Vor dem Zusammenbau des Motors müssen alle Teile von Kohlenstoff- und Harzablagerungen befreit werden
Es ist nicht möglich, Teile aus Aluminiumlegierungen (Zylinderblock und -kopf, Kolben usw.) in alkalischen Lösungen zu waschen, da diese Lösungen Aluminium angreifen.
Die folgenden Lösungen werden zum Reinigen von Teilen von Kohlenstoffablagerungen empfohlen:
- Für Aluminiumteile:
- Soda (Na2CO3) - 18,5 g
- Seife (grün oder Wäsche) - 10,0 g
- Flüssigglas - 8,5 g
- Wasser - 1 l
Für Stahlteile:
- Ätznatron (NaOH) - 25,0 g
- Soda (Na2CO3) - 33,0
- Seife (grün oder Wäsche) - 8,5 g
- Flüssigglas - 1,5 g
- Wasser - 1 l
Beachten Sie beim Zusammenbau des Motors die folgenden Bedingungen:
- - Wischen Sie alle Teile vor dem Zusammenbau mit einem sauberen Tuch ab und blasen Sie sie mit Druckluft aus und schmieren Sie alle Reibflächen mit sauberem Öl;
- - Teile vor dem Einbau prüfen (Risse, Absplitterungen, Kerben bei sonstigen Mängeln), Passgenauigkeit der eingepressten Teile prüfen, defekte Teile müssen repariert oder durch neue ersetzt werden;
- - Alle Gewindeteile (Bolzen, Stopfen, Fittings), wenn sie während des Reparaturvorgangs herausgedreht oder ersetzt wurden, müssen auf ein mit natürlichem Trockenöl verdünntes Waschmittel oder Tünche gelegt werden.
Alle dauerhaften Verbindungen, wie Zylinderblockstopfen etc., müssen auf Nitrolack gelegt werden.
Folgendes darf nicht auf dem Motor installiert werden:
- - Splinte, Splinte und Sicherungsbleche, gebraucht;
- - Federscheiben, die an Elastizität verloren haben;
- - beschädigte Dichtungen;
- - Teile mit mehr als zwei verstopften oder gebrochenen Gewinden am Gewinde;
- - Bolzen und Stehbolzen mit verlängerten Gewinden; Schrauben und Muttern mit abgenutzten Kanten.
Schrauben und Muttern müssen ordnungsgemäß gesichert sein (Splinte, Splintdraht, Feder- und Spezialscheiben und Sicherungsmuttern).
Bauen Sie den Motor in der folgenden Reihenfolge zusammen:
- - Reinigen Sie alle Kontaktflächen des Zylinderblocks von festsitzenden und während der Demontage zerrissenen Dichtungen;
- - Den Zylinderblock auf dem Ständer befestigen, den Ölkanalstopfen vom hinteren Ende abschrauben und alle Ölkanäle mit Druckluft ausblasen.
Setzen Sie den Korken wieder ein;
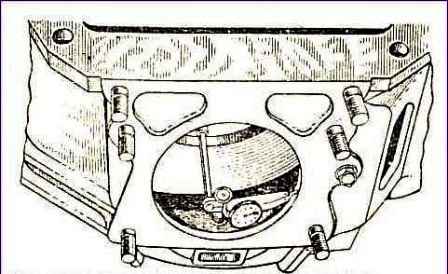
- - Wenn das Kupplungsgehäuse ausgetauscht werden muss oder nach der Reparatur am Zylinderblock installiert wird, müssen zuerst zwei Passstifte aus dem Block entfernt und dann das Kurbelgehäuse mit sechs Schrauben am Zylinderblock befestigt werden.
Eine Kurbelwelle ist im Zylinderblock an den äußeren Lagern installiert, an deren Flansch das Anzeigegestell befestigt ist.
Prüfen Sie durch Drehen der Kurbelwelle den Rundlauf der Bohrungen für die Zentrierschulter des Getriebes sowie die Rechtwinkligkeit des hinteren Endes des Kupplungsgehäuses zur Achse der Kurbelwelle, wie in Abb. 1 und Abb. 2.
Der Rundlauf des Kurbelgehäuses und der Stirnflächen sollte 0,08 mm nicht überschreiten.
Wenn der Schlag der Bohrung den angegebenen Wert überschreitet, sollten Sie die Schrauben lösen, mit denen das Kurbelgehäuse am Zylinderblock befestigt ist, und mit leichten Schlägen auf den Kurbelgehäuseflansch die korrekte Montage erreichen;
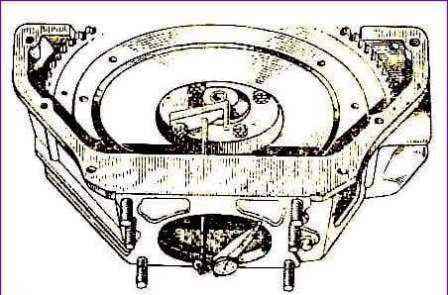
- - Nach dem Anziehen der Schrauben werden die Bohrungen für die Passstifte im Kupplungsgehäuse und Zylinderblock auf das Reparaturmaß aufgeweitet.
Der Durchmesser des Lochs sollte so sein, dass keine Schwärze in den erweiterten Löchern verbleibt.
