Вам знадобляться: переносна лампа, набір плоских щупів, лінійка, штангенциркуль, нутромір, мікрометр, шабер
Після розбирання ретельно вимийте деталі гасом, продуйте та просушіть їх стисненим повітрям (особливо масляні канали деталей).
Огляньте блок, особливо уважно – опори колінчастого валу.
Тріщини в будь-яких місцях блоку не допускаються.
Якщо є підозра на наявність тріщин у блоці (потрапила охолоджувальна рідина в картер або масло в охолоджувальну рідину), перевірте герметичність блоку на спеціальному стенді.
Перевірку проводьте в ремонтних майстернях, які мають відповідне обладнання.
Огляньте циліндри з обох боків.
Дряпини, задираки та тріщини не допускаються.
Під час огляду циліндрів рекомендуємо висвітлювати дзеркала циліндрів переносною лампою – при цьому дефекти видно значно краще.
Визначте нутроміром фактичні діаметри циліндрів.
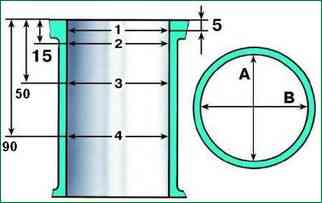
Діаметр циліндра виміряйте у чотирьох поясах (рис. 1), розташованих по висоті циліндра на відстані 5, 15, 50 та 90 мм від площини роз'єму з головкою блоку.
У кожному поясі діаметр вимірюють у двох взаємно перпендикулярних напрямках (у поздовжньому та поперечному).
Циліндри блоку діаметром поділяються на п'ять класів:
- A = 82,00–82,01 мм;
- B = 82,01-82,02 мм;
- C = 82,02-82,03 мм;
- D = 82,03–82,04 мм;
- E = 82,04–82,05 мм.
Клас кожного циліндра блоку відповідно до документації заводу-виробника відзначений клеймом на правій стороні нижньої площини (площини роз'єму з масляним картером).
Відповідно до документації заводу-виробника на лівій стороні нижньої площини блоку має бути нанесено тавро з умовним номером блоку циліндрів.
Такий же номер повинен бути на всіх кришках корінних підшипників для вказівки належності кришок до цього блоку.
У зоні першого пояса (на відстані 5 мм від площини роз'єму з головкою блоку) циліндри практично не зношуються.
За різницею розмірів у першому та інших поясах можна судити про знос циліндрів.
Якщо максимальне значення зносу більше 0,15 мм, розточіть циліндри до найближчого ремонтного розміру поршнів (збільшеного на 0,4 або 0,8 мм), залишивши припуск 0,03 мм на діаметр під хонінгування.
Потім відхонінгуйте циліндри, витримуючи такий діаметр, щоб при встановленні обраного ремонтного поршня розрахунковий зазор між ним і циліндром був 0,05–0,07 мм.
Дефектування, розточування та хонінгування блоку проводите в майстернях, що мають спеціальне обладнання.
Перевірте відхилення від площини поверхні роз'єму блоку з головкою циліндрів.
Прикладіть штангенциркуль (або лінійку) до площини: у середині блоку; у поперечному та поздовжньому напрямках; по діагоналях площині.
У кожному положенні плоским щупом визначте зазор між штангенциркулем та площиною.
Це буде відхилення від площинності. Якщо відхилення перевищує 0,1 мм, замініть блок.
Очистіть від нагару днище поршня шабером (можна виготовити зі старого напилка).
Очистіть від нагару канавки під поршневі кільця старим кільцем, обертаючи його.
Огляньте поршні, шатуни, кришки: на них не повинно бути тріщин.
Огляньте вкладки. Якщо на робочій поверхні виявите ризики, задираки та відшарування антифрикційного шару, замініть вкладки новими.
Всі шатунні вкладиші однакові та взаємозамінні.
Виміряйте діаметр поршнів у площині перпендикулярної осі поршневого пальця на відстані 52,4 мм від днища поршня.
За результатами вимірів визначте зазор між поршнем і циліндром і при необхідності підберіть нові поршні до циліндрів.
