Ölfilter ausbauen
Schrauben Sie den Öleinfülldeckel ab.
Entfernen Sie das PCV-Ventil.
Entfernen Sie die Zündkerzen.
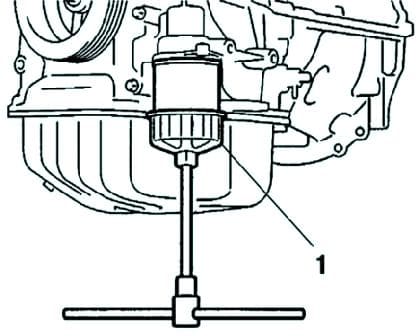
Entfernen Sie den Ölfilter mit dem Spezialwerkzeug 09228-06501 (Abb. 1).
Schrauben Sie die Mutter und das Anschlussstück ab, entfernen Sie den O-Ring vom Ölkühler, entfernen Sie den Kühler.
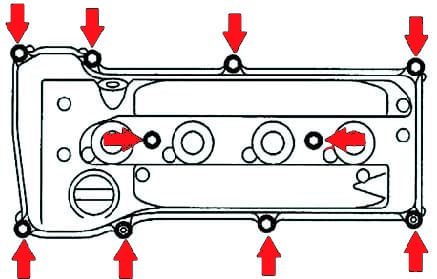
Entfernen Sie die Zylinderkopfhaube mit Dichtung, indem Sie die acht Schrauben und zwei Muttern lösen, die durch die Pfeile in Abbildung 2 gezeigt werden.
Kurbelwellenriemenscheibe ausbauen
Entfernen Sie den Nockenwellensensor.
Stellen Sie den Kolben des ersten Zylinders beim Kompressionshub auf OT.
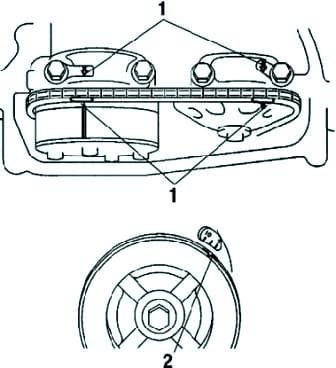
Um die Kurbelwellenriemenscheibe zu entfernen, drehen Sie sie und richten Sie die Markierung mit der „0“-Markierung auf der Steuerkettenabdeckung aus.
Stellen Sie sicher, dass die Markierungen auf den Kettenrädern mit den Markierungen auf den Nockenwellen-Lagerdeckeln Nr. 1 und Nr. 2 ausgerichtet sind, wie in Abbildung 3 gezeigt.
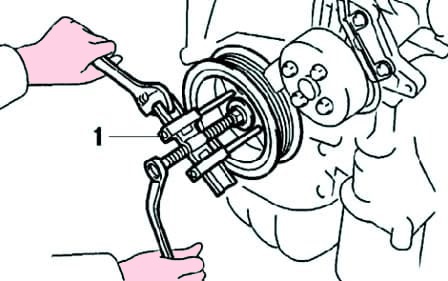
Entfernen Sie die Riemenscheibenschraube mit einem Spezialwerkzeug, und entfernen Sie dann die Kurbelwellenriemenscheibe mit einem Abzieher (Abb. 4).
Kühlmittelpumpe ausbauen
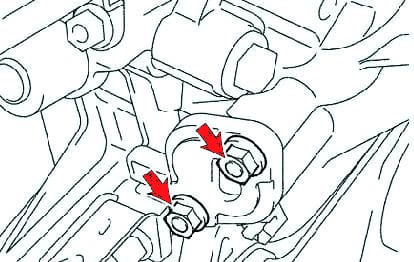
Entfernen Sie den Steuerkettenspanner, indem Sie die beiden Muttern abschrauben, die durch die Pfeile in Abbildung 5 gezeigt werden.
