Der K4M-Motor ist ein Benzin-Viertakt-Vierzylinder-Reihenmotor mit 16 Ventilen und zwei obenliegenden Nockenwellen. Die Betriebsreihenfolge der Zylinder: 1-3-4-2, gezählt - vom Schwungrad aus
Antriebssystem – verteilte Kraftstoffeinspritzung (Euro 4-Toxizitätsnormen).
Ein Motor mit Getriebe und Kupplung bilden eine Antriebseinheit – eine einzige Einheit, die im Motorraum auf drei elastischen Gummi-Metall-Trägern montiert ist.
Die rechte Halterung ist an der oberen Abdeckung des Steuerradantriebs befestigt, die linke und die hintere Halterung sind am Getriebegehäuse befestigt.
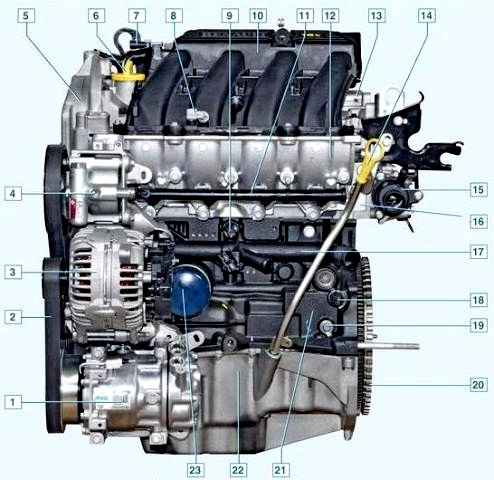
Motor (Vorderansicht K4M): 1 - Klimakompressor; 2 - Hilfsantriebsriemen; 3 - Generator; 4 - Servolenkungspumpe: 5 - obere Abdeckung des Gasverteilungsmechanismusantriebs; 6 - Öleinfülldeckel; 7 - absoluter Luftdrucksensor; 8 - Ansauglufttemperatursensor; 9 - Klopfsensor; 10 - Empfänger; 11 - Kraftstoffverteiler mit Einspritzdüsen; 12 - Einlassrohr; 13 - Zylinderkopfhaube; 14 - Ölstandsanzeige; 15 - Thermostatgehäuse; 16 - Zylinderkopf 17 - Kühlmittelpumpenrohr; 18 - Sensor für Öldruckanzeige: 19 - Stecker; 20 - Schwungrad; 21 - Zylinderblock; 22 - Ölwanne; 23 - Ölfilter
Vorne am Motor (in Richtung des Autos, Abbildung 1) befinden sich: Einlassrohr; Ölfilter; Ölstandsanzeige; Sensor zur Anzeige von niedrigem Öldruck; Kraftstoffverteiler mit Einspritzdüsen; Klopfsensor; Einlassrohr der Kühlmittelpumpe; Generator; Servolenkungspumpe; Klimakompressor.
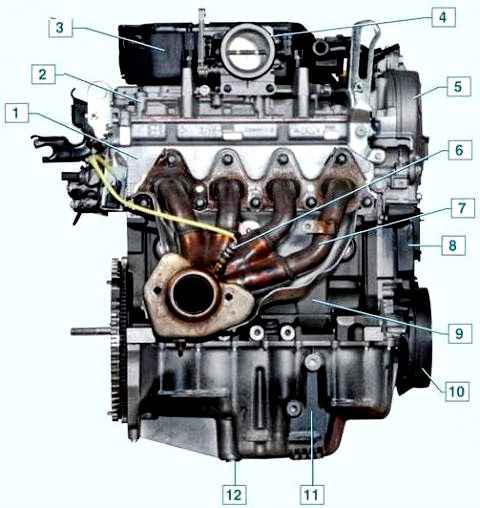
Motor (Rückansicht des K4M): 1 - Zylinderkopf; 2 - Zylinderkopfhaube; 3 - Empfänger; 4 - Drosselklappenbaugruppe; 5 - obere Abdeckung des Antriebs des Gasverteilungsmechanismus; 6 - Sauerstoffkonzentrationssensor steuern; 7- Abgaskrümmer; 8 - untere Abdeckung des Antriebs des Gasverteilungsmechanismus; 9 - Zylinderblock; 10 - Hilfsantriebsriemen; 11 - Ölwanne; 12 - Ölablassschraube
Hinten (Bild 2) am Motor befinden sich:
- - Luftfiltergehäuse mit Leerlaufdrehzahlregelung;
- - Abgaskrümmer mit einem Kontrollsauerstoffkonzentrationssensor;
- - Starter.
