Aus- und Einbau des Zylinderkopfes finden Sie im Artikel – Austausch der Zylinderkopfdichtung des VAZ-2126-Motors
Wir schauen uns auch verwandte Artikel an:
Sie benötigen: ein Werkzeug zum Zusammendrücken von Ventilfedern, ein Werkzeug zum Auspressen und einen Dorn zum Auspressen von Ventilschaftdichtungen, Steckschlüssel „8“, „10“, „13“, Schlüssel „19“, „21“ , Sechskant „10“, Schraubendreher, Pinzette.
Entfernen Sie den Zylinderkopf vom Motor
Montieren Sie den Kopf des Blocks mit den Nockenwellen nach oben und legen Sie hölzerne Unterlegscheiben darunter, um die Ventile nicht zu beschädigen.
Lösen Sie die drei Muttern mit Innensechskant 13, mit denen die linke Halterung der Antriebseinheit befestigt ist
Entfernen Sie die Stütze
Entfernen Sie mit einem 10er-Schraubenschlüssel die beiden Schrauben, mit denen die Kraftstoffrohrhalterung befestigt ist
Halterung entfernen
Lösen Sie die beiden Schrauben des Phasensensors mit einem 10er-Schraubenschlüssel
Entfernen Sie den Phasensensor
Schrauben Sie den 21 Öldruck-Warnlichtsensor mit einem Schlüssel 21 vom Nockenwellenlagergehäuse ab
Schrauben Sie den Kühlmitteltemperatursensor mit einem 19er-Schlüssel vom Thermostat ab
Schrauben Sie den Schlüssel zum Sensor 21 der Kühlmitteltemperaturanzeige vom hinteren Ende des Blockkopfes ab
Lösen Sie die beiden Muttern, mit denen der Thermostat befestigt ist, mit einem 13er Schraubenschlüssel
Thermostat entfernen
Entfernen Sie die Dichtung darunter
Drehen Sie die Zündkerzen mit einem Kerzenschlüssel heraus, um sie nicht versehentlich zu beschädigen
Drehen Sie mit einem Innensechskant 8 zwanzig Schrauben heraus, mit denen das Nockenwellenlagergehäuse befestigt ist
Entfernen Sie das Gehäuse
Entfernen Sie die Nockenwellen aus den Zylinderkopflagern und entfernen Sie die Öldichtungen von ihren vorderen Enden
Entfernen Sie die Stopfen vom hinteren Ende des Blockkopfes
Entfernen Sie die Ventilstößel aus den Zylinderkopflöchern
Reinigen Sie die Brennräume von Ruß.
Inspizieren Sie den Blockkopf.
Wenn es Risse oder Brandflecken in den Brennkammern aufweist, tauschen Sie den Kopf aus.
Entfernen Sie Grate und Kerben auf der Blockkopfebene.
Überprüfen Sie die Ebenheit der Oberfläche neben dem Zylinderblock.
Legen Sie dazu das Lineal mit einer Kante zuerst in der Mitte entlang, dann diagonal auf die Kopfoberfläche und messen Sie mit einer Fühlerlehre den Abstand zwischen der Kopfoberfläche und dem Lineal.
Wenn der Spalt größer als 0,1 mm ist, kann die Passfläche geschliffen werden.
Prüfen Sie auf ähnliche Weise die Ebenheit der Passflächen des Blockkopfes unter dem Ansaugkrümmer
Prüfen Sie die Ebenheit unter dem Kollektor. Die Ebenheit dieser Oberflächen sollte 0,1 mm nicht überschreiten
Um den festen Sitz des Blockkopfes zu überprüfen, verschließen Sie das Loch im Kopf unter der Thermostatbuchse.
Dies kann beispielsweise dadurch erreicht werden, dass Sie eine leere Unterlage aus dickem Karton unter die Steckdose legen und die Befestigungsmuttern festziehen.
Bringen Sie den Kühlmitteltemperatursensor wieder ein, falls er entfernt wurde.
Gießen Sie Kerosin in die Kanäle des Wassermantels.
Wenn der Kerosinspiegel während der Einwirkung von 15 bis 20 Minuten sinkt, weist der Kopf Risse auf und er muss ersetzt werden.