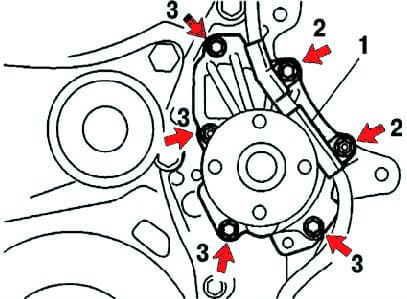
Entfernen Sie die Wasserpumpenriemenscheibe.
Entfernen Sie die Wasserpumpe, indem Sie die vier Schrauben und zwei Muttern entfernen (Abb. 6).
Ölwanne ausbauen
Entfernen Sie den Kurbelwellenpositionssensor.
Entfernen Sie die Ölwannen-Ablassschraube.
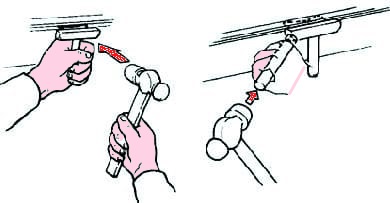
Um die Ölwanne zu entfernen, lösen Sie die zwölf Schrauben und zwei Muttern.
Die Klinge des Spezialwerkzeugs 09032-00100 zwischen die Oberflächen des Kurbelgehäuses und der Ölwanne einführen, die Dichtung durchtrennen und die Ölwanne entfernen (Abb. 7).
Achten Sie darauf, die Verbindungsflächen von Kurbelgehäuse, Ölwanne und Steuerkettenabdeckung nicht zu beschädigen.
Zerlegen der Arbeitskomponenten des Zeittriebantriebs
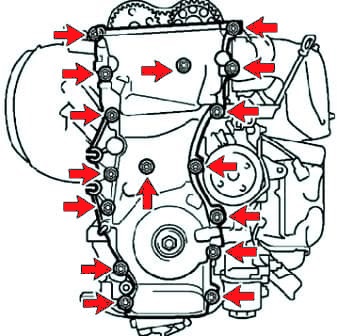
Entfernen Sie die vierzehn Schrauben und zwei Muttern, mit denen die Steuerkettenabdeckung befestigt ist (Abb. 8).
Verwenden Sie einen Schraubendreher, um die Abdeckung vom Kopf und Zylinderblock zu trennen.
Abheben Steuerkettenabdeckung.
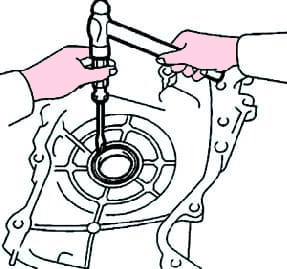
Entfernen Sie den Rotor des Kurbelwellenpositionssensors, nachdem Sie den O-Ring mit einem Schraubendreher entfernt haben (Abb. 9).
Entfernen Sie die Steuerkettenführung.
Entfernen Sie den Steuerkettenspannerschuh.
Entfernen Sie den Steuerkettendämpfer.
Entfernen Sie die Steuerkette.
Entfernen Sie das Kurbelwellenrad.
Antriebskette der Ölpumpe ausbauen
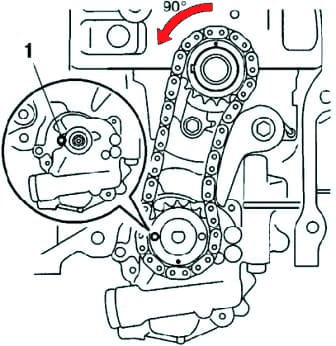
Drehen Sie die Kurbelwelle um 90° gegen den Uhrzeigersinn und richten Sie die Markierung auf der Ölpumpenwelle mit dem Loch im Pumpengehäuse aus, wie in Abbildung 10 gezeigt.
Führen Sie einen 4-mm-Stift in das Loch der Welle ein, befestigen Sie ihn und schrauben Sie die Mutter ab.
Entfernen Sie den Antriebskettenspanner der Ölpumpe mit einer Feder, indem Sie die Befestigungsschraube lösen, und entfernen Sie dann die Kettenräder und die Kette.