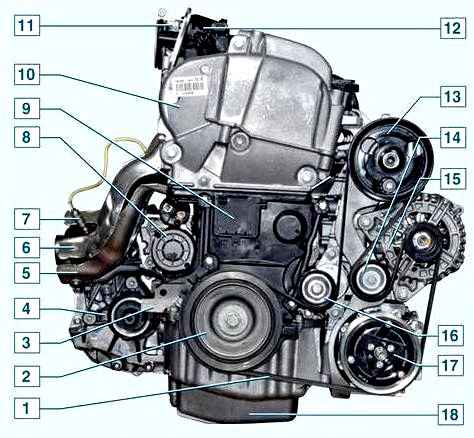
Motor (Blick von rechts in Fahrtrichtung): 1 - Hilfsantriebsriemen; 2 - Hilfsantriebsriemenscheibe; 3 - Zylinderblock; 5 - unterer Hitzeschild des Abgaskrümmers; 6 - oberer Hitzeschild des Abgaskrümmers; 7 - Sauerstoffkonzentrationssensor steuern; 8 - Abgaskrümmer; 9 - untere Abdeckung des Antriebs des Gasverteilungsmechanismus; 10 - obere Abdeckung des Antriebs des Gasverteilungsmechanismus; 11 - Drosselklappenbaugruppe; 12 - Empfänger; 13 - Riemenscheibe der Servolenkungspumpe; 14 - Riemenstützrolle; 15 - Generator; 16 - Riemenspannrolle; 17 - Riemenscheibe des Klimakompressors; 18 - Ölwanne
Rechts (Abbildung 3) – Kühlmittelpumpe; Steuerrad- und Kühlmittelpumpenantrieb (Zahnriemen); Antrieb von Nebenaggregaten (Keilrippenriemen).
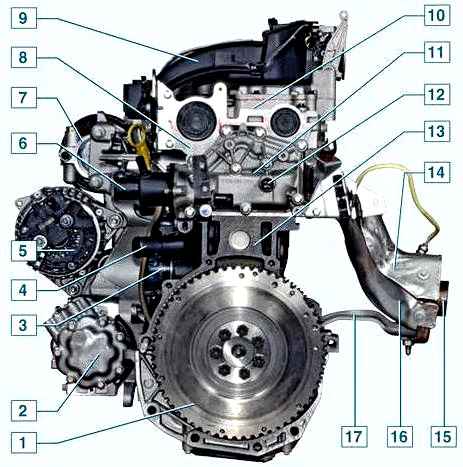
Motor (Blick von links in Richtung Auto): 1 - Schwungrad; 2 - Klimakompressor; 3 - Ölfilter; 4 - Einlassrohr der Kühlmittelpumpe; 5 - Generator; 6 - Thermostatgehäuse; 7 - Servolenkungspumpe; 3 - Zylinderkopf; 9 - Empfänger; 10 - Zylinderkopfhaube; 11 - Abdeckung des Zylinderkopfkühlmantels; 12 - Kühlmitteltemperatursensor; 13 - Zylinderblock; 14 - oberer Hitzeschild des Abgaskrümmers; 15 - Abgaskrümmer; 16 - unterer Hitzeschild des Abgaskrümmers; 17 - Auspuffkrümmerhalterung
Auf der linken Seite (Abbildung 4) befinden sich: Schwungrad; Kurbelwellenpositionssensor; Thermostat; Thermostatgehäuse mit Kühlmitteltemperatursensor Granne.
