die Liner. Wenn Sie auf der Arbeitsfläche Risiken, Abnutzungserscheinungen oder Ablösungen der Gleitschicht feststellen, ersetzen Sie die Auskleidungen durch neue.
Alle Pleuellager sind gleich und austauschbar.
Messen Sie den Durchmesser der Kolben in einer Ebene senkrecht zur Achse des Kolbenbolzens in einem Abstand von 52,4 mm vom Kolbenboden.
Bestimmen Sie anhand der Messergebnisse das Spiel zwischen Kolben und Zylinder und wählen Sie gegebenenfalls neue Kolben aus Zylinder.
Das berechnete Spiel zwischen Kolben und Zylinder (für Neuteile) beträgt 0,05–0,07 mm. Sie wird durch Vermessung der Zylinder und Kolben ermittelt und durch den Einbau von Kolben gleicher Klasse wie die Zylinder sichergestellt.
Maximal zulässiges Spiel (bei abgenutzten Teilen) 0,15 mm.
Wenn ein gebrauchter Motor einen Spalt von mehr als 0,15 mm aufweist, müssen die Kolben an die Zylinder angepasst werden: Der Spalt sollte so nah wie möglich am berechneten liegen.
Führen Sie einen ölgeschmierten Finger in die Bohrung der Kolbennabe ein.
Der Bolzen dreht sich frei in den Kolbennaben und im oberen Ende der Pleuelstange. Nach dem Außendurchmesser werden die Finger bis 0,004 mm in drei Kategorien eingeteilt.
Die Kategorie wird durch die Farbe am Ende des Fingers angezeigt:
- 1. (blaue Markierung) – 21,982–21,986 mm;
- 2. Platz (grünes Etikett) – 21.986–21.990;
- 3. (rote Markierung) – 21.990–21.994.
Der Finger sollte durch die Kraft des Daumens fest, aber ohne zu verklemmen, in die Löcher der Nabe und der Pleuelstange passen.
Drehen Sie den Kolben vertikal mit der Fingerachse.
Der Finger darf nicht aus der Nabe fallen.
Ersetzen Sie den Finger, der aus dem Vorsprung herausfällt, durch einen anderen der nächsten Kategorie.
Wenn sich im Kolben ein Stift der Kategorie 3 befindet, ersetzen Sie den Kolben durch den Stift.
Überprüfen Sie den Höhenunterschied zwischen den Nuten im Kolben und den Ringen mit einer Fühlerlehre, indem Sie den Ring in die entsprechende Nut einführen.
Das nominale (berechnete) Spiel beträgt:
- – für den oberen (ersten) Kompressionsring 0,04–0,07 mm;
- - für den zweiten Kompressionsring 0,03–0,06 mm;
- - für Ölabstreifring 0,02–0,05 mm.
Maximal zulässiger Verschleißspalt: 0,15 mm.
Überprüfen Sie den Spalt im Verschluss der Ringe mit einer flachen Fühlerlehre, indem Sie den Ring bis zu einer Tiefe von etwa 50 mm in den Zylinder einbauen.
Um den Ring ohne Fehlausrichtung zu installieren, drücken Sie den Ring mit dem Kolben tief in den Zylinder.
Der Spalt wird bei Ringen überprüft, die in eine spezielle Lehre eingesetzt werden, deren Lochdurchmesser dem Nenndurchmesser des Rings mit einer Toleranz von ±0,003 mm entspricht.
Der Abstand sollte bei allen neuen Ringen 0,25–0,45 mm betragen.
Der maximale Verschleißspalt beträgt 1,0 mm.
Wenn kein Kaliber vorhanden ist, ist die Verwendung der gezeigten Methode zulässig.
Wenn nicht genügend Spiel vorhanden ist, sägen Sie die Verbindungsflächen des Rings ab. Wenn der Spalt den Grenzwert überschreitet, ersetzen Sie den Ring.