Ölpumpe ausbauen
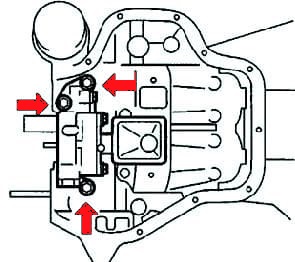
Entfernen Sie die drei Schrauben und entfernen Sie die Ölpumpe
Deckel und Nockenwellenlager ausbauen
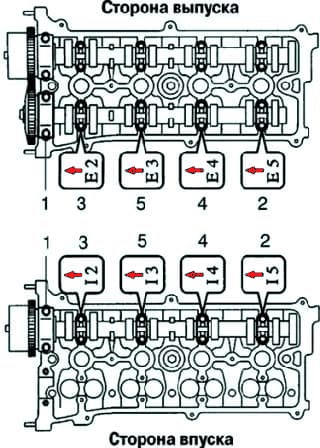
Entfernen Sie die Auslass- und Einlassnockenwellenabdeckungen in der in Abbildung 12 gezeigten Reihenfolge.
Entfernen Sie das Nockenwellenlager.
Entfernen Sie das VVT-i-Ventil.
Zylinderkopf demontieren, Axialspiel der Ausgleichswellen prüfen
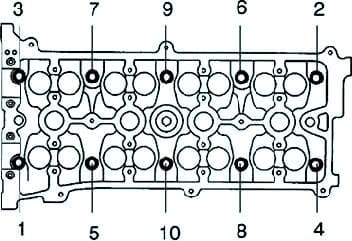
Lösen und entfernen Sie mit einem 10-mm-Steckschlüssel in mehreren Durchgängen die zehn Zylinderkopfschrauben in der in Abbildung 13 gezeigten Reihenfolge.
Wenn die Schrauben in der falschen Reihenfolge gelöst werden, kann der Zylinderkopf beschädigt werden oder im Zylinderkopf Risse bekommen.

Zehn Unterlegscheiben entfernen.
Verwenden Sie einen Schraubendreher, um den Kopf vom Zylinderblock zu trennen.
Entfernen Sie die Zylinderkopfdichtung.
Entfernen Sie die Ölkühlerarmatur.
Entfernen Sie den VVT-i-Ölfilter.
Verwenden Sie eine Messuhr, um das Endspiel zu messen, während Sie die Ausgleichswellen hin und her bewegen (Abb. 14).
Axialspiel der Ausgleichswellen:
- Standard - 0,050-0,090 mm;
- maximal zulässig - 0,090 mm.
Radialspiel der Ausgleichswellen prüfen
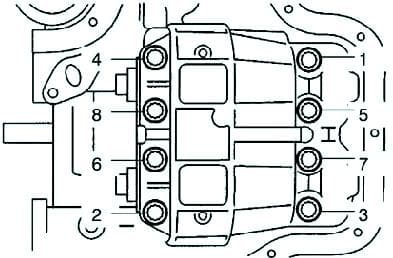
Lösen Sie nacheinander in mehreren Durchgängen die acht Befestigungsschrauben und entfernen Sie die Abdeckung des Ausgleichsmechanismus (Abb. 15).
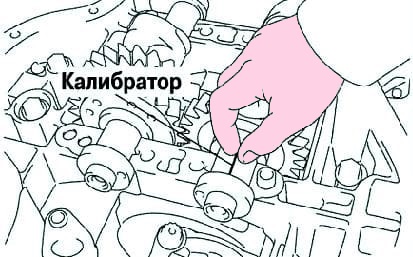
Messen Sie mit einem Kunststoffkalibrator das Spiel in den Gleitlagern für jeden Zapfen (Abb. 16).
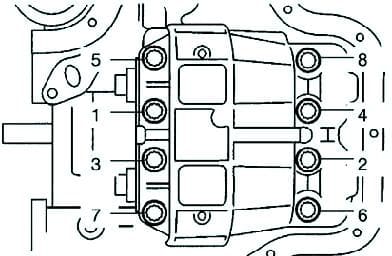
Tragen Sie etwas Motoröl unter den Köpfen und auf den Gewinden der Befestigungsschrauben auf.
Installieren Sie die Ausgleichsmechanismusabdeckung.