Vergessen Sie nach der Überprüfung nicht, die Kartonauskleidung zu entfernen und die Stopfen zu entfernen.
Überprüfen Sie den Zustand der Lagerflächen für die Nockenwellenzapfen am Blockkopf und Lagergehäuse.
Wenn mindestens einer von ihnen Anzeichen von Abnutzung, Abnutzung oder tiefe Kratzer aufweist, tauschen Sie den Kopf und das Lagergehäuse aus
Spülen Sie die Ölkanäle.
Verschließen Sie dazu den vertikalen Ölkanal von der Seite des Brennraums (der Kanal befindet sich zwischen dem 3. und 4. Zylinder).
Gießen Sie Benzin in den Ölkanal des Blockkopfes.
Benzin in den Kanal des Nockenwellenlagergehäuses gießen und 15–20 Minuten einweichen lassen.
Gießen Sie das Benzin aus, entfernen Sie den Stopfen und spülen Sie abschließend die Kanäle mit einem Blasebalg mit Benzin durch.
Um die Dichtheit der Ventile zu überprüfen, schrauben Sie die Kerzen ein und gießen Sie Kerosin in die Brennkammern.
Wenn nicht innerhalb von 3 Minuten Kerosin aus den Brennkammern in die Kanäle gelangt, sind die Ventile dicht.
Wenn nicht, läppen Sie die Ventile oder tauschen Sie die Ventile aus.
Um die Ventile auszutauschen oder zu schleifen, entfernen Sie die folgenden Teile vom Zylinderkopf: 1 - Ventil; 2 - Frühling; 3 - Teller, 4 - Cracker.
Platzieren Sie einen geeigneten Anschlag unter dem zu entfernenden Ventil.
Montieren Sie den Ventilfederspanner, indem Sie die Schraube des Nockenwellenlagerdeckels in eines der Löcher im Kopf des Blocks schrauben und das Werkzeug an dieser Schraube einhaken.
Ventilfeder mit dem Werkzeug zusammendrücken.
Entfernen Sie die beiden Cracker mit einer Pinzette oder einem magnetischen Schraubendreher von der oberen Federplatte.
Dann entfernen Sie die Halterung.
Wenn die Kraft beim Bewegen des Hebels des Geräts erheblich zunimmt und die Cracker nicht aus der Ventilnut herauskommen, schlagen Sie leicht mit einem Hammer auf die Federplatte, um die Cracker zu lösen.
Entfernen Sie die Federplatte.
Entfernen Sie die Feder
Drücken Sie das Ventil und entfernen Sie es vom Blockkopf
Drücken Sie die Ventilschaftdichtung mit einem Werkzeug oder einer Zange auf die Ventilführung.
Entfernen Sie Kohlenstoffablagerungen mit einem geeigneten Werkzeug vom Ventil. Überprüfen Sie dann das Ventil sorgfältig.
Ersetzen Sie Ventile mit folgenden Mängeln: tiefe Kratzer und Kratzer an der Arbeitsfase 1, Risse, Verformung des Schafts 3, Verformung der Platte 2, Spuren von Durchbrennen.
Flache Risiken und Kratzer an der Arbeitsfase können durch Läppen der Ventile entfernt werden.
Wenn Schäden an der Arbeitsfase der Ventile nicht durch Schleifen beseitigt werden können, können Sie die Fase auf einer Spezialmaschine schleifen.
Überprüfen Sie den Zustand der Ventilsitze.
Die Sitzschrägen müssen frei von Verschleiß, Lochfraß, Korrosion usw. sein.
Ventilsitze können ausgetauscht werden.
Größere Defekte an Ventilsitzen werden durch Schleifen beseitigt.
Sättel können manuell mit einem Fräsersatz geschliffen werden.
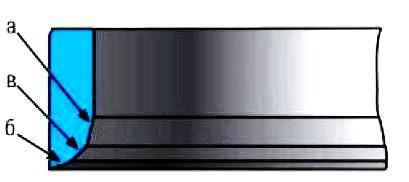
Zuerst wird die Fase „a“ im Winkel von 15˚ bearbeitet, dann die Fase „b“ im Winkel von 20˚ und die Fase „c“ im Winkel von 45˚.