Überprüfen Sie nach Möglichkeit die Masse der Kolben: Bei einem Motor sollten sie nicht mehr als ± 2,5 g voneinander abweichen.
Sie können beschwert werden, indem das Metall an der gezeigten Stelle auf beiden Seiten des Kolbens entfernt wird.
Die Metallabtragstiefe sollte 4,5 mm, basierend auf der Nennkolbenhöhe von 59,4 mm, nicht überschreiten.
Messen Sie den Innendurchmesser D in der Pleuelsitzbaugruppe mit der Abdeckung mit einem Innenmessschieber.
Ziehen Sie die Muttern der Pleuelschrauben vor der Messung mit dem angegebenen Drehmoment fest.
Messen Sie die Dicke T der Pleuellager mit einem Messschieber
Messen Sie den Durchmesser Dn der Kurbelzapfen mit einem Mikrometer
Berechnen Sie das Spiel z zwischen den Pleuellagern und den Kurbelwellenzapfen mithilfe der Formel z=Dв–2T–Dн
Der nominale Konstruktionsspalt beträgt 0,02–0,07 mm. Grenzspalt 0,1 mm.
Wenn die tatsächliche Konstruktionslücke unter dem Grenzwert liegt, können Sie die installierten Liner wiederverwenden.
Wenn der Spalt größer als der Grenzwert ist, ersetzen Sie die Lager an diesen Lagerzapfen durch neue mit Nenndicke (1,723–1,730 mm).
Wenn die Kurbelwellenzapfen abgenutzt und auf Reparaturmaß geschliffen sind, ersetzen Sie die Laufbuchsen durch Reparaturlaufbuchsen (mit erhöhter Dicke):
- "0,25" = 1,848 - 1,855 mm;
- "0,50" = 1,973 - 1,980 mm;
- "0,75" = 2,098 - 2,105 mm;
- "1,0" = 2,223 - 2,230 mm. Der Nenndurchmesser der Pleuelzapfen beträgt 47,83–47,85 mm.
Die Hälse werden geschliffen, wenn sie Kerben und Risiken aufweisen oder der Verschleiß (oder die Ovalität) mehr als 0,03 mm beträgt, wobei der Durchmesser in Schritten von 0,25 mm verringert wird, um (abhängig vom Grad des Verschleißes) die folgenden Werte zu erhalten:
- "0,25" = 47,58 - 47,60 mm;
- "0,50" = 47,33-47,35 mm;
- "0,75" = 47,08 - 47,10 mm;
- "1,0" = 46,83 - 46,85 mm. Die Bezeichnungen „0,25“ und andere geben an, um wie viel sich der Durchmesser der Kurbelwellenzapfen nach dem Schleifen verringert.
Inspizieren Sie die oberen und unteren Hauptlagerschalen. Die oberen Schalen des 1., 2., 4. und 5. Hauptlagers haben eine Nut auf der Innenfläche (die unteren nicht).
Die mittlere (3.) Hauptlagerschale unterscheidet sich vom Rest durch eine größere Breite, außerdem hat ihre obere Schale keine Nut.
Wenn sich auf der Arbeitsfläche der Auskleidungen Flecken, Schrammen oder Ablösungen der Gleitschicht befinden, ersetzen Sie die Auskleidungen durch neue.
Es ist verboten, jegliche Montagearbeiten an den Linern durchzuführen.
Überprüfen Sie die Kurbelwelle. Risse sind nicht erlaubt.
Auf den Flächen, die mit den Arbeitskanten der Dichtungen zusammenpassen, dürfen keine Kratzer, Kerben oder Kratzer vorhanden sein. Falls gefunden, ersetzen Sie die Welle.
Messen Sie den Außendurchmesser Dn der Hauptzapfen mit einem Mikrometer.
Das tatsächliche Spiel zwischen den Hauptlagerschalen und den Hauptlagerzapfen der Kurbelwelle wird nach der für Pleuellager beschriebenen Methode ermittelt.