Oben – Spulen und Zündkerzen; Öleinfüllstutzen; ein Empfänger mit Sensoren für Absolutdruck und Ansauglufttemperatur, eine Drosselklappenbaugruppe mit einem Drosselklappenstellungssensor.
Der Zylinderblock des Motors besteht aus Gusseisen, die Zylinder sind direkt im Block gebohrt.
Im unteren Teil des Zylinderblocks befinden sich fünf Kurbelwellen-Hauptlagerstützen mit abnehmbaren Abdeckungen, die mit speziellen Schrauben am Block befestigt werden.
Die Bohrungen im Zylinderblock für die Lager werden mit montierten Abdeckungen bearbeitet, sodass die Abdeckungen nicht austauschbar sind und zur Unterscheidung auf der Außenfläche markiert sind (die Abdeckungen werden von der Schwungradseite aus gezählt).
An den Endflächen des Mittelträgers sind Buchsen für Druckhalbringe angebracht, die eine axiale Bewegung der Kurbelwelle verhindern.
Um die Kolben während des Motorbetriebs zu kühlen, werden ihre Böden von unten mit Motoröl durch spezielle Düsen umspült, die im Bereich der zweiten und vierten Stütze (auf beiden Seiten der Stützen) in den Zylinderblock gedrückt werden die Hauptlager.
Kurbelwelle mit fünf Hauptzapfen und vier Kurbelzapfen.
Die Schalen der Haupt- und Pleuellager der Kurbelwelle bestehen aus dünnwandigem Stahl mit einer reibungsmindernden Beschichtung auf den Arbeitsflächen der Schalen.
Die Welle ist mit vier in die Welle integrierten Gegengewichten ausgestattet.
Um Öl von den Hauptzapfen zu den Pleuelzapfen zu transportieren, sind Kanäle in den Hälsen und Wangen der Welle angebracht.
Am vorderen Ende (Zehe) der Kurbelwelle sind Folgendes installiert: ein Ölpumpen-Antriebsrad, eine Steuerrad-Antriebsriemenscheibe (Timing) und eine Hilfsantriebsriemenscheibe.
Die Zahnriemenscheibe wird durch einen Vorsprung auf der Welle befestigt, der in die Nut an der Spitze der Kurbelwelle passt.
Die Antriebsriemenscheibe des Nebenaggregats ist ebenfalls auf der Welle befestigt.
Die Kurbelwelle ist mit zwei Wellendichtringen abgedichtet, von denen einer (auf der Steuerantriebsseite) in den Zylinderblockdeckel und der andere (auf der Schwungradseite) in die durch die Oberflächen gebildete Buchse gedrückt wird Zylinderblock und Hauptlagerdeckel.
Ein Schwungrad ist mit sieben Schrauben am Kurbelwellenflansch befestigt. Es ist aus Gusseisen gegossen und verfügt über eine gepresste Stahlkrone zum Starten des Motors mit einem Anlasser.
Zusätzlich ist am Schwungrad ein Zahnkranz für den Kurbelwellen-Positionssensor eingeschnitten.
Pleuelstangen – geschmiedeter Stahl, I-Profil, zusammen mit Abdeckungen verarbeitet.
Die Abdeckungen werden mit speziellen Schrauben und Muttern an den Pleuelstangen befestigt.
Mit ihren unteren (Kurbel-)Köpfen sind die Pleuel über Buchsen mit den Pleuelzapfen der Kurbelwelle verbunden, und die oberen Köpfe sind über die Kolbenbolzen mit den Kolben verbunden.
Kolbenbolzen sind aus Stahlrohr.
Der in den oberen Kopf der Pleuelstange eingepresste Bolzen dreht sich frei in den Kolbennaben.
Kolben bestehen aus einer Aluminiumlegierung. Der Kolbenschaft hat eine komplexe Form; Im Längsschnitt tonnenförmig und im Querschnitt oval.
Im oberen Teil des Kolbens sind drei Nuten für Kolbenringe eingearbeitet. Die beiden oberen Kolbenringe sind Kompressionsringe und der untere ist ein Ölabstreifer.