Ziehen Sie nacheinander in mehreren Durchgängen die acht Schrauben, mit denen der Deckel des Ausgleichsmechanismus befestigt ist, mit einem Anzugsdrehmoment von 22 Nm an (Abb. 17).
Markieren Sie die Schrauben mit Farbe.
Ziehen Sie die Schrauben in der in Abbildung 2.70 gezeigten Reihenfolge um 90° an.
Stellen Sie sicher, dass die Markierungen auf den Schrauben jetzt 90° von ihrer ursprünglichen Position entfernt sind.
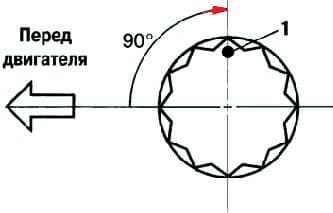
Entfernen Sie die Abdeckung des Ausgleichsmechanismus. Messen Sie die maximale Breite des abgeflachten Drahts, um das Radialspiel zu bestimmen.
Radialspiel:
- Standard - 0,004-0,031 mm;
- maximal zulässig - 0,031 mm.
Wenn das Spiel den Grenzwert überschreitet, die Ausgleichswellenlager ersetzen.
Wenn das Spiel innerhalb der Spezifikation liegt, die Ausgleichswellenlager wieder einbauen.
Wenn Sie Liner in Standardgröße ersetzen, verwenden Sie Liner derselben Größengruppe.
Es gibt drei Standard-Ohrstöpselgrößen.
Lagerbettdurchmesser:
- Markierung „1“ ..... 26.000–26.006 mm;
- Markierung "2" ..... 26,007–26,012 mm;
- Markierung "3" ..... 26,013–26,018 mm.
Der Durchmesser des Lagerzapfens beträgt 22.985–23.000 mm
Wandstärke der Auskleidung (im Mittelteil):
- Markierung „1“ ..... 1,486–1,489 mm;
- Markierung "2" ..... 1.489–1.492 mm;
- Markierung „3“ ..... 1.492–1.495 mm.
Ersetzen des hinteren Öldichtrings der Kurbelwelle
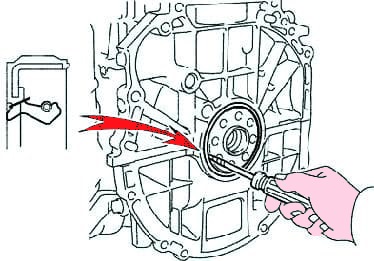
Schneiden Sie die Lippe der Drüse mit einem Messer ab. Hebeln Sie die Öldichtung mit einem in Stoff gehüllten Schraubendreher heraus (Abb. 19).
Entfernen Sie mit Schleifpapier die Reste des Wellendichtrings von der Kante des hinteren Wellendichtringhalters.
Tragen Sie Fett auf die Oberfläche der neuen Öldichtung auf.
Den neuen Wellendichtring mit einem Dorn und einem Hammer so eindrücken, dass seine Oberfläche nicht über die Kante des hinteren Wellendichtringhalters hinausragt.
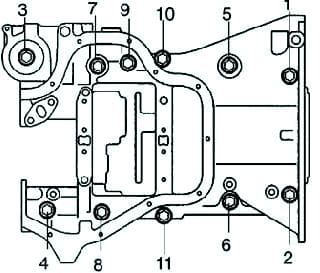
Lösen Sie nacheinander in mehreren Durchgängen die elf Kurbelgehäuse-Befestigungsschrauben (Abb. 20).
Kontrolle der Steuerkette und der Kettenräder der Wellen
Messen Sie die Länge von fünfzehn Kettengliedern unter Spannung mit einem Messschieber.
Wenn die Kettenlänge fünfzehn Glieder überschreitet, ersetzen Sie die Kette.
Machen Sie drei oder mehr Messungen an beliebigen Abschnitten der Schaltung.
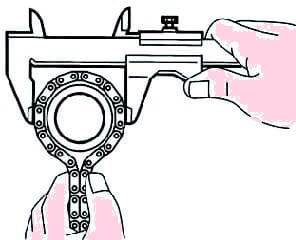
Wickle die Kette um das Kettenrad.