Danach werden Stifte in die Löcher gedrückt, deren Durchmesser 0,015-0,051 mm größer ist als die Größe der Löcher;
- - das Schlagen des Kurbelgehäuseendes wird durch Schaben beseitigt.
Es ist zu beachten, dass bei der Überprüfung der oben beschriebenen Punkte unverschlissene Kurbelwellen und Laufbuchsen verwendet werden müssen.
Verschlissene Teile führen zu falschen Ergebnissen;
- - Kurbelwelle ausbauen;
- - Ersetzen Sie (falls erforderlich) Zylinderlaufbuchsen wie folgt durch neue:
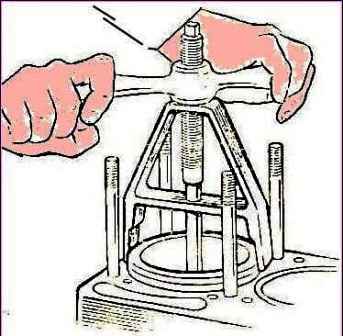
- - Entfernen Sie die alte Hülse mit einem Abzieher (Abb. 3) vom Block;
- - gründlich reinigen Auflageflächen und Dichtflächen an der Laufbuchse und im Zylinderblock vor Zunder und Korrosion bewahren;
- - Setzen Sie eine neue oder reparierte Muffe mit aufgesetzter roter Kupferdichtung ein.
Die Hülse sollte ohne Kraftaufwand frei in den Zylinderblock eingeführt werden;
- - Fixieren Sie die Hülse mit dem Halter vor dem Herausfallen.
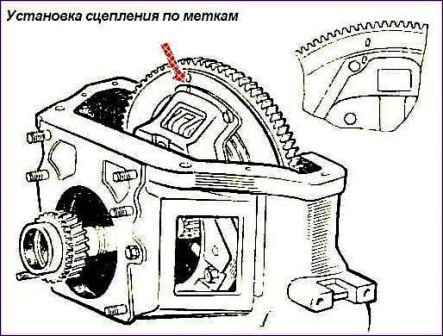
Wenn defekte oder verschlissene Buchsen durch neue oder reparierte ersetzt werden, ist ihre Position im Zylinderblock nicht ausgerichtet.
In anderen Fällen ist es vor dem Entfernen der Laufbuchsen aus dem Zylinderblock erforderlich, sie mit Seriennummern zu markieren (Zählung von Wasserpumpe und Getriebe) und auch ihre Position im Zylinderblock zu markieren, um ihre Installation sicherzustellen in der vorherigen Position während der Montage.
Bei Verwendung - verschlissener Zylinderlaufbuchsen, sowie jedes Mal, wenn neue Kolbenringe in verschlissene Laufbuchsen eingebaut werden, ist es notwendig, auf der Maschine oder mit einem Schaber einen unverschlissenen Riemen über den oberen Verdichtungsring zu bohren.
Es ist notwendig, das Metall bündig mit dem verschlissenen Teil der Hülse zu entfernen;
- - schneiden Sie zwei Packungen des Öldichtrings des hinteren Hauptlagers der Kurbelwelle (jeweils 120 mm lang) von der Schnur ab und legen Sie sie in den Öldichtungsblock und die Halterung;
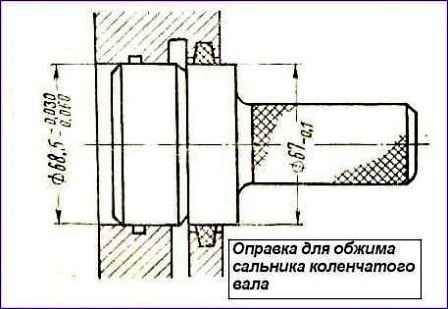
Bauen Sie die Kurbelwelle wieder zusammen:
- - Schrauben Sie alle Stopfen der Schmutzfänger der Pleuelzapfen heraus und entfernen Sie diese von Ablagerungen.
- Ölkanäle und Hohlräume der Schmutzfänger mit Druckluft spülen und ausblasen, Stopfen einschrauben und verschließen;
- - Überprüfen Sie den Zustand der Arbeitsflächen der Welle. Kerben, Einkerbungen und andere äußere Mängel sind nicht erlaubt;
- - mit Feuerfestfett 1-13 schmieren und das Getriebeeingangswellenlager in das hintere Ende der Kurbelwelle drücken;
- - Schrauben Sie das Schwungrad mit einem Drehmomentschlüssel an die Kurbelwelle des Motors (Anzugsmoment der Mutter 7,6-8,3 kgm); Splint;
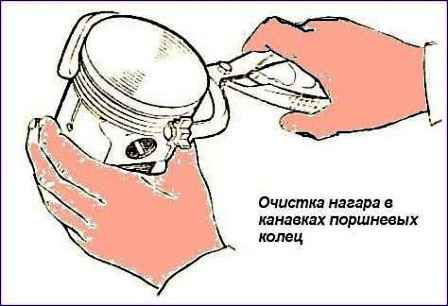
- - Schrauben Sie die Kupplungsdruckplattenbaugruppe mit dem Gehäuse an das Schwungrad, nachdem Sie zuvor die angetriebene Scheibe mit einem Dorn (Sie können die Antriebswelle des Getriebes verwenden) durch das Loch im Lager am hinteren Ende der Kurbelwelle zentriert haben .
