So tauschen Sie die hydraulischen Ventilkompensatoren des K4M-Motors aus
Sie benötigen: die gleichen Werkzeuge wie für den Wechsel der Ventilschaftdichtungen, mit Ausnahme derjenigen, die direkt für den Austausch benötigt werden (Werkzeuge werden nur für vorbereitende Arbeiten verwendet), und zusätzlich drei Behälter zum Spülen von Dieselkraftstoff mit einem Fassungsvermögen von ca. 2 Liter je ein Stück gehärteter Draht mit einem Durchmesser von 0,5 mm und einer Länge von ca. 10 cm.
Das Auto für die Arbeit vorbereiten.
Wir installieren es auf einem Aufzug oder einem Inspektionsgraben.
Entfernen Sie den Zahnriemen (siehe Artikel zum Austausch des Zahnriemens).
Entfernen Sie den Ölabscheider des Belüftungssystems.
Lösen Sie mit einem 10er-Kopf die Schraube, mit der die Halterung des Sondenführungsrohrs an der Lufteinlasshalterung befestigt ist
Entfernen Sie den Schlauch mit der Sonde aus der Buchse der Motorwanne.
Das Rohr ist mit einem Gummiring abgedichtet.
Bei einem Kopf von 8 lösen wir die beiden Schrauben, mit denen das Auge befestigt ist
Entfernen Sie das Auge mit der Halterung
Mit einem Kopf von 8 lösen wir die vierundzwanzig Schrauben, mit denen die Zylinderkopfhaube befestigt ist
Hebeln Sie mit einem Schraubenzieher die Zylinderkopfabdeckung ab (um die Abdeckung zu fixieren, legen Sie einen Lappen auf)
Entfernen Sie die Zylinderkopfhaube
Wir entfernen zwei Gummi-Metallstopfen vom Zylinderkopf
Entfernen Sie den Auslassventilschaft
Einlassventilschaft ausbauen
Um die Hydrauliklager zu überprüfen, entfernen Sie den Hebel
Entfernen Sie den hydraulischen Kompensator aus der Buchse des Zylinderkopfs
Die Überprüfung von Hydraulikstößeln wird weiter unten besprochen.
Um die Riemenscheibe zu entfernen, legen Sie die Nockenwelle hin.
Wir haben einen 18er Schraubenschlüssel an der Befestigungsmutter der Riemenscheibe angebracht. Wir stecken einen Schraubenzieher durch das Loch in der Riemenscheibe.
Stützen Sie mit einer Schraubendreherklinge auf die Riemenscheibennabe, drücken Sie mit der Schraubendreherstange auf den Schlüssel und drehen Sie ihn gegen den Uhrzeigersinn.
Die Riemenscheibe sollte sich nicht drehen und die Mutter dreht sich weg.
Entfernen Sie die Riemenscheibe vom Ende der Nockenwelle
Entfernen Sie das Siegel. Wir entfernen auch den Wellendichtring von der anderen Nockenwelle
Tragen Sie Dichtmittel auf die Passfläche der Abdeckung auf
Wir montieren die Zylinderkopfhaube und ziehen die Schrauben ihrer Befestigung mit dem vorgeschriebenen Drehmoment in der in der Tabelle angegebenen Reihenfolge an.
Nachdem wir die Zylinderkopfhaube montiert haben, drücken wir mit einem Werkzeugkopf oder einem Rohrstück geeigneter Größe die neuen Nockenwellendichtringe in die Zylinderkopfbuchsen, nachdem wir zuvor eine dünne Schicht Motoröl auf die Arbeitskanten aufgetragen haben der Öldichtungen.