Messen Sie den Durchmesser des Kettenrads über den Rollen mit einem Messschieber, wie in Abbildung 21 gezeigt.
Minimaler Kettenraddurchmesser:
- - Nockenwelle - 97,3 mm;
- - Kurbelwelle - 51,6 mm.
Wenn der Durchmesser nicht wie angegeben ist, Kettenräder durch Kette ersetzen.
Überprüfen Sie den Spannschuh und die Steuerkettenführung auf Verschleiß.
Der maximale Verschleiß sollte 1 mm nicht überschreiten.
Überprüfung der Funktion des Steuerkettenspanners Abteilungen
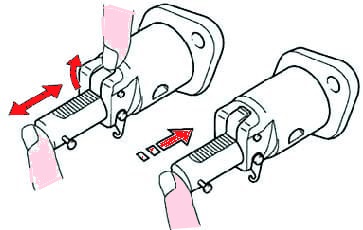
Stellen Sie sicher, dass sich der Kolben frei bewegt, wenn die Ratsche angehoben wird.
Lassen Sie die Ratsche los und vergewissern Sie sich, dass der Kolben verriegelt ist (Abb. 22).
Nockenwellenschlag prüfen
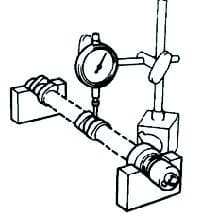
Die Nockenwelle auf zwei Prismen einbauen.
Setzen Sie den empfindlichen Kopf des Indikators auf den Hals.
Die Nockenwelle von Hand zur Seite drehen und den Schlag mit einer Messuhr messen (maximaler Messwert) (Abb. 23).
Die maximale Rundlauftoleranz beträgt 0,03 mm.
Prüfen der Nockenhöhe der Nockenwelle
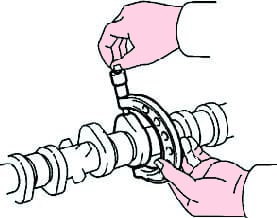
Die Höhe der Nockenwelle messen (Abb. 24).
Die Standardhöhe der Nockenkontur beträgt 46,495–46,595 mm.
Die Mindesthöhe der Nockenkontur beträgt 46,385 mm.
Nockenwellenzapfenspiel (Außendurchmesser des Nockenwellenzapfens)
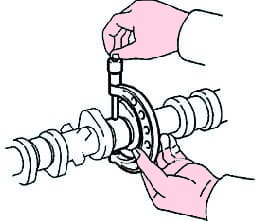
Messen Sie den Außendurchmesser des Nockenwellenzapfens (Abb. 25).
Innendurchmesser der Standard-Nockenwellenhalterung:
- Nr. 1.....35,971–35,985 mm;
- Nr. 2,3,4,5.....22.959–22.975 mm.
Getriebenes Kettenrad einbauen (Einlassnockenwelle)
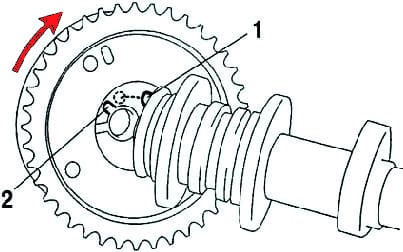
Halten Sie das Kettenrad in einer solchen Position, dass sich die Nut darin etwas links vom Nockenwellen-Fixierstift (Wellenseite) befindet.
Montieren Sie das Kettenrad auf der Nockenwelle.
Drücken Sie leicht auf den Stern und drehen Sie ihn gegen den Uhrzeigersinn.
Achten Sie darauf, dass zwischen dem Kettenrad und dem Ende der Nockenwelle kein Spalt sichtbar ist.
Halten Sie die Welle mit einem Schraubenschlüssel fest und ziehen Sie die Befestigungsschraube mit 54 Nm fest.
Achten Sie darauf, dass sich der WT-Antrieb im Uhrzeigersinn bewegt und mit dem Arretierstift in der richtigen Position arretiert (Abb. 26).