- Der nominale Konstruktionsspalt beträgt 0,026–0,073 mm.
- Das Grenzspiel beträgt 0,15 mm.
Wenn die tatsächliche Konstruktionslücke unter dem Grenzwert liegt, können Sie die installierten Liner wiederverwenden.
Wenn der Spalt größer als der Grenzwert ist, ersetzen Sie die Auskleidungen an diesen Hälsen durch neue mit Nenndicke (1,824–1,831 mm).
Wenn die Kurbelwellenzapfen abgenutzt und auf Reparaturmaß geschliffen sind, ersetzen Sie die Laufbuchsen durch Reparaturlaufbuchsen (mit erhöhter Dicke):
- "0,25" = 1,949 - 1,956 mm;
- "0,50" = 2,074 - 2,081 mm;
- "0,75" = 2,199 - 2,206 mm;
- "1,0" = 2,324 - 2,331 mm.
Der Nenndurchmesser der Hauptzapfen beträgt 50,799 - 50,819 mm. Die Hälse werden geschliffen, wenn sie Kerben und Risiken aufweisen oder der Verschleiß (oder die Ovalität) mehr als 0,03 mm beträgt, wobei der Durchmesser in Schritten von 0,25 mm reduziert wird, um (je nach Grad des Verschleißes) die folgenden Werte zu erhalten:
- "0,25" = 50,549 - 50,569 mm;
- "0,50" = 50,299 - 50,319 mm;
- "0,75" = 50,049 - 50,069 mm;
- "1,0" = 49,799 - 49,819 mm. Die Bezeichnungen „0,25“ und andere geben an, um wie viel sich der Durchmesser der Kurbelwellenzapfen nach dem Schleifen verringert.
Der entsprechende Stempel wird auf der ersten Wange der Kurbelwelle angebracht, zum Beispiel K 0,75; W 0,50.
Montieren Sie die Welle mit den äußersten Hauptzapfen auf den Prismen und überprüfen Sie sie anhand des Indikators:
- - Axialschlag der übrigen Hauptlagerzapfen (nicht mehr als 0,03 mm);
- - Axialschlag der Sitzflächen für das Kettenrad und das Lager der Eingangswelle des Getriebes (nicht mehr als 0,04 mm);
- - Verschiebung der Achsen der Pleuelzapfen von der Nennebene, die durch die Achsen der Pleuel- und Hauptzapfen verläuft (nicht mehr als ± 0,35 mm);
- – Planlauffehler des Flansches bei einem Durchmesser von 68 mm (nicht mehr als 0,025 mm).
Die Überprüfung des Rundlauffehlers ist in einer Werkstatt nahezu unmöglich. Lassen Sie dies daher in einer Werkstatt mit Spezialausrüstung durchführen.
Überprüfen Sie die Stopfen der Schmierkanäle.
Testen Sie sie vorsichtig mit einem Schraubenzieher. Wenn die Stecker nicht sicher installiert sind, ersetzen Sie sie.
Setzen Sie die Stopfen auf das UG-6-Dichtmittel und dichten Sie es an drei Stellen ab.
Wir raten davon ab, die Stöpsel selbst zu öffnen, um die Kanäle zu reinigen, was sicherlich nützlich ist.
Kontaktieren Sie Werkstätten mit Spezialausrüstung oder spülen Sie die Kanäle, ohne die Stopfen zu öffnen. Dazu gießen Sie Benzin in die radialen Kanäle (durch Pfeile dargestellt) und verschließen diese zunächst auf einer Seite mit Holzstopfen.
Halten Sie es mindestens 20 Minuten lang gedrückt und spülen Sie die Kanäle mit Benzin durch, indem Sie es mit einem Gummiball einspritzen.
Entfernen Sie die Holzstopfen nach dem Spülen der Verbindungskanäle (dargestellt in gestrichelten Linien).
Wenn nötig, wiederholen Sie die Spülung, bis sauberes Benzin austritt.