Розрахунковий зазор між поршнем та циліндром (для нових деталей) становить 0,05–0,07 мм. Його визначають проміром циліндрів і поршнів і забезпечують установкою поршнів того ж класу, що й циліндри.
Максимально допустимий зазор (при зносі деталей) 0,15 мм.
Якщо у двигуна, що був в експлуатації, зазор перевищує 0,15 мм, необхідно підібрати поршні до циліндрів: зазор повинен бути максимально наближеним до розрахункового.
Вставте змащений моторним маслом палець у отвір бобишки поршня.
Палець вільно обертається в бобишках поршня та у верхній головці шатуна. По зовнішньому діаметру пальці поділяються на три категорії через 0,004 мм.
Категорія вказується фарбою на торці пальця:
- 1-а (синя мітка) – 21,982–21,986 мм;
- 2-а (зелена мітка) – 21,986–21,990;
- третя (червона мітка) – 21,990–21,994.
Палець повинен щільно, але без заїдання входити в отвори боби і шатуна від зусилля великого пальця.
Поверніть поршень віссю пальця вертикально.
Палець не повинен випадати з бобишки.
Палець, що випадає з бобишки, замініть на наступну категорію.
Якщо в поршні палець третьої категорії, замініть поршень з пальцем.
Перевірте плоским щупом зазор по висоті між канавками в поршні та кільцями, вставляючи кільце у відповідну канавку.
Номінальний (розрахунковий) зазор становить:
- – для верхнього (першого) компресійного кільця 0,04–0,07 мм;
- – для другого компресійного кільця 0,03–0,06 мм;
- – для олійного кільця 0,02–0,05 мм.
Гарно допустимі зазори при зносі – 0,15 мм.
Перевірте плоским щупом зазор у замку кілець, встановивши кільце в циліндр на глибину близько 50 мм.
Щоб встановити кільце без перекосу, просуньте кільце вглиб циліндра поршнем.
Зазор перевіряють у кілець, вставлених у спеціальний калібр, що має діаметр отвору, що дорівнює номінальному діаметру кільця з допуском ±0,003 мм.
Зазор повинен становити 0,25–0,45 мм для всіх нових кілець.
При зносі гранично допустимий зазор – 1,0 мм.
За відсутності калібру можна застосовувати показаний спосіб.
Якщо зазор недостатній, спиляйте стикові поверхні кільця. Якщо зазор перевищує допустимий, замініть кільце.
При можливості перевірте масу поршнів: для одного двигуна вони не повинні відрізнятися один від одного більш ніж на ±2,5 г.
Можна підігнати їх по масі видаленням металу в показаному місці з обох боків поршня.
Глибина зняття металу не повинна перевищувати 4,5 мм, рахуючи від номінальної висоти поршня 59,4 мм.
Виміряйте нутроміром внутрішній діаметр Dв посадкового місця шатуна в зборі з кришкою.
Перед виміром затягніть гайки шатунних болтів номінальним моментом.
Виміряйте товщину Т шатунних вкладишів штангенциркулем
Виміряйте мікрометром діаметр Dн шатунних шийок
Розрахуйте зазор z між шатунними вкладишами та шийками колінчастого валу за формулою z=Dв–2T–Dн
Номінальний розрахунковий зазор становить 0,02-0,07 мм. Граничний проміжок 0,1 мм.
Якщо фактичний розрахунковий зазор менший за граничний, можна знову використовувати вкладки, які були встановлені.
Якщо зазор більший за граничний, замініть вкладиші на цих шийках новими номінальною товщиною (1,723–1,730 мм).
Якщо шийки колінчастого валу зношені та перешліфовані до ремонтного розміру, замініть вкладки ремонтними (збільшеної товщини):
- «0,25» = 1,848–1,855 мм;
- «0,50» = 1,973–1,980 мм;
- «0,75» = 2,098–2,105 мм;
- «1,0» = 2,223-2,230 мм. Номінальний діаметр шатунних шийок 47,83–47,85 мм.
Шийки шліфують, якщо на них є вибоїни та ризики або зношування (або овальність) становить більше 0,03 мм, зменшуючи діаметр з кроком 0,25 мм так, щоб отримати (залежно від ступеня зношування) наступні значення:
- «0,25» = 47,58–47,60 мм;
- «0,50» = 47,33–47,35 мм;
- «0,75» = 47,08–47,10 мм;
- «1,0» = 46,83-46,85 мм. Позначення «0,25» та ін. вказують, наскільки зменшується діаметр шийок колінчастого валу після шліфування.