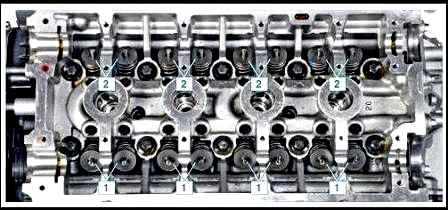
Der Zylinderkopf (Bild 5) ist aus einer Aluminiumlegierung gegossen, die allen vier Zylindern gemeinsam ist.
Der Zylinderkopf wird mit zwei Buchsen auf dem Block zentriert und mit zehn Schrauben befestigt.
Zwischen dem Block und dem Kopf ist eine nicht schrumpfende Metalldichtung angebracht. Auf gegenüberliegenden Seiten des Zylinderkopfes befinden sich die Einlass- und Auslasskanäle.
Zündkerzen sind in der Mitte jeder Brennkammer installiert.
Stahlventile, in zwei Reihen im Zylinderkopf angeordnet, V-förmig, zwei Einlass- und zwei Auslassventile für jeden Zylinder.
Die Einlassventilplatte ist größer als das Auslassventil.
Die Ventilsitze und Führungen werden in den Zylinderkopf eingepresst.
Ölkappen werden oben auf den Ventilführungen angebracht.
Das Ventil schließt unter der Wirkung einer Feder. Sein unteres Ende ruht auf einer Unterlegscheibe und sein oberes Ende ruht auf einer Platte, die von zwei Semmelbröseln gehalten wird.
Die gefalteten Cracker haben außen die Form eines Kegelstumpfes und sind innen mit hartnäckigen Perlen ausgestattet, die in die Nut am Ventilschaft eindringen.
Zwei Nockenwellen sind oben auf dem Zylinderkopf montiert.
Eine Welle treibt die Einlassventile des Gasverteilungsmechanismus an, die andere die Auslassventile.
Auf jeder Welle sind acht Nocken angebracht – ein benachbartes Nockenpaar steuert gleichzeitig die Ventile (Einlass oder Auslass) jedes Zylinders.
Das Konstruktionsmerkmal der Nockenwelle besteht darin, dass die Nocken auf die Rohrwelle gepresst werden.
Stützen (Betten) Die Begrenzungswellen (sechs Lager für jede Welle) sind abnehmbar und befinden sich im Zylinderkopf und in der Kopfabdeckung.
Nockenwellenantrieb – Zahnriemen von der Kurbelwellenriemenscheibe.
Auf jeder Nockenwelle ist auf der Seite der Zahnscheibe ein Druckflansch angebracht, der bei der Montage in die Nut des Zylinderkopfes eindringt und so eine axiale Bewegung der Welle verhindert.
Die Befestigung der Nockenwellenriemenscheibe auf der Welle erfolgt nicht durch Passung, Passfeder oder Stift, sondern nur durch die Reibungskräfte, die beim Anziehen der Riemenscheiben-Befestigungsmutter an den Endflächen der Riemenscheibe und der Welle auftreten.
Die Spitze der Nockenwelle wird mit einer Öldichtung abgedichtet, auf den Wellenhals aufgesetzt und in die durch die Oberflächen des Zylinderkopfs und der Kopfabdeckung gebildete Aussparung gedrückt.
Ventile werden von Nockenwellen über Ventilhebel angetrieben.
Um die Lebensdauer der Nockenwelle und der Ventilhebel zu erhöhen, wirkt der Nocken der Welle über eine Rolle, die sich auf der Achse des Hebels dreht, auf den Hebel.
Die hydraulischen Lager der Ventilhebel sind in den Buchsen des Zylinderkopfes eingebaut.
Das Öl im Inneren des Hydrolagers kommt von der Leitung im Zylinderkopf durch das Loch im Hydrolagergehäuse.
Hydrosupport sorgt automatisch für einen spielfreien Kontakt des Nockenwellennockens mit der Ventilhebelrolle und gleicht den Verschleiß an Nocken, Hebel, Ventilschaftende, Sitzfasen und Ventilteller aus.