Die auf dem Gehäuse der Druckplatte und des Schwungrads eingeprägten „O“-Markierungen in der Nähe eines der Löcher für die Befestigungsschrauben des Gehäuses (Abb. 4) müssen fluchten.
Stellen Sie die Kupplungsscheibe so ein, dass der Dämpfer zum Schwungrad zeigt.
Kurbelwelle, Schwungrad und Kupplung werden als Baugruppe ausgewuchtet, daher sollte beim Austausch eines dieser Teile ein dynamisches Auswuchten durchgeführt werden.
Die Unwucht sollte 70 Gcm nicht überschreiten.
Beim Auswuchten wird überschüssiges Gewicht von der schweren Seite entfernt, indem das Schwungradmetall mit einem Radius von 151 mm mit einem 10-mm-Bohrer bis zu einer Tiefe von nicht mehr als 12 mm gebohrt wird.
Der Abstand zwischen den Bohrzentren muss mindestens 14 mm betragen.
Node Balancing sollte nicht gestartet werden, wenn das anfängliche Ungleichgewicht größer als 180 Gcm ist. In diesem Fall ist es notwendig, die Baugruppe zu demontieren und das Gleichgewicht jedes Teils separat zu prüfen;
- - auf den ersten Hauptlagerzapfen der Kurbelwelle die hintere Anlaufscheibe mit der Kugelseite zur Wellenwange aufsetzen;
- - Crimpen Sie den hinteren Wellendichtring. Dazu einen Dorn in die Bohrung des hinteren Hauptlagers stecken (Abb. 5), den Stopfbuchshalter einbauen und die Muttern von Lager und Halter anziehen;
wischen Sie die Buchsen der Hauptlager in ihrem Bett mit einem sauberen Tuch ab; legen Sie die Buchsen in das Bett;
- - Schmieren Sie die Hauptlagerschalen und Kurbelwellenzapfen mit sauberem Motoröl und setzen Sie die Kurbelwelle in den Zylinderblock ein;
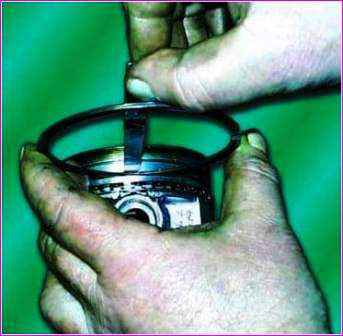
- - Setzen Sie die Hauptlagerdeckel so auf die Stehbolzen des Zylinderblocks, dass sich die Verriegelungslaschen an der oberen und unteren Schale jeder Abdeckung auf der gleichen Seite befinden und die auf den Abdeckungen eingestanzten Nummern mit den auf dem Zylinder eingestanzten Bettnummern übereinstimmen Block in der Nähe der Stollen.
Beim Einbau des vorderen Lagerdeckels den hinteren Kurbelwellen-Axiallagerscheiben müssen in die Nut des Deckels passen.
Das Ende des vorderen Lagerdeckels muss in derselben Ebene liegen wie das Ende des Zylinderblocks;
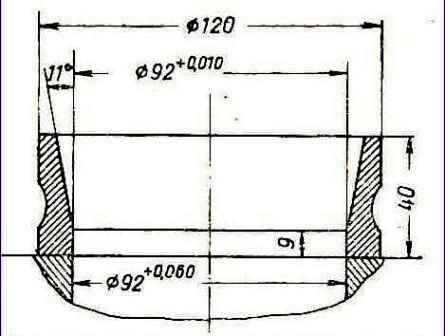
- - die Hauptlagerdeckel mit einem leichten Schlag mit einem Gummihammer anbringen; die Abdeckungen müssen in die Rillen der Betten des Blocks passen;
- - Schrauben Sie die Muttern zur Befestigung der Abdeckungen auf und ziehen Sie sie gleichmäßig an, nachdem Sie die Sicherungsplatte angebracht haben.
Das endgültige Anziehen muss mit einem Drehmomentschlüssel erfolgen (Drehmoment 10-11 kGm), die Antennen der Verriegelungsplatte biegen;
- - Gummidichtungen in die Nuten des Stopfbüchsenhalters einbauen und ihre aus der Nut herausragende Seitenfläche mit Seifenlauge bestreichen.
Den Stopfbüchsenhalter anbringen und die Muttern festziehen;
- - Drehen Sie die Kurbelwelle, die sich mit geringem Kraftaufwand frei drehen sollte.
Sie können die Kurbelwelle mit dem Schwungrad oder mit einer Vorrichtung drehen, die aus einer Getriebeeingangswelle mit einem daran angeschweißten Vierkantschlüssel oder einem Griff mit Vierkantloch besteht.
Die Vorrichtung kann auch zum Zentrieren beim Einstellen der Mitnehmer- und Druckplatten der Kupplung verwendet werden;
- die vordere Unterlegscheibe des Axiallagers mit der Babbitt-Seite auf die Welle legen, sodass die in den Zylinderblock und die Abdeckung eingepressten Stifte in die Nuten der Unterlegscheibe passen;
- - die stählerne Druckscheibe der Kurbelwelle mit ihrer unverschlissenen Oberfläche gegen die geriffelte Oberfläche der vorderen Drucklagerscheibe legen;
- - Kurbelwellenrad bis zum Anschlag drücken und Axialspiel der Kurbelwelle prüfen.