Огляньте верхні та нижні вкладки корінних підшипників. Верхні вкладиші 1, 2, 4 і 5 корінних підшипників мають канавку на внутрішній поверхні (у нижніх її немає).
Вкладиші центрального (3-го) корінного підшипника відрізняються від інших більшою шириною, крім того, його верхній вкладиш не має канавки.
Якщо на робочій поверхні вкладишів є ризики, задираки, відшарування антифрикційного шару, замініть вкладки на нові.
Забороняється проводити будь-які підгонки на вкладишах.
Огляньте колінчастий вал. Тріщини не допускаються.
На поверхнях, що сполучаються з робочими крайками сальників, не повинно бути подряпин, вибоїн, рисок. Під час виявлення замініть вал.
Виміряйте мікрометром зовнішній діаметр Dн корінних шийок.
Фактичний зазор між вкладишами корінних підшипників та корінними шийками колінчастого валу визначають за методикою, викладеною для шатунних вкладишів.
- Номінальний розрахунковий зазор становить 0,026–0,073 мм.
- Граничний зазор – 0,15 мм.
Якщо фактичний розрахунковий зазор менший за граничний, можна знову використовувати вкладки, які були встановлені.
Якщо зазор більший за граничний, замініть на цих шийках вкладиші новими номінальною товщиною (1,824–1,831 мм).
Якщо шийки колінчастого валу зношені та перешліфовані до ремонтного розміру, замініть вкладки ремонтними (збільшеної товщини):
- «0,25» = 1,949–1,956 мм;
- «0,50» = 2,074–2,081 мм;
- «0,75» = 2,199–2,206 мм;
- «1,0» = 2,324–2,331 мм.
Номінальний діаметр корінних шийок 50,799–50,819 мм. Шийки шліфують, якщо на них є вибоїни та ризики або зношування (або овальність) становить більше 0,03 мм, зменшуючи діаметр з кроком 0,25 мм так, щоб отримати (залежно від ступеня зношування) наступні значення:
- «0,25» = 50,549–50,569 мм;
- «0,50» = 50,299–50,319 мм;
- «0,75» = 50,049–50,069 мм;
- «1,0» = 49,799-49,819 мм. Позначення «0,25» та ін. вказують, наскільки зменшується діаметр шийок колінчастого валу після шліфування.
Відповідне тавро ставлять на першій щоці колінчастого валу, наприклад, До 0,75; Ш 0,50.
Встановіть вал крайніми корінними шийками на призми та перевірте індикатором:
- – осьове биття інших корінних шийок (не більше 0,03 мм);
- – осьове биття посадкових поверхонь під зірочку та підшипник первинного валу коробки передач (не більше 0,04 мм);
- – усунення осей шатунних шийок від номінальної площини, що проходить через осі шатунних та корінних шийок (не більше ±0,35 мм);
- – торцеве биття фланця на діаметрі 68 мм (не більше 0,025 мм).
Перевірка биття в гаражних умовах практично нездійсненна, тому проводьте її в майстернях, що мають спеціальне обладнання.
Огляньте заглушки каналів системи мастила.
Перевірте надійність посадки викруткою, не докладаючи значних зусиль. Якщо заглушки встановлені ненадійно, замініть їх.
Заглушки встановіть на герметик УГ-6 і зачеканьте у трьох місцях.
Не рекомендуємо самостійно розкривати заглушки для очищення каналів, яка, безумовно, корисна.
Зверніться до майстерень з спеціальним обладнанням вання, або промийте канали, не розкриваючи заглушки, для чого залийте в радіальні канали (показані стрілками) бензин, заглушивши їх з одного боку дерев'яними пробками.
Витримайте не менше 20 хв і промийте канали бензином, впорскуючи його гумовою грушею.
Дерев'яні заглушки зніміть після промивання з'єднувальних каналів (показані пунктиром).
За необхідності повторюйте промивання, перш ніж витікати чистий бензин.