Motorschmierung – kombiniert.
Unter Druck wird Öl den Haupt- und Pleuellagern der Kurbelwelle, den Nockenwellenlagern und den hydraulischen Ventilhebellagern zugeführt.
Andere Motorkomponenten sind spritzgeschmiert.
Der Druck im Schmiersystem wird durch eine Zahnradölpumpe erzeugt, die sich in der Ölwanne befindet und am Zylinderblock befestigt ist.
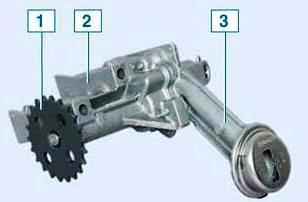
Die Ölpumpe wird über einen Kettentrieb (Abbildung 6) von der Kurbelwelle angetrieben.
Das Pumpenantriebsritzel ist auf der Kurbelwelle unter der Zylinderabdeckung montiert.
Auf dem Kettenrad ist ein zylindrischer Riemen angebracht, entlang dem der vordere Kurbelwellen-Öldichtring arbeitet.
Das Kettenrad wird spannungsfrei auf der Kurbelwelle montiert und nicht mit einem Schlüssel fixiert.
Beim Zusammenbau des Motors wird das Antriebsritzel des Pumpenantriebs zwischen der Zahnriemenscheibe und der Kurbelwellenschulter eingeklemmt, da das Teilepaket durch die Befestigungsschraube der Nebenantriebsriemenscheibe zusammengezogen wird.
Das Drehmoment von der Kurbelwelle wird nur aufgrund der Reibungskräfte zwischen den Endflächen des Kettenrads, der Zahnscheibe und der Kurbelwelle auf das Kettenrad übertragen.
Wenn die Schraube der Nebenantriebsriemenscheibe gelöst wird, beginnt sich möglicherweise das Antriebsritzel der Ölpumpe auf der Kurbelwelle zu drehen und der Motoröldruck sinkt.
Der Ölbehälter ist einstückig mit dem Deckel des Ölpumpengehäuses gefertigt. Der Deckel wird mit fünf Schrauben am Pumpengehäuse befestigt.
Das Druckminderventil befindet sich im Deckel des Pumpengehäuses und wird durch eine Federsicherung gegen Herausfallen gesichert.
Das Öl von der Pumpe fließt durch den Ölfilter und gelangt in die Hauptölleitung des Zylinderblocks.
Ölfilter – Vollstrom, nicht trennbar.
Von der Hauptleitung fließt Öl zu den Hauptlagern der Kurbelwelle, den Kolbenkühldüsen und weiter (durch die Kanäle in der Kurbelwelle) zu den Pleuellagern der Welle.
Durch zwei vertikale Kanäle im Zylinderblock wird Öl aus der Hauptleitung dem Zylinderkopf zugeführt – zu den äußersten Halterungen der Nockenwellen von der Seite der Stopfen und den hydraulischen Ventilhalterungen.
Durch die Nuten und Bohrungen in den äußersten Lagerzapfen der Nockenwellen gelangt Öl in die Wellen und dann durch die Bohrungen in anderen Wellenzapfen zu den übrigen Nockenwellenlagern.
Vom Zylinderkopf fließt das Öl durch vertikale Kanäle in den Motorsumpf.
Kurbelgehäuseentlüftungssystem – geschlossener, erzwungener Typ.
Gase, die aus den Brennräumen der Zylinder durch die Kolbenringe in das Kurbelgehäuse des Motors gelangt sind, gelangen durch die Kanäle im Block und im Zylinderkopf in die Zylinderkopfhaube.
Nachdem sie den Ölabscheider im Zylinderkopfdeckel passiert haben, werden die Kurbelgehäusegase von Ölpartikeln gereinigt und strömen dann durch das Luftfiltergehäuse, die Drosselklappenbaugruppe, den Sammler und die Einlassleitung in die Motorzylinder.
Steuerungs-, Strom-, Kühl- und Abgassysteme werden in den entsprechenden Artikeln beschrieben.