Die Prüfung wird wie folgt durchgeführt: Einen Schraubendreher (Knopf, Hammerstiel etc.) zwischen die Kurbel der ersten Welle und die Stirnwand des Zylinderblocks stecken und als Hebel die Welle nach hinten drücken Ende des Motors.
Mit einer Fühlerlehre den Abstand zwischen der Stirnfläche der hinteren Scheibe des Axiallagers und der Schulterebene des ersten Hauptzapfens ermitteln.
Der Abstand sollte zwischen 0,075 und 0,175 mm liegen;
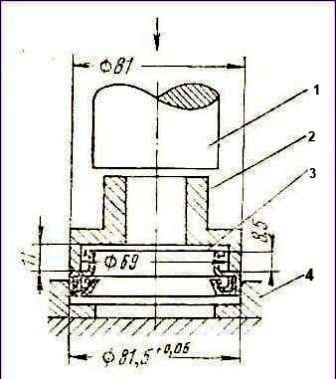
- - Unterbaugruppe der Pleuel- und Kolbengruppe:
Säubern Sie die Kolbenböden und Kolbenringnuten von Kohlenstoffablagerungen, wie in Abb. 6;
- - Beim Austausch eines Kolbens, Kolbenbolzens oder einer Pleuelstange müssen Sie:
- - die Sicherungsringe der Kolbenbolzen mit einer Zange entfernen;
- - Kolbenbolzen am Werkzeug entfernen (Kolbenringe müssen vorher entfernt werden);
- - Neue Kolben entsprechend den Hülsen mit einem Spalt von 0,012-0,024 mm aufnehmen.
Die Auswahl wird überprüft, indem mit einem Federstahlband ein Prüfband zwischen Kolben und Zylinder gezogen wird.
Die Sonde befindet sich in einer Ebene senkrecht zur Achse des Kolbenbolzens.
Der Kolben muss ohne Kolbenringe sein. Die Zugkraft bei normaler Raumtemperatur (+20°C) sollte im Bereich von 3,5-4,5 kg liegen.
Bandabmessungen: Dicke -0,05 mm, Breite - 13 mm, Länge - 250 mm;
Maßgruppen von Kolben und Hülsen |
||
---|---|---|
Gruppe |
Durchmesser, mm |
|
Kolben |
Fälle |
|
A |
92.000–91.988 |
92.036–92.024 |
Б |
92.012–92.000 |
92.048–92.036 |
В |
92.024–92.012 |
92.060–92.048 |
Г |
92.036–92.024 |
92.072–92.060 |
Д |
92.043–92.036 |
92.084–92.072 |
- - Heben Sie den Kolbenbolzen an der Pleuelstange an, so dass er sich bei normaler Raumtemperatur leichtgängig in der Bohrung des oberen Kopfes unter einer leichten Anstrengung des Daumens bewegt.
Kolbenbolzen, sollte leicht eingeölt werden.
Die Farbe der Stiftmarkierung muss mit der Farbe der Markierung auf den Kolbennaben übereinstimmen;
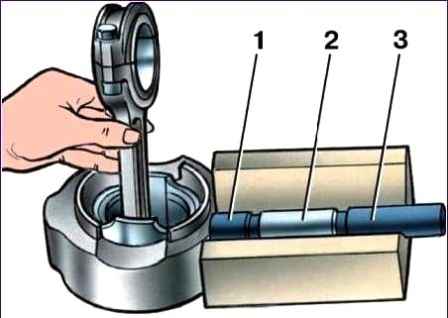
- - eine Unterbaugruppe aus Pleuel und Kolbengruppe auf der Vorrichtung herstellen (Abb. 7).
Vor dem Einpressen des Kolbenbolzens muss der Kolben in heißem Wasser auf eine Temperatur von 70 °C erhitzt werden; Das Drücken eines Fingers gegen einen kalten Kolben kann die Oberfläche der Löcher in den Kolbennaben sowie den Kolben selbst beschädigen.
Setzen Sie die Sicherungsringe des Kolbenbolzens in die Ringnuten der Kolbennaben ein;
- - Kolbenringe nach Zylinder auswählen; Lücke; am Stoß des Rings mit einer Fühlerlehre gemessen, sollte 0,3 - 0,5 mm betragen.
Bei verschlissenen Zylindern sollte das kleinste Spiel 0,3 mm betragen;
- - Mit einer Fühlerlehre das seitliche Spiel zwischen dem Ring und der Wand der Kolbennut prüfen (Abb. 8).
Überprüfen Sie den Umfang des Kolbens an mehreren Stellen.
Der Wert des Seitenspiels sollte zwischen 0,050 und 0,082 mm für den oberen Kompressionsring und zwischen 0,035 und 0,067 mm für die unteren Kompressions- und Ölabstreifringe liegen;
- - Setzen Sie die Kolbenringe mit dem Werkzeug auf den Kolben. Kompressionsringe werden mit einer inneren Fase zum Kolbenboden platziert, wie in Abb. 12, die Ringe in den Nuten sollten sich frei bewegen;
- - Wischen Sie die Betten der Pleuel und ihre Kappen mit einer Serviette ab, wischen Sie die Auskleidungen ab und setzen Sie sie ein;
- - die Kurbelwelle so drehen, dass die Kurbeln des ersten und vierten Zylinders die Position einnehmen, die dem unteren Totpunkt entspricht;
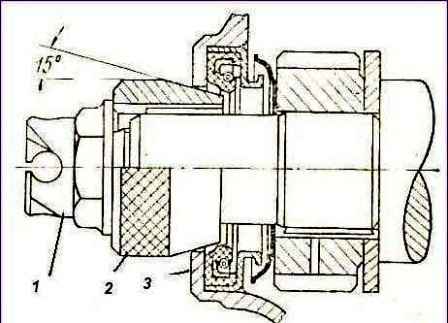
- - Schmieren Sie die Laufbuchsen, den Kolben, den Pleuelhals der Welle und die Hülse des ersten Zylinders mit sauberem Motoröl, spreizen Sie die Gelenke der Kolbenringe in einem Winkel von 120 ° zueinander und setzen Sie schützende Messingspitzen auf die Pleuelschrauben, die Ringe durch Bördeln oder mit einem Konusring zusammenpressen ( Bild 9), den Kolben in den Zylinder einsetzen.
Vor dem Einbau des Kolbens sollten Sie sich noch einmal vergewissern, dass die auf der Pleuelstange und deren Deckel eingestanzten Nummern mit der Seriennummer des Zylinders übereinstimmen, die korrekte Position des Kolbens und der Pleuelstange im Zylinder überprüfen; die Markierung auf dem Kolben „Back“ sollte zum Schwungrad zeigen und das Loch im unteren Kopf der Pleuelstange sollte in entgegengesetzter Richtung zur Nockenwelle sein;
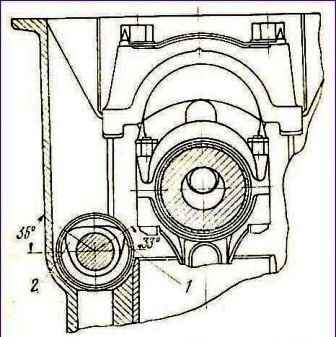
- - Pleuel am unteren Kopf zum Pleuelhals ziehen, Messingspitzen von den Schrauben entfernen, Pleueldeckel so aufsetzen, dass die auf dem Deckel und dem Pleuel eingestanzten Zahlen in die gleiche Richtung zeigen.
Die Muttern mit einem Drehmomentschlüssel anziehen (Drehmoment 6,8-4,5 kGm) und mit einer aus Stahlblech gestanzten Kontermutter kontern. Anzugsdrehmoment der Kontermutter 0,3-0,5 kgm;
- - Setzen Sie in der gleichen Reihenfolge den Kolben des vierten Zylinders ein, drehen Sie dann die Kurbelwelle um 180 ° und setzen Sie die Kolben des zweiten und dritten Zylinders ein.
Drehen Sie die Kurbelwelle mehrmals, die sich leicht und ohne Kraftaufwand drehen sollte;
- - Unterbaugruppe der Nockenwelle:
- - am vorderen Ende der Nockenwelle eine Distanzhülse und einen Druckflansch anbringen;
- - Drücken Sie das Steuerrad auf die Welle und befestigen Sie es mit einer Schraube und einer Unterlegscheibe;
- - mit einer Fühlerlehre, die zwischen dem Druckflansch der Nockenwelle und der Nabe der Nockenwelle eingesetzt wird, das Axialspiel der Nockenwelle prüfen, das innerhalb von 0,1-0,2 mm liegen sollte;
- - Reinigen Sie das Rohr zum Schmieren der Zahnräder und schrauben Sie es mit einer Schraube und einer Klemme an den Block;
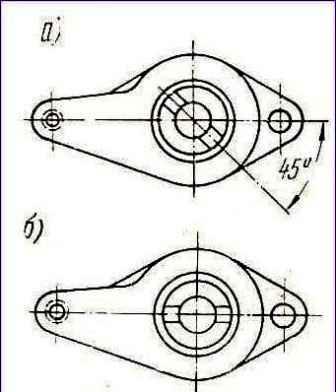
- - Setzen Sie den zusammengebauten Verteilerraum in das Loch des Blocks ein, nachdem Sie zuvor seine Stützzapfen mit Motoröl geschmiert haben.
Wann Zahnräder kämmen, muss der Zahn des Kurbelwellenrads mit der „O“-Markierung an den Rillen der Zahntäler des Nockenwellenrads anliegen (siehe Abb. 17).
Das Seitenspiel im Eingriff sollte im Bereich von 0,03-0,08 mm liegen. Wählen Sie bei einem größeren oder kleineren Abstand ein anderes Paar;
- - Befestigen Sie den Druckflansch durch die Löcher im Nockenwellenzahnrad mit zwei Schrauben mit Federscheiben am Block;
- - setzen Sie den Ölabweiser auf den Hals des vorderen Endes der Kurbelwelle mit der konvexen Seite zum Zahnrad;
- - Prüfen Sie die Eignung des in den Deckel der Steuerräder eingepressten Wellendichtrings für den weiteren Betrieb.
Wenn die Öldichtung verschlissene Lippendichtungen aufweist oder die in die Öldichtung eingesetzte Nabe der Kurbelwellenriemenscheibe lose greift, ersetzen Sie sie durch eine neue.
Es wird empfohlen, die Stopfbuchse mit einem Dorn auf einer Presse in den Deckel zu pressen, wie in Abb. 10;
- setzen Sie die Dichtung und die Abdeckung der Steuerräder auf die Stehbolzen;
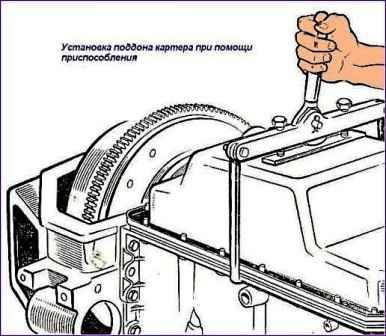
- - Zentrieren Sie die Abdeckung auf dem vorderen Ende der Kurbelwelle mit einem Dorn (Abb. 11) und ziehen Sie alle Schrauben und Muttern der Abdeckung fest.
Wenn kein Zentrierdorn vorhanden ist, kann die Montage des Deckels auf der Nabe der Kurbelwellenriemenscheibe erfolgen.
Die Nabe muss so auf die Kurbelwelle aufgepresst werden, dass ihr Ende 5 mm tief in die Bohrung im Deckel eindringt.
Dann den Deckel mit Muttern fixieren, dabei am Umfang zwischen der Nabe und der Öffnung des Deckels den gleichen Abstand einhalten.
Richten Sie den Spalt mit leichten Schlägen eines Holz- oder Gummihammers auf die Abdeckung aus. Danach die Abdeckung endgültig befestigen;
- - Zentrierdorn entfernen und auf die Nabe der Kurbelwellenriemenscheibe drücken;
- - Wickeln Sie eine Ratsche in die Kurbelwelle, nachdem Sie eine Federscheibe darauf gesetzt haben.
Drehen Sie die Kurbelwelle mit der Ratsche und prüfen Sie, ob der Deflektor die Abdeckung der Steuerräder berührt, weil der Deflektor verbogen ist oder lose auf der Nabe sitzt;
- - Kurbelwellenriemenscheibe an der Nabe festschrauben;
- - die Ölpumpenbaugruppe mit dem Ölbehälter einbauen;
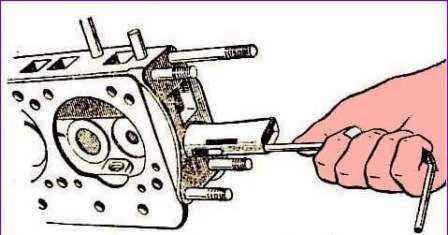
- - Installieren Sie das Unterbrecher-Verteiler-Laufwerk;
- - Drehen Sie die Kurbelwelle, um die Markierung c auszurichten. m.t. am Kranz der Kurbelwellenriemenscheibe mit einem Zeiger auf dem Steuerraddeckel (siehe Abb. 14).
Die Nocken der Nockenwelle, die die Ventile des ersten Zylinders betätigen, müssen mit ihren Spitzen in die entgegengesetzte Richtung von den Stößeln (in Richtung der Ölwanne) gerichtet sein und symmetrisch angeordnet sein, wie in Abb. 12;
- - Axialspiel der Antriebswelle mit einer zwischen Antriebsgehäuse und Getriebe eingesetzten Fühlerlehre prüfen.
Der Abstand sollte zwischen 0,15 und 0,40 mm liegen;
Legen Sie eine Dichtung auf die Bolzen des Leistungsschalter-Verteiler-Antriebs;
- - drehen Sie die Antriebsrolle in die in Abb. 15, a, und setzen Sie den Antrieb in die Buchse des Zylinderblocks.
Beim Einsetzen des Antriebs in den Sitz muss die Ölpumpenwelle so gedreht werden, dass das Ende der Antriebswelle in das Loch in der Pumpenwelle eintritt,
Bei einem ordnungsgemäß installierten Antrieb sollte der Schlitz in der Wellenhülse parallel zur Motorachse und vom Motor versetzt sein, wie in Abb. 15, b;
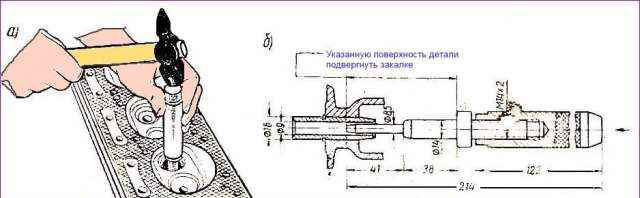
- - Laufwerk reparieren;
- - auf Spiel in den Schrägstirnrädern der Nockenwelle und des Unterbrecher-Verteiler-Antriebs prüfen.
Wenn aus irgendeinem Grund nur ein Schalter-Verteiler-Antrieb vom Motor entfernt wurde, kann er ohne Demontage der Ölwanne eingebaut werden.
Stellen Sie in diesem Fall den Kolben des ersten Zylinders auf c. mt Verdichtungstakt, beim Einbau des Antriebs die Kurbelwelle leicht in die eine oder andere Richtung drehen.