Nach dem Schleifen ist es notwendig, die Ventile zu schleifen
Überprüfen Sie den Zustand der Ventilfedern. Ersetzen Sie verbogene, gebrochene oder gerissene Federn.
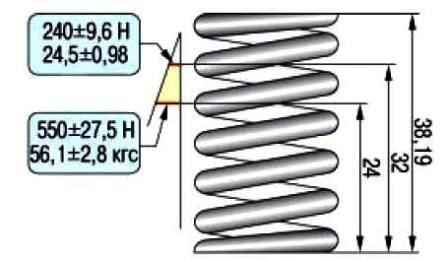
Um die Elastizität der Außenfeder zu überprüfen, messen Sie deren Höhe im freien Zustand und dann unter zwei verschiedenen Belastungen.
Wenn die Feder nicht den erforderlichen Parametern entspricht, ersetzen Sie sie.
Überprüfen Sie die Ventilstößel.
Wenn Kratzer oder andere Mängel vorhanden sind, tauschen Sie die hydraulischen Stößel aus.
Messen Sie die Außendurchmesser der Stößel und ersetzen Sie die abgenutzten Stößel.
Auf den Arbeitsflächen 2 dürfen keine Schrammen, Kerben, Kratzer, Anzeichen von stufenförmiger oder ungleichmäßiger Abnutzung oder Metallabrieb vorhanden sein.
Hydraulische Stößel mit solchen Defekten müssen ersetzt werden. Auf den Flächen 2 sind konzentrische Einlaufspuren mit Nockenwellennocken zulässig.
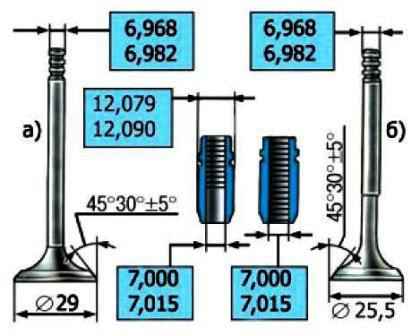
Überprüfen Sie die Abstände zwischen Führungsbuchsen und Ventilen.
Das Spiel wird als Differenz zwischen dem Durchmesser des Lochs in der Hülse und dem Durchmesser des Ventilschafts berechnet.
Abstände zwischen Ventil und Führungshülse, mm:
- – Nennwert für Einlass- und Auslassventile – 0,018–0,047
- – maximal zulässiger Wert für Einlass- und Auslassventile – 0,3
Wenn der Spalt nicht den maximal zulässigen Wert erreicht, können Sie versuchen, ihn durch Austausch des Ventils zu beseitigen. Wenn dies fehlschlägt oder das Spiel den Grenzwert überschreitet, ersetzen Sie die Führungsbuchse.
Dazu drücken Sie die defekte Buchse mit einem Dorn seitlich aus der Brennkammer heraus, nachdem Sie zuvor die Höhe des Überstands des oberen Teils der Buchse über der Oberfläche des Blockkopfes gemessen haben.
Kühlen Sie die neue Buchse ab (z. B. mit Kohlendioxid, schmieren Sie sie mit Öl, führen Sie sie in einen speziellen Dorn ein und drücken Sie sie von der Nockenwellenseite her so ein, dass die Höhe des Vorsprungs des oberen Teils der Buchse entspricht der Messwert.
Reiben Sie das Loch in der Buchse mit einer Reibahle auf 7,0–7,015 mm für die Einlass- und Auslassventile auf.
Wenn ein altes Ventil eingebaut wird, entgraten Sie die Cracker-Rillen. Danach muss das Ventil an den Sitz geschliffen werden.
Installieren Sie die Ventile gemäß den zuvor vorgenommenen Markierungen im Blockkopf, nachdem Sie den Schaft geschmiert haben und Motoröl.
Ventilschaftdichtungen einbauen.
Bauen Sie die Nockenwellen und das Nockenwellenlagergehäuse ein.
Montieren Sie alle bei der Demontage entfernten Teile und Baugruppen am Kopf des Blocks.