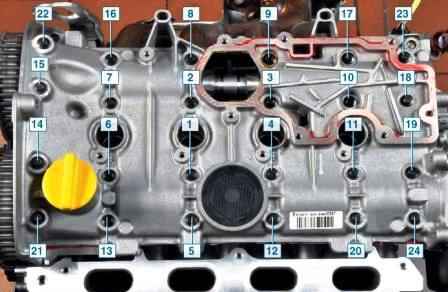
Nummerierung der Zylinderkopfhaubenschrauben
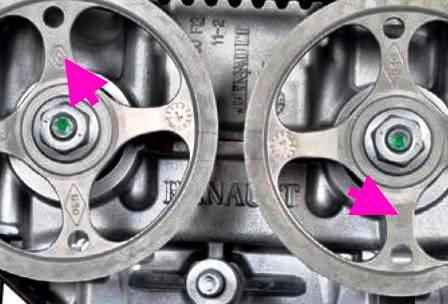
Nachdem wir die Phasen des Gasverteilungsmechanismus überprüft und die Wellen befestigt haben, montieren wir die Zahnscheiben an den Zehen der Nockenwellen, sodass die auf den Speichen der Riemenscheiben aufgedruckten Renault-Embleme senkrecht nach oben (Auslassventilwelle) und liegen unten (Einlassventilschaft).
Nachdem wir die Befestigungsmuttern der Riemenscheibe aufgeschraubt haben, ziehen wir sie leicht an.
Wir montieren die Riemenscheiben und ziehen den Zahnriemen.
Ziehen Sie die Muttern zur Befestigung der Nockenwellenriemenscheiben mit einem Anzugsdrehmoment von 30 Nm und einem Drehmoment von 84˚ an.
Wir drehen die Kurbelwelle zwei Umdrehungen im Uhrzeigersinn und prüfen den korrekten Einbau der Ventilsteuerung. Wiederholen Sie ggf. den Einbau der Ventilsteuerung.
Hydraulische Ventilkompensatoren prüfen und spülen
Die hydraulischen Spaltkompensatoren im Ventiltriebmechanismus dienen zum Ausgleich der thermischen Ausdehnung der Antriebselemente.
Die Funktionsweise des hydraulischen Kompensators basiert auf dem Prinzip der Inkompressibilität des Motoröls, das während des Motorbetriebs ständig den inneren Hohlraum des hydraulischen Kompensators füllt und seinen Kolben bewegt, wenn im Ventiltrieb ein Spalt entsteht, wodurch ein konstanter Kontakt gewährleistet wird Die Druckhebelrolle des Ventiltriebs spielfrei mit dem Nockenwellennocken verbinden. Dadurch entfällt die Notwendigkeit einer Ventileinstellung während der Wartung.
Hydraulikheber sind nicht trennbare kompakte Geräte, die in die Buchsen des Zylinderkopfs eingesetzt werden.
Ventilklopfen bei laufendem Motor kann folgende Ursachen haben:
- - Luft dringt in die Hohlräume über dem Kolben hydraulischer Kompensatoren ein, wenn der Ölstand im Kurbelgehäuse zu niedrig oder zu hoch ist, sowie wenn das Auto längere Zeit am Hang geparkt ist;
- - Verschmutzung der Präzisionsflächen der hydraulischen Spielkompensatoren im Ventilantriebsmechanismus durch Schlamm aus minderwertigem Motoröl (oder wenn dieses nicht rechtzeitig ausgetauscht wird, sowie wenn der Ölfilter beschädigt ist);
- - Verschleiß der hydraulischen Kompensatoren.
Wenn die hydraulischen Kompensatoren durch Pumpen oder Spülen nicht wiederhergestellt werden können, ersetzen Sie sie, da sie nicht trennbar sind.
Stellen Sie zunächst sicher, dass Fremdgeräusche beim Motorbetrieb durch eine Fehlfunktion der Hydrostößel verursacht werden:
- – Motor starten. Bei einer Fehlfunktion der Hydrostößel treten unmittelbar nach dem Starten des Motors Fremdgeräusche im Bereich des Kopfdeckels auf, die sich entsprechend der Änderung der Motordrehzahl ändern.
Wenn das Geräusch nicht unmittelbar nach dem Starten des Motors auftritt oder sich bei einer Änderung der Kurbelwellendrehzahl nicht ändert, liegt die Fehlfunktion nicht an einer Fehlfunktion der Hydrostößel. Wenn sich außerdem das Geräusch beim Ändern der Kurbelwellendrehzahl nicht ändert, ist es wahrscheinlich, dass dies die Ursache für den Pfosten ist Hupengeräusch nicht im Motor;
- - Stellen Sie im Leerlauf des Motors sicher, dass sich der Geräuschpegel bei Laständerungen nicht ändert (z. B. beim Umschalten des Automatikgetriebewählers von Position N auf Position D beim Auskuppeln eines Fahrzeugs mit Schaltgetriebe). oder beim Einschalten von elektrischen Verbrauchern und Klimaanlagen) .