Bei korrekt eingebautem Antrieb, wenn der Kolben des ersten Zylinders auf OT steht. Kompressionshub, der Rotor des Schalter-Verteilers nimmt eine Position gegen den ersten Kontakt ein, der mit der Nummer 1 auf dem Deckel des Schalter-Verteilers gekennzeichnet ist;
- - die Dichtung der Ölwanne auf den Flansch des Zylinderblocks legen;
- - die zusammengesetzte Palette auf den Bolzen montieren, mit dem Werkzeug (Abb. 16) auf den Block drücken und mit Muttern und Unterlegscheiben sichern;
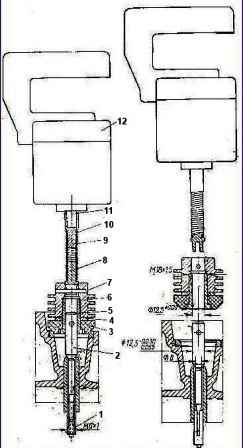
- - den unteren Teil des Kupplungsgehäuses einbauen und verschrauben;
- - Reinigen Sie die Brennkammern des Zylinderkopfs von Kohlenstoffablagerungen, wischen Sie sie ab und blasen Sie sie mit Druckluft aus.
Wenn nötig, reinigen Sie die Löcher im Wasserverteilungsrohr, um es zu entfernen, wie in Abb. 17;
- - Schleifen Sie die Ventile, dazu benötigen Sie:
- - Tragen Sie eine dünne Schicht einer Mischung auf, die aus einem Teil M-20-Mikropulver (GOST 3647-59) und zwei Teilen Industrieöl 20 (Spindel 3) (GOST 1707-51) besteht, auf die geläppte Oberfläche des Ventils Sitz.
Mischung vor Gebrauch gründlich aufrühren;
Setzen Sie eine technologische Feder auf den Ventilschaft, führen Sie das Ventil in die Führungshülse ein. Der Innendurchmesser der Feder sollte ca. 10 mm betragen.
Federkraft ist gering; es sollte das Ventil leicht vom Sitz abheben. Bei leichtem Druck sollte das Ventil auf dem Sitz sitzen;
- - Drücken Sie den Gummisaugnapf auf die obere Ebene des Ventilkopfs. Saugnapf- und Ventiloberflächen müssen trocken und absolut sauber sein;
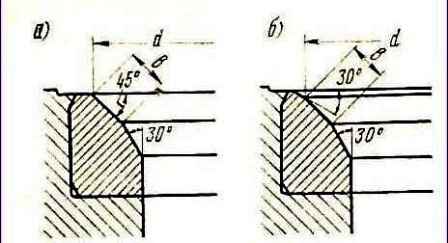
- - Durch abwechselndes Drehen des Saugnapfgriffs in die eine oder andere Richtung und gleichzeitiges Auf- und Abbewegen des Ventils erreichen Sie eine gleichmäßige matte Fase an den Arbeitsflächen von Sitz und Kopf über den gesamten Umfang.
Bevor Sie mit dem Läppen beginnen, prüfen Sie, ob sich der Ventilkopf verzogen und Ventil und Sitz verbrannt sind.
Wenn diese Mängel vorhanden sind, ist es unmöglich, die Dichtheit des Ventils mit einem Läppen wiederherzustellen, und der Sitz muss zuerst geschliffen und das beschädigte Ventil durch ein neues ersetzt werden.
Beträgt der Spalt zwischen Ventil und Hülse mehr als 0,25 mm, kann die Dichtigkeit ebenfalls nicht wiederhergestellt werden, in diesem Fall sollten Ventil und Hülse durch neue ersetzt werden.
Ventile (für Ersatzteile) werden in Standardgröße hergestellt, und Führungsbuchsen - mit einem um 0,3 mm reduzierten Innendurchmesser (um sie nach dem Einpressen in den Zylinderkopf auf die endgültige Größe einzusetzen).
Die verschlissene Führungsbuchse wird mit einem Stempel ausgepresst (Abb. 18).
Ventilsitze werden durch Fräsen mit einem Hartmetallsenker entfernt.
Reparatursitze haben einen um 0,25 mm größeren Außendurchmesser als der Standard, daher sind die Sitzbuchsen gebohrt auf:
- für den Einlassventilsitz - 47,25 + 0,027 mm und für den Auslass - 38,75 + 0,027 mm.
Die Ventilsitze und Führungsbuchsen müssen vor der Montage in Kohlendioxid (Trockeneis) gekühlt und der Zylinderkopf auf eine Temperatur von 160-175 °C erwärmt werden.
Bei der Montage müssen die Sitze und die Hülse frei oder mit leichtem Druck in die Zylinderkopfsitze eingeführt werden.
Nach dem Einbau des Sitzes wird das Metall des Zylinderkopfes mit einem flachen Dorn mit einem Durchmesser von 49 bzw. 41 mm um den Sitz gerollt, zentriert auf das Loch im Sitz.
Die neue Buchse wird mit einem Durchschlag von der Seite der Kipphebel eingepresst.
Die Hülse sollte nach dem Pressen 22 mm über die Zylinderkopfebene hinausragen.
Nach dem Pressen das Buchsenloch auf einen Durchmesser von 9 + 0,022 mm aufweiten und die Fasen der Sitze schleifen, wobei das Loch in der Buchse zentriert wird.
Zum Schleifen der Sitze können Sie das in Abb. 19.
Der Spreizdorn wird in die bearbeitete Bohrung der Hülse eingebaut, der Dornschaft dient als Achse für die Schleifscheibe mit einer Fase im Winkel von 45°.
Die Schleifscheibe wird von einem kleinen Elektromotor angetrieben.
