Disassemble the generator in the following order:
Remove the brush holder with brushes.
Remove the bearing cover and unscrew the nut securing the rear end of the rotor shaft.
Remove the alternator clamping screws and remove the back cover with the stator.
Disconnect the phase ends of the stator winding from the rectifier unit and remove the stator.
Remove the pulley, fan, key and spacer from the rotor shaft.
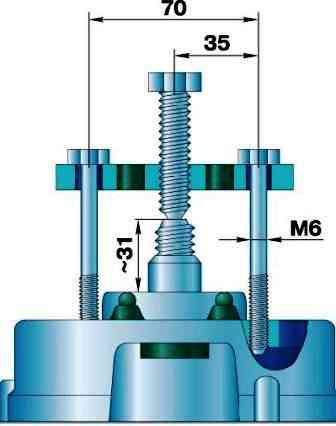
Remove the front cover with the bearing from the rotor shaft using the threaded holes in the cover and a special tool (fig. 1).
Inspect and check the parts and components of the generator.
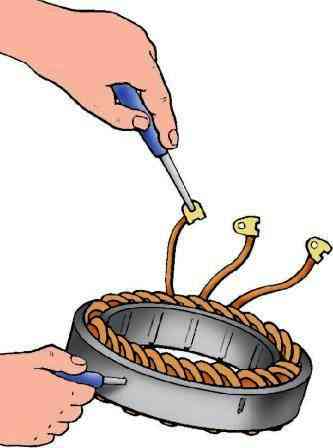
Checking the generator stator
Using a special device or a test lamp connected to the AC mains, check if the stator coils are shorted to the housing (Fig. 2).
When checking with a test lamp, connect it to any terminal of the stator winding and the housing. In this case, the tips should not touch the body.
The lamp should not be lit. If the lamp is on, this indicates a short circuit of the stator coil winding to the housing.
In this case, repair the problem or replace the stator.
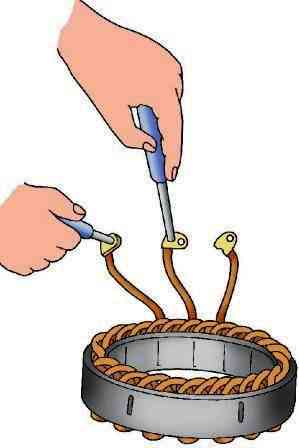
Then, using a test lamp, check for a short circuit in the stator windings between turns.
To do this, connect the test lamp in turn to the two terminal lugs of each winding (Fig. 3); with a good winding, the lamp should be on.
If the lamp does not light between any two terminals, this indicates a winding break or a connection failure at the midpoint of the phases.
There should be no traces of rotor grabbing on the stator poles. If there is interference, check the covers and bearings, replace the covers if necessary.
When inspecting, pay attention to the absence of damage to the covers, especially at the locations of the attachment legs.
The bearing should enter the back cover (from the side of the slip rings) freely, but without noticeable slack.
The diameter of the bearing hole should be 35 + 0.03 mm. If the diameter of the bore for the bearing is higher than specified, then the cover must be replaced.
Make sure the bearing in the front cover (pulley side) is tight (press fit).
The diameter of the bearing hole should be 47 + 0.03 mm.
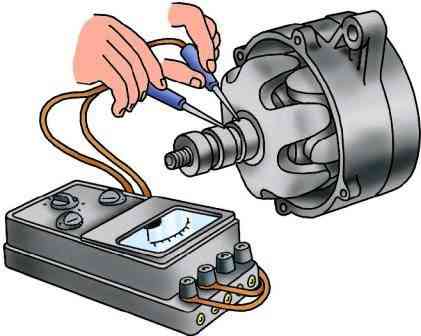
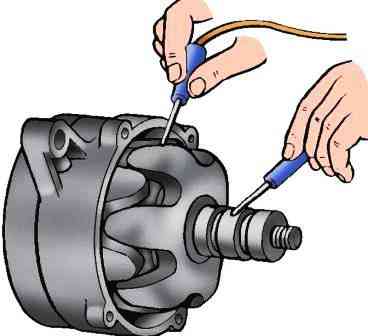
Checking the generator rotor
Check with an ohmmeter if there is a short circuit between the turns in the rotor winding (Fig. 4) and a short circuit of the winding to the housing (Fig. 5).
Replace rotor if damaged.