Wenn sich der Geräuschpegel ändert, kann die Ursache eine Kollision von Teilen aufgrund von Verschleiß der Pleuelstange und der Hauptlager der Kurbelwelle sein und nicht eine Fehlfunktion der Hydrostößel;
- – Den Motor auf Betriebstemperatur erwärmen. Wenn das Geräusch nachgelassen hat oder ganz verschwunden ist, ist es möglich, dass das Klappern der Hydrostößel auf eine Ölverschmutzung zurückzuführen ist. In diesem Fall ist es notwendig, die Hydrostößel zu spülen:
- – Wenn das Geräusch nicht verschwindet, ist wahrscheinlich Luft in die Hydrostößel gelangt und sollte entfernt werden.
Wenn der Ölstand im Kurbelgehäuse zu niedrig ist, saugt die Ölpumpe zusammen mit dem Öl Luft an; Ist der Ölstand im Kurbelgehäuse zu hoch, wird das Öl durch die Gegengewichte der Kurbelwelle aufgewirbelt und aufgeschäumt.
Wenn das Auto längere Zeit am Hang geparkt ist, fließt Öl aus den Hohlräumen der hydraulischen Kompensatoren und Ölkanälen, und die Ölversorgung der hydraulischen Kompensatoren nach dem Starten des Motors dauert einige Zeit, während der Hohlraum des hydraulischen Kompensators hat Zeit, Luft zu bekommen.
Wenn in all diesen Fällen Öl mit Luft in den Hohlraum über dem Kolben des hydraulischen Kompensators gelangt, wird die Luft im Hohlraum beim Öffnen des Ventils komprimiert und der hydraulische Kompensator wird nicht komprimiert, was zu einem charakteristisches Klopfen des Ventilmechanismus mit erhöhtem Spiel.
Um die hydraulischen Stößel zu entlüften, gehen Sie wie folgt vor:
Überprüfen Sie den Ölstand im Kurbelgehäuse und füllen Sie gegebenenfalls nach;
- - Starten Sie den Motor und lassen Sie ihn 1–3 Minuten lang im Leerlauf warmlaufen;
- - Erhöhen Sie die Kurbelwellendrehzahl auf 3000 min-1, reduzieren Sie sie dann stark auf die Leerlaufdrehzahl und lassen Sie den Motor im Leerlauf laufen;
- - Wiederholen Sie den Zyklus und prüfen Sie, ob das Geräusch des Ventilantriebsmechanismus verschwunden ist
Wenn die Hydrostößel in gutem Zustand sind, verschwindet das Geräusch nach 10–30 Zyklen;
- - Nachdem das Geräusch verschwunden ist, wiederholen Sie den Vorgang, um die Luft noch fünf Mal zu entfernen;
- - Lassen Sie den Motor 1-3 Minuten lang im Leerlauf laufen und stellen Sie sicher, dass das Geräusch des Ventilantriebsmechanismus verschwunden ist.
Wenn das Geräusch des Ventilantriebsmechanismus nach dem Entlüften und Aufwärmen des Motors auf Betriebstemperatur nicht verschwindet, identifizieren Sie fehlerhafte Hydrostößel wie folgt.
- 1. Stellen Sie den Motor ab und stellen Sie sofort nach dem Abstellen den Kolben des 1. Zylinders auf die OT-Position des Kompressionshubs und entfernen Sie die Zylinderkopfhaube.
- 2. Entfernen Sie die Nockenwellen.
- 3. Um die Funktion der hydraulischen Kompensatoren des Motors zu überprüfen, drücken Sie auf den Arm des Kipphebels, der auf dem hydraulischen Kompensator aufliegt. Lässt sich der Kipphebel ohne oder mit geringem Kraftaufwand bewegen, ist der Hydrostößel defekt.
- 4. Überprüfen Sie in ähnlicher Weise den Zustand der hydraulischen Kompensatoren der übrigen Zylinder (Betriebsreihenfolge der Zylinder 1-3-4-2).