Achten Sie beim Schleifen darauf, dass die Fase am Ventilsitz innerhalb von 0,03 mm des Gesamtanzeigewerts konzentrisch mit dem Loch in der Hülse ist.
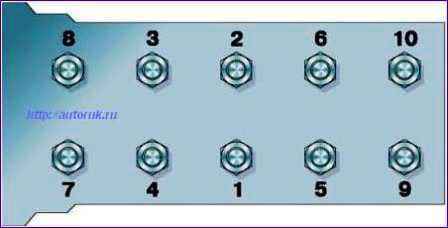
Fasen werden in einem Winkel von 45° geschliffen. Der Außendurchmesser „d“ (Abb. 18) der Fase muss am Einlassventilsitz 46 mm und am Auslass 35 mm betragen.
Die Breite der Fase „c“ sollte am Einlassventilsitz 1,8-2,3 mm betragen, bei Teilung - 2,3-2,5 mm.
Die Fasenbreite erhält man durch Schleifen der Sitzbohrung in einem Winkel von 30°, wie in Abb. 80, u.
Beim Schleifen verschlissener Sitze ist der Außendurchmesser der Fase größer als die oben genannten Maße.
In diesem Fall wird der Außendurchmesser der Fase auf den erforderlichen Wert eingestellt, indem die Stirnfläche des Sitzes in einem Winkel von 30° geschliffen wird, wie in Abb. 18, B.
Nach dem Schleifen der Sitze und Läppen der Ventile alle Gaskanäle gründlich reinigen und mit Druckluft ausblasen, damit kein Schleifstaub zurückbleibt.
Die Ventilschäfte werden vor der Montage mit einer Mischung geschmiert, die aus sieben Teilen eines Öl-Kolloid-Graphit-Präparats (GOST 5262-50) und drei Teilen Luftfahrtöl MS-20 besteht;
- - Setzen Sie die Ventile gemäß den Markierungen in die Buchsen ein und montieren Sie sie mit den Federn.
- - Vergewissern Sie sich, dass die Vorsprünge der Cracker in die Ringnut des Ventilschafts eingedrungen sind;
- - Setzen Sie eine Dichtung auf die Zylinderkopfbolzen, montieren Sie den Kopf und befestigen Sie ihn mit Muttern und Unterlegscheiben.
- - Ziehen Sie die Muttern mit einem Drehmomentschlüssel mit einem Drehmoment von 7,3-7,8 kGm an, indem Sie die in Abb. 19;
- - Reinigen Sie mit Draht und blasen Sie die Löcher in den Kipphebeln, in der Achse der Kipphebel und Einstellschrauben, das Loch in der hinteren Säule der Achse der Kipphebel und im Zylinderkopf mit Druckluft aus.
Überprüfen Sie den festen Sitz der Buchsen der Kipphebel.
Im Falle einer lockeren Passung während des Betriebs kann sich die Buchse bewegen und die Schmierbohrung der Ventilstößelstange blockieren.
Solche Buchsen müssen ersetzt werden;
- - Untermontage der Wippenachse durchführen. Schmieren Sie vor dem Einbau jedes Kipphebels dessen Buchse mit Motoröl.
Maßgruppen von Drückern
Äußere Durchmesser, mm |
Markierung |
Durchmesser, mm |
Farbe Markierung |
Lücke, mm |
---|---|---|---|---|
25-0,06-0,022 |
1 |
25+0,023+0,011 |
Blau |
0,038 0,019 |
25-0,015-0,022 |
2 |
25+0,011 |
Gelb |
0,033 0,015 |
Die Kipphebel und Achsschenkel werden so auf der Achse montiert, dass der Versatz der Löcher für die Befestigungsbolzen in den Achsschenkeln zu den Einstellschrauben der Kipphebel zeigt.
Die vierte (hintere) Zahnstange muss auf der unteren Ebene ein Loch für den Öldurchgang haben;
- - Stecken Sie die Drücker gemäß den Beschriftungen in die Buchsen. Schmieren Sie die Stößel und Löcher im Block mit Motoröl;
- - Führen Sie die Stangenbaugruppe mit Spitzen in die Löcher im Zylinderkopf ein;
- - Installieren Sie die zusammengebaute Kipphebelachse auf den Stehbolzen und sichern Sie sie mit Muttern und Unterlegscheiben.
Stellschrauben sollten mit ihrem kugelförmigen Teil auf der Kugel der oberen Stangenspitze aufliegen;
- - Stellen Sie die Lücken zwischen dem Ende der Stange der mittleren Ventile und der Spitze des Kipphebels auf 0,35-0,40 mm und die äußersten Ventile (Auslass des ersten und vierten Zylinders) auf 0,30-0,35 mm ein.
Dies muss wie im Artikel "Einstellen des Ventils durchgeführt werden Abstände des ZMZ-402-Motors ";
- - Setzen Sie die Dichtung und die Kipphebelabdeckung ein und befestigen Sie sie mit Schrauben und Unterlegscheiben;
- - die Kupplungsausrückbaugruppe mit dem Lager schmieren und auf die vordere Abdeckung des Getriebes setzen und die Ausrückfeder befestigen;
- - Getriebe einsetzen und befestigen;
- - Kupplungsausrückgabel einsetzen;
- - Motorteile und -baugruppen in umgekehrter Reihenfolge anordnen.