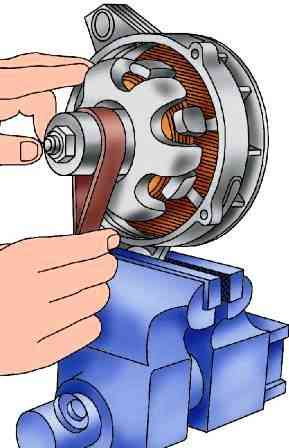
If the slip rings of the rotor are dirty, have traces of burning and uneven wear along the width, clean them with fine glass sandpaper with a grit of 80 or 100.
To clean the slip rings, fix the generator by the front cover in a vise and, while smoothly turning the rotor, clean the rings with sandpaper, as shown in fig. 6.
If the rings have severe wear and beating of the surface, turn and grind them (for the G250P2 generator, the minimum allowable diameter of the slip ring groove is 29.2 mm).
The surface roughness of the rings should be grade 7.
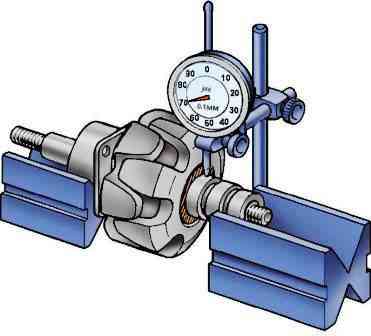
After turning, check the runout of the slip rings with an indicator (Fig. 7).
Beating rings more than 0.08 mm leads to their rapid burning and wear of the brushes, especially at high speeds.
Checking the brush assembly and rectifier unit of the generator
Check whether the brushes in the brush holders are seized, as well as the condition and amount of wear of the brushes, and the tension of the brush springs.
When the brushes are pressed lightly, the sparks and rings burn out.
Excessive pressure on the brushes causes increased wear. The pressing force of the brushes should be in the range of 180–260 gc.
Make sure that the brushes in the brush holders move freely, without jamming or excessive play.
Even slight sticking of the brushes, which is sometimes difficult to determine, increases the spark underneath.
Brushes worn to a height of 8 mm or damaged, replace with new type M1.
Do not use other types of brushes.
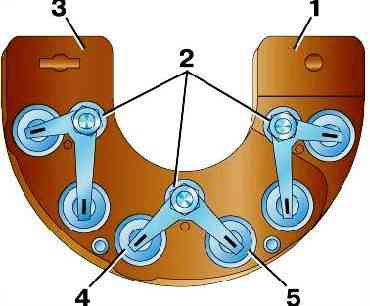
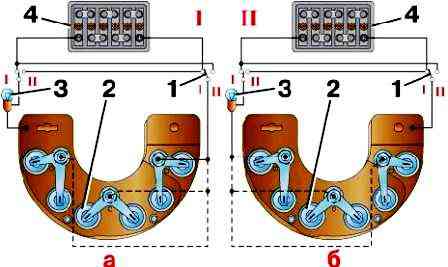
Thoroughly clean the rectifier block VBG-1 (or PBV-4-45) (Fig. 8).
Check the diodes with test lamp 3 (fig. 9).
Due to the fact that diodes of different polarity are mounted in each section of the block, check them with different polarity (Fig. 9, a, b) of turning on the battery.
If the diode is in good condition, the lamp should be on in switch position I, and off in position II.
If the lamp is off in position I, this indicates a break in the diode junction.
If the control lamp in position II of the switches is on, this indicates a short circuit in the diode.
Replace the rectifier section with the bad diode.
Unsolder the leads of the rectifier section with two soldering irons at the same time with the nut of the phase winding connection terminal unscrewed.
When installing a new section, keep in mind that the soldering point can be heated no more than 150 ° C for five seconds.
For a more thorough check of the diodes, use a special device for testing semiconductor devices.
Assemble the generator in reverse order.
Checking the generator
The serviceability of the generator and the correctness of its assembly are determined by checking the rotor speed, at which a voltage of 12.5 V is reached when the generator is running without load and at full load.
Check on a test stand consisting of an electric motor that allows you to smoothly change the dyeing frequency of the generator up to 3000 min -1, a rheostat that allows you to create a load of up to 40 A in the generator circuit, a 6ST–60– storage battery EM, rheostat in the excitation winding circuit for 3-5 A and devices.
You can use the model 533 GARO test stand.
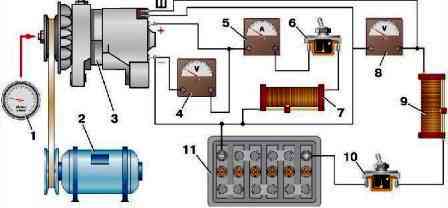
Scheme of checking the generator on the simplest stand is shown in fig. 10.
To check the generator, turn on the switch 10 and adjust the voltage of 12.5 V using the voltmeter 8 with the rheostat 9.