Nachdem Sie fehlerhafte Hydrostößel identifiziert haben, sollten Sie zunächst versuchen, diese wie folgt zu spülen.
- 1. Entfernen Sie die Kipphebel.
- 2. Entfernen Sie den defekten hydraulischen Kompensator aus der Zylinderkopfaufnahme.
- 3. Bereiten Sie drei identische Behälter mit einem Fassungsvermögen von ca. 2 Litern zum Spülen von Hydrostößeln vor.
Die Abmessungen jedes Behälters müssen ausreichend sein, damit der hydraulische Kompensator, der in vertikaler Position auf den Boden des Behälters abgesenkt wird, vollständig in die Flüssigkeit eingetaucht ist.
Befüllen Sie die Behälter mit sauberem Dieselkraftstoff.
- 4. Stellen Sie den Hydrostößel in den ersten Behälter und reinigen Sie die Außenfläche.
- 5. Nachdem Sie den hydraulischen Kompensator zur Hälfte mit dem Kolben nach unten in den ersten Behälter eingetaucht haben, drücken Sie den Draht leicht durch das Loch, drücken Sie die Ventilkugel zusammen und bewegen Sie den Kolben des hydraulischen Kompensators 5-10 Mal, während Sie die Kugel gedrückt halten, bis sich der Kolben vollständig frei bewegt .
Wenn sich der Kolben nicht leicht bewegen lässt, ersetzen Sie den hydraulischen Kompensator.
- 6. Nehmen Sie den hydraulischen Kompensator aus dem Behälter und bewegen Sie durch Drücken der Ventilkugel den Kolben, bis der Dieselkraftstoff aus dem hydraulischen Kompensator fließt.
- 7. Setzen Sie den Hydrostößel in den zweiten Behälter und wiederholen Sie Schritt 5.
- 8. Nehmen Sie den hydraulischen Kompensator aus dem Behälter und lassen Sie den Dieselkraftstoff ab, wie in Schritt 6 beschrieben.
- 9. Platzieren Sie den hydraulischen Kompensator senkrecht mit dem Kolben nach oben auf dem Boden des dritten Behälters und wringen Sie die Kugel seines Ventils mit einem Draht aus.
- 10. Während Sie die Ventilkugel gedrückt halten, bewegen Sie den Kolben nach unten und dann langsam nach oben, sodass der Hohlraum über dem Kolben des hydraulischen Kompensators mit Dieselkraftstoff gefüllt wird.
- 11. Entfernen Sie den hydraulischen Kompensator aus dem Behälter. Halten Sie es mit dem Kolben nach oben und drücken Sie es mit etwas Kraftaufwand auf den Kolben und stellen Sie sicher, dass er ruhig bleibt.
Überprüfen Sie gleichzeitig die Gesamthöhe des Hydrostößels durch einen Vergleich mit dem neuen Hydrostößel.
Wenn es während der Prüfung möglich war, den Kolben des hydraulischen Kompensators zu bewegen, wiederholen Sie die Schritte 9 und 10, bis der Hohlraum des hydraulischen Kompensators vollständig mit Dieselkraftstoff gefüllt ist.
Wenn der Hydrostößel danach immer noch nicht betriebsbereit ist oder seine Gesamthöhe geringer ist als die Höhe des neuen Hydrostößels, ersetzen Sie ihn.
Bevor Sie den Ventilantriebsmechanismus zusammenbauen, lagern Sie gefüllte Hydrostößel nur in vertikaler Position mit den Kolben nach oben. Vermeiden Sie, dass Schmutz in die Hydrostößel gelangt.
Installieren Sie Hydrostößel so bald wie möglich nach dem Tanken am Motor, um einen möglichen Verlust von Dieselkraftstoff zu vermeiden.
- 12. Montieren Sie die Hydrostößel und alle ausgebauten Teile in umgekehrter Reihenfolge des Ausbaus.
- 13. Starten Sie den Motor und lassen Sie ihn 1-3 Minuten lang im Leerlauf laufen. Entlüften Sie bei Bedarf die Hydrostößel wie oben beschrieben.