Without load (switch 6 is off), when the generator is cold, voltmeter 4 should show 12.5 V at a rotor speed of no more than 900 min -1.
Then turn on switch 6 and, by increasing the generator rotor speed, increase the load.
With a load of 28 A and a voltage of 12.5 V (according to voltmeter 4), the rotor speed should be no more than 2100 min -1 .
During these tests, keep the voltage at the "Ш" terminal within 12.5 V (according to voltmeter 8) with a rheostat.
Generators 665.3701–01 and 161.3771
Disassemble the generator 665.3701–01 in the following order:
- 1. Unscrew the nuts securing the positive terminal of the generator and disconnect the capacitor terminal.
- 2. Loosen the two screws securing the shroud to the cover.
- 3. Separate the casing from the cover, for which disconnect the wires with plugs from the generator.
- 4. Loosen the screw securing the brush holder and remove it.
- 5. Loosen the four nuts on the pinch screws and remove the cover y on the side of the slip rings together with the stator.
- 6. Unscrew the three nuts securing different leads from the rectifier unit and separate the stator from the cover.
- 7. Loosen the pulley nut.
- 8. Remove the pulley, knock out the key.
- 9. Remove the drive side cover with the bearing from the rotor shaft.
If the voltage regulator needs to be replaced, remove the two screws securing the voltage regulator to the housing, and then the two screws securing the voltage regulator to the insulating base.
If it is necessary to separate the rectifier unit from the cover, unscrew the contact bolt, the positive terminal nut, the three screws securing the unit to the cover and disconnect the unit terminal from the block plug.
Inspect and check the parts and components of the generator.
Assemble the generator in reverse order.
Disassembly and assembly of the generator 161.3771 are similar.
The main difference is the lack of a rear protective cover.
The voltage regulator is located in the brush holder housing.
Checking the brush assembly
Make sure that the brushes are intact, do not jam in the brush holders and are in good contact with the slip rings. If the brushes are worn out, replace them.
Blow out the socket in the alternator before reinstalling the brush holder.
Checking the rectifier unit
Operations and techniques for checking the rectifier unit are similar to the rectifier unit VBG–1 described above.
Assigning and testing a capacitor
The capacitor serves to protect the electronic equipment of the car from voltage pulses in the ignition system, as well as to reduce radio interference.
If there is a radio receiver in the car, damage to the capacitor or loosening of its fastening on the generator (deterioration of contact with the "ground") is detected by an increase in radio interference when the engine is running.
Tentatively, the health of the capacitor can be checked with a megohmmeter or tester (on a scale of 1–10 mΩ).
If there is no break in the capacitor, then at the moment the probes of the device are connected to the terminals of the capacitor, the arrow should deviate in the direction of decreasing resistance, and then gradually return back.
The capacitance of the capacitor, measured with a special device, should be 2.2 uF ± 20%.
Checking the generator covers
On inspection, pay attention to the absence of damage to the covers, especially at the locations of the mounting feet, bearing seats.
Replace damaged caps.
Checking the generator
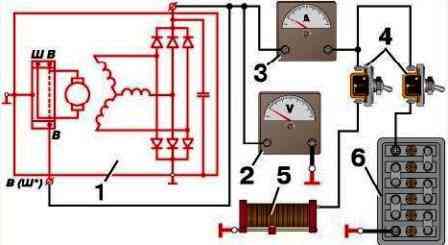
To determine the performance and compliance with the technical characteristics, the generator is checked at the stand according to the scheme shown in fig. 11. Turn on the electric motor of the stand.
The check is made immediately after the generator has been running for 1.5 hours at a generator rotor speed of 3000 min -1 , a load current of 40 A and a voltage of 13 V with the switches on.
When testing, gradually increase the rotor speed until the voltage on the voltmeter reaches 13 V.
For a serviceable generator, the output current must be at least 55 (57 *) A at a rotor speed of 5000 min -1. (* For generator 161.3771)
If the measured value of the output current is less, then this indicates a malfunction in the stator and rotor windings, damage to the valves or wear of slip rings and brushes.
In this case, a thorough check of the windings and diodes is necessary to determine the location of the fault.
The generator output voltage is checked at rotor speed (3500±125) min -1 .
The generator current is maintained by means of a rheostat equal to (18 ± 0.9) A.
Measure the voltage at the generator output, which should be within the limits specified in the technical data for this type of generator.
If the voltage is not within the specified limits, then replace the voltage regulator with a control, known to be good, and repeat the test.
If the voltage still does not fit within the specified limits, then it is necessary to check the generator